Waren Sie schon einmal neugierig auf den Herstellungsprozess komplexer Fahrzeugteile wie Motorblöcke, Antriebsstränge und Aufhängungskomponenten? Im Gegensatz dazu können leichte Werkzeuge für die medizinische Industrie einfach hergestellt werden. Hochdruckguss (HPDC), eine gängige Art der Herstellung, kann beide Arten von Produkten herstellen.
Was macht HPDC so beliebt und vielseitig? In diesem Artikel werden die technischen Aspekte des Druckgussverfahrens sowie seine vielfältigen Einsatzmöglichkeiten und Vorteile ausführlich erläutert. Mit diesem Wissen können Sie eine fundierte Entscheidung darüber treffen, ob HPDC die richtige Fertigungsmethode für Ihre Anforderungen ist.
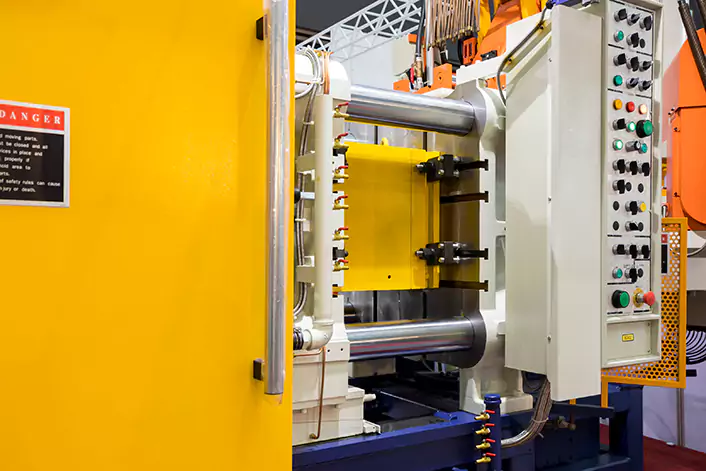
Was ist Druckguss?
Beim Hochdruck-Druckgussverfahren wird geschmolzenes Metall in eine Form geleitet und erstarrt, um das gewünschte Bauteil zu erzeugen. Das geschmolzene Metall wird unter hohem Druck, typischerweise mit Hilfe von hydraulischem Druck, in den Formhohlraum gedrückt und von einer robusten Presse an Ort und Stelle gehalten. Nachdem die Erstarrung abgeschlossen ist, wird die Gussform geöffnet, um den Guss zu entnehmen. Anschließend wird die Matrize für den nächsten Produktionszyklus wieder gesperrt. Das Werkzeug für den Hochdruck-Druckguss besteht aus zwei Stahlblöcken, die die beiden Enden des Formhohlraums bilden und so das gewünschte Objekt formen.
Entwicklungsgeschichte des Hochdruck-Druckgusses
Druckguss wurde erstmals Mitte des 1800. Jahrhunderts für die Druckindustrie entwickelt, wo eine Mischung aus Blei und Zinn in eine Stahlform gegossen wurde, um Tasten für Druckmaschinen herzustellen. Im Laufe der Zeit erfreute sich das Verfahren in zahlreichen Branchen zunehmender Beliebtheit. Durch die Verwendung unterschiedlicher Formformen könnte beim Druckguss eine vielfältige Produktpalette entstehen. Ab 1914 begann der Herstellungsprozess mit der Einbeziehung anderer Materialien wie Zink- und Aluminiumlegierungen, die auch heute noch häufig in der Industrie verwendet werden. Darüber hinaus waren Mitte der 1930er Jahre die meisten derzeit in der Industrie verwendeten Legierungen verfügbar.
Wie funktioniert Hochdruck-Druckguss?
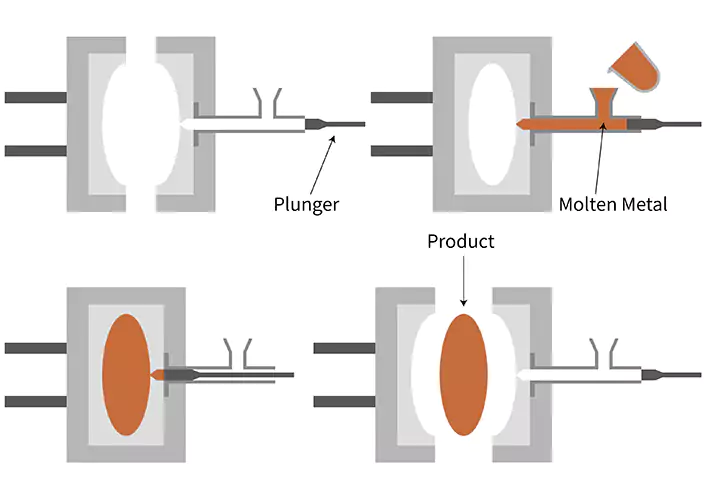
Der typische Betrieb von HPDC umfasst vier Phasen, nämlich Formvorbereitung, Einspritzung, Auswurf und Nachbehandlung des Gusses. Anpassungen an spezifische Produktanforderungen können zu Techniken wie Vakuumdruckguss, Slow-Fill-Druckguss und halbfester Metallverarbeitung (SSM) führen. Dennoch bleibt der grundsätzliche Verfahrensablauf wie folgt:
Formenvorbereitung
Um den Produktionszyklus zu starten, ist es wichtig, die Druckgussform von allen Verunreinigungen zu reinigen und die Innenwände zu schmieren. Dieser Prozess reguliert die Temperatur der Form und erleichtert die mühelose Entnahme des Gussprodukts.
