Gängige Arten von Kunststoffformen
In diesem Abschnitt geben wir einen aufschlussreichen Überblick über Kunststoffformen und ihre Grundtypen. Kunststoffformen ermöglichen eine effiziente Massenproduktion und gewährleisten gleichzeitig Maßhaltigkeit und Wiederholbarkeit. Der Einsatz von Kunststoffformen revolutioniert den Herstellungsprozess und führt zu einer höheren Produktivität und geringeren Kosten.
1. Spritzgussformen
Spritzgießen ist ein Herstellungsprozess, bei dem geschmolzenes Material, typischerweise Kunststoff, in einen Formhohlraum eingespritzt wird. Das geschmolzene Material wird unter hohem Druck in die Form gedrückt, wo es abkühlt und erstarrt und die Form der Form annimmt. Dieses Verfahren ermöglicht die Massenproduktion komplexer und präziser Kunststoffteile mit gleichbleibender Qualität und hoher Produktionseffizienz. Spritzguss wird aufgrund seiner Vielseitigkeit, Kosteneffizienz und Fähigkeit zur Herstellung komplizierter Designs in verschiedenen Branchen häufig eingesetzt.
Die Formen bestehen aus zwei Hälften, dem Kern und der Kavität, die präzise bearbeitet werden, um die gewünschte Produktform zu erzeugen. Geschmolzener Kunststoff wird unter hohem Druck in den Formhohlraum eingespritzt, wo er abkühlt und erstarrt und die Form der Form annimmt. Aufgrund der hohen Druck- und Hochtemperaturkorrosion, denen Spritzgussformen während des Spritzgussprozesses ausgesetzt sind, müssen sie aus härteren Formenstählen hergestellt werden. Auch die Innenfläche der Form erfordert häufig eine hitzebeständige und korrosionsbeständige Oberflächenbehandlung. Darüber hinaus ist die Formstruktur relativ komplex, um die Präzision auch nach Tausenden oder sogar Millionen von Einspritzzyklen sicherzustellen.
2. Blasformen
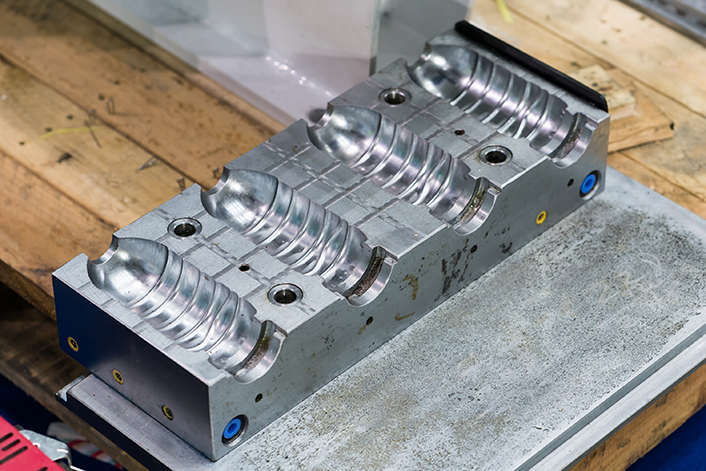
Blasformen ist ein spezielles Herstellungsverfahren zur Herstellung von Hohlkörpern wie Flaschen, Behältern und Automobilkomponenten. Dabei wird Kunststoffharz geschmolzen und dann mit Druckluft in einen Formhohlraum aufgeblasen. Die Form, auch Blasform genannt, ist ein zweiteiliges Werkzeug, das aus einem Kern und einem Hohlraum besteht und dazu dient, den geschmolzenen Kunststoff in die gewünschte Form zu bringen. Die Druckluft dehnt den Kunststoff gegen die Formwände aus und ermöglicht so das Abkühlen und Erstarren in die endgültige Produktform. Das Blasformen bietet Vorteile wie Kosteneffizienz, hohe Produktionsraten und die Möglichkeit, komplexe Geometrien zu erstellen.
