Spritzgießen ist eine weit verbreitete Methode zur Herstellung einer Vielzahl von Kunststoffprodukten, -teilen und -komponenten. Bei diesem Verfahren werden Kunststoffpellets geschmolzen und das geschmolzene Material in einen Formhohlraum eingespritzt, wo es erstarrt und die Form der Form annimmt. Die Fähigkeit, präzise Toleranzen einzuhalten, die zur Gewährleistung einer gleichbleibenden Produktqualität, Leistung und Funktionalität erforderlich sind, ist ein entscheidender Aspekt von Spritzgießen.
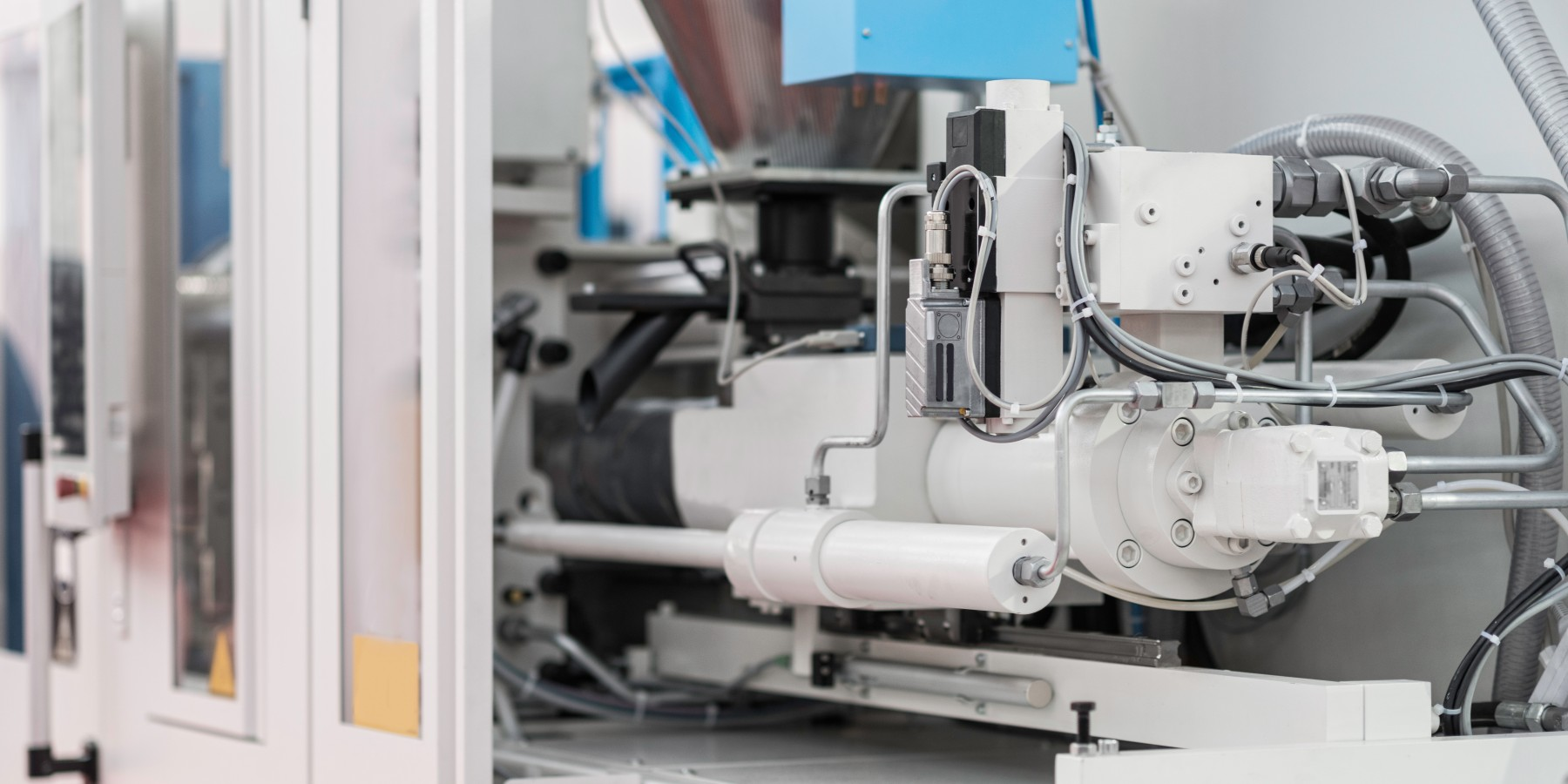
Bei der Konstruktion und Herstellung von Spritzgussteilen müssen die richtigen Abmessungen und engen Toleranzen eingehalten werden, um eine optimale Leistung zu gewährleisten. Die Vernachlässigung dieser Aspekte könnte zu einer Minderleistung oder sogar zum Ausfall des Teils führen. Spritzgusstoleranzen sind insbesondere bei komplexen Kunststoffspritzgussteilen von entscheidender Bedeutung. Standard-Spritzgusstoleranzen liegen bei etwa +/- 0.1 mm, während bei sehr anspruchsvollen Spritzgussteilen +/- 0.025 mm erreichbar sind.
Faktoren, die die Toleranzen beeinflussen und die Spritzgusstoleranzen optimieren
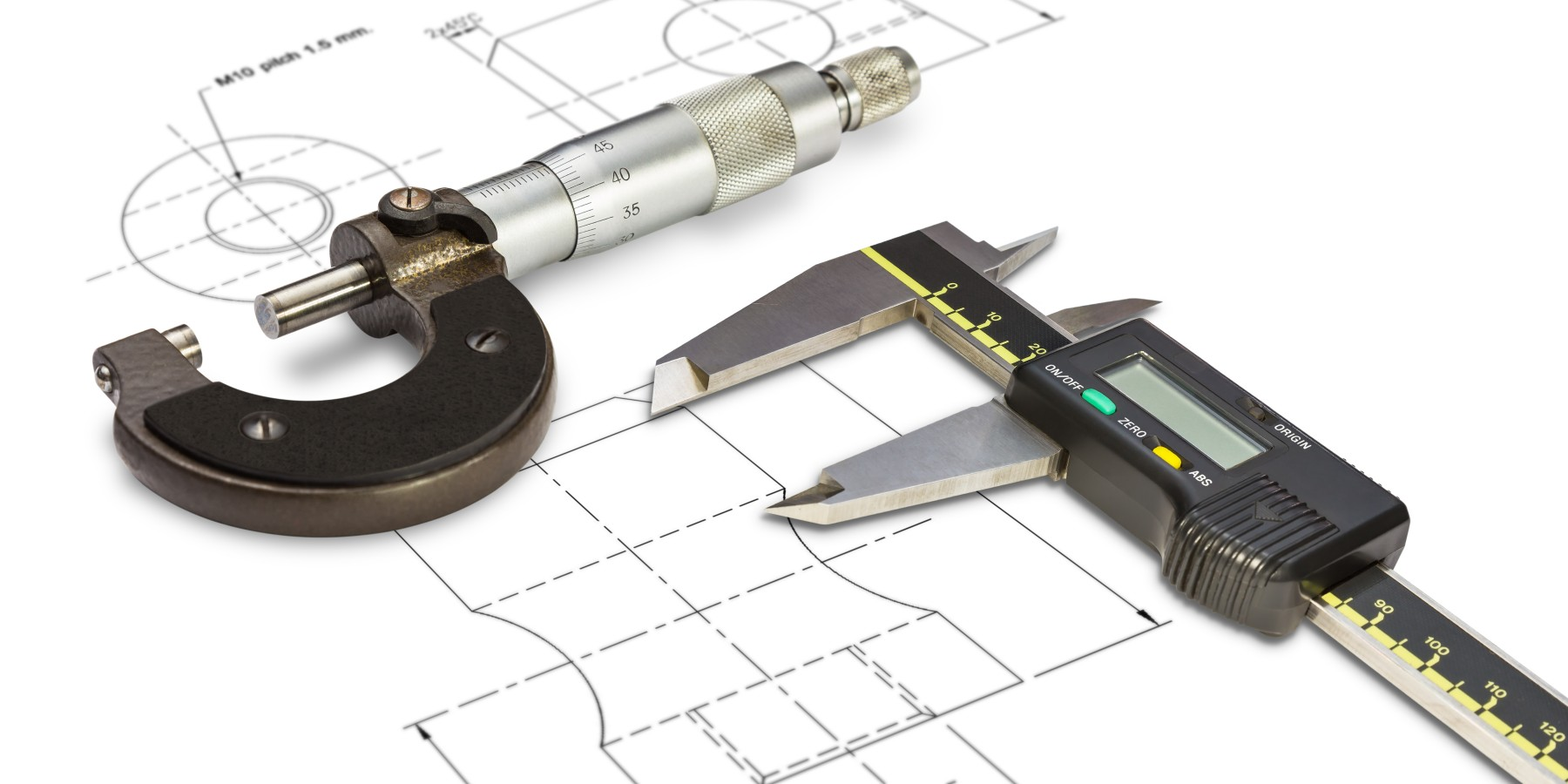
Schrumpfung
Der Grad der Schrumpfung variiert je nach Material, wobei höhere Schrumpfungsraten es schwieriger machen, präzise Spritzgusstoleranzen einzuhalten. Amorphe Materialien wie PE, PC und PS weisen im Allgemeinen bessere Spritzgusstoleranzen auf als kristalline Materialien wie z PEEK, PA und PP. Dies liegt daran, dass kristalline Materialien beim Schmelzen einen Phasenwechsel von einer dicht gepackten Molekülstruktur zu einer weniger dichten Flüssigkeitsstruktur