Grundlegender Leitfaden zur Spritzgussverarbeitung
Von: CapableMaching
Vorwort:
Dieser prägnante Leitfaden soll eine einfache Einführung in die grundlegenden Aspekte des Spritzgießens bieten. Ganz gleich, ob Sie neu auf dem Gebiet sind oder eine Kurzreferenz suchen: Auf dieser Seite werden die Grundlagen, der Maschinenbetrieb und die Optimierung behandelt. Das Spritzgießen ist ein wichtiger Akteur in der Fertigungsindustrie und formt Produkte, die von Alltagsgegenständen bis hin zu Industrieteilen reichen. Ziel dieses Leitfadens ist es, die Komplexität zu vereinfachen und praktische Einblicke in effektive und effiziente Formprozesse zu bieten. Ganz gleich, ob Sie Student, Ingenieur oder Branchenprofi sind, wir hoffen, dass dieser Leitfaden eine praktische Ressource ist, die Ihnen dabei hilft, sich in der Welt des Spritzgießens zurechtzufinden.
Ein „Spritzzyklus“ kann sich je nach Kontext auf unterschiedliche Prozesse beziehen. Eine häufige Bedeutung des Begriffs „Spritzzyklus“ bezieht sich jedoch auf das Spritzgießen, einen Herstellungsprozess zur Herstellung von Kunststoffteilen. Beim Spritzgießen bezieht sich ein Einspritzzyklus auf die Abfolge von Schritten, die zur Herstellung eines einzelnen Teils oder Produkts ausgeführt werden.
Um den detaillierten Prozess des Spritzgießens zu verstehen und die entsprechenden Parameter der Spritzgießmaschine anzupassen, müssen wir theoretisch verstehen, wie der Kunststoff fließt.
Um qualitativ hochwertige Produkte herzustellen, ist es notwendig, die Details des Spritzgussprozesses zu verstehen und zu verstehen, wie die entsprechenden Parameter der Spritzgussmaschine eingestellt werden. Dazu müssen wir verstehen, wie der Kunststoff in der Maschine fließt Andererseits müssen wir die Theorien und Terminologie in diesem Bereich kennen.
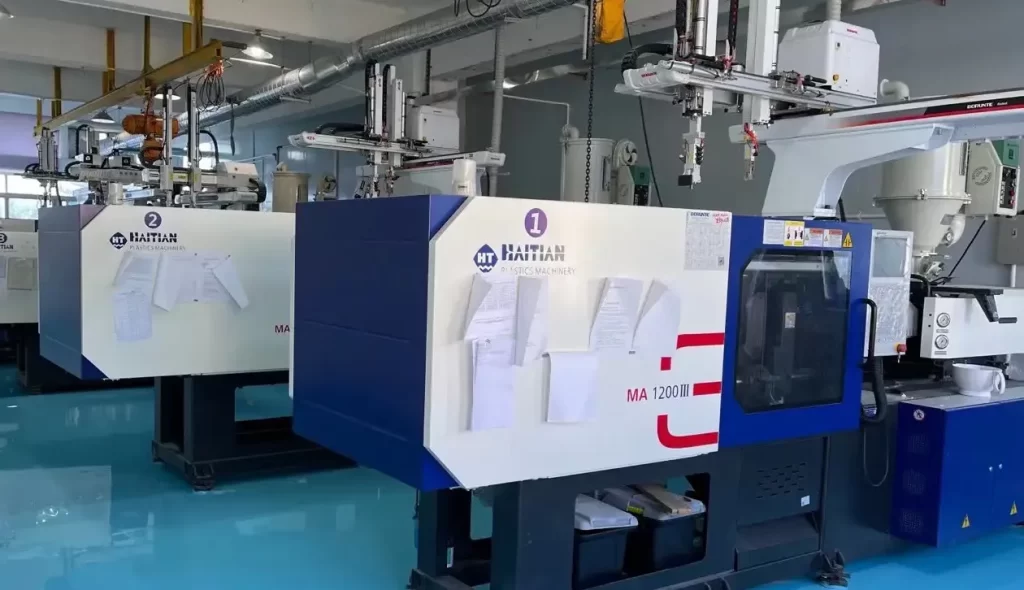
Fountain-Flow-Theorie
Die Fountain-Flow-Theorie ist nach dem Verhalten des geschmolzenen Kunststoffmaterials benannt, wenn es in den Formhohlraum eintritt und ihn füllt. In dieser Theorie wird davon ausgegangen, dass das Kunststoffmaterial auf ähnliche Weise in die Form fließt wie eine Flüssigkeit in einem Brunnen. [ 1 ] Hier ist eine vereinfachte Erklärung des Konzepts:
A) . Eintrittspunkt: Das Kunststoffmaterial gelangt an einem oder mehreren Eintrittspunkten in den Formhohlraum. Dieser Eintrittspunkt wird normalerweise als Tor bezeichnet.
B) . Strömungsmuster: Wenn das Material durch den Anschnitt eingespritzt wird, bewegt es sich im Formhohlraum nach außen und oben, ähnlich wie Wasser aufsteigt und sich ausbreitet, wenn eine Flüssigkeit in einen zentralen Punkt gepumpt wird, wodurch ein brunnenartiges Strömungsmuster entsteht.
C) . Füllverhalten: Der geschmolzene Kunststoff fließt diesem brunnenartigen Muster folgend durch den Formhohlraum und füllt dabei die komplizierten Details des Teils aus. Dieses Fließverhalten ist entscheidend, um sicherzustellen, dass auch komplexe und dünnwandige Abschnitte des Teils ausreichend gefüllt werden.
Die Fountain-Flow-Theorie ist ein wichtiges Konzept für Formenbauer und Verfahrenstechniker im Spritzguss. Um eine gleichmäßige Teilequalität zu erreichen, Fehler wie Lufteinschlüsse oder kurze Spritzlinge zu minimieren und die Zykluszeiten zu optimieren, ist es wichtig zu verstehen, wie das Material im Formhohlraum fließt.
Im Allgemeinen handelt es sich bei Spritzgussprodukten um flache Produkte mit geringer Wandstärke. Als Flachprodukt gilt ein Produkt mit einer Dicke von 3 bis 4 mm oder weniger und einer Breite, die dem Fünffachen der Dicke entspricht. [ 2 ]
In dieser Art von Hohlraum fließt das Harz und bildet eine verfestigte Schicht auf der Form, um im Voraus eine wasserspaltende Form zu bilden.
Nach diesem Prinzip bildet das dosierte Harz am vorderen Ende den Oberflächenteil des Produkts und das dosierte Harz am hinteren Ende füllt den mittleren Teil des Produkts.
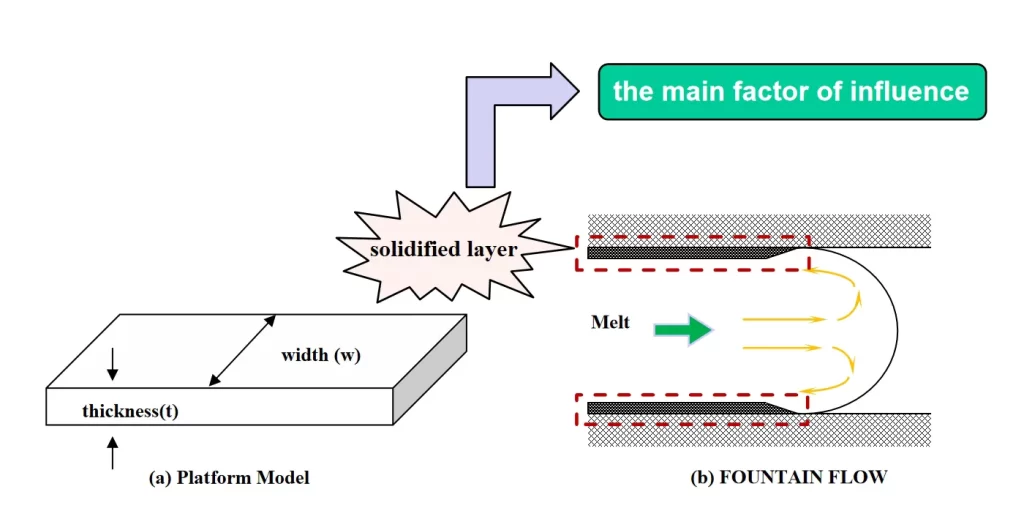
Scherverformungsrate und Reibungswärme
Die Scherverformungsrate, oft als γ (Gamma) bezeichnet, ist ein grundlegendes Konzept der Strömungsmechanik und Rheologie, das beschreibt, wie sich verschiedene Schichten oder Elemente einer Flüssigkeit relativ zueinander bewegen und dabei Scherung oder Verformung innerhalb der Flüssigkeit erzeugen. Im Kontext der Fontänenströmungstheorie beim Spritzgießen ist die Scherverformungsrate relevant, da sie dabei hilft, zu beschreiben, wie sich das geschmolzene Kunststoffmaterial verformt, wenn es im Formhohlraum fließt.
In der Fontänenströmungstheorie bezieht sich die Scherverformungsrate auf die Geschwindigkeit, mit der benachbarte Schichten oder Partikel des geschmolzenen Kunststoffs eine relative Bewegung oder Verformung erfahren, während das Material durch den Formhohlraum fließt. Diese Verformungsgeschwindigkeit wird von Faktoren wie der Einspritzgeschwindigkeit, der Viskosität des Kunststoffmaterials und der Geometrie der Form beeinflusst. [ 3 ]
Wenn die Einspritzgeschwindigkeit langsam ist und das Material immer weiter in das Innere der Form eindringt, ist der Wärmeverlust größer. Zu diesem Zeitpunkt wird die Scherverformungsrate verringert und die erzeugte Reibungswärme kleiner, was zur Folge hat Die Härtungsschicht der Produktoberfläche wird dicker, was sich letztendlich auf das Wachstum des Produkts auswirkt.
Die Einspritzgeschwindigkeit ist hoch, das Material dringt in das Innere der Form ein, der Wärmeverlust ist gering, zu diesem Zeitpunkt wird die Scherverformungsrate erhöht und die erzeugte Reibungswärme nimmt zu, was dazu führt, dass die Produktoberfläche aushärtet wird dünner, verlängert jedoch die Abkühlzeit des Produkts, ist weniger effizient und führt gleichzeitig zu einer Vielzahl von Fehlern (z. B. Chargenfronten) usw. [ 4 ]
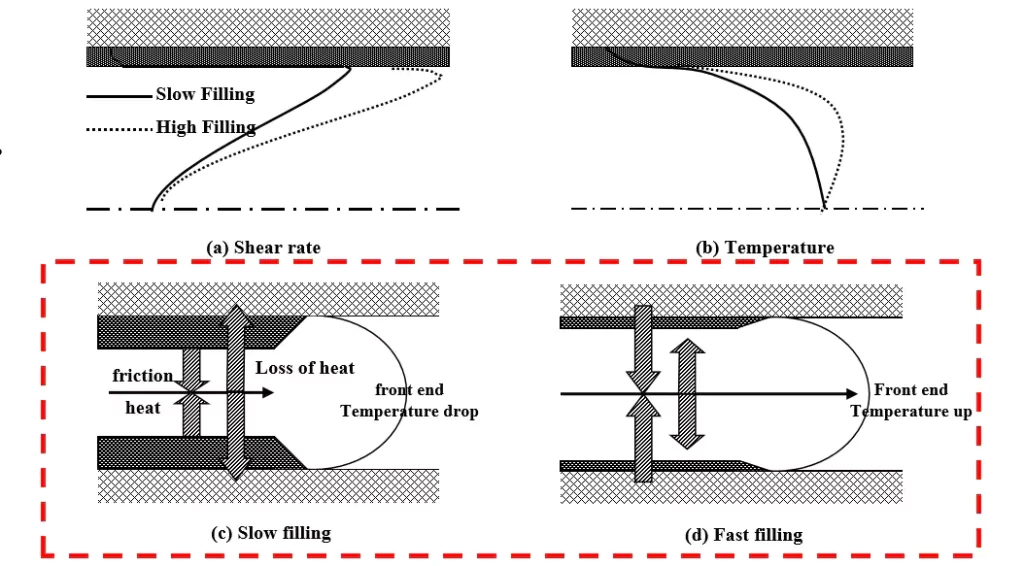
Einspritzdruck
Unter Einspritzdruck versteht man im Kontext des Spritzgießens die Kraft oder den Druck, der während der Einspritzphase des Formprozesses ausgeübt wird, um das geschmolzene Kunststoffmaterial in den Formhohlraum zu drücken. Es ist einer der Schlüsselparameter, die von der Spritzgießmaschine gesteuert werden, und ein entscheidender Faktor für die Qualität und Konsistenz der Formteile.
Der Einspritzdruck wird typischerweise in Pfund pro Quadratzoll (psi) oder Megapascal (MPa) gemessen und kann je nach Faktoren wie dem verwendeten Material, der Geometrie des Teils und dem Design der Form variieren.
Die Höhe des erforderlichen Einspritzdrucks hängt von mehreren Faktoren ab, darunter:
a)
Materialviskosität:
Viskosere (dickere) Materialien erfordern höhere
Einspritzdrücke, um richtig zu fließen.
b)
Formdesign: Die Komplexität
und Größe der Form sowie die Anzahl und Gestaltung der Kavitäten
können den erforderlichen Druck beeinflussen.
c)
Teilegeometrie: Dünnwandige
oder komplizierte Teile erfordern möglicherweise einen höheren
Druck, um richtig gefüllt zu werden.
d)
Einspritzgeschwindigkeit:
Schnellere Einspritzgeschwindigkeiten erfordern oft einen
höheren Druck, um den Durchfluss aufrechtzuerhalten.
e)
Aus Sicherheitsgründen sollte
während der Produktion ein Druck verwendet werden, der kleiner
als der maximale Einspritzdruck der Spritzgießmaschine ist, bis
der Endpunkt der Kavität gefüllt ist.
Im Allgemeinen beträgt der
Einspritzdruck weniger als 80 % des maximalen Einspritzdrucks
der Spritzgießmaschine.
[
5
]
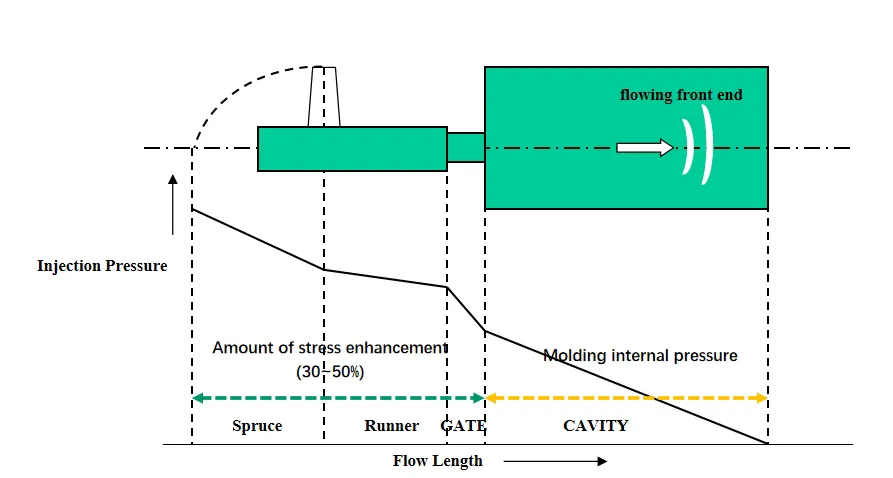
Zeit füllen
Beim Spritzgießen bezieht sich die „Füllzeit“ auf die Zeit, die das geschmolzene Kunststoffmaterial benötigt, um den Formhohlraum während der Einspritzphase des Formprozesses vollständig zu füllen. Dieser Parameter ist ein entscheidender Aspekt des Formprozesses und wird typischerweise in Sekunden oder Millisekunden gemessen. Die Füllzeit ist einer der Schlüsselfaktoren, die die Qualität und Konsistenz der Formteile beeinflussen.
Der Zusammenhang zwischen Einspritzgeschwindigkeit und Einspritzdruck ist in der Grafik als U-förmige Kurve dargestellt. Bei langsamer Einspritzgeschwindigkeit ist der Wärmeverlust hoch, die Fließtemperatur sinkt, die Viskosität steigt, die Dicke der aushärtenden Schicht nimmt zu, der Fließwiderstand ist also hoch und der Einspritzdruck steigt.
Im Gegenteil: Bei hoher Einspritzgeschwindigkeit steigt die Fließtemperatur, die Viskosität sinkt und die Dicke der aushärtenden Schicht wird geringer. Allerdings erhöht sich der Reibungswiderstand zwischen der Aushärtungsschicht und der Fließschicht erheblich, was wiederum den Injektionsdruck erhöht. Der Injektionsdruck wird minimiert, wenn die Durchflussrate in Caviti konstant ist. [ 6 ]
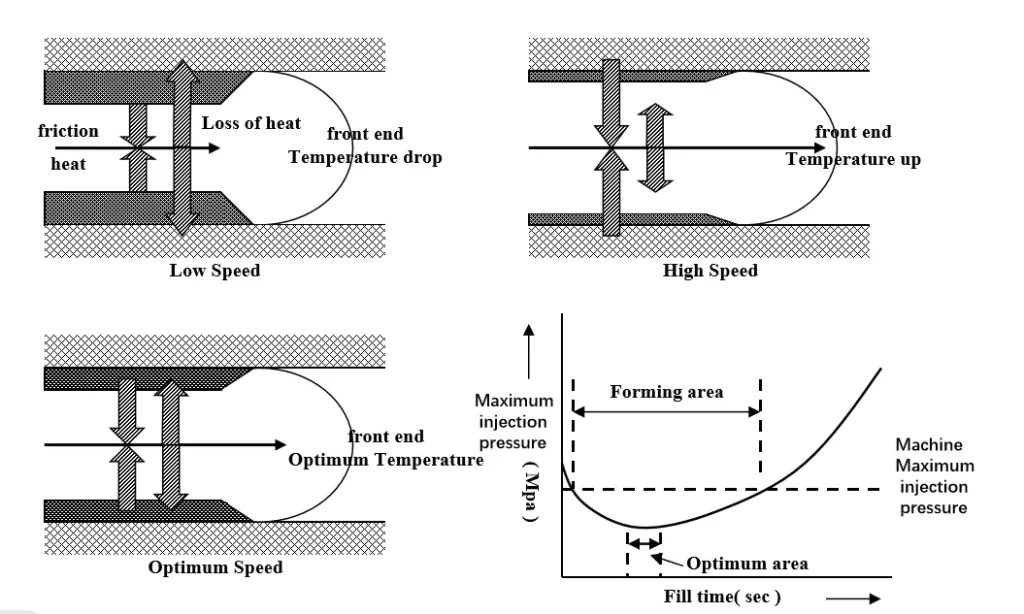
Die optimale Einspritzgeschwindigkeit ist diejenige, die den Einspritzdruck unter den gegebenen Bedingungen minimiert. Abhängig von der Dicke der Kavität sollte die Einspritzgeschwindigkeit unterschiedlich sein. Dünne haben einen kleineren effektiven Strömungsquerschnitt als dicke. Daher ist es notwendig, die Einspritzgeschwindigkeit zu erhöhen, die Verformungsrate des gesamten Abschnitts zu erhöhen und die Reibungsverformungskraft zu erhöhen, um die Fließtemperatur zu stabilisieren und den Einspritzdruck zu verringern. [ 7 ]
Abhängig vom Material des Harzes können die spezifische Wärme, die Wärmeleitfähigkeit, die Viskosität usw. stark variieren. Abhängig von der Temperatur haben Materialien mit starken Viskositätsänderungen (PC, PMMA) einen kleineren U-Bogen, Materialien ohne diese Eigenschaft (PP, ABS) jedoch einen größeren U-Bogen. Daher reagieren einige Materialien empfindlich auf die Einspritzgeschwindigkeit, andere nicht.
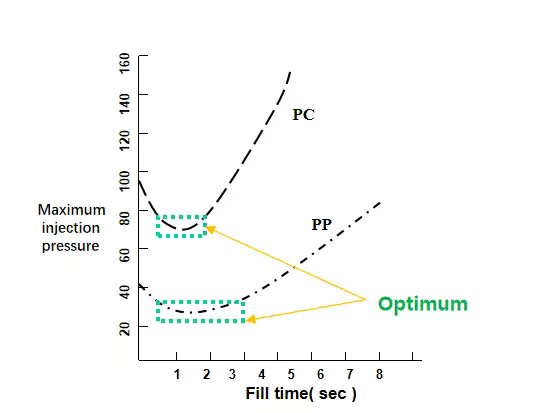
Einstellung des Haltedrucks
Der Haltedruck bezieht sich auf das Einspritzen in das Material nach dem Hohlraum, um sicherzustellen, dass die Schrumpfung des Harzes beim Abkühlen nicht zu groß ist. In der richtigen Zeit muss die Schraube vorgeschoben werden, um den entsprechenden Druck im Hohlraum aufrechtzuerhalten und weiterhin Harz bereitzustellen Zum Prozess des Hohlraums und zum Ausgleich der Abkühlung des geschmolzenen Kunststoffmaterials beim Aushärten hat dieser Prozess einen großen Einfluss auf die Qualität des Produkts.
Bestimmung der Nachdruckstärke und -zeit
Haltekraft: Die Höhe des Haltedrucks bestimmt das Ausmaß der Schrumpfung. Wenn der Haltedruck erhöht wird, wird das Produkt im Allgemeinen voller und es kann keine Schrumpfung auftreten. Wenn der Haltedruck zu niedrig ist, wird das Produkt kleiner und es kommt zu einer Schrumpfung. Allerdings erhöht ein zu hoher Nachdruck die Formkraft und die Resthärte, was zu einer Verformung des Produkts führt. Im Allgemeinen beträgt der geeignete Haltedruck 70–80 % des maximalen Einspritzdrucks.
Nachdruckzeit: Die Nachdruckzeit hat viel mit der Dicke der Kavität zu tun. Denn je dicker das Produkt ist, desto länger ist die Abkühlzeit. Um ein Schrumpfen zu verhindern, muss das Harz während dieser Zeit ständig zugeführt werden, sodass der Druck über einen bestimmten Zeitraum aufrechterhalten werden muss. Da das Harz jedoch nach dem Aushärten des GATE nicht in die Kavität gelangen kann, verliert der Nachdruck seine optimale Wirkung, da das Harz nach dem Aushärten des GATE keinen Druck übertragen kann. Hier ist es notwendig, das GATE entsprechend der Dicke des Produkts zu gestalten, um die Haltezeit anzupassen. Die Aushärtezeit des GATE hängt natürlich von der Dicke und Länge des GATE ab. [ 8 ]
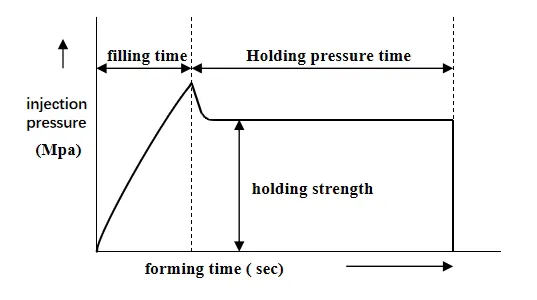
Wenn der Haltedruck entsprechend einem bestimmten Druck gleichmäßig ausgeübt wird, ist im Allgemeinen der Haltedruck in der Nähe des GATE groß und die Schrumpfungsrate des Produkts gering, aber wenn die Füllung das Endteil erreicht, ist sie dem relativ unzureichend ausgesetzt Druck, und die Wahrscheinlichkeit einer Schrumpfung nimmt stark zu und es kommt zu einer ungleichmäßigen Schrumpfung. Diese Unebenheiten erhöhen die Eigenspannung im Produkt, was eine wichtige Ursache für Verformungen ist. Anstatt den Haltedruck auf einen durchschnittlichen Druck einzustellen, wird daher die Größe des Haltedrucks schrittweise verringert, und durch mehrmaliges Einstellen des Haltedrucks kann die Abweichung der Position des Drucks innerhalb des Hohlraums verringert werden [ 9 ].
Darüber hinaus ist es auch möglich, die Fehler zu reduzieren, indem das GATE an der dicken Stelle des Produkts angebracht wird. Im Allgemeinen hängt die Schrumpfrate vom Druck und der Aushärtegeschwindigkeit ab. Wenn Sie GATE an einer Stelle einstellen, an der die Aushärtungsgeschwindigkeit langsam und die Schrumpfungsrate groß ist, und ausreichend Druck bereitstellen, kann die Schrumpfungsrate in einem kleinen Bereich gehalten werden. Im Allgemeinen sollte die Nachdruckzeit länger als die GATE-Aushärtungszeit eingestellt werden. Wenn der Haltedruck kürzer als die GATE-Aushärtungszeit eingestellt wird, kann es dazu kommen, dass die Schnecke nach dem Druckverlust aufgrund des nicht ausgehärteten Harzes zurückfährt (da normalerweise nach dem Haltedruckprojekt das Dosierprojekt folgt) und das Harz komprimiert wird Die Vorderseite des GATE wird nach hinten fließen, und dann wird die Schrumpfungsrate um das GATE herum größer sein.
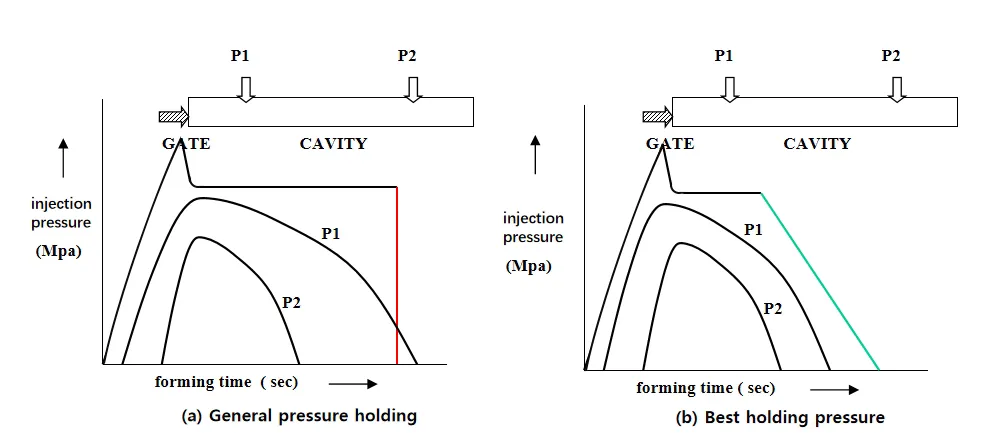
Formbedingungen
Unter Spritzgussbedingungen versteht man die spezifischen Parameter und Einstellungen, die während des Spritzgussprozesses zur Herstellung von Formteilen verwendet werden. Diese Bedingungen spielen eine entscheidende Rolle bei der Bestimmung der Qualität, Konsistenz und Effizienz des Formprozesses. Um optimale Ergebnisse zu erzielen, werden verschiedene Faktoren und Einstellungen berücksichtigt.
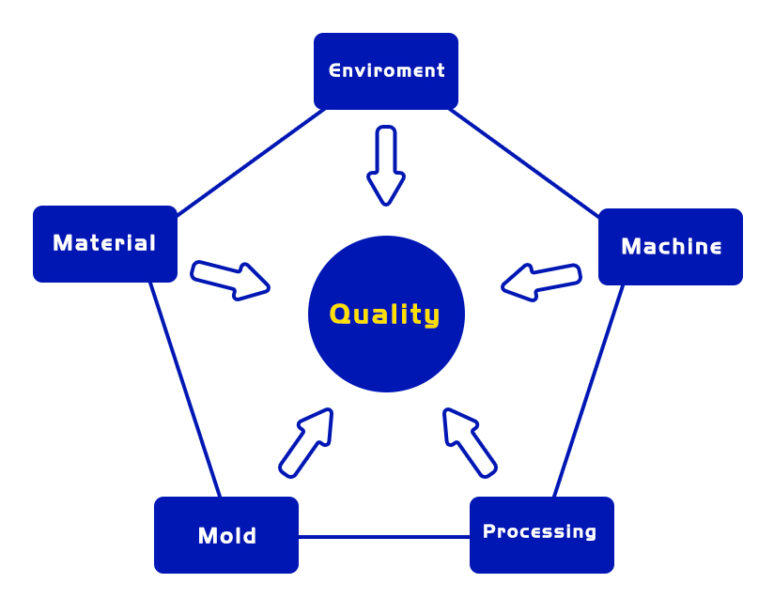
Hier sind einige wichtige Spritzgussbedingungen:
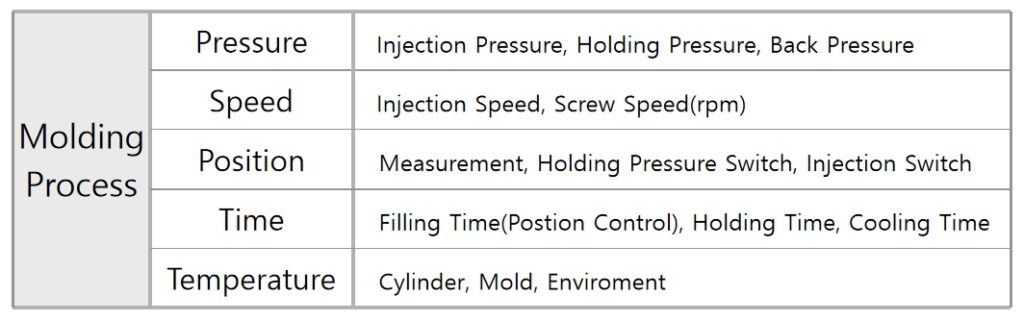
Die Optimierung dieser Spritzgussbedingungen erfordert ein umfassendes Verständnis der Materialeigenschaften, des Teiledesigns und der Formeigenschaften. Prozessingenieure und Bediener passen diese Parameter sorgfältig an, um die gewünschte Teilequalität zu erreichen und Fehler während des Spritzgussprozesses zu minimieren. [ 10 ]
Hier müssen wir einige häufig verwendete Begriffe erklären.
Zylinder
Beim Spritzgießen bezieht sich der Begriff „Zylinder“ typischerweise auf den Zylinder der Spritzgießmaschine. Der Zylinder der Maschine ist eine entscheidende Komponente, in der das Kunststoffmaterial geschmolzen, gemischt und dann in den Formhohlraum eingespritzt wird, um das gewünschte Teil zu formen. Der Zylinder besteht aus mehreren Zonen, von denen jede beim Plastifizierungsprozess eine bestimmte Funktion erfüllt.
Formtemperatur
Unter Formtemperatur versteht man die Temperatur der Form beim Spritzgießen. Sie ist ein kritischer Parameter im Spritzgussprozess und hat erheblichen Einfluss auf die Qualität und Eigenschaften der Formteile. Die Formtemperatur wird sorgfältig kontrolliert und während des gesamten Formzyklus auf einem bestimmten Niveau gehalten.
Einspritzgeschwindigkeit
Unter Einspritzgeschwindigkeit versteht man im Kontext des Spritzgießens die Geschwindigkeit, mit der das geschmolzene Kunststoffmaterial während der Einspritzphase des Formprozesses in den Formhohlraum eingespritzt wird. Es handelt sich um einen kritischen Parameter, der die Qualität, das Aussehen und die Eigenschaften der Formteile erheblich beeinflussen kann. Die Einspritzgeschwindigkeit wird in Millimetern pro Sekunde (mm/s) oder Zoll pro Sekunde (in/s) gemessen und stellt die Bewegungsgeschwindigkeit der Einspritzschnecke oder des Kolbens dar.
Schraubendrehzahl
Die Schneckendrehzahl (Umdrehungen pro Minute) bezieht sich im Kontext des Spritzgießens auf die Drehzahl der Schnecke in der Spritzgießmaschine. Die Schnecke ist eine Schlüsselkomponente im Plastifizierungsprozess und verantwortlich für das Schmelzen, Mischen und Einspritzen des geschmolzenen Kunststoffmaterials in den Formhohlraum.
Einspritzdruck
Es bezieht sich auf die Kraft oder den Druck, der während der Einspritzphase des Formprozesses ausgeübt wird, um das geschmolzene Kunststoffmaterial in den Formhohlraum zu drücken.
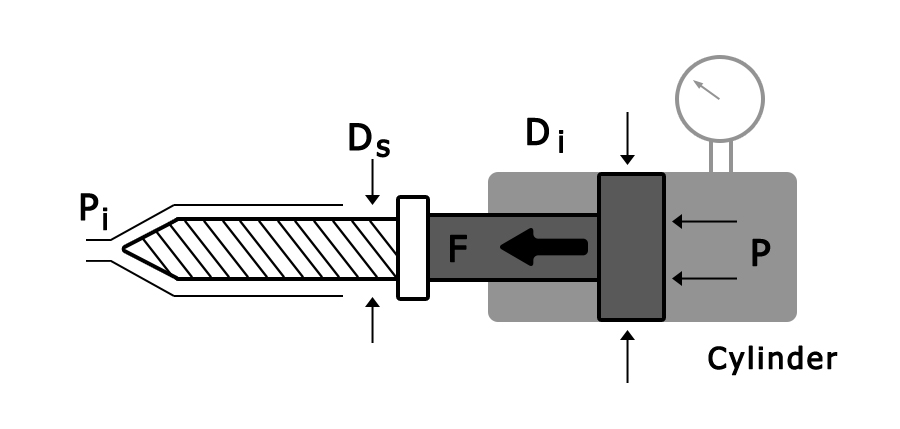
Verpackungsdruck
Der Packdruck, auch Nachdruck oder Druck der zweiten Stufe genannt, ist eine Phase im Spritzgussprozess, in der nach dem ersten Einspritzen in den Formhohlraum zusätzlicher Druck auf das geschmolzene Kunststoffmaterial ausgeübt wird. Dieser Druck wird während der Pack- oder Haltephase des Formzyklus für eine bestimmte Dauer aufrechterhalten. Der Hauptzweck des Packungsdrucks besteht darin, die Schrumpfung auszugleichen und eine vollständige Formfüllung sicherzustellen, was zur Herstellung qualitativ hochwertiger Formteile beiträgt. [ 11 ]
Gegendruck
Beim Schmelzen und Plastifizieren von Kunststoffen bewegt sich das geschmolzene Material immer weiter zum vorderen Ende des Zylinders (innerhalb der Dosierkammer) und baut dabei allmählich einen Druck auf, der die Schnecke nach hinten drückt. Um ein zu schnelles Zurückbewegen der Schnecke zu verhindern und eine gleichmäßige Verdichtung der Schmelze zu gewährleisten, ist es erforderlich, einen Druck in Gegenrichtung zur Schnecke bereitzustellen und diesen Druck in Gegenrichtung zu verhindern, dass sich die Schnecke zurückbewegt Gegendruck genannt. [ 12 ]
Schraubendrehzahl
Die Schraubendrehzahl wird in Umdrehungen pro Minute gemessen und gibt an, wie oft die Schraube in einer Minute eine volle Umdrehung durchführt.
V/P-Umschaltpunkt
Der V/P-Umschaltpunkt, auch Geschwindigkeit-zu-Druck-Umschaltpunkt genannt, ist ein Parameter beim Spritzgießen, der sich auf den Übergangspunkt während des Einspritzvorgangs bezieht, wenn die Maschine von Geschwindigkeitsregelung auf Druckregelung umschaltet. Dieser Übergang ist wichtig für die Optimierung des Spritzgussprozesses und die Erzielung gleichbleibender und qualitativ hochwertiger Formteile.
In den frühen Phasen des Einspritzvorgangs arbeitet die Maschine typischerweise im Geschwindigkeitsregelungsmodus. In diesem Modus ist die Einspritzgeschwindigkeit der primäre Regelparameter. Wenn sich die Form füllt und das Material erstarrt, schaltet die Maschine in den Druckregelmodus, in dem der Einspritzdruck zum primären Regelparameter wird.
Der V/P-Umschaltpunkt ist der Punkt im Einspritzzyklus, an dem die Maschine von der Geschwindigkeitsregelung zur Druckregelung übergeht. Dieser Übergang ist entscheidend, um Probleme wie Über- oder Unterfüllung der Form zu vermeiden, die sich auf die Qualität der Formteile auswirken können.
Saugen Sie zurück
„Zurücksaugen“ bezieht sich im Kontext des Spritzgießens auf ein absichtliches Zurückziehen oder eine Rückwärtsbewegung der Schnecke während des Formzyklus. Dies geschieht, um das Vorhandensein von geschmolzenem Kunststoffmaterial am Ende der Schnecke während der Abkühl- und Erstarrungsphase des Spritzgussprozesses zu reduzieren oder zu eliminieren.
Der Hauptzweck des Rücksaugens besteht darin, ein Auslaufen oder Fädenziehen des geschmolzenen Materials zu verhindern, nachdem die Form gefüllt wurde und bevor die Form zum Auswerfen des Teils geöffnet wird. Zu Speichelbildung kommt es, wenn überschüssiges Material an der Düse oder im Angusssystem zurückbleibt, was zur Bildung unerwünschter Kunststofftröpfchen oder -stränge führt.
So funktioniert das Zurücksaugen normalerweise:
- Nachdem die Form gefüllt ist, fährt die Schnecke kurzzeitig zurück bzw. bewegt sich zurück.
- Diese Rückwärtsbewegung erzeugt einen Hohlraum oder Unterdruck an der Vorderseite der Schraube.
-
Durch den Unterdruck wird
überschüssiges geschmolzenes Kunststoffmaterial an der Düse
oder im Angusssystem zurück in den Zylinder gezogen.
T4. Anschließend durchläuft die Form die Abkühl- und Erstarrungsphase, ohne dass die Gefahr von Tropfen oder Fäden besteht.
Das Zurücksaugen ist besonders nützlich, wenn mit Thermoplasten gearbeitet wird, die dazu neigen, Fäden zu ziehen oder zu sabbern, und es trägt dazu bei, sauberere und präzisere Formteile herzustellen. Das Ausmaß der Rücksaugung ist in der Regel einstellbar und die optimale Einstellung hängt von Faktoren wie dem verwendeten Material und den spezifischen Anforderungen der Formanwendung ab.
Kissen
Beim Spritzgießen bezieht sich der Begriff „Kissen“ auf die kleine Menge geschmolzenen Kunststoffmaterials, die am Ende des Spritzhubs absichtlich im Zylinder zurückbleibt. Dieses Materialpolster dient im Formprozess mehreren wichtigen Zwecken:
- Ausgleich der Schrumpfung: Wenn das Kunststoffmaterial in der Form abkühlt und erstarrt, unterliegt es einer Schrumpfung. Das Kissen gleicht diese Schrumpfung aus, indem es zusätzliches Material bereitstellt, das in die Form fließen kann, um eventuelle Hohlräume zu füllen, die durch die Erstarrung des Kunststoffs entstehen.
- Verhindern von Kurzschüssen: Ein Kurzschuss tritt auf, wenn nicht genügend Material vorhanden ist, um den Formhohlraum vollständig zu füllen. Das Kissen trägt dazu bei, Kurzschüsse zu verhindern, indem es sicherstellt, dass genügend Material im Lauf vorhanden ist, um eventuelle Schwankungen im Formprozess auszugleichen.
3. Vermeidung von Strahlbildung: Strahlbildung ist ein Defekt, der auftreten kann, wenn der geschmolzene Kunststoff mit hoher Geschwindigkeit in die Form eingespritzt wird, was dazu führt, dass das Material schert und ein stromartiger Fluss entsteht. Das Kissen trägt dazu bei, die Injektionsgeschwindigkeit und den Injektionsdruck zu reduzieren und so das Risiko von Spritzern zu minimieren.
Haltezeit
Beim Spritzgießen bezeichnet die „Haltezeit“ den Zeitraum, in dem das geschmolzene Kunststoffmaterial nach der Einspritzphase in der Form unter Druck gehalten wird. Der Hauptzweck der Haltezeit besteht darin, sicherzustellen, dass das Formteil die Form des Formhohlraums vollständig annimmt und mögliche Probleme wie Einfallstellen oder Hohlräume minimiert werden.
Während der Haltezeit kann das Kunststoffmaterial in der Form unter Druck abkühlen und erstarren. Dadurch wird verhindert, dass das Material schrumpft oder sich verformt, bevor das Teil vollständig geformt ist. Diese Phase ist entscheidend für das Erreichen der gewünschten Abmessungen, Oberflächenbeschaffenheit und mechanischen Eigenschaften des Formteils.
Zu den wichtigsten Punkten zur Haltezeit beim Spritzgießen gehören:
- Druckerhaltung: Der auf das geschmolzene Kunststoffmaterial ausgeübte Druck wird während der Haltezeit aufrechterhalten, um der Schrumpfung entgegenzuwirken, die beim Abkühlen und Erstarren des Materials auftritt. Dies ist besonders wichtig für Materialien mit höheren Schrumpfraten.
- Einfrieren des Angusses: Durch die Haltezeit kann der Anguss (der Punkt, an dem der geschmolzene Kunststoff in den Formhohlraum eintritt) einfrieren oder erstarren. Dies trägt dazu bei, ein vorzeitiges Öffnen der Form zu verhindern, das Risiko von Graten (überschüssigem Material) zu verringern und sicherzustellen, dass das Teil vollständig geformt ist.
4. Materialkühlung: Die Haltezeit trägt zur Gesamtkühlung des Formteils bei. Die Abkühlzeit ist ein entscheidender Faktor für die Erzielung gleichbleibender und qualitativ hochwertiger Teile.
Kühlzeit
Unter Abkühlzeit versteht man beim Spritzgießen die Dauer, während der das Formteil in der geschlossenen Form verbleibt, damit der geschmolzene Kunststoff abkühlen und erstarren kann. Die Abkühlzeit ist ein kritischer Schritt im Spritzgusszyklus und hat direkten Einfluss auf die Qualität, Abmessungen und Eigenschaften des endgültigen Formteils.
Zu den wichtigsten Punkten zur Abkühlzeit beim Spritzgießen gehören:
- Erstarrung des Kunststoffs: Der Hauptzweck der Abkühlzeit besteht darin, sicherzustellen, dass das geschmolzene Kunststoffmaterial im Formhohlraum vollständig erstarrt. Dieser Prozess ist wichtig, um die gewünschte Form und strukturelle Integrität des Formteils zu erreichen.
- Minimierung von Verzug und Schrumpfung: Die richtige Kühlung ist entscheidend für die Minimierung des Risikos von Verzug und Schrumpfung der Teile. Eine kontrollierte und gleichmäßige Kühlung trägt dazu bei, eine ungleichmäßige Spannungsverteilung im Material zu verhindern.
- Zykluszeitoptimierung: Während längere Kühlzeiten zu einer besseren Teilequalität beitragen können, sind kürzere Zykluszeiten im Allgemeinen wünschenswerter, um die Produktionseffizienz zu maximieren. Es ist wichtig, die Abkühlzeit mit anderen Faktoren wie Teiledesign und Materialeigenschaften in Einklang zu bringen.
- Temperaturkontrolle: Die Formtemperatur spielt eine wichtige Rolle beim Kühlprozess. Viele Formen verfügen über Kühlkanäle, durch die eine temperaturgesteuerte Flüssigkeit (normalerweise Wasser) zirkuliert, um die Formtemperatur zu kontrollieren und den Abkühlprozess zu beschleunigen. [ 13 ]
Spannkraft
Die Schließkraft ist ein kritischer Parameter beim Spritzgießen und bezieht sich auf die Kraft, die auf die Form ausgeübt wird, um sie während der Einspritz- und Abkühlphase des Formprozesses geschlossen zu halten. Die Klemmkraft ist wichtig, um die Integrität des Formteils aufrechtzuerhalten und zu verhindern, dass Kunststoff aus der Form austritt. [ 14 ]
Die erforderliche Schließkraft hängt von mehreren Faktoren ab, darunter dem zu formenden Material, der Größe und Form des Teils sowie dem Einspritzdruck. Es gibt keine allgemeingültige Formel zur Berechnung der Schließkraft, da diese von verschiedenen Faktoren beeinflusst wird und verschiedene Spritzgießmaschinen möglicherweise unterschiedliche Anforderungen an die Schließkraft haben.
Ein gängiger Ansatz zur Schätzung der Schließkraft besteht jedoch darin, die projizierte Fläche des Formteils und den Einspritzdruck zu verwenden. Die Formel lautet:
Spannkraft = Einspritzdruck × projizierte Fläche des Teils
Hier ist die projizierte Fläche die maximale Fläche des Teils, gesehen aus Richtung der Formöffnung. Der Einspritzdruck ist der Druck, der erforderlich ist, um die Form mit geschmolzenem Kunststoff zu füllen.
Allgemeine Produkte:
Kraft (Tonne) > Projizierte Produktfläche (㎠) × Innendruck der Harzform (kgf/㎠) × 10 -3
Schussgewicht
Das Schussgewicht ist ein kritischer Parameter beim Spritzgießen und bezieht sich auf die Materialmenge (normalerweise in Gramm oder Unzen), die in die Form eingespritzt wird, um ein einzelnes Formteil herzustellen. Es ist ein Schlüsselfaktor im Formprozess, da es die Qualität, Abmessungen und Eigenschaften des Endprodukts beeinflusst.
Das Schussgewicht wird durch das spezifische Gewicht des Materials, die Teilegeometrie und die Hohlräume der Form bestimmt. Es ist wichtig, das Schussgewicht genau zu kontrollieren, um eine gleichbleibende und qualitativ hochwertige Produktion sicherzustellen. Zu geringes oder zu hohes Schussgewicht kann zu Defekten an den Formteilen führen.
Um das Schussgewicht zu berechnen, können Sie die folgende Formel verwenden:
Schussgewicht = Materialspezifisches Gewicht × Teilvolumen
Hierbei ist das spezifische Materialgewicht das Verhältnis der Dichte des Formstoffs zur Dichte des Wassers und das Teilvolumen das Volumen des zu formenden Teils. Das spezifische Gewicht kann den Materialdatenblättern der Materiallieferanten entnommen werden.
Es ist wichtig zu beachten, dass das Schussgewicht durch Faktoren wie das Formdesign, die Materialschrumpfung und die Leistungsfähigkeit der Spritzgießmaschine beeinflusst werden kann. Spritzgießmaschinen werden in der Regel nach ihrer maximalen Schussgröße bewertet, die die maximale Materialmenge darstellt, die sie in einem einzigen Schuss einspritzen können.
Schusskapazität
Der Begriff „Schusskapazität“ bezieht sich beim Spritzgießen typischerweise auf die maximale Materialmenge, die eine Spritzgießmaschine in einem einzigen Schuss einspritzen kann. Dies ist ein entscheidender Parameter, da er die Größe und Komplexität der herstellbaren Teile beeinflusst. Die Schusskapazität wird häufig vom Hersteller der Spritzgießmaschine angegeben.
Die Formel für die Schusskapazität lautet:
Schusskapazität = Max. Einspritzhub × Schneckenquerschnittsfläche
Hier:
Maximaler Injektionshub
Der maximale Injektionshub ist die maximale Distanz, die die Injektionsschnecke während der Injektionsphase zurücklegen kann. Dazu gehören natürlich ein Hohlraum, ein Angusskanal und ein Kissen, das sollten Sie berechnen.
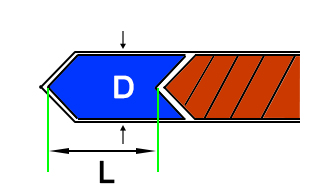
Schraubenquerschnittsfläche
Die Schneckenquerschnittsfläche ist die Querschnittsfläche der Einspritzschnecke. Sie wird mit der Formel für die Fläche eines Kreises (π×(Radius) 2 )/4 berechnet, wobei der Radius der Hälfte des Schraubendurchmessers entspricht.
Es ist wichtig zu beachten, dass die Schusskapazität von Faktoren wie dem Design der Einspritzeinheit, der Größe der Schnecke und den Gesamtspezifikationen der Maschine beeinflusst wird. Die maximale Schusskapazität wird häufig in den technischen Spezifikationen der Spritzgießmaschine angegeben.
Injektionszyklus
Der Spritzgießzyklus bezeichnet den vollständigen Ablauf von Ereignissen und Phasen, die bei der Herstellung eines Formteils mit einer Spritzgießmaschine ablaufen. Der Zyklus besteht aus mehreren Phasen mit jeweils spezifischen Aufgaben und Zwecken. Es umfasst hauptsächlich Formklemmung, Einspritzung, Packpresse, Kühlung/Zuführung und Auswurf. Weitere Schritte, die nicht sehr kritisch sind, werden vorerst nicht besprochen.
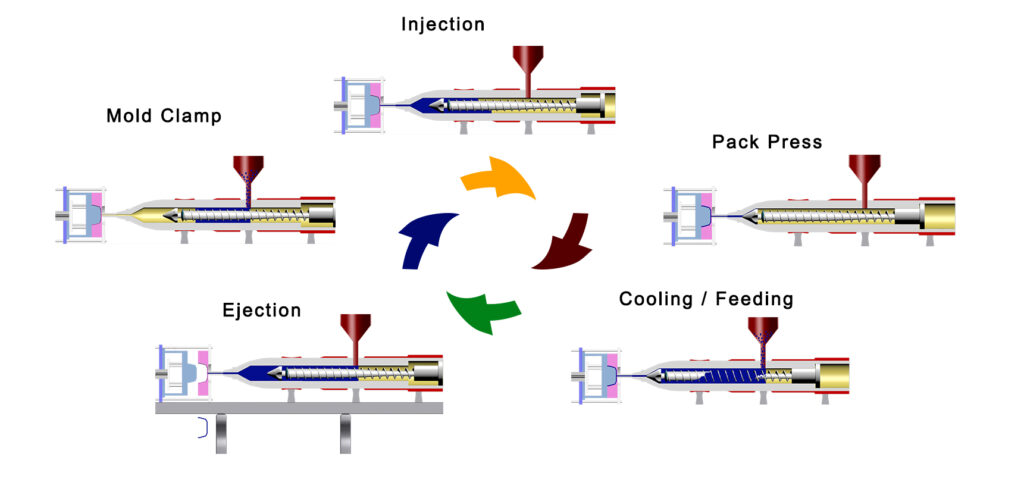
Hier noch ein paar Fachbegriffe.
Formenschließen
„Formschließen“ ist einer der Schlüsselschritte im Spritzgießzyklus. Es bezieht sich auf den Vorgang des Schließens der beiden Formhälften (allgemein bekannt als Form-„Spannung“) vor dem Einspritzen von geschmolzenem Kunststoffmaterial. Um dem Druck des eingespritzten Materials standzuhalten und die präzise Formung des Formteils zu gewährleisten, muss die Form sicher verschlossen sein.
Die Formschließphase umfasst die folgenden Schritte:
- Ausrichtung: Die beiden Formhälften, die auf der beweglichen und der stationären Aufspannplatte der Spritzgießmaschine montiert sind, sind richtig ausgerichtet.
- Schließen: Die bewegliche Aufspannplatte, die oft an der beweglichen Formhälfte befestigt ist, bewegt sich auf die stationäre Aufspannplatte zu und bringt die beiden Formhälften zusammen. Mit Hilfe einer Schließeinheit wird die Form sicher verschlossen.
In der tatsächlichen Produktion ist eine langsame Bewegung zum Zeitpunkt des endgültigen Schließens der Form erforderlich, weil Bedenken hinsichtlich einer Beschädigung der Form durch schlechte Formtrennung oder Gratbildung am geformten Produkt bestehen.
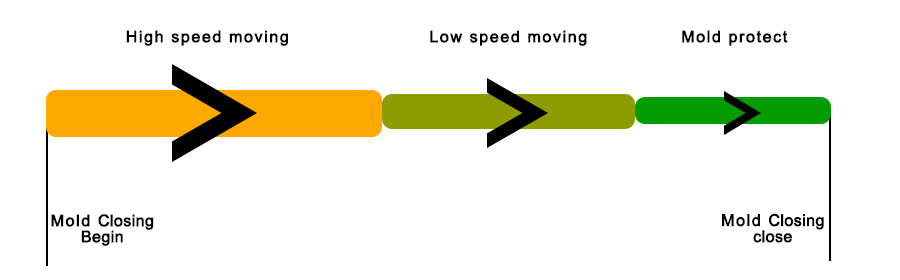
Formenspannung
Das Spannen der Form ist ein kritischer Schritt im Spritzgussprozess, bei dem die beiden Hälften der Form, die sogenannte stationäre Hälfte (feste Aufspannplatte) und die bewegliche Hälfte (bewegliche Aufspannplatte oder Stößel), sicher geschlossen und befestigt werden, um einen abgedichteten Hohlraum zu schaffen das Einspritzen von geschmolzenem Kunststoffmaterial. [ 15 ]
Der Klemmvorgang ist wichtig, um die strukturelle Integrität der Form aufrechtzuerhalten und das Austreten von geschmolzenem Material während des Einspritzens zu verhindern.
Düsenvorschub
Nachdem der Typ geschlossen ist, unterstützt er die Kraft der Form, um zu verhindern, dass die Form durch den Druck des fließenden Harzes gedrückt wird, wodurch die Düse beim Spritzgießen entstehen kann.
Plastifizierung
Wenn das Harz in der Form aushärtet, beginnt in der Spritzgießmaschine die Phase des Harzschmelzens als Vorbereitung für den nächsten Einspritzzyklus. (einschließlich der Dosierstufe)
Das Kunststoffmaterial wird durch einen Einfüllstutzen zum beheizten Zylinder der Maschine gefördert. Im Inneren des Zylinders befindet sich eine rotierende Schraube, die mehreren Zwecken dient. Die vom Zylinder erzeugte Wärme und die mechanische Energie der rotierenden Schnecke wirken zusammen, um das Kunststoffmaterial zu schmelzen. Durch den Schmelzprozess werden die festen Kunststoffpellets in einen geschmolzenen Zustand überführt.
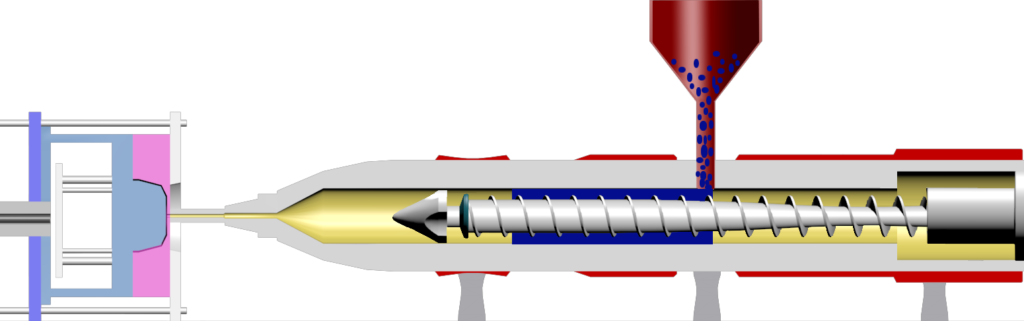
Injektion
Nachdem die Düse und die Angussbuchse miteinander verbunden sind, bewegt sich die Einspritzschnecke nach vorne, um geschmolzenes Harz in die Form zu transportieren.
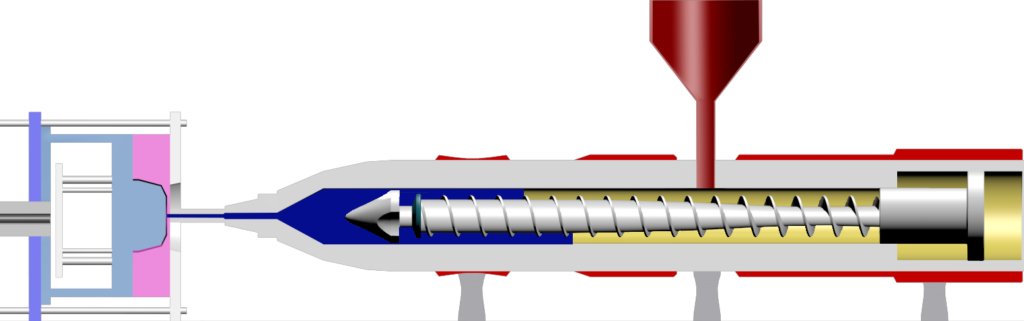
Halten
Unter Unterdruck versteht man im Kontext des Spritzgießens den Druck, der nach der Einspritzphase und vor dem Öffnen der Form auf das geschmolzene Kunststoffmaterial im Formhohlraum aufrechterhalten wird. Diese Phase wird allgemein als Halte- oder Verweilphase bezeichnet. Der Nachdruck ist ein kritischer Parameter im Spritzgussprozess und dient mehreren wichtigen Zwecken: Kompensation von Schrumpfungen, Vermeidung von Einfallstellen und Verhinderung des Einfrierens des Angusses.
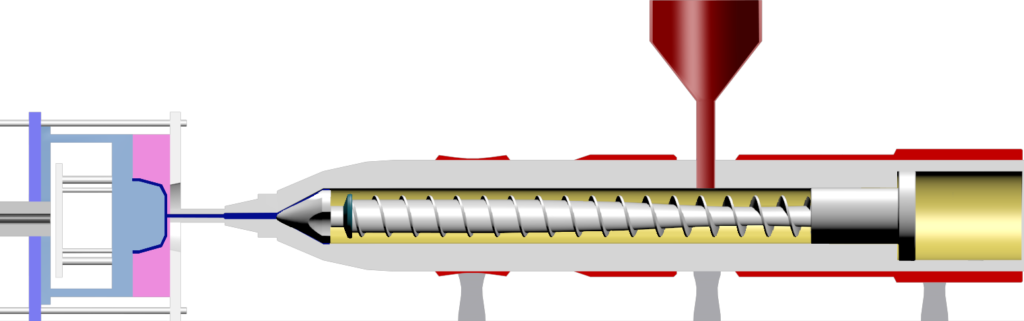
Kühlung
Im Kontext des Spritzgießens bezieht sich „Abkühlung“ auf die Phase im Formzyklus, in der das geschmolzene Kunststoffmaterial, das in den Formhohlraum eingespritzt wurde und die Form des gewünschten Teils angenommen hat, abkühlen und erstarren kann. Die Kühlung ist ein entscheidender Schritt im gesamten Spritzgussprozess und beeinflusst maßgeblich die Qualität, Abmessungen und mechanischen Eigenschaften des endgültigen Formteils.
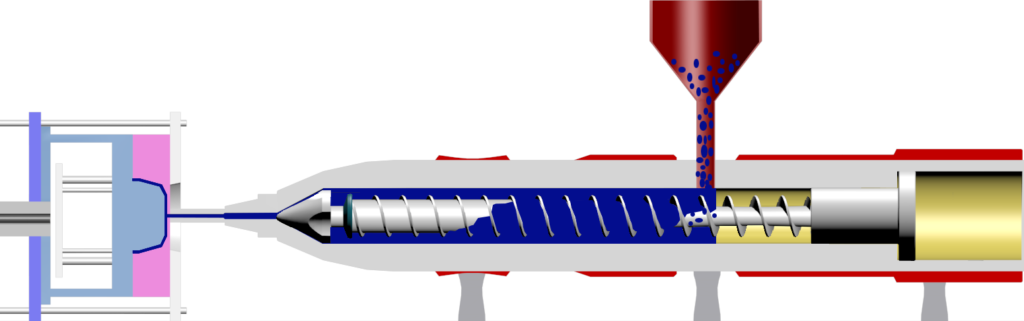
Düsenrückzug
Während des Abkühlvorgangs des geformten Harzes soll verhindert werden, dass sich das Harz aufgrund der Abkühlung der Form verfestigt. Die Düse wird zurückgezogen, der Kontakt zwischen der Düse und der Angussbuchse gelöst und die nächste Spritzgussphase vorbereitet. (Sie können es weglassen, wenn Sie keine Bedenken hinsichtlich der Düsenverfestigung haben)
Es hat andere Funktionen als der Düsenvorschub.
Der spezifische Zeitpunkt und die Bewegung des Düsenrückzugs können programmiert und gesteuert werden, um den Spritzgussprozess für die spezifischen Anforderungen des zu produzierenden Materials und Teils zu optimieren. Fortschrittliche Spritzgießmaschinen verfügen häufig über Funktionen, die eine präzise Steuerung der Düsenbewegung und anderer Parameter ermöglichen und so zur Herstellung hochwertiger Formteile beitragen.
Öffnen und Auswerfen der Form
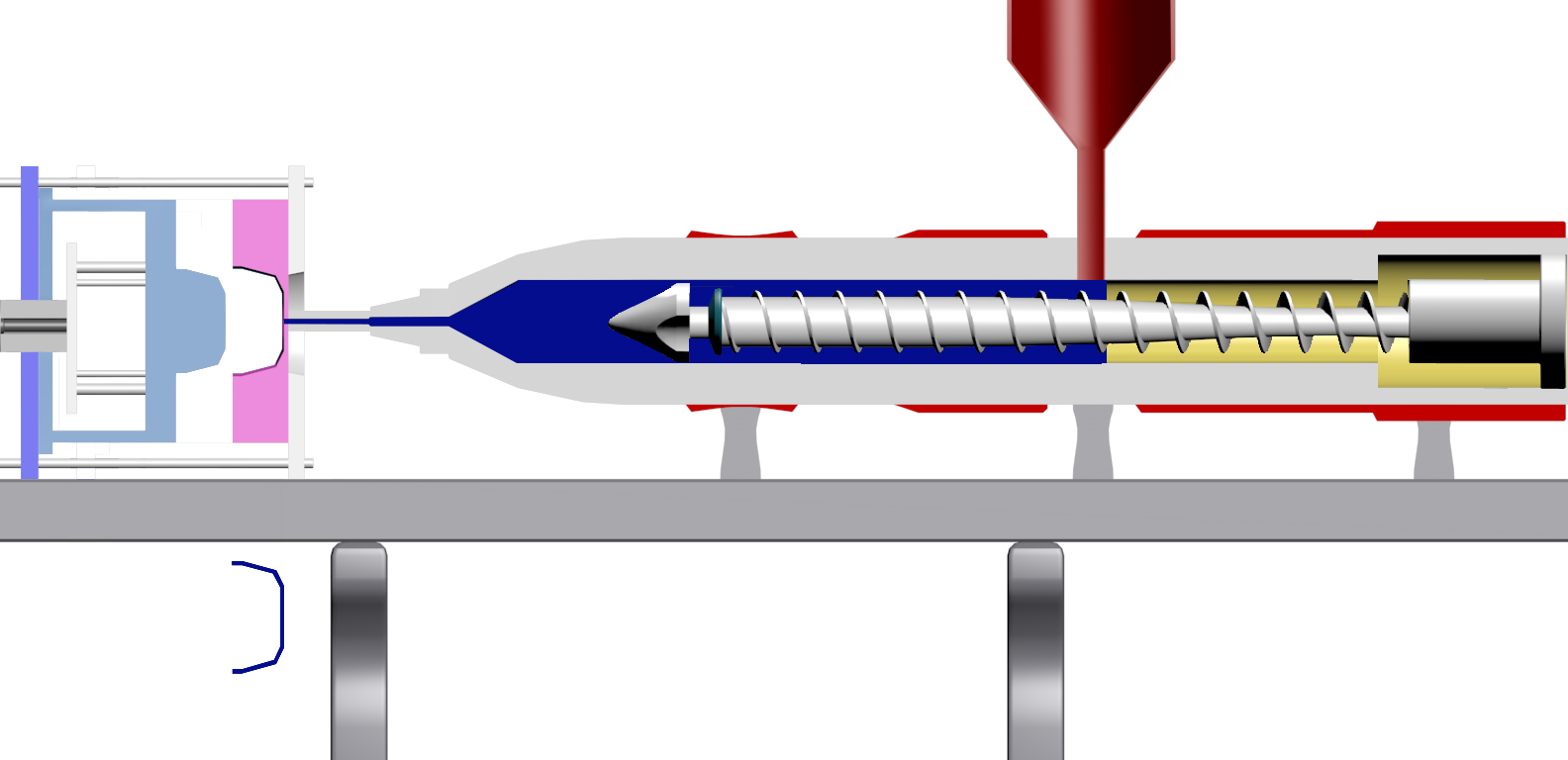
Nachdem das Harz ausgehärtet ist und die Form geöffnet ist, bewegt sich der Auswerferstift auf der festen Seite, um das Produkt aus der Form auszuwerfen.
Zu den wichtigsten Punkten in Bezug auf die Auswurfphase beim Spritzgießen gehören Auswerferstifte, Auswerfersystem, Überlegungen zum Teiledesign, Zykluszeitoptimierung und Teilehandhabung.
Wichtige Punkte der Spritzgussbedingungen
Grundlagen zum Festlegen der anfänglichen Formbedingungen
1) Temperatur: So niedrig wie möglich einstellen (um Zersetzung zu verhindern und die Zykluszeit zu verkürzen)
2) Druck: Einspritzdruck, Kompensationsdruck und Gegendruck sind alle auf niedrig eingestellt (um Formschäden durch Überpacken zu verhindern).
3) Verpackungsdruck: Halten Sie die Einstellung hoch (um Grate zu vermeiden und die Sicherheit der Ausrüstung zu gewährleisten).
4) Geschwindigkeit
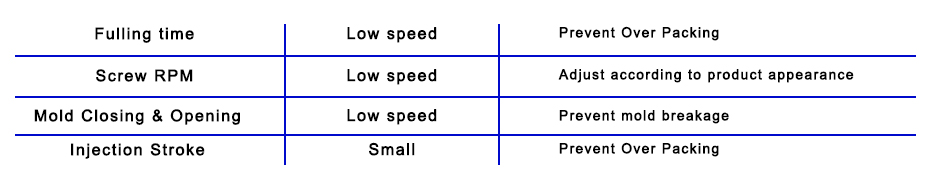
5) Zeit
Wenn das Material abkühlt, dauert es besonders während der Druckhaltephase lange, bis der Anschnitt dicht ist.
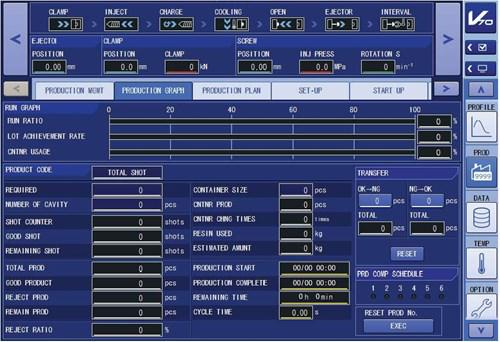
Stufenspritzguss (Mehrstufenspritzguss)
Prinzip:
- Spritzen Sie den Kleber beim ersten Einspritzen mit niedriger Geschwindigkeit ein, bewegen Sie die Düse zum Kopf des kalten Rohlings und erhöhen Sie dann die zweite Einspritzgeschwindigkeit, um den Formhohlraum zu füllen und so die Zeit zu verkürzen, die der Kunststoff bis zum Ende des Anschnitts fließt dass die Viskosität des Kunststoffs beim Befüllen auf einem Minimum gehalten und verfestigt werden kann. Es ist jedoch schwierig, den richtigen Druckhalte-Schaltpunkt für eine Hochgeschwindigkeitseinspritzung zu steuern, daher muss eine mehrstufige Verzögerung verwendet werden, um den Druckhalte-Schaltpunkt effektiv zu steuern.
- Das Funktionsprinzip der segmentierten Einspritzung: Die elektrooptische Steuerung wird verwendet, um das Durchflussproportionalventil im Hydrauliksystem anzuweisen, sofort die Einspritzgeschwindigkeit an einem Punkt zu erreichen, um die segmentierte Einspritzgeschwindigkeit zu erreichen.
Methode zur Einstellung der Spritzgussgeschwindigkeit:
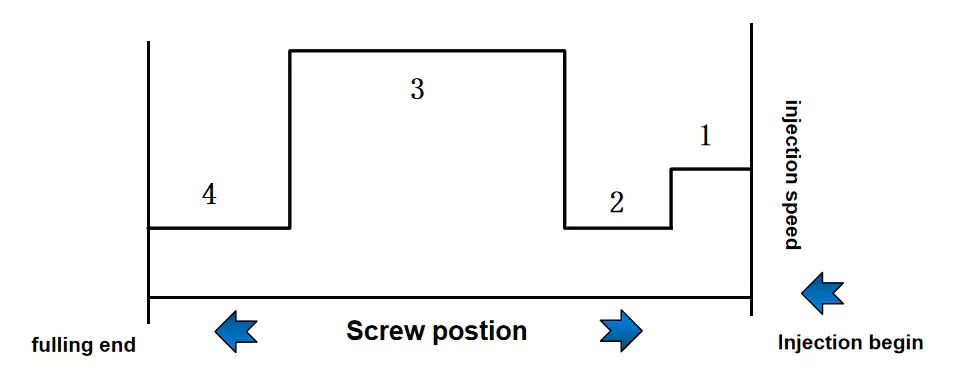
1)
Angusskanalabschnitt: hohe
Geschwindigkeit im Frühstadium bis mittlere Geschwindigkeit in
der Massenproduktion (um Erstarrung und Überhitzung zu
verhindern).
2)
Klebereinlass: niedrige
Geschwindigkeit (verhindert Spritzen, Silberstreifen usw.).
3)
Formteil: Hohe
Geschwindigkeit (Verhinderung von Fließmarken und
Schweißnähten).
4)
Druckhalteteil: niedrige
Geschwindigkeit (Gas, Grat usw. werden reduziert, und die
Schaltposition des Haltedrucks ist wichtig).
Spritzgießgeschwindigkeitsfunktion
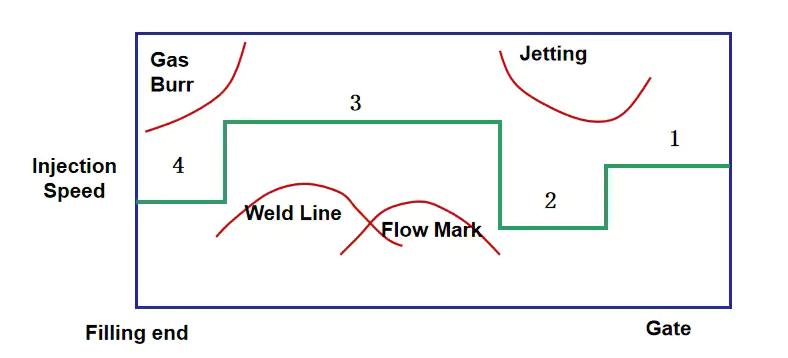
1) Um Jetting oder Silver
Streak um das Tor herum zu verhindern, muss die Geschwindigkeit
niedrig sein.
2) Um Fließmarkierungen oder
Schweißnähte zu vermeiden, ist eine hohe Geschwindigkeit
erforderlich.
3) Um Gasverbrennungen oder
Grate zu verhindern, sind mittlere und niedrige
Geschwindigkeiten und sicheres Schalten erforderlich.
Haltezustand
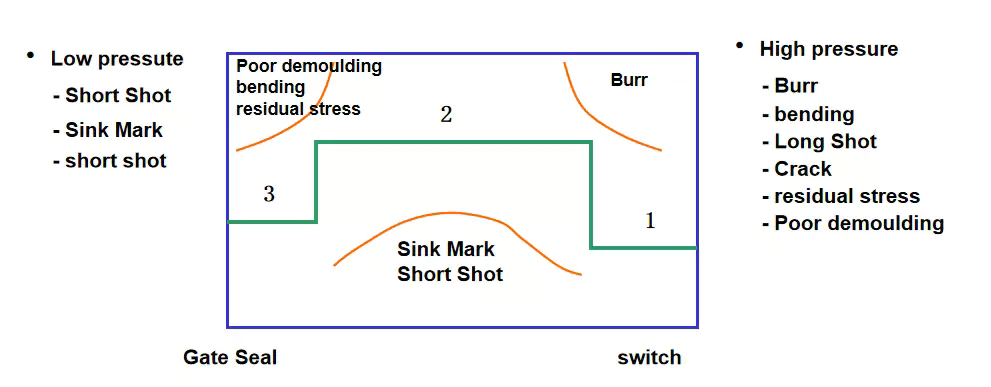
1)
Um Grate zu vermeiden,
verwenden Sie einen niedrigen Druck.
2)
Um zu verhindern, dass die
Einfallstelle oder die eingestellte Zahl kleiner wird, ist
Hochspannung erforderlich.
3)
Um Restspannungen zu
vermeiden, ist ein niedriger Druck erforderlich.
Druckverteilung innerhalb der Form während des Spritzgießprozesses
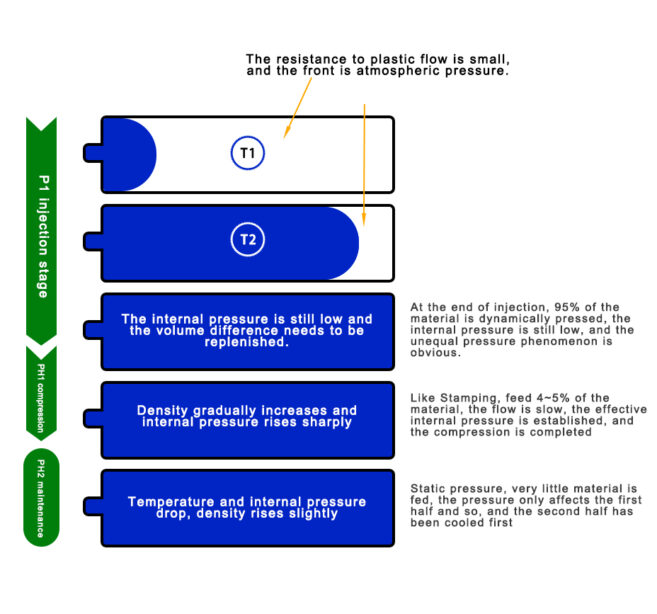
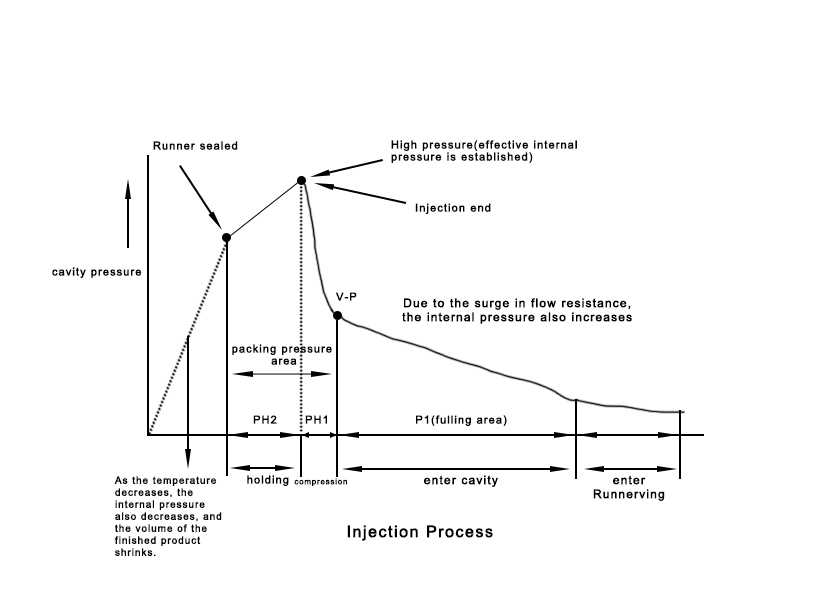
Druckänderungen im Hohlraum bei V/P-Umschaltung
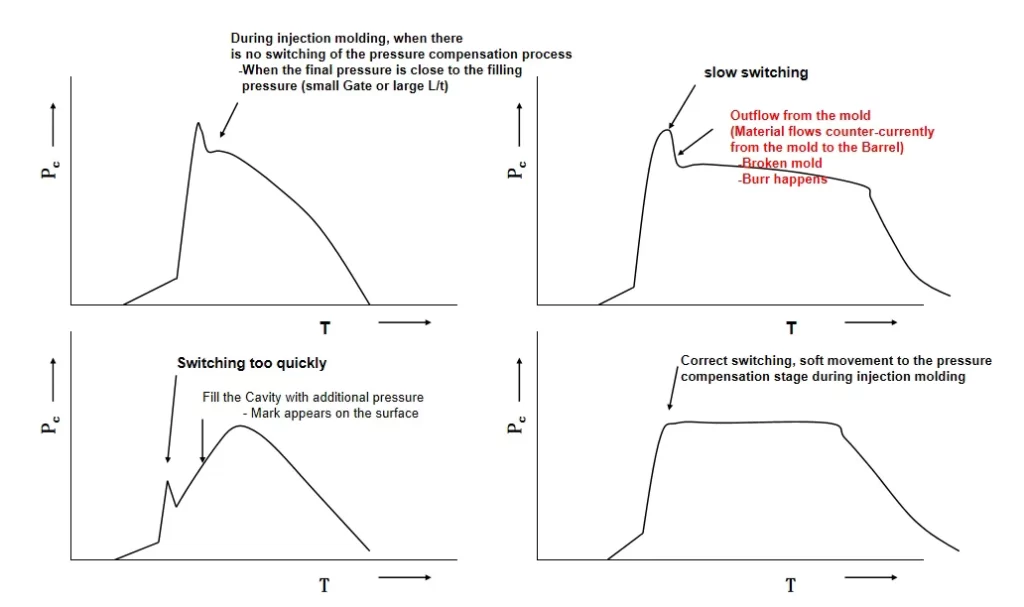
Einfluss der Spritzgussbedingungen auf die Schrumpfrate
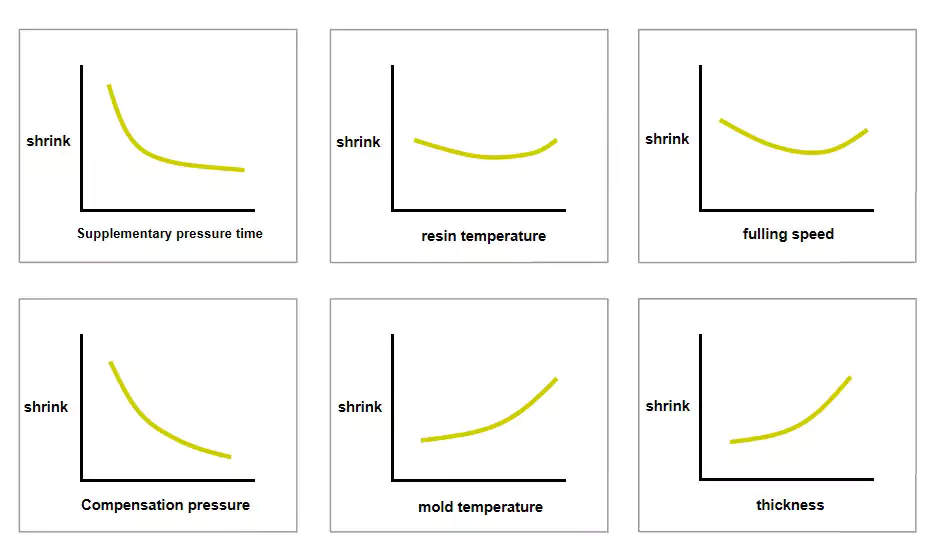
Optimierung des Spritzgussprozesses:
Verkürzen Sie durch die anfänglichen Abbindebedingungen beim Spritzgießen die Abbindezeit und die Anzahl der Formversuche.
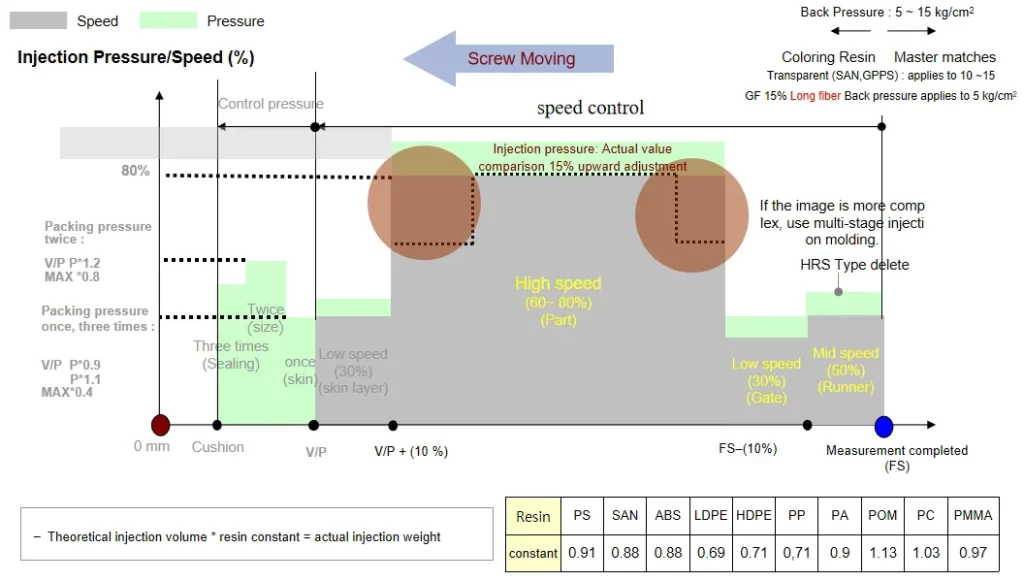
Verweise:
- [ 1 ] Z. Tadmor, Molekulare Orientierung beim Spritzgießen, J. Appl. Polym. Wissenschaft. 18 (6), S. 1753–1772, 1974. doi:10.1002/app.1974.07018061
- [ 2 ] M. Huszar et al. Der Einfluss von Strömungs- und thermischen Eigenschaften auf die Vorhersage von Einspritzdruck und Kühlzeit App Math Model (2016)
- [ 3 ] PC Roozemond et al. Modellierung der strömungsinduzierten Kristallisation in isotaktischem Polypropylen bei hohen Scherraten J Rheol (NYNY) (2015)
- [ 4 ] O. Ogorodnyk et al. Überwachung und Steuerung für das Spritzgießen von Thermoplasten, eine Übersicht Procedia CIRP (2018)
- [ 5 ] Druckanalyse beim dynamischen Spritzgießen und Prozessparameteroptimierung zur Reduzierung des Verzugs von Spritzgussprodukten Xinyu Wang, Hongxia Li, Junfeng Gu,2 Zheng Li, * Shilun Ruan, Changyu Shen und Minjie Wang
- [ 6 ] Optimieren Sie die Parameter des Spritzgussprozesses und bauen Sie ein adaptives Prozesskontrollsystem basierend auf dem Düsendruckprofil und der Schließkraft auf. Guan-Yan Liou, Wei-Jie Su, Feng-Jung Cheng, Chen-Hsiang Chang, Ren-Ho Tseng, Sheng-Jye Hwang, * Hsin-Shu Peng und Hsiao-Yeh Chu https://www.ncbi.nlm .nih.gov/pmc/articles/PMC9921389/
- [ 7 ] Schnelle Optimierung des Injektionsgeschwindigkeitsprofils basierend auf der Graphentheorie. Peng Zhao, Ding Yang, Huamin Zhou und Kai Xu
- [ 8 ] Huang, MS Kavitätsdruckbasierte Grauvorhersage des Füll-zu-Packungs-Umschaltpunkts beim Spritzgießen. J. Mater. Verfahren. Technol. 2007, 183, 419–424.
- [ 9 ] Huang, MS; Nian, SC; Chen, JY; Lin, CY Einfluss der Schließkraft auf die Dehnung der Verbindungsstange, die Formtrennung und die Teileabmessungen beim Spritzgießen. Präzise. Ing. 2018, 51, 647–658.
- [ 10 ] Handbuch zum Spritzgießen Dominick V. Rosato PE, Donald V. Rosato PH.D. & Marlene G. Rosato PE
- [ 11 ] Energy Management in Plastics Processing Strategies, Targets, Techniques, and Tools Book • Dritte Auflage • 2019
- [ 12 ] XIONG Wen nan, ZHANG Ya jun, JIN Zhi ming et al., „Research on Energy Consumption of Clamping Process of Injection Molding Machine Based on AMESim [J]“, Plastics, vol. 47, nein. 5, S. 122-125, 2018.
- [ 13 ]wissenschaftliche Methode zur Bestimmung der Abkühlzeit beim Spritzgießen mittels Infrarot-Thermografie Autor: Boud, Eric D
- [ 14 ] https://zeus.plmsc.psu.edu/~manias/MatSE447/17-22_Processing.pdf
- [ 15 ] Was ist Schließkraft beim Spritzgießen | FUTEK https://www.futek.com/applications/Injection-Molding-Force-Feedback
Der Basisleitfaden zur Spritzgussverarbeitung
von
fähigemachining
ist lizenziert unter
CC BY-NC 4.0