Kochendes Wasser im Hochgebirge braucht keine 100 Grad Celsius. Dies liegt daran, dass der Siedepunkt einer Substanz bei niedrigem Druck sinkt. Wenn also a Umgebung mit unteratmosphärischem Druck bereitgestellt werden, verflüchtigen sich viele Substanzen, die sich unter Normaldruck nicht verflüchtigen, leicht. Bei der Vakuumbeschichtung handelt es sich um einen Prozess, der dieses Phänomen nutzt, um das Beschichtungsmaterial zu verflüchtigen und es auf dem Substrat abzuscheiden, um durch Erhitzen oder Ionensputtern unter niedrigem Druck eine Beschichtung zu bilden.
Vakuumbeschichtungen finden umfangreiche Anwendung beim Schutz einer Vielzahl von Gegenständen, von medizinischen Instrumenten bis hin zu Komponenten für die Luft- und Raumfahrt. Diese Beschichtungen bieten eine außergewöhnliche Beständigkeit gegen Verschleiß, Reibung, korrosive Chemikalien und hohe Temperaturen und erhöhen so die Langlebigkeit der geschützten Objekte erheblich. Insbesondere bieten durch Vakuumverfahren hergestellte Dünnfilm-Abscheidungsbeschichtungen deutliche Vorteile gegenüber alternativen Schutzbeschichtungsmethoden. Im Gegensatz zu anderen Techniken eliminieren Vakuumbeschichtungen das Potenzial für unerwünschte Nebenwirkungen. Herkömmliche Beschichtungsmethoden können unbeabsichtigt die Präzision eines Werkzeugs beeinträchtigen oder eine übermäßige Dicke hinzufügen, wodurch die beabsichtigte Leistung beeinträchtigt wird.
Was ist eine Vakuumbeschichtung?
Bei der Vakuumbeschichtung oder Dünnschichtabscheidung wird durch einen Vakuumkammerprozess eine bemerkenswert dünne und gleichmäßige Beschichtungsschicht auf die Oberfläche eines Substrats aufgetragen. Diese Technik dient dazu, das Substrat vor äußeren Faktoren zu schützen, die zu Verschleiß führen und seine Gesamteffizienz verringern könnten. Vakuumbeschichtungen zeichnen sich durch ihre Dicke aus, typischerweise im Bereich von 0.25 bis 10 Mikrometern (0.01 bis 0.4 Tausendstel Zoll).
Grundlagen
Zu den Grundprinzipien der Vakuumbeschichtung gehört die Schaffung einer kontrollierten Umgebung mit niedrigem Druck und der Einsatz verschiedener Verfahren zur Abscheidung dünner Filme oder Beschichtungen auf Substraten. Hier sind die Grundprinzipien:
Vakuumumgebung
Die Vakuumbeschichtung erfordert eine kontrollierte Niederdruckumgebung, um unerwünschte Wechselwirkungen zwischen dem Beschichtungsmaterial und den umgebenden Gasen zu minimieren. Durch die Reduzierung der Dichte der Gasmoleküle wird die Wahrscheinlichkeit von Kollisionen und Reaktionen minimiert, was eine präzise Steuerung des Vakuumbeschichtungsprozesses ermöglicht.
Verdampfung
Die Verdampfung ist eine gängige Technik bei der Vakuumbeschichtung. Dabei wird das Beschichtungsmaterial erhitzt, bis es seinen Verdampfungspunkt erreicht, wodurch es von der festen in die Dampfphase übergeht. Das verdampfte Material kondensiert dann auf dem Substrat und bildet einen dünnen Film. Die Verdampfung kann durch thermisches Erhitzen oder Elektronenstrahlbeschuss erreicht werden.

Sputtern
Eine Sputterabscheidung ist eine physikalische Gasphasenabscheidung (PVD). Dabei wird ein Zielmaterial mit hochenergetischen Ionen (normalerweise aus einem Plasma) beschossen, die Atome von der Zieloberfläche lösen. Diese gelösten Atome lagern sich dann auf dem Substrat ab und bilden eine Beschichtung. Sputtern ermöglicht eine präzise Kontrolle der Beschichtungszusammensetzung und wird häufig für Metall- und Verbundbeschichtungen eingesetzt. Dies ist besonders nützlich für Materialien, die einen sehr hohen Schmelzpunkt haben (z. B. Wolfram) oder bei hohen Temperaturen zerfallen könnten (z. B. Nickeloxid).