Spritze
Das geschmolzene Metall wird in eine Schusskammer gegossen und anschließend in die Form eingespritzt, was durch zwei Methoden erreicht werden kann: Heißkammer- und Kaltkammer-Einspritzung.
Heißkammerinjektion
Bei der Tauchmethode wird das Einspritzsystem in den Schmelzofen eingetaucht, wo das geschmolzene Metall durch den Schusskolben und die Düse fließt, bevor es in die Form gelangt. Diese Technik ist ideal für Metalle wie Zink, Magnesium und Blei.
Kaltkammerinjektion
Bei der Kaltkammermethode wird geschmolzenes Metall manuell oder automatisch in eine Kaltkammerhülse gegossen, gefolgt von der Verwendung eines hydraulischen Kolbens, um das Metall nach dem Abdichten der Öffnung in die Form zu drücken. Sobald die Erstarrung abgeschlossen ist, wird der Kolben entfernt und die Matrize geöffnet, um den Hohlraum auszuwerfen. Dieser Ansatz eignet sich am besten für feste Materialien mit hohen Schmelzpunkten wie Aluminium, Messing und Magnesium. Das Kaltkammerverfahren kann entweder eine horizontale oder eine vertikale Injektion nutzen.
Magnesium kann sowohl mit Kaltkammer- als auch mit Heißkammer-Injektionsverfahren eingesetzt werden. Typischerweise werden Warmkammermaschinen aufgrund ihrer Größenbeschränkungen für kleine und komplizierte Teile verwendet. Darüber hinaus sind Hochdruck-Zinkdruckgussteile im Allgemeinen stärker als Aluminium-Druckgussteile.
Bei beiden Methoden erfolgt der Injektionsprozess schnell und bei hohen Drücken, typischerweise im Bereich von 1,500 bis 25,000 PSI. Die Form muss vollständig versiegelt sein und unter hohem Druck gehalten werden, um die Erstarrung zu erleichtern. Mithilfe hydraulischer Drücke werden alle in der Form eingeschlossenen Gase komprimiert und die Erstarrungsschrumpfung während des Abkühlvorgangs ausgeglichen. Handelsübliche Kräfte von bis zu 4000 Tonnen reichen aus, um die Matrize zu sichern und den hohen Drücken standzuhalten.
Teileentfernung
Sobald bestätigt ist, dass die Metallschmelze erstarrt ist, kann der Hohlraum aus der Form entfernt werden. Dies wird durch den Einsatz von Auswerferstiften erreicht, die sich meist am beweglichen Ende der Form befinden und den erstarrten Guss aus der Kavität drücken.
Beschneiden
Im letzten Schritt des Hochdruck-Druckgusses wird überschüssiges Material sowohl vom Produkt als auch von der Form entfernt. Der Beschnittvorgang kann den Einsatz von Werkzeugen wie einer Beschnittstanze oder einer Säge erfordern. Darüber hinaus können bei der Produktion anfallende Metallabfälle recycelt und in nachfolgenden Zyklen wiederverwendet werden.
Wenn Sie mehr über Druckguss erfahren möchten, kann unser Leitfaden zum Thema Niederdruck-Druckguss eine wertvolle Ressource zur Erweiterung Ihres Wissens sein.
Vorteile des Hochdruck-Druckgusses
Hochdruck-Druckguss ist aufgrund seiner zahlreichen Vorteile im Vergleich zu anderen Herstellungsverfahren ein beliebtes Verfahren in verschiedenen Branchen. Nachfolgend sind einige der Vorteile aufgeführt.
Höhere Produktionsraten
Im Vergleich zum Niederdruck- oder Schwerkraftgussverfahren führen Hochdruckgussverfahren zu höheren Produktionsraten. Die Verwendung von hohem Druck ermöglicht das Einspritzen von geschmolzenem Metall mit hoher Geschwindigkeit, was zu kürzeren Produktionszeiten führt. Daher ist dieser Ansatz in der Großserienfertigung beliebt.
Hochwertige Teile hergestellt
Darüber hinaus bietet der Hochdruckguss eine hervorragende Qualität hinsichtlich Maßhaltigkeit und hervorragender Oberflächengüte. Die mit dieser Methode hergestellten hochpräzisen Produkte erfordern normalerweise keine zusätzlichen Beschnittprozesse, die sowohl zeitaufwändig als auch kostspielig sein können. Die glatte Oberflächenbeschaffenheit vereinfacht zudem den Galvanisierungsprozess. Darüber hinaus bieten Hochdruck-Druckgussprodukte Vorteile wie eine hervorragende Gleichmäßigkeit und optimale mechanische Eigenschaften.
Dünnwandige Produkte
Die hohen Drücke dieses Druckgussverfahrens ermöglichen die Herstellung dünnerer Querschnitte im Vergleich zu anderen Gießverfahren. Je nach Größe und Anforderung des Bauteils sind Wandstärken von weniger als 0.40 mm realisierbar. Diese dünnen Wände können dazu beitragen, das Gewicht des Endprodukts zu reduzieren. Darüber hinaus ermöglichen die dünnen Wände den Einbau von Einsätzen (auch „Co-Cast“-Teile genannt) wie Schrauben und Auskleidungen in das Produkt während des Gussprozesses. Dies reduziert die Anzahl der benötigten Komponenten bei der Montage.
Erzielen Sie komplexes Design
Das Druckgussverfahren bietet die Möglichkeit, verschiedene Formformen zu verwenden und bietet so Flexibilität bei der Herstellung komplexer Teile. Dies ermöglicht die Erstellung komplizierter Komponenten, die bei komplexen Baugruppen hilfreich sein können.
Langlebige Stanzformen
Die dabei verwendeten Matrizen haben eine lange Lebensdauer und eignen sich daher für die Wiederverwendung in mehreren Produktionszyklen. Dies trägt dazu bei, die Stückkosten des Druckgussprodukts zu senken.
Anwendungen des Hochdruck-Druckgusses
Aufgrund der überlegenen Qualität der durch HPDC erzielten Produkte hat das Verfahren zahlreiche wichtige Anwendungen in den unterschiedlichsten Branchen gefunden.
Automobilindustrie
Hochdruck-Kokillenguss eignet sich zur Herstellung einer Reihe von Automobilstrukturbauteilen aus Aluminium und Magnesium. Zu diesen Komponenten gehören unter anderem Motorblöcke, Getriebegehäuse, Ölwannen, Motorlager und Fahrzeugquerträger.
Medizintechnik
Das HPDC-Verfahren wird auch in der medizinischen Industrie häufig zur Herstellung leichter chirurgischer Instrumente eingesetzt. Darüber hinaus wird es für die Herstellung medizinischer Geräte wie Infusionspumpen und hochproduktiver Bildgebungsgeräte verwendet.
Luft-und Raumfahrtindustrie
Die Luft- und Raumfahrtindustrie nutzt das HPDC-Verfahren aufgrund seiner Fähigkeit, komplizierte Designs zu erstellen und zu automatisieren, häufig. Legierungen aus Aluminium, Zink und Magnesium werden üblicherweise zur Herstellung von Motorkomponenten für Luft- und Raumfahrtanwendungen verwendet.
FAQs
Q1. Warum heißt es Druckguss?
Beim Hochdruck-Druckgussverfahren kommen Matrizen zum Einsatz, die typischerweise aus Stahl bestehen und durchgehend hergestellt werden CNC-Bearbeitung. Diese Matrizen dienen als Formen, in die flüssiges Metall eingespritzt wird. Die Form ist in zwei Hälften geteilt: eine feste Hälfte, die an der Gießmaschine befestigt ist, und eine bewegliche Auswerferhälfte.
Q2. Wie unterscheidet sich Druckguss von anderen Gussherstellungsverfahren?
Die Vorteile von Druckgussteilen überschneiden sich mit denen von Schwerkraftgussprodukten. Sie haben ähnliche Vorteile wie die Festigkeit, Ästhetik und Textur des Metalls sowie nachgewiesene Ermüdungsfestigkeit und wirksame schalldämpfende Eigenschaften. Darüber hinaus ermöglicht Druckguss schnelle Produktionsraten mit außergewöhnlicher Maßhaltigkeit, sodass häufig keine weitere Bearbeitung erforderlich ist. Im Gegensatz dazu ist beim Sandguss für jede Produktion eine neue Form erforderlich, während der Kokillenguss vergleichsweise langsamer ist als der Hochdruckguss (HPDC).
Q3. Was ist der Unterschied zwischen Niederdruck- und Hochdruck-Kokillenguss?
Niederdruckdruckguss (LPDC) arbeitet in einem Druckbereich von 0.08–0.15 MPa, während Hochdruck-Druckguss (HPDC) in einem viel höheren Bereich von 30–70 MPa arbeitet. LPDC hat eine moderate Produktionsrate und einen langsamen Gießzyklus, während HPDC schnellere Produktionsraten und schnellere Gießzyklen aufweist. HPDC produziert typischerweise Produkte mit einem gewissen Grad an Porosität, aber einer hochwertigen Oberflächenbeschaffenheit. Mittlerweile produziert LPDC Gussteile ohne Porosität, aber die Oberflächenbeschaffenheit ist durchschnittlich.