durchlaufen, was zu einer Volumenänderung und einer stärkeren Schrumpfung führt. Im Gegensatz dazu bleiben amorphe Materialien auch im geschmolzenen Zustand in ihrem nichtkristallinen Zustand, was zu einer geringeren Schrumpfung führt.
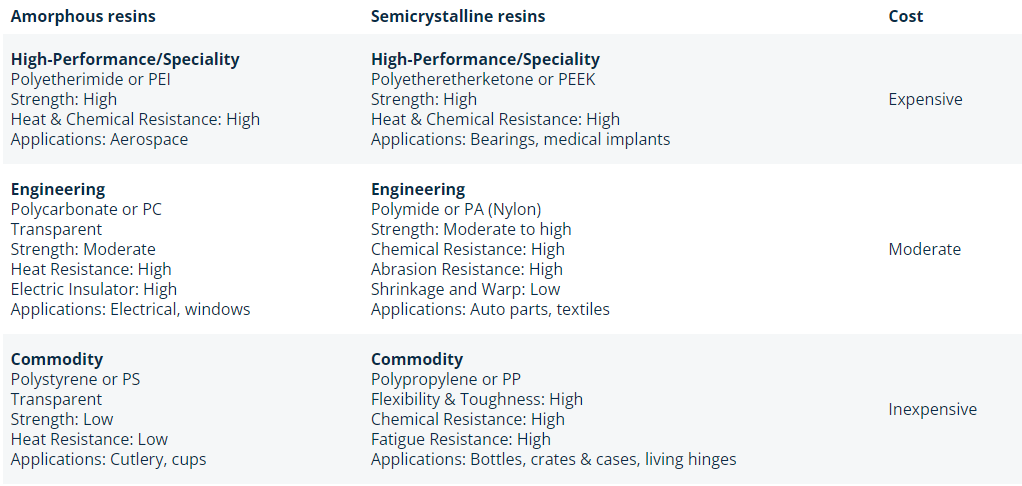
So reduzieren Sie den Einfluss der Schrumpfung
Spritzgussformen werden mit hoher Präzision hergestellt CNC-Bearbeitung Techniken auf Aluminium- oder Stahlmaterialien. Sie können bei Bedarf Toleranzen im Bereich von +/-0.01 einhalten. Sobald der Kunststoff in die Form eingespritzt wird, durchläuft er einen Abkühlungsprozess, der ihn zum Schrumpfen bringt. Das Ausmaß der Schrumpfung hängt vom jeweils verwendeten Harz oder Kunststoff ab. Um dieser Schrumpfung Rechnung zu tragen, wird jede Form etwas größer als die gewünschte Endgröße des Teils hergestellt.
Auftragen von Kunststoffmaterial mit Glasfaser oder Faserkohlenstoff könnte seine Schrumpfungsrate drastisch reduzieren. Beispielsweise weist POM typischerweise eine Schrumpfrate von etwa 2 bis 3 % auf, während POM mit 15 % Glasfaser nur eine typische Schrumpfrate von weniger als 0.5 % aufweist.
Verzug
Während der Abkühlphase beim Spritzgießen kommt es bei allen Teilen zu einer gewissen Schrumpfung. Teile mit gleichmäßiger Wandstärke schrumpfen gleichmäßig und verziehen sich seltener oder weisen Einfallstellen auf. Wenn die Wände jedoch ungleichmäßig sind, variieren die Abkühlungs- und Schrumpfraten, was aufgrund inhärenter Designprobleme zu einer stärkeren Verformung des Teils führen kann.
Lösung
Um Verzug bei Teilen mit ungleichmäßiger Wandstärke zu verhindern, empfiehlt es sich, die Dickenänderung auf maximal 15 % der Nennwandstärke zu begrenzen. Darüber hinaus sollte immer ein glatter oder konischer Übergang verwendet werden, um sicherzustellen, dass das Teil effektiv geformt wird. Die folgende Tabelle enthält empfohlene Wandstärken zur Vermeidung von Verformungen:
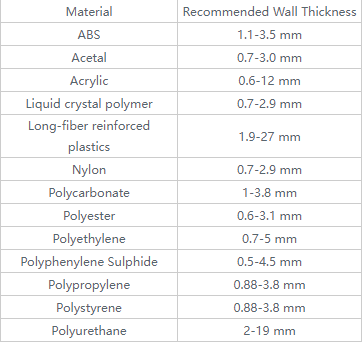
Wärmeausdehnung
In der Entwurfsphase muss auch die Temperatur berücksichtigt werden. Bei den meisten Harzen und Kunststoffen kann es aufgrund ihrer hohen Wärmeausdehnung schwierig sein, enge Toleranzen einzuhalten. Selbst wenn Spritzgussteile zunächst unter kontrollierten Bedingungen enge Toleranzen erreichen können, ist dies keine Garantie dafür, dass sie diese Abmessungen über die Zeit oder als Reaktion auf Temperaturänderungen, wie sie beispielsweise bei der Verwendung im Freien unter realen Bedingungen auftreten, beibehalten. Dies ist besonders wichtig, wenn Kunststoffteile mit anderen Materialien wie Metallen kombiniert werden und das Teil extremen Temperaturschwankungen ausgesetzt ist.
Lösung
Um sicherzustellen, dass enge Toleranzen eingehalten werden, ist es für Ingenieure wichtig, das geeignete Spritzgussmaterial auszuwählen, das den zu erwartenden Umgebungs- und Temperaturbedingungen standhält. Die Wahl des falschen Materials, das unvorhersehbar auf solche Bedingungen reagieren kann, kann die Einhaltung enger Toleranzen beeinträchtigen.
Es ist zu beachten, dass Kunststoffe im Allgemeinen erhebliche Wärmeausdehnungskoeffizienten aufweisen. Dies bedeutet, dass die Toleranzen in einer kontrollierten Umgebung von den realen Bedingungen, unter denen die Teile verwendet werden, abweichen können. Beispielsweise sind ULTEM- und PEEK-Kunststoffe widerstandsfähiger gegen hohe Temperaturen als ABS oder PC.
Teiledesign
Die Bestimmung der Toleranzen eines Teils wird in erster Linie von seiner Konstruktion beeinflusst. Die Verbesserung des Designs in den Anfangsphasen eines Projekts trägt nicht nur dazu bei, gute Spritzgusstoleranzen während der Produktion zu erreichen, sondern verbessert auch die Qualität und Herstellbarkeit, senkt die Kosten und erhöht die Zufriedenheit der Endbenutzer.
Verschiedene Faktoren wie Teilegeometrie, Gesamtgröße und Anforderungen an die Wandstärke können einen Einfluss haben Formtoleranzen Kontrolle. Beispielsweise können dicke Wände innerhalb der dicken Abschnitte unterschiedliche Schrumpfungsraten aufweisen, was die Einhaltung enger Toleranzen erschwert, da das Teil in verschiedenen Abschnitten unterschiedlich schrumpft. Ebenso kann sich die Größe des Teils auf die Fähigkeit auswirken, enge Toleranzen einzuhalten, insbesondere wenn die Abmessung mit der engen Toleranz groß ist. Selbst in kleineren Bereichen ist es einfacher, enge Maßtoleranzen einzuhalten, wohingegen bei größeren Abmessungen eine größere Gesamtschrumpfung auftreten kann, was es schwieriger macht, enge Toleranzen zu kontrollieren und einzuhalten.
Lösung
Durch die frühzeitige Erkennung enger Toleranzen in der Konstruktionsphase können Ingenieure verschiedene Faktoren berücksichtigen, die sich auf die Spritzgusstoleranzen auswirken, darunter Teilegeometrie, Größe und Merkmale wie Wandstärke. Um enge Toleranzen einzuhalten, ist es wichtig, eine gleichmäßige Wandstärke im gesamten Teil sicherzustellen, um ungleichmäßige Schrumpfraten zu vermeiden, die zu Verformungen führen und die Effizienz des Teils beeinträchtigen können. In vielen Fällen sind Konstruktionsmerkmale wie Stützrippen oder Zwickel wirksamer für die Festigkeit als eine Erhöhung der Wandstärke.
Teilekomplexität
Die Komplexität der Teile wirkt sich auch auf den Materialfluss und die Werkzeugkonstruktion aus, da das schnelle Einfüllen der Teile in die Form, die Aufrechterhaltung der richtigen Werkzeugtemperatur und die Steuerung des Kühlprozesses für die Dichtigkeit wichtig sind Formtoleranzen.
Lösung
Obwohl der Herstellungsprozess in der Regel für Hersteller von größerer Bedeutung ist, ist es dennoch wichtig, ihn bereits in der Entwurfsphase zu berücksichtigen. Um Hinterschneidungen zu vermeiden, empfiehlt es sich, das Design möglichst einfach zu halten. Wenn eine Hinterschneidung erforderlich ist, sollte eine Form mit Seitenwirkungen entworfen werden. Richtig konstruierte Formwerkzeuge sind von entscheidender Bedeutung, um sicherzustellen, dass die Teile richtig abkühlen und strenge Toleranzstandards einhalten.
Ingenieure können Variablen wie Einspritzdruck, Harzviskosität und Formfüllzeit verfolgen und anpassen, um während des Prozesses den richtigen Druck, die richtige Erwärmung und Kühlung sicherzustellen. Die Formflussanalyse ist für genaue Vorhersagen über Faktoren erforderlich, die die Toleranzen beeinflussen, wie z. B. Formtemperaturen, Erhitzen und Abkühlen, Schrumpfung und Verzug.
Werkzeugbau
Beim Spritzgießen gibt es drei Arten von Werkzeugen:
Werkzeug mit einer Kavität – Produziert ein einzelnes Teil für einen einzigen Kunststoffschuss
Werkzeug mit mehreren Kavitäten – Produziert mehrere Teile mit einem einzigen Kunststoffschuss
Hohlraumwerkzeug für Familien – Produziert alle Teile einer Baugruppe mit einem einzigen Kunststoffschuss
Die Fähigkeit, beim Spritzgießen gewünschte Toleranzen zu erreichen, wird durch Werkzeugdesign, Werkzeugmaterial und Kavitation beeinflusst. Die Anzahl der Kavitäten in einem Werkzeug und der Bedarf an Heizung und Kühlung können das Erreichen enger Toleranzen erschweren. Wenn die Werkzeugkonstruktion keine gleichmäßige und wiederholbare Kühlung gewährleistet, erhöhen sich die Schrumpfraten und es kommt zu schlechten Toleranzen. Beispielsweise benötigt ein Multitool oder Familienwerkzeug mit mehr Hohlräumen mehr Kühlunterstützung. Enge Toleranzen können schwierig zu erreichen sein, wenn die Werkzeughohlräume schlecht konstruiert sind oder durch Faktoren wie Druck oder Temperatur beeinflusst werden.
Lösung
Während dieser Teil für Hersteller möglicherweise relevanter ist, ist es für Designer dennoch wichtig, die Auswirkungen der Herstellungsprozesse auf die Lebensfähigkeit und Qualität ihrer Teile zu berücksichtigen. Mithilfe von Prozesskontrollen werden die vielen an der Produktion beteiligten Faktoren kalibriert, um Abweichungen zu minimieren.
In die Form integrierte Temperatur- und Drucksensoren spielen eine entscheidende Rolle bei der Entwicklung effektiver Prozesssteuerungen, indem sie Echtzeit-Feedback zu diesen Parametern liefern und bei Bedarf schnelle Anpassungen ermöglichen. Durch die richtige Steuerung dieser Faktoren können die Formwerkzeuge Teile mit engen Toleranzen und minimalen Abweichungen herstellen. Die Formfüllanalyse ist auch ein nützliches Werkzeug zur Beurteilung des Zustands der Form und zur Sicherstellung einer konsistenten Produktion.
Andere Überlegungen
Die Kontrolle von Prozessvariablen ist in der Fertigung von entscheidender Bedeutung, um die Qualität und Brauchbarkeit von Teilen sicherzustellen. Echtzeit-Feedback von Druck- und Temperatursensoren in Formwerkzeugen ist für die Entwicklung robuster Prozesssteuerungen unerlässlich.
Dieses Feedback ermöglicht schnelle Anpassungen, um Abweichungen zu minimieren und die Wiederholbarkeit sicherzustellen. Wenn Prozessvariablen auf wiederholbare Weise gesteuert werden, können die Formwerkzeuge Teile mit präzisen Toleranzen und minimalen Abweichungen herstellen, was zu Produkten höherer Qualität führt.
Schlussfolgerung
Zusammenfassend lässt sich sagen, dass das Erreichen enger Toleranzen beim Kunststoffspritzguss ein umfassendes Verständnis des Zusammenspiels verschiedener Faktoren erfordert, darunter Teiledesign, Materialauswahl, Werkzeugdesign und Prozesssteuerung. Durch einen ganzheitlichen Ansatz für den Spritzgussprozess können Produktteams Teiledesigns optimieren, Materialien und Harze verfeinern und Prozesssteuerungen kalibrieren, um Präzision zu erreichen und Abweichungen zu minimieren.
Dies führt nicht nur zu qualitativ hochwertigen Teilen, sondern trägt auch dazu bei, Kosten zu senken, die Effizienz zu verbessern und die Kundenzufriedenheit zu steigern. Durch die Anwendung der in diesem Artikel beschriebenen Best Practices können Produktteams Spritzgussteile mit höchster Genauigkeit und Zuverlässigkeit herstellen.