Im Vergleich zu Spritzgussformen ist der Druck beim Blasformen relativ niedrig und die Anforderungen an die Präzision relativ gering. Außerdem wird der Kunststoff beim Blasformen nicht bis zum geschmolzenen Zustand erhitzt und daher ist auch die Betriebstemperatur niedriger. All dies führt zu einfacheren Formen und damit relativ geringeren Kosten.
3. Kompressionsformen
Pressformen werden zum Formen duroplastischer Kunststoffe verwendet. Dabei wird eine präzise Menge Kunststoffmaterial in den Formhohlraum gegeben und anschließend Druck ausgeübt, um das Material gleichmäßig zu verteilen. Anschließend wird Wärme zugeführt, um den Aushärtungsprozess einzuleiten und den Kunststoff in einen festen Zustand zu überführen. Nach dem Aushärten wird die Form geöffnet und das fertige Teil entnommen. Kompressionsformen eignen sich ideal für die Herstellung stabiler, komplexer Kunststoffteile mit hervorragender Maßhaltigkeit und Oberflächengüte. Formpressen wird typischerweise für Gummi, duroplastische Kunststoffe, Silikonkautschuk und andere Materialien verwendet, die nach dem Aushärten nicht mehr umgeformt werden können.
Bis auf wenige Ausnahmen sind die Anforderungen an die Präzision von Pressformen in der Regel nicht sehr hoch. Der Öffnungs- und Schließmechanismus ist viel einfacher. Da keine Hochdruckeinspritzung erforderlich ist, ist die Formstruktur viel schwächer und leichter. Die Kosten sind viel günstiger als bei anderen Kunststoff-Prozessformen.
4. Rotationsformen
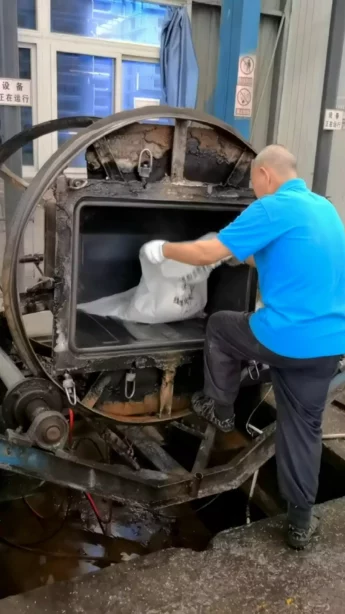
Rotationsformen, auch Rotorformen genannt, werden zur Herstellung großer, hohler Kunststoffteile eingesetzt. Der Herstellungsprozess beginnt mit einer beheizten Form, die sich um zwei Achsen dreht. Flüssiger Kunststoff wird in die Form gegossen und durch die Rotation wird der Kunststoff gleichmäßig über die Innenflächen verteilt. Sobald die Form abgekühlt ist, verfestigt sich der Kunststoff und es entsteht die gewünschte Form. Rotationsformen ist eine ideale Methode zur Herstellung komplexer Formen mit gleichmäßiger Wandstärke und eignet sich daher für die Herstellung von Tanks, Lagerbehältern und Spielgeräten. Zu den Vorteilen gehören Designflexibilität, Einheitlichkeit und der Wegfall von Montageprozessen.
5. Thermoformformen
Thermoformformen werden in einem Herstellungsprozess namens Thermoformen oder Vakuumformen verwendet. Bei diesem Verfahren wird eine Kunststofffolie erhitzt, bis sie flexibel wird, und dann über eine Form gelegt. Durch Anlegen eines Vakuums oder Drucks wird die Kunststoffplatte in die gewünschte Form der Form gebracht. Nach dem Abkühlen wird das geformte Kunststoffteil aus der Form ausgeworfen. Tiefziehformen werden häufig zur Herstellung von Verpackungsmaterialien, Schalen und Einwegbechern verwendet.
Beim Vakuumformverfahren muss der Kunststoff nur erweicht und nicht geschmolzen werden, sodass die Anforderungen an die Temperaturbeständigkeit der Form nicht hoch sind. Da das Produkt durch niedrigen Druck geformt wird, muss die Form nicht zu viel Druck aushalten und die Präzisionsanforderungen sind geringer. Daher muss die Form nicht aus Stahl bestehen, sondern es können Holz, Aluminium usw. verwendet werden. Der Bearbeitungsprozess ist außerdem einfacher und schneller als bei anderen Formtypen. Daher sind die Formkosten niedrig.
In den folgenden Abschnitten stellen wir am Beispiel von Spritzgussformen die Schritte zur Herstellung von Kunststoffformen vor.
Wie stellt man Spritzgussformen her? -7 Schritte
Schritt 1. Wählen Sie das passende Formmaterial für die gewünschte Anwendung.
Die Auswahl des geeigneten Formmaterials ist ein entscheidender Schritt bei der Herstellung von Kunststoffformen. Die Wahl des Materials richtet sich nach der gewünschten Anwendung und den spezifischen Anforderungen. Zu den zu berücksichtigenden Faktoren gehören mechanische Eigenschaften, chemische Beständigkeit, Temperaturbeständigkeit, Dimensionsstabilität und Kosten. Zu den gängigen Formmaterialien gehören Thermoplaste wie Polyethylen, Polypropylen und Polystyrol, die Flexibilität, Haltbarkeit und einfache Verarbeitung bieten. Für spezielle Anwendungen können duroplastische Kunststoffe wie Epoxid- oder Phenolharze geeignet sein, die Hitzebeständigkeit und Dimensionsstabilität bieten. Darüber hinaus bieten technische Kunststoffe wie ABS, Nylon oder Polycarbonat eine verbesserte Festigkeit und Leistung. Durch sorgfältige Berücksichtigung der Materialeigenschaften wird sichergestellt, dass mit der Form qualitativ hochwertige Teile hergestellt werden können, die den funktionalen und ästhetischen Anforderungen der Anwendung entsprechen.
Schritt 2. Entwerfen Sie Konzepte und erstellen Sie ein 3D-Modell der Form.
Alle Formenkonstruktionen beginnen mit dem 3D-Modell der herzustellenden Kunststoffteile. Sobald das Material ausgewählt ist, ist die Schrumpfrate bekannt. Mit moderner CAD-Software können Formenkonstruktionen problemlos aus 3D-Modellen von Kunststoffteilen erstellt werden. Natürlich muss der Formenbauer noch viele technische Aspekte berücksichtigen, wie z. B. die Wandstärke des Teils, die Schrumpfrate, ob genügend Platz für den Schieber vorhanden ist, wo die Trennfuge das Erscheinungsbild nicht beeinträchtigt usw. Komplexere Formen Außerdem müssen Sie eine professionelle Moldflow-Software für die Moldflow-Analyse verwenden, um sicherzustellen, dass es im Produktionsprozess der Teile nicht zu Qualitätsproblemen kommt. Auch die Wahl des Formkernmaterials erfordert professionelles Urteilsvermögen. Zu den Einflussfaktoren gehören die Lebensdauer der Form, die Korrosivität von Kunststoffmaterialien usw. Capable Machining verfügt über ein professionelles Formenbauteam mit jahrzehntelanger Erfahrung im Formenbau. Wir formen einfach richtig.
Schritt 3. Stellen Sie die Form mithilfe von CNC-Bearbeitung, Funkenerosion und anderen Verfahren her.