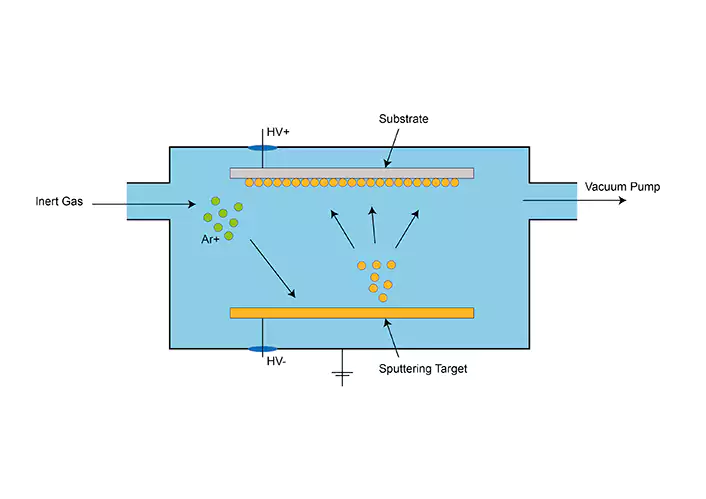
Ionenplattierung
Bei der Ionenplattierung handelt es sich um eine Technik, die Verdampfung und Ionenbeschuss kombiniert, um die Haftung und Dichte der Beschichtung zu verbessern. Bei der Ionenplattierung wird das Beschichtungsmaterial verdampft und gleichzeitig erfolgt ein Ionenbeschuss des Substrats. Die Ionen unterstützen die Reinigung der Substratoberfläche und fördern ein dichteres und haftfähigeres Beschichtungswachstum.
Chemische Gasphasenabscheidung (CVD)
CVD ist ein Prozess, bei dem Vorläufergase auf der Substratoberfläche chemisch reagieren und eine feste Beschichtung bilden. Bei der Vakuumbeschichtung werden üblicherweise Niederdruck-CVD und plasmaunterstütztes CVD eingesetzt. Beim Niederdruck-CVD kommt es zur thermischen Zersetzung oder Reaktion von Vorläufergasen, während beim plasmaunterstützten CVD Plasma zur Steigerung der chemischen Reaktionen und Abscheidungsraten eingesetzt wird.
Arten der Vakuumbeschichtungstechnologie
Es gibt verschiedene Arten und Anwendungen von Vakuumbeschichtungen. Im Folgenden finden Sie einen kurzen Überblick, um Sie mit den verwendeten Technologien vertraut zu machen.
PVD-Beschichtungen (Physical Vapour Deposition).
A. Thermische Verdampfung: Bei diesem Verfahren werden Materialien erhitzt, bis sie ihren Verdampfungspunkt erreichen, und der entstehende Dampf kondensiert auf dem Substrat und bildet eine Beschichtung.
B. Elektronenstrahlverdampfung: Ähnlich wie bei der thermischen Verdampfung wird die Verdampfung mithilfe eines Elektronenstrahls erreicht, um die Materialquelle zu erhitzen. Diese Technik wird häufig zum Auftragen von Metallen und anderen Materialien mit hohem Schmelzpunkt verwendet.
C. Sputtern: Beim Sputtern wird ein Zielmaterial mit hochenergetischen Ionen beschossen, wodurch Atome herausgeschleudert und auf dem Substrat abgelagert werden.
D. Ionenplattierung: Beim Ionenplattieren wird ein hochenergetischer Ionenstrahl in einer Vakuumkammer auf das Zielmaterial gerichtet. Die Ionen bombardieren das Ziel, wodurch Atome herausgeschleudert und auf der Substratoberfläche abgelagert werden. Im Gegensatz zum herkömmlichen Sputtern wird beim Ionenplattieren ein gleichzeitiger oder aufeinanderfolgender Ionenstrahl verwendet, um den Filmabscheidungsprozess zu unterstützen.
Beschichtungen durch chemische Gasphasenabscheidung (CVD).
A. Plasmaverstärktes CVD: Hierbei handelt es sich um eine Vakuumtechnologie, bei der Plasma zur Erzeugung reaktiver Spezies verwendet wird, die mit Vorläufergasen reagieren, was zur Abscheidung einer festen Beschichtung auf dem Substrat führt.
B. Niederdruck-CVD: Die Beschichtungsabscheidung erfolgt in einer Niederdruckumgebung unter Nutzung der thermischen Zersetzung oder Reaktion von Vorläufergasen.
C. Atmosphärendruck-CVD: Die Beschichtung wird bei Atmosphärendruck abgeschieden, was eine schnellere und kostengünstigere Verarbeitung ermöglicht.
Magnetron-Sputtern
Es handelt sich um eine Variante des Sputterns, bei der ein Magnetfeld angelegt wird, um die Effizienz und Kontrolle des Sputterprozesses zu verbessern.
Atomlagenabscheidung (ALD)
Bei der ALD wird das Substrat in eine Vakuumkammer gelegt und ein Abscheidungszyklus durchgeführt. Während jedes Zyklus wird das Substrat einem bestimmten Vorläufergas ausgesetzt, wodurch auf der Oberfläche eine selbstlimitierende Monoschicht entsteht. Das Vorläufergas reagiert mit der Oberfläche und erzeugt eine dünne Materialschicht. Überschüssige Vorläufer- und Reaktionsnebenprodukte werden dann entfernt, bevor der nächste Zyklus beginnt. Dieser kontrollierte schichtweise Abscheidungsprozess ermöglicht eine präzise Kontrolle der Filmdicke, Zusammensetzung und Gleichmäßigkeit.
ALD bietet mehrere Vorteile, darunter hervorragende Konformität, präzise Dickenkontrolle auf atomarer Ebene und die Möglichkeit, eine breite Palette von Materialien abzuscheiden, darunter Metalle, Oxide, Nitride und mehr. Es eignet sich besonders für die Abscheidung dünner Filme auf komplexen Strukturen mit hohem Aspektverhältnis, wie z. B. Halbleiterbauelementen, Mikroelektronik, katalytischen Materialien und Energiespeichersystemen.
Materialien, die bei der Vakuumbeschichtung verwendet werden
Die bei der Vakuumbeschichtung verwendeten Materialien können je nach spezifischer Anwendung und Art der Vakuumbeschichtungsmaschine variieren. Hier sind einige häufig verwendete Materialien:
Metallindustrie
Aufgrund ihrer wünschenswerten Eigenschaften wie hoher Leitfähigkeit, Reflektivität und Korrosionsbeständigkeit werden bei der Vakuumbeschichtung häufig verschiedene Metalle eingesetzt. Beispiele hierfür sind Aluminium, Titan, Kupfer, Silber, Gold und Chrom.
Legierungen
Legierungszusammensetzungen werden verwendet, um bestimmte Eigenschaften zu erreichen oder die Leistung der Beschichtung zu verbessern. Beispielsweise ist Titannitrid (TiN) eine beliebte Hartbeschichtung für die Verschleißfestigkeit, während Nickel-Chrom-Legierungen (NiCr) für den Korrosionsschutz verwendet werden.
Keramik
Keramische Materialien werden bei der Vakuumbeschichtung eingesetzt, um Hochtemperaturbeständigkeit, elektrische Isolierung und Verschleißfestigkeit zu gewährleisten. Beispiele hierfür sind Titandioxid (TiO2), Aluminiumoxid (Al2O3) und Siliziumnitrid (Si3N4).
Polymere
Bestimmte Polymere können bei der Vakuumbeschichtung verwendet werden, um funktionelle Eigenschaften wie Gleitfähigkeit, Antihaftung oder Antireflexion bereitzustellen. Beispiele hierfür sind Polytetrafluorethylen (PTFE) und Polyethylenterephthalat (PET).
Dünne Filme der Siliziumverbindung
Beim Vakuumbeschichten können auch dünne Schichten aus Materialien wie Siliziumdioxid (SiO2) oder Siliziumnitrid (Si3N4) abgeschieden werden. Diese Filme können optische Eigenschaften und Barriereeigenschaften bieten oder als Isolierschichten dienen.
Nanomaterialien
Nanoskalige Materialien, darunter Nanopartikel und Nanokomposite, erfreuen sich aufgrund ihrer einzigartigen Eigenschaften zunehmender Beliebtheit bei Vakuumbeschichtungsanwendungen. Mit Nanomaterialien lässt sich die Härte von Beschichtungen erhöhen, die Kratzfestigkeit verbessern oder bestimmte optische Effekte erzielen.
Anwendungen der Vakuumbeschichtung
Die Vakuumbeschichtung findet aufgrund ihrer Fähigkeit, die Leistung, Haltbarkeit und Ästhetik von Materialien und Oberflächen zu verbessern, ein breites Anwendungsspektrum in verschiedenen Branchen. Hier sind einige häufige Anwendungen der Vakuumbeschichtung:
Optik und optische Beschichtungen
Vakuumbeschichtungen werden in der Optikindustrie häufig zur Herstellung von Antireflexbeschichtungen, Spiegelbeschichtungen und Filtern für Linsen, Brillen, Teleskope, Mikroskope und Kameraobjektive eingesetzt. Diese Beschichtungen verbessern die Lichtdurchlässigkeit, minimieren Reflexionen und verbessern die optische Klarheit.
Elektronik- und Halbleiterindustrie
Vakuumbeschichtungen spielen in der Elektronikfertigung eine entscheidende Rolle. Sie werden zur Herstellung leitfähiger Beschichtungen für elektrische Kontakte, Leiterplatten (PCBs) und Steckverbinder verwendet. Durch Vakuumbeschichtung abgeschiedene Dünnfilme werden auch zur Isolierung, Passivierung und zum Korrosionsschutz elektronischer Komponenten eingesetzt.
Automobilindustrie
Im Automobilbereich werden Vakuumbeschichtungen eingesetzt, um die Haltbarkeit und Optik verschiedener Bauteile zu verbessern. Beispiele hierfür sind dekorative Beschichtungen für Innenverkleidungen, Korrosionsschutzbeschichtungen für Motorkomponenten, verschleißfeste Beschichtungen für Kolben und Zylinder sowie Antireflexbeschichtungen für Scheinwerfer und Spiegel.
Sonnenkollektoren und Energiesysteme
Vakuumbeschichtungen werden bei der Herstellung von Solarmodulen eingesetzt, um Antireflexbeschichtungen auf Glasoberflächen zu erzeugen. Diese Beschichtungen erhöhen die Lichtabsorption und verbessern die Effizienz der Energieumwandlung. Vakuumbeschichtungen werden auch für Schutzbeschichtungen für energieeffiziente Fenster und Wärmedämmbeschichtungen für Energiesysteme eingesetzt.
Medizinische Geräte und Ausrüstung
Vakuumbeschichtungen sind in der medizinischen Industrie von entscheidender Bedeutung, um die Leistung und Langlebigkeit medizinischer Werkzeuge und Geräte zu verbessern. Sie sorgen für Verschleißfestigkeit und Gleitfähigkeit bei chirurgischen Instrumenten, Korrosionsschutz für Implantate und biokompatible Beschichtungen für medizinische Geräte wie Stents und Katheter.
Verpackungs- und dekorative Beschichtungen
Vakuumbeschichtungen werden zu dekorativen Zwecken eingesetzt, beispielsweise zur Herstellung metallischer Oberflächen auf Schmuck, Uhren und Luxusgütern. Sie werden auch zur Bereitstellung von Barrierebeschichtungen auf Verpackungsmaterialien eingesetzt, um die Haltbarkeit von Lebensmitteln und pharmazeutischen Produkten zu verlängern.
Im Bereich der CNC-Bearbeitung sind die besten Beispiele die Beschichtung von Schneidwerkzeugen, die dafür sorgt, dass diese Werkzeuge länger halten, höheren Temperaturen standhalten und stärkere Materialien schneiden können.
Vorteile der Vakuumbeschichtung
Präzise Dickenkontrolle: Die Vakuumbeschichtung ermöglicht eine präzise Kontrolle der Dicke der aufgetragenen Beschichtungen. Dieses Maß an Kontrolle gewährleistet Gleichmäßigkeit und Konsistenz, was für die Erzielung der gewünschten funktionalen und optischen Eigenschaften von entscheidender Bedeutung ist.
Verbesserte Oberflächeneigenschaften: Vakuumbeschichtungen können die Oberflächeneigenschaften von Materialien verbessern, indem sie ihnen wünschenswerte Eigenschaften wie Härte, Verschleißfestigkeit, Schmierfähigkeit, Korrosionsbeständigkeit und Antireflexion verleihen. Diese Eigenschaften können die Haltbarkeit, Leistung und Ästhetik beschichteter Oberflächen verbessern.
Verbesserte Produkthaltbarkeit: Vakuumbeschichtungen bieten hervorragenden Schutz vor Verschleiß, Reibung, Korrosion und anderen Umweltfaktoren. Durch das Hinzufügen einer dünnen Schutzschicht verlängert die Vakuumbeschichtung die Lebensdauer der Produkte, reduziert die Notwendigkeit häufiger Austausche und verbessert die Gesamthaltbarkeit.
Vielseitigkeit bei der Materialauswahl: Vakuumbeschichtungstechniken können auf eine Vielzahl von Materialien angewendet werden, darunter Metalle, Legierungen, Keramik und Polymere. Diese Vielseitigkeit ermöglicht die individuelle Anpassung der Beschichtungseigenschaften an spezifische Anwendungen und Materialanforderungen.
Schlussfolgerung
Zusammenfassend lässt sich sagen, dass es sich bei der Vakuumbeschichtung um eine vielseitige und wertvolle Technologie handelt, die in verschiedenen Branchen zahlreiche Vorteile bietet. Es ermöglicht eine präzise Kontrolle der Beschichtungsdicke, verbessert die Oberflächeneigenschaften, verbessert die Produkthaltbarkeit und ermöglicht eine individuelle Anpassung der Materialauswahl.
Trotz ihrer Vorteile weist die Vakuumbeschichtung auch Einschränkungen auf, darunter hohe anfängliche Einrichtungs- und Wartungskosten, Einschränkungen bei der Beschichtungsfläche und Prozesskomplexität. Bei sorgfältiger Berücksichtigung dieser Faktoren und ordnungsgemäßer Umsetzung können die Vorteile der Vakuumbeschichtung diese Einschränkungen jedoch überwiegen.
Im Rahmen unserer Verarbeitungsdienstleistungen Kompetente Bearbