In diesem Artikel werden hauptsächlich verschiedene Gummiproduktionsprozesse vorgestellt. Naturkautschuk, Synthesekautschuk, thermoplastische Elastomere (TPE, TPU usw.), Silikonkautschuk und andere elastische Polymermaterialien sind alle in der Gummidefinition dieses Artikels enthalten.
Pökeln
Der Formprozess von Gummi hängt vom Aushärtungsprozess des Gummis ab. Heat Cured Rubber (HCR) wird auch als hochtemperaturvulkanisierender Silikonkautschuk (HTV) bezeichnet. Diese Art von Gummimaterial befindet sich vor dem Aushärten in einem Gel- oder Geleezustand mit hoher Plastizität und einer bestimmten Viskosität. Das Material weist nach dem Aushärten keine Plastizität auf, sondern ist lediglich elastisch und die Form verfestigt sich. Die Aushärtungsprozesse von Naturkautschuk, Synthesekautschuk und Festsilikon sind ähnlich und gehören zum Vulkanisations- oder vulkanisationsähnlichen Prozess. Durch Druckbeaufschlagung und Erhitzen stabilisiert eine kleine Menge Schwefel oder andere Vernetzungsmittel im Material die chemischen Vernetzungen in der Materialstruktur.
Eine andere Art von Elastomer ist LSR oder Flüssigsilikonkautschuk. Der Hauptunterschied zwischen LSR und HCR besteht in der flüssigen Natur der LSR-Materialien. Aufgrund seiner flüssigen Form ist das Spritzgießen das gebräuchlichste LSR-Formverfahren.
Das Formen thermoplastischer Elastomere unterscheidet sich geringfügig. Bei hohen Temperaturen weist dieses Material ähnliche Eigenschaften wie Thermoplaste auf. Bei Raumtemperatur weist es Eigenschaften auf, die denen von vulkanisiertem Gummi ähneln. Daher ist der Formungsprozess von thermoplastischen Elastomeren dem von Thermoplasten sehr ähnlich. Auch die verwendeten Technologien sind ähnlich, wie Spritzguss, Blasformen usw.
Typischer Arbeitsablauf beim Gummiformen
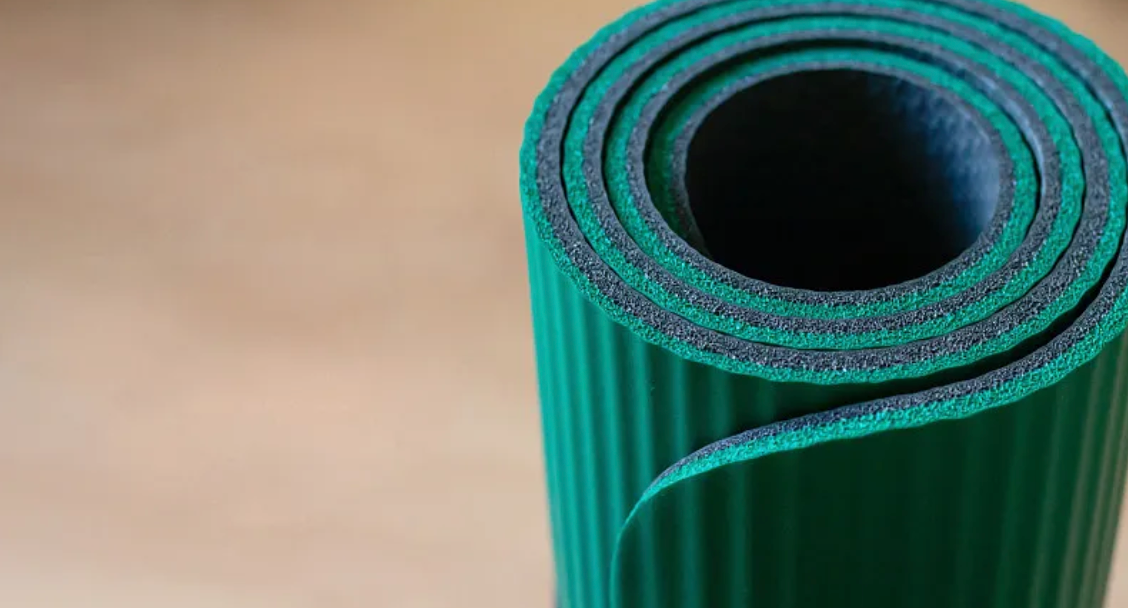
Es gibt 4 beliebteste Technologien zum Formen von Gummi, nämlich Spritzgießen, Formpressen, Spritzpressen und Gummiextrusion. Nehmen wir als Beispiel das Formpressen. Der typische Arbeitsablauf zur Herstellung geformter Gummiteile ist wie folgt:
1. Mischen
Die verschiedenen Rohstoffe, Gummimaterialien, Füllstoffe und Zusatzstoffe werden zu einer einheitlichen Mischung vermischt. Die genaue Rezeptur der Mischung kann je nach den gewünschten Eigenschaften des Endprodukts angepasst werden. Wir haben hier also einen unvulkanisierten Gummi.
2. Vorformen
Die Mischung wird in eine einfache Form vorgeformt, die dem Volumen des Endprodukts nahe kommt. Diese Vorformung trägt dazu bei, die Menge des benötigten Gummimaterials zu reduzieren und den Herstellungsprozess zu beschleunigen. Die vorgeformte Mischung ist hier noch ein unvulkanisierter Gummi.
3. Formpressen
Die vorgeformte Mischung wird in einen Formhohlraum gegeben und unter hohem Druck und Hitze komprimiert. Hier findet die Vulkanisation statt und verfestigt das Gummimaterial in der gewünschten Form.
3. Nachhärten
Das Endprodukt wird nachgehärtet, um seine Eigenschaften weiter zu verbessern. Bei diesem Schritt wird das Produkt stundenlang in einem Ofen oder einer anderen Heizquelle erhitzt, um die Bindung zwischen den Gummimolekülen zu stärken.
Die 4 beliebtesten Gummiformverfahren
Formpressen

Wie bereits beschrieben, werden beim Formpressverfahren unvulkanisierte Gummivorformlinge in die Form eingelegt. Anschließend wird die Form erhitzt, der Gummi vulkanisiert und nimmt die Form des Endprodukts an.
Die Kompressionsform ist im Vergleich zu anderen Gummiformverfahrensformen viel einfacher. Auch der Maschinenpark ist viel einfacher. Die geringen Investitionen sowohl in Maschinen als auch in Formen machen es zum beliebtesten Gummiformverfahren, insbesondere für kundenspezifisch geformte Gummiprodukte. Aufgrund der geringen Investition eignet sich das Verfahren auch für die Produktion kleiner Stückzahlen.
Der Nachteil dieser Technologie ist die lange Zykluszeit. Die Herstellung eines Vorformlings braucht Zeit. Bei einer Großserienproduktion könnte dies zu hohen Kosten führen. Auch die Präzision der Teilegröße ist nicht so gut wie bei anderen Technologien. Formpressen ist für einfache oder grundlegende Designs und große Gummiformteile effizienter.
Spritzgießen
thermoplastische Elastomere
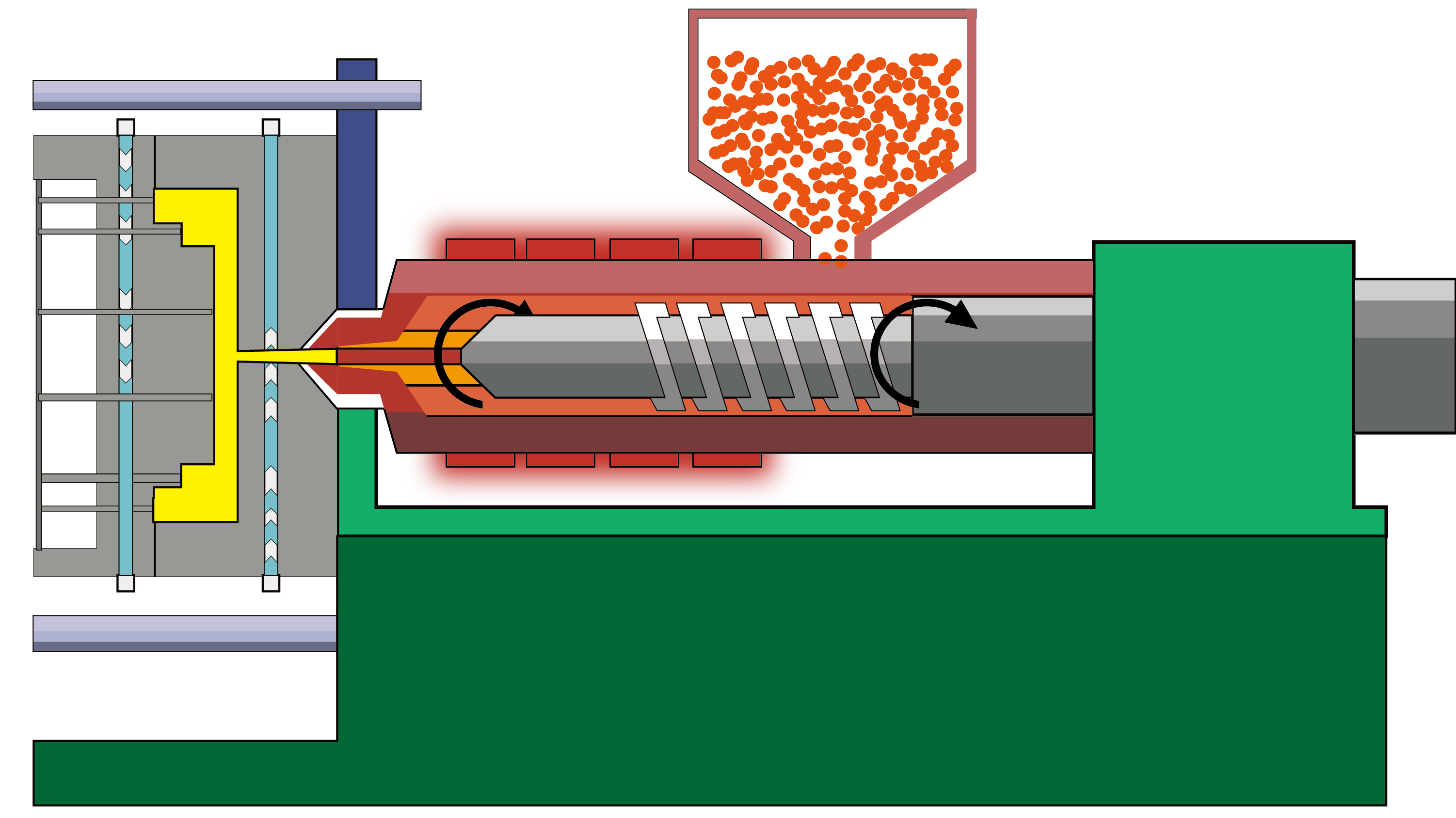
Das Spritzgießen thermoplastischer Elastomere ist im Wesentlichen dasselbe wie das Spritzgießen thermoplastischer Elastomere. Das Material wird in Form von Pellets durch einen Trichter geleitet, zu einer Flüssigkeit erhitzt, in eine Form eingespritzt und abgekühlt, um sich zu verfestigen. Wie bei Thermoplasten können auch Umspritzen und Umspritzen realisiert werden.
HCR
Beim HCR-Spritzgießen wird eine abgemessene Menge unvulkanisierten Gummis in einen Trichter oder ein kontinuierlicher Streifen Rohgummi in die Spritzgießmaschine eingespeist. Der Rohkautschuk wird erhitzt und von einer rotierenden Schneckenstange durch den Zylinder in die Formhohlräume gedrückt. Die Vulkanisation erfolgt sowohl im Zylinder als auch in den Formhohlräumen.
LSR

Flüssigsilikonkautschuk Beim (LSR)-Spritzgießen wird unbeheiztes, flüssiges oder viskoses Material verwendet. Es wird über eine Düse und mit Hilfe von Druck in einen geschlossenen und beheizten Formhohlraum dosiert. Diese Technik ermöglicht einen schnellen Herstellungsprozess und eignet sich daher ideal für Produktionsläufe mit hohen Stückzahlen. Die Rohstoffgewinnung erfolgt bequem direkt aus Fässern oder Eimern über eine Dosiereinheit mit minimaler Vorlaufzeit. Das Rohmaterial kann eine vorgemischte Flüssigkeit oder zwei verschiedene flüssige Komponenten sein, die vor dem Einbringen in die Form gründlich gemischt werden. Ein weiterer Unterschied zwischen dem LSR-Formverfahren und dem HCR-Formverfahren besteht darin, dass das Material vor dem Eintritt in den Formhohlraum nicht erhitzt werden muss.
Spritzgussformen sind komplizierter als Kompressionsformen und daher teurer. Der Einspritzzyklus umfasst jedoch nicht die Herstellung von Vorformen. Der Aushärtungsprozess des HCR-Spritzgießens beginnt, bevor das Material in die Formhohlräume gelangt, sodass der Prozess viel kürzere Zykluszeit und damit Zykluskosten hat. Das Spritzgussverfahren führt zudem zu einer besseren Präzision. Dieses Verfahren eignet sich besser für Produkte mit großen Chargen, komplexen Formen oder präzisen Größenanforderungen.
Spritzguss
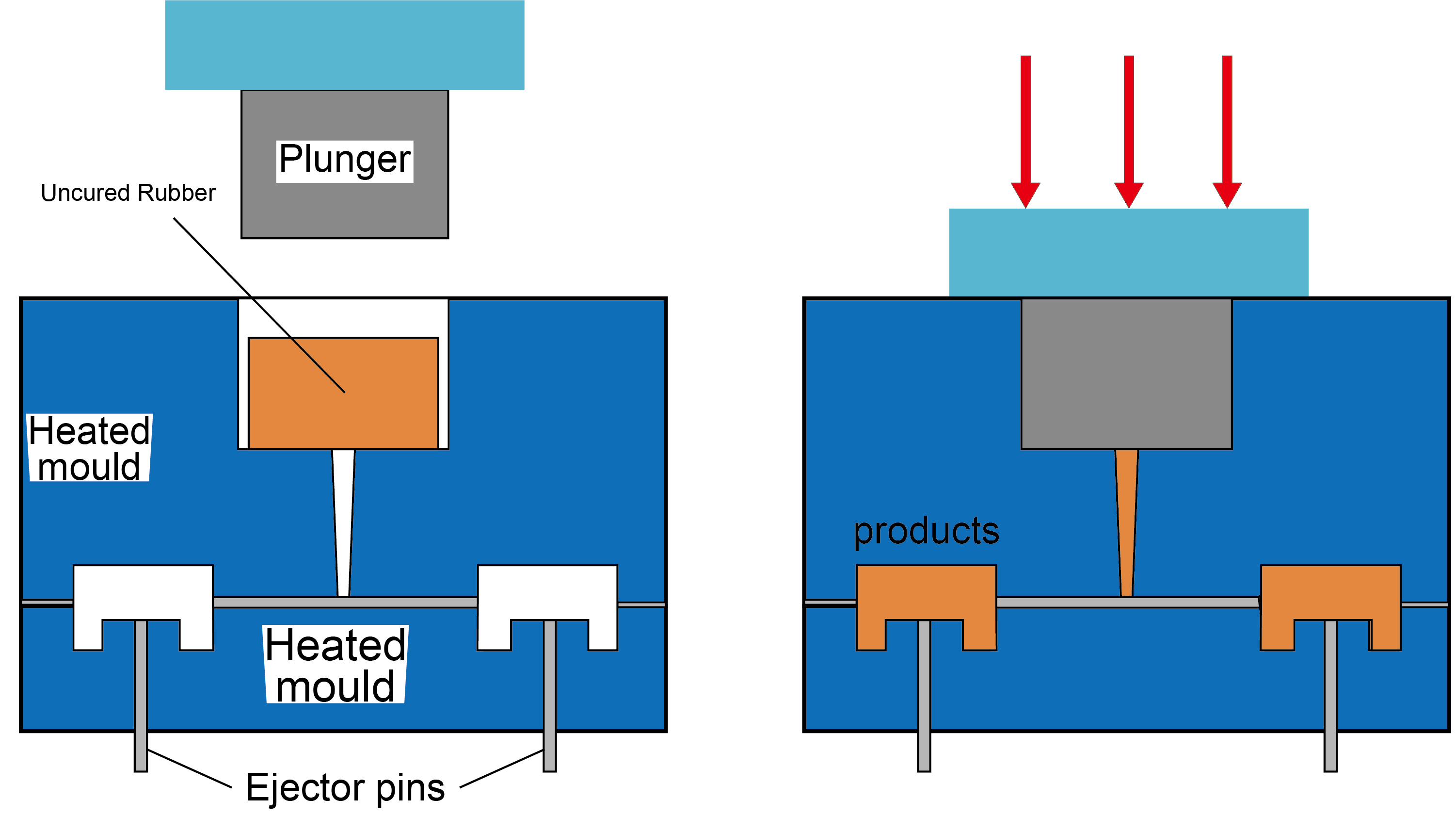
Das Transferformen ähnelt dem Formpressen, außer dass das Material in einer separaten Kammer und nicht innerhalb der Kavität unter Druck gesetzt wird. Die Druckbeaufschlagung und das erzwungene Einführen über eine schmale Öffnung verbessern die Temperaturverteilung des Materials und sorgen für schnellere Vernetzungsreaktionszeiten mit weniger Verformung des Endprodukts. Dadurch können aufgrund der größeren Fließfähigkeit des Materials auch kompliziertere Formen hergestellt werden, was im Vergleich zu anderen Methoden zu kürzeren Zykluszeiten führt.
Die Investitionen in Formen und mechanische Ausrüstung für diesen Prozess sind geringer als beim Spritzgießen und die Präzision des Produkts ist höher als die beim Formpressen. Obwohl keine Vorformen hergestellt werden müssen, muss in jedem Zyklus eine bestimmte Menge Rohkautschuk hinzugefügt werden, und die Zykluszeit ist länger als die des Spritzgussverfahrens. Es eignet sich für die Herstellung von Präzisionsteilen in kleinen oder mittleren Serien.
Gummiextrusion
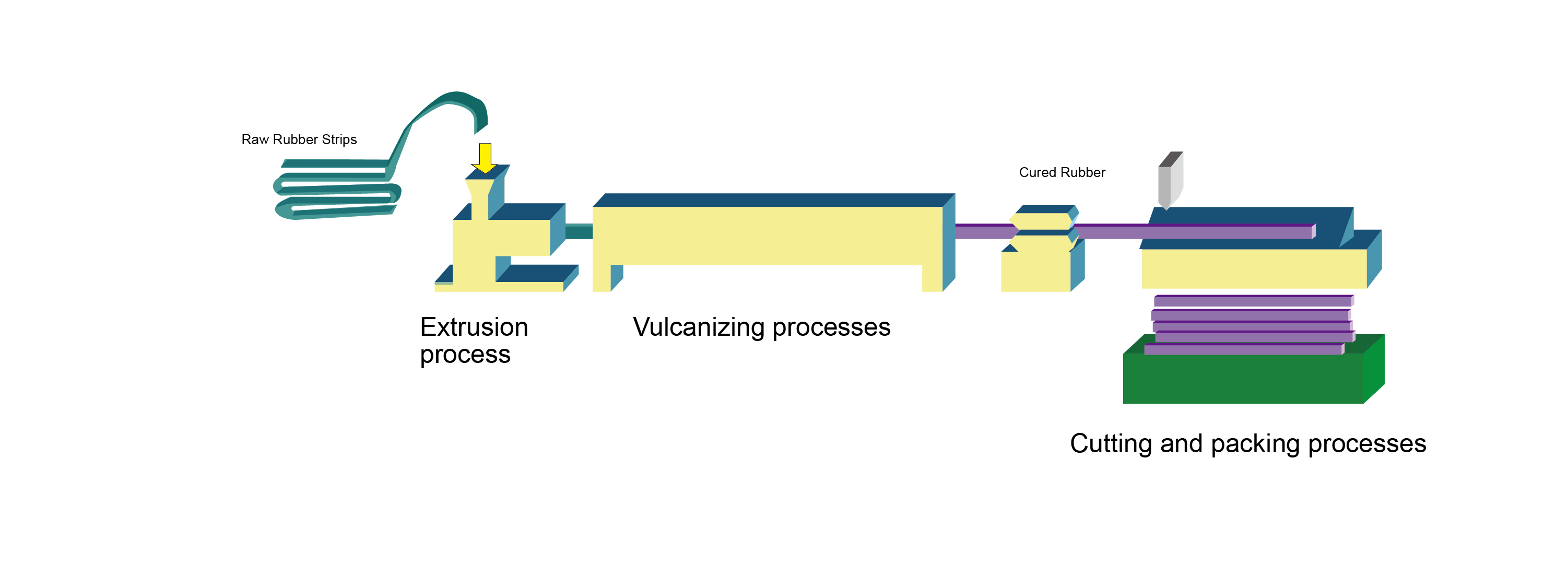
Gummiextrusion ist ein Verfahren zur Herstellung von Gummiprodukten. Dabei wird synthetischer oder natürlicher, unvulkanisierter Gummi durch eine Extrusionsmaschine geleitet, die über eine geformte Düse und ein unter Druck stehendes Förderband verfügt. Während des Extrusionsprozesses wird das Material erhitzt und erweicht, um es geschmeidig zu machen, bevor es durch die Düse gedrückt wird und seine endgültige Form annimmt.
Die Gummiextrudermaschine besteht aus zwei Hauptteilen: einer Scherschnecke, die das Rohmaterial beim Hinzufügen von Verbindungen entlang des Förderers schiebt; und eine Matrize, in die das erweichte, gefaltete Material gedrückt wird. Nachdem das Werkstück seine endgültige Form erreicht hat, wird es vulkanisiert, um es zu einem verwendbaren Produkt zu härten.
Dieses Verfahren eignet sich zur Herstellung großer, länglicher Gummiteile mit gleichmäßigen Querschnitten. Formen sind relativ preiswert. Wird häufig zur Herstellung von Dichtungsbändern oder Gummischläuchen verwendet.
Vergleich der Gummiformverfahren:
Formkosten:
Gummispritzguss: Hoch
Rubber Transfer Moulding: Niedrig bis mäßig
Gummikompressionsformung: Niedrig
Gummiextrusion: Gering bis mäßig
Zykluszeit:
Gummispritzguss: Am schnellsten
Rubber Transfer Moulding: Langsamer als Spritzguss
Gummikompressionsformen: Die langsamste aller Optionen
Gummiextrusion: Schneller als Formpressen, aber langsamer als Spritz- und Transferformen.
Toleranz/Wiederholbarkeit:
Gummispritzguss: Hervorragende Toleranz und Wiederholbarkeit
Rubber Transfer Moulding: Gute Toleranz und Wiederholbarkeit
Gummi-Kompressionsformen: Faire Toleranz und Wiederholbarkeit
-Gummiextrusion: Gute Toleranz; begrenzte Wiederholbarkeit
Andere Gummiherstellungsprozesse
Kalandrieren von Gummi ist ein mechanischer Prozess, bei dem rohes Gummimaterial zwischen einer oder mehreren erhitzten Stahlwalzen gepresst wird, um Platten mit gleichmäßiger Dicke zu bilden. Anschließend wird der Gummi ausgehärtet. Diese Rollen, sogenannte Kalender, können in Druck und Geschwindigkeit angepasst werden, um unterschiedliche Oberflächenbeschaffenheiten und Texturen wie glänzende oder matte Oberflächen, Glätte und Haftung zu erzielen. Die resultierenden Platten werden dann entweder direkt verwendet oder zu Endprodukten weiterverarbeitet. Darüber hinaus können diese langen Endlosfolien über Trägerstoffe oder Laminierung auf Folien mit anderen Materialien kombiniert werden.
Blasformen ist ein Herstellungsverfahren zur Herstellung hohler Kunststoffteile sowie von Gegenständen wie Flaschen. Bei der Gummiherstellung kann das Verfahren auf thermoplastische Elastomere angewendet werden, um Schläuche, Rohre oder andere hohle Gummiteile herzustellen.
Dieser Prozess beginnt mit dem Erhitzen des Vorformlings (ein röhrenförmiges Stück Plastik mit einem Loch an einem Ende), bis er weich wird. Die erweichten thermoplastischen Elastomere werden dann in eine Form gegeben und durch das Loch wird unter hohem Druck Luft hineingeblasen, wodurch sich das Material der Form der Form anpasst. Sobald das Teil abgekühlt und ausgehärtet ist, wird es aus der Form entnommen, wobei Wasserkanäle dabei helfen, die Temperatur schneller zu senken.
CNC-VERARBEITUNG kann auch auf Gummiprodukte angewendet werden. Es eignet sich gut für vulkanisierte Gummimaterialien mit relativ hoher Härte.
Gummimaterialoptionen für die Gummiformung
Die Palette der in der Branche verfügbaren Gummimaterialien ist umfangreich und vielfältig, wobei jeder Typ unterschiedliche Eigenschaften besitzt, die ihn für bestimmte Anwendungen geeignet machen. In diesem Abschnitt geben wir einen kurzen Überblick über einige der am häufigsten verwendeten Arten verschiedener Gummimischungen.
Naturkautschuk (NR)
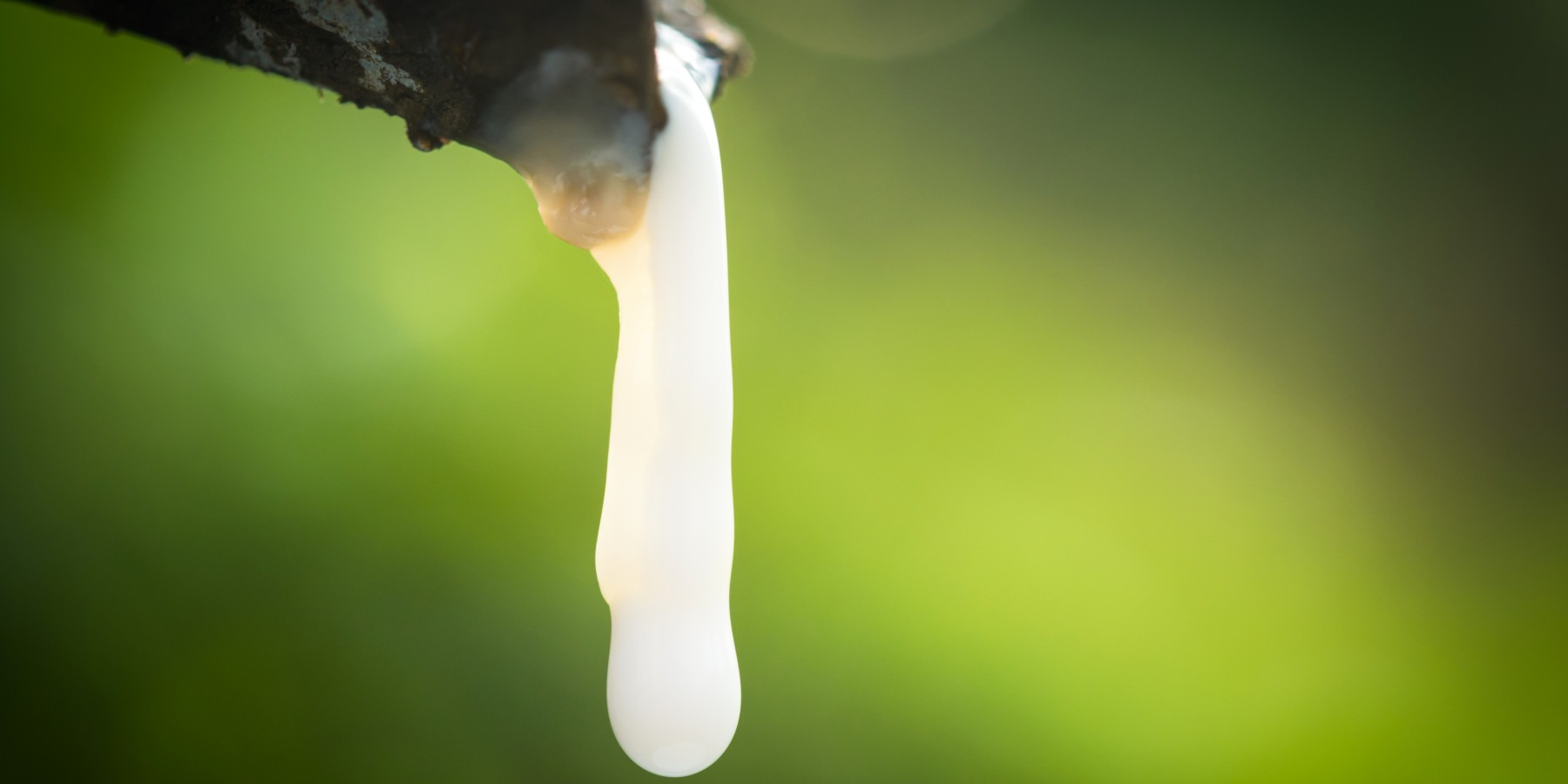
Naturkautschuk ist ein flexibles, widerstandsfähiges und langlebiges Material, das aus dem Latex des Hevea brasiliensis-Baums gewonnen wird. Es verfügt über eine gute Abriebfestigkeit, eine hohe Zugfestigkeit und eine gute Reißfestigkeit. Es wird häufig für Reifen, Förderbänder und Schuhe verwendet.
Styrol-Butadien-Kautschuk (SBR)
SBR ist ein synthetischer Kautschuk, der durch die Kombination von Styrol und Butadien hergestellt wird. Es weist eine gute Abriebfestigkeit, eine ausgezeichnete Elastizität und eine gute Flexibilität auf. Es wird häufig für Autoreifen, Förderbänder und Schuhsohlen verwendet.
Nitrilkautschuk (NBR)
NBR ist ein synthetischer Kautschuk, der durch Copolymerisation von Butadien und Acrylnitril hergestellt wird. Es verfügt über eine ausgezeichnete Ölbeständigkeit, gute Abriebfestigkeit und gute Zugfestigkeit. Es wird häufig für Öldichtungen, Dichtungen und Schläuche verwendet.
EPDM Gummi
EPDM ist ein synthetischer Kautschuk, der durch Copolymerisation von Ethylen, Propylen und einer kleinen Menge Dienmonomer hergestellt wird. Es verfügt über eine ausgezeichnete Witterungsbeständigkeit, gute chemische Beständigkeit und gute elektrische Isolationseigenschaften. Es wird häufig für Dichtungsstreifen im Automobilbereich, Dachbahnen und elektrische Isolierungen verwendet.
Silikon-Gummi
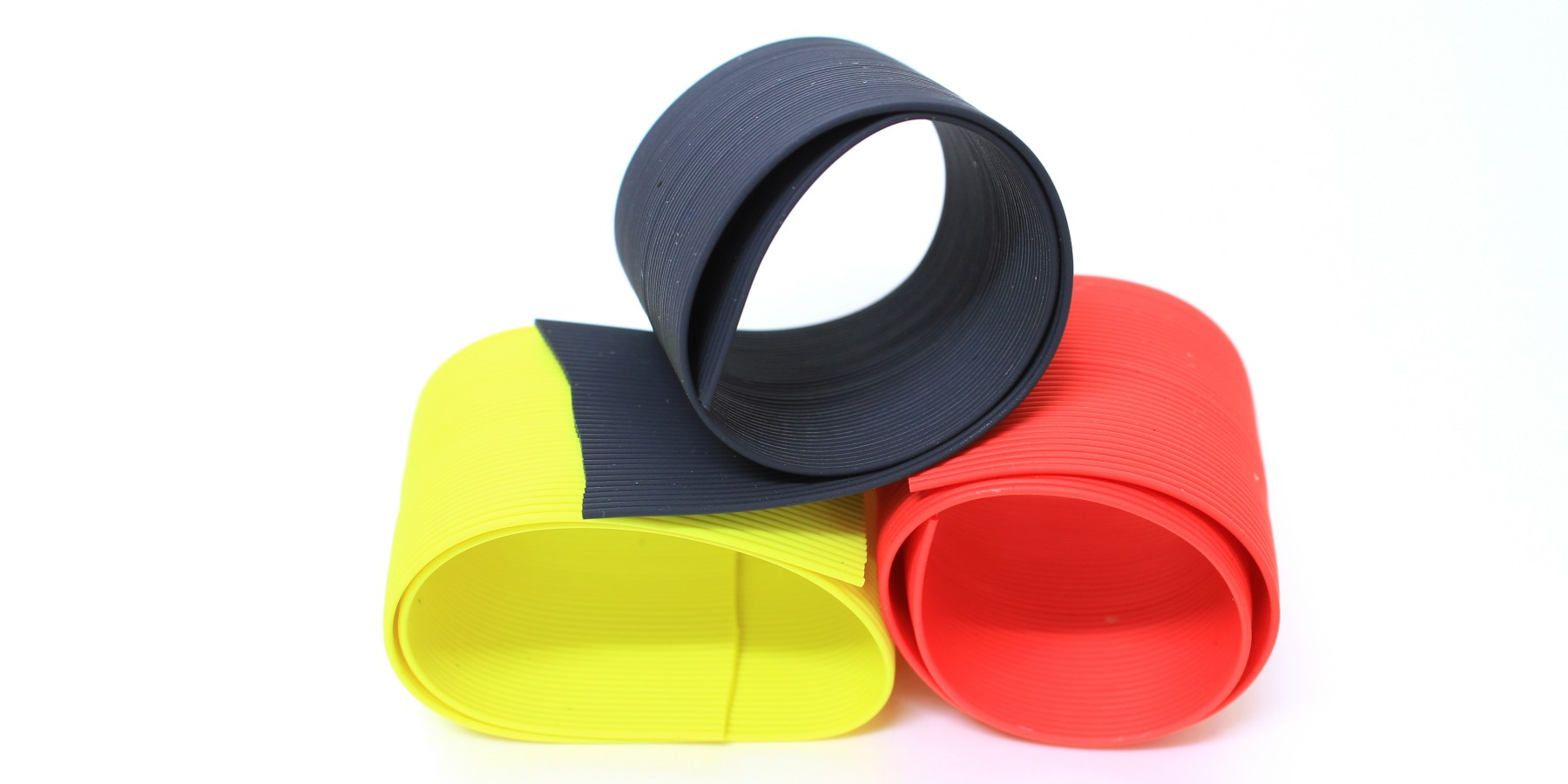
Silikonkautschuk ist ein synthetischer Kautschuk, der durch die Kombination von Silizium, Sauerstoff, Kohlenstoff und Wasserstoff hergestellt wird. Es verfügt über eine ausgezeichnete Hitzebeständigkeit, gute Flexibilität und hervorragende elektrische Isolationseigenschaften. Es wird häufig für Automobil- und Luft- und Raumfahrtanwendungen, elektrische Isolierung und medizinische Geräte verwendet.
Fluorkautschuk (FKM)
FKM ist ein synthetischer Kautschuk, der durch Copolymerisation von Hexafluorpropylen und Vinylidenfluorid hergestellt wird. Es verfügt über eine ausgezeichnete Chemikalienbeständigkeit, Hochtemperaturbeständigkeit und eine gute Druckverformungsrestbeständigkeit. Es wird häufig für Dichtungen, Dichtungen und Schläuche in der Chemie- und Erdölindustrie verwendet.
Thermoplastische Elastomere (TPE)
Thermoplastisches Elastomer (TPE) ist ein Polymermaterial mit den Eigenschaften sowohl von duroplastischem vulkanisiertem Gummi als auch von Thermoplasten. Es wurde in den 1960er Jahren kommerziell eingeführt und ist für seine hohe Elastizität bei Raumtemperatur und gute Verarbeitbarkeit bei höheren Temperaturen bekannt.
Der Unterschied zwischen duroplastischen Elastomeren/Kautschuken und thermoplastischen Elastomeren liegt in ihren vernetzenden Strukturbindungen. Die Vernetzung trägt dazu bei, die starken elastischen Eigenschaften von TPEs zu erzeugen, die leicht durch einfache Anpassung der Mischungszusammensetzung, Viskosität und Compoundierungsbestandteile erreicht werden können.
Die Anwendung von TPE umfasst Dichtungen, Staubmanschetten, O-Ringe, Schuhsohlen, Atemschläuche und mehr.
Anwendungen von geformtem Gummi
Geformter Gummi wird in einer Vielzahl von Anwendungen und Branchen eingesetzt, darunter:
Automobilindustrie
Geformter Gummi wird in der Automobilindustrie zur Herstellung von Dichtungen, Buchsen und anderen Komponenten verwendet. Diese Komponenten tragen dazu bei, Geräusche und Vibrationen zu reduzieren und die Gesamtleistung des Fahrzeugs zu verbessern.
Luft-und Raumfahrtindustrie
Geformter Gummi wird in der Luft- und Raumfahrtindustrie zur Herstellung von Schwingungsdämpfern, Dichtungen und anderen Komponenten verwendet. Diese Komponenten tragen dazu bei, die Auswirkungen von Vibrationen auf das Flugzeug zu reduzieren und sicherzustellen, dass es sicher und effizient arbeitet.
Industrielle Anwendungen
Geformter Gummi wird in industriellen Anwendungen zur Herstellung von Dichtungen, Schläuchen und anderen Komponenten verwendet. Diese Komponenten werden in einer Vielzahl von Branchen eingesetzt, darunter Öl und Gas, chemische Verarbeitung und Fertigung.
Verbraucherprodukte
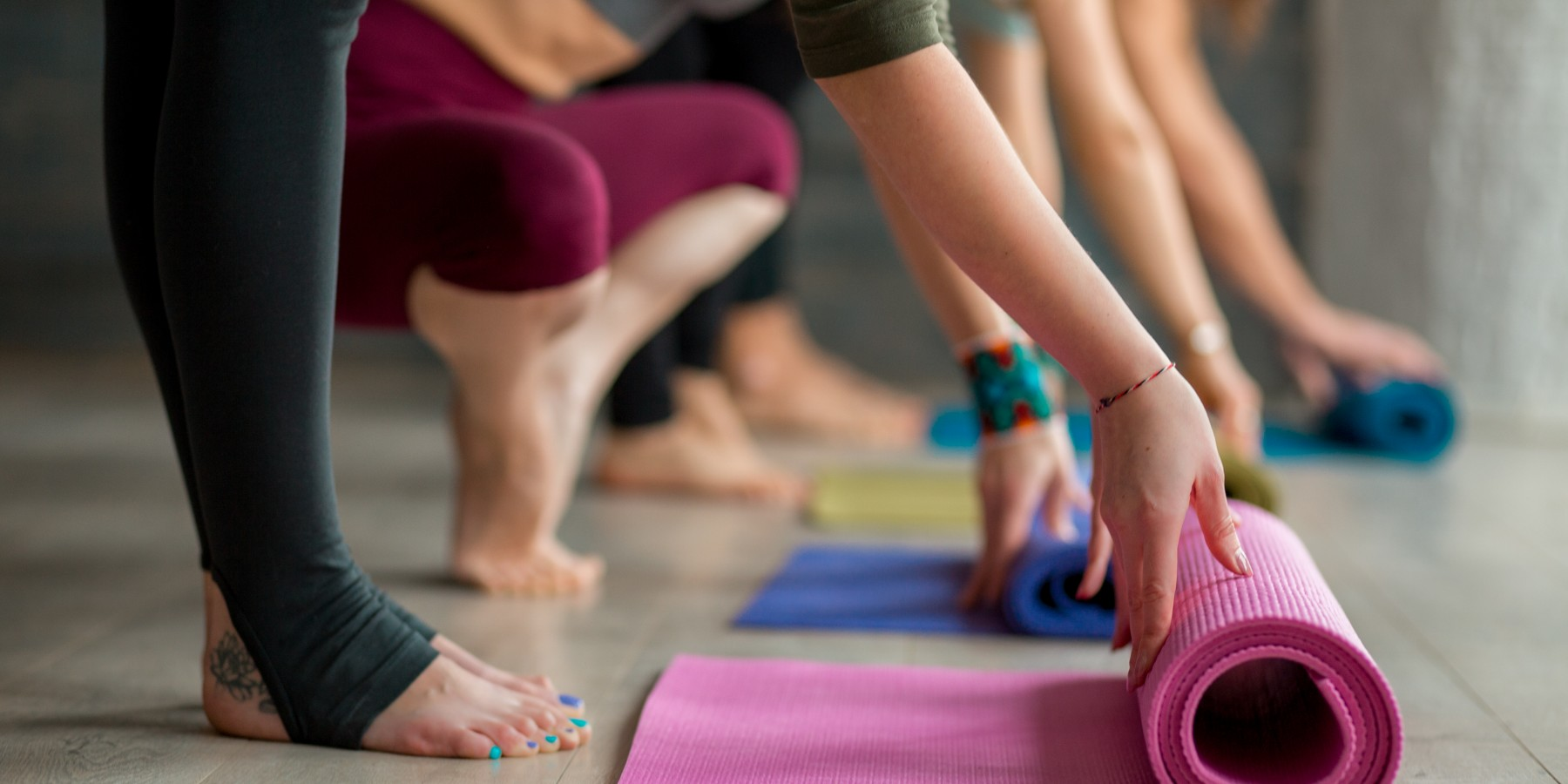
Geformter Gummi wird in einer Vielzahl von Konsumgütern wie Schuhen, Sportartikeln und Haushaltsgeräten verwendet. Es wird auch bei der Herstellung von Spielzeug und anderen Kinderprodukten verwendet.
Schlussfolgerung
Gummi ist ein unglaublich vielseitiges Material und wird für eine Vielzahl von Anwendungen eingesetzt. Je nach Anwendung und gewünschtem Ergebnis stehen vier Hauptverfahren zur Gummiverarbeitung zur Verfügung: Spritzgießen, Spritzpressen, Formpressen und Extrusion.
Spritzguss eignet sich am besten für Thermoplaste wie Polyurethan und Polypropylen, während Spritzguss besser für Duroplaste wie Polyester und Epoxidharz geeignet ist. Das Formpressen eignet sich ideal für Elastomere wie Silikon und Neopren, während sich die Extrusion für eine Vielzahl von Gummimaterialien eignet, darunter Naturkautschuk, Nitril, Styrol-Butadien-Kautschuk (SBR), Ethylen-Propylen-Dien-Monomer-Kautschuk (EPDM) und mehr. Es ist wichtig, das richtige Gummimaterial für die jeweilige Aufgabe auszuwählen, um Leistung und Kosteneffizienz sicherzustellen.
Die Wahl des für Ihre Anforderungen am besten geeigneten Gummiverfahrens hängt letztendlich von Ihren Produktspezifikationen und Budgetüberlegungen ab. Wenn Sie die Vorteile jedes Prozesses kennen, können Sie bei der Auswahl Ihrer Herstellungs- oder Prototyping-Methode eine fundierte Entscheidung treffen, um die optimale Leistung Ihres Endprodukts sicherzustellen.
Kundenspezifisch geformte Gummiteile
Sie sind auf der Suche nach Gummiformteilen, die höchste Qualität und technische Anforderungen erfüllen? Dann sind Sie bei Capable Machining genau richtig! Wir verfügen über jahrelange Erfahrung im Formenbau und Werkzeugbau von Gummi. Darüber hinaus verwenden wir die richtigen Materialien, um sicherzustellen, dass Ihr Projekt genau Ihren Spezifikationen entspricht. Kontaktieren Sie uns noch heute, um mehr über unsere zuverlässigen und kostengünstigen Formgummilösungen zu erfahren!