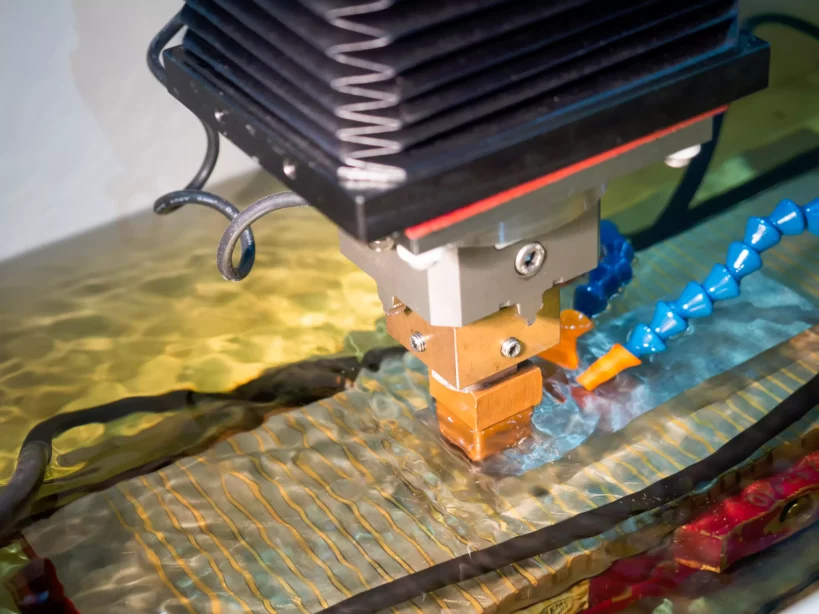
Der moderne Formenbau ist längst spezialisiert. Die Formbasis wurde standardisiert, und es gibt auch professionelle Hersteller, die sich auf die Herstellung verschiedener Formzubehörteile wie Platten, Fingerhüte und Zylinder spezialisiert haben. Sogar die Versorgung mit Rohstoffen für die Kerne wurde halbstandardisiert. Verschiedene Formbleche aus Stahl mit einer Präzision von bis zu 10 µm werden von professionellen Zulieferern bearbeitet und anschließend an Formenhersteller (wie uns) versendet.
Abhängig von den Kunststoffteilen und den Anforderungen an die Form verwenden Hersteller CNC-Bearbeitung (für ungehärteten Stahl) oder EDM (für gehärteten Stahl oder komplizierte Formen), um den Formhohlraum herzustellen. Manchmal müssen wir auch kein Standard-Formzubehör herstellen.
Schritt 4. Bereiten Sie die Formoberfläche durch Polieren oder Auftragen von Beschichtungen vor.
Aufgrund der unterschiedlichen Anforderungen an Spritzgussmaterialien, Oberflächentexturen und die gesamte Lebensdauer der Form erfordert der Formhohlraum häufig verschiedene Oberflächenbehandlungsmethoden, um das Erscheinungsbild der Spritzgussteile zu verbessern oder die Korrosionsbeständigkeit der Form zu verbessern. Zu den gängigen Oberflächenbehandlungsmethoden gehören Strukturätzen, Sandstrahlen, Polieren und verschiedene Arten von Beschichtungen.
Schritt 5. Formmontage: Formkomponenten für präzises Formen ausrichten und befestigen.
Der Montageprozess beginnt mit der sorgfältigen Positionierung und Ausrichtung der Formplatten, die die äußere Struktur der Form bilden. Im nächsten Schritt erfolgt der Einbau von Kernen und Hohlräumen, die die Form des Formteils definieren. Diese Komponenten müssen präzise positioniert und sicher befestigt werden, um eine genaue Formgebung zu gewährleisten.
Darüber hinaus umfasst die Montage die Integration von Auswerfersystemen, die die Entnahme des Formteils aus dem Formhohlraum erleichtern. Bei der Montage werden auch Kühlkanäle eingebaut, die die Temperatur der Form während des Spritzvorgangs regulieren sollen. Weitere Elemente wie Führungsstifte, Schrauben und Anschlüsse sorgen für die richtige Ausrichtung und Stabilität der Formkomponenten. Während des Montageprozesses wird besonderes Augenmerk auf die Passung und das Spiel zwischen den Komponenten gelegt, um mögliche Fehlausrichtungen oder Störungen zu minimieren. Sobald alle Komponenten angebracht sind, werden sie sicher befestigt, typischerweise mit Bolzen, Schrauben oder Klemmsystemen.
Für die Montage von Spritzgussformen sind qualifizierte Techniker oder Formenbauer erforderlich, die über ein tiefes Verständnis für Formendesign und -funktionalität verfügen. Ihr Fachwissen gewährleistet die präzise Ausrichtung der Komponenten, die ordnungsgemäße Integration von Systemen und die Gesamtfunktionalität der Form. Eine gut zusammengebaute Spritzgussform ist entscheidend für die Erzielung qualitativ hochwertiger, konsistenter und fehlerfreier Kunststoffteile während des Spritzgussprozesses.
Schritt 6. Formtest: Führen Sie gründliche Tests und Validierungen der Form durch.
Ähnlich wie bei anderen Ingenieurarbeiten müssen Formen einer Prüfung unterzogen werden, um ihre ordnungsgemäße Funktionalität sicherzustellen. Der Prüfprozess für Formen ähnelt dem Spritzguss-Produktionsprozess. Der Spritzgussmaschine wird Kunststoffmaterial zugeführt und verschiedene Parameter der Maschine werden für den Spritzguss angepasst. Wenn das geformte Produkt nicht den gewünschten Erwartungen entspricht, sind Verbesserungen an der Form erforderlich. Durch jahrelange Erfahrung im Formenbau, gepaart mit moderner Formdesign- und Formflussanalyse-Software, haben wir das Auftreten größerer Probleme während der Probeformphase deutlich reduziert. Gelegentliche Formanpassungen sind jedoch immer noch erforderlich. Durch die Durchführung dieser Schritte stellt der Hersteller sicher, dass das Kunststoffteil den vorgesehenen Spezifikationen entspricht und zur Verwendung oder Montage bereit ist.
Schritt 7: Wiederholen Sie den Vorgang für weitere Formen oder Produktionsläufe.
Im letzten Schritt wird der gesamte Prozess der Erstellung zusätzlicher Formen oder der Durchführung von Produktionsläufen wiederholt. Sobald eine Form erfolgreich zur Herstellung eines Kunststoffteils verwendet wurde, kann sie zur Herstellung weiterer Teile wiederverwendet werden. Dieser Schritt umfasst das Vorbereiten der Form, das Aufstellen der Formmaschine und das Einspritzen oder Gießen der Schmelze Plastik, Anlegen von Druck oder Abkühlen, Öffnen der Form und Entnehmen der fertigen Teile. Durch die Wiederholung dieses Prozesses können Hersteller Kunststoffteile in Massenproduktion herstellen und so eine gleichbleibende Qualität gewährleisten und die erforderlichen Produktionsmengen erreichen. Es ermöglicht die effiziente und kostengünstige Herstellung großer Mengen an Kunststoffkomponenten für verschiedene Branchen und Anwendungen.
Zusammenfassend lässt sich sagen, dass das Verständnis der gängigen Arten von Kunststoffformen und das Erlernen der Herstellung von Kunststoffformen, z. B. der Herstellung von Spritzgussformen, mithilfe des schrittweisen Prozesses von entscheidender Bedeutung für eine erfolgreiche Formenherstellung sind. Der Prozess der Herstellung von Spritzgussformen erfordert sorgfältige Überlegungen zur Materialauswahl, präzises Formendesign, Fertigung mit fortschrittlichen Techniken, Oberflächenbehandlung, sorgfältige Montage, gründliche Tests und Wiederholungen für die Massenproduktion. Durch die Befolgung dieser Schritte können Hersteller hochwertige Formen erstellen, die eine effiziente und kostengünstige Produktion von Kunststoffteilen ermöglichen. Erfolgreicher Formenbau gewährleistet die Umsetzung präziser Designs und die Erfüllung spezifischer Anwendungsanforderungen und trägt so zum Fortschritt verschiedener Branchen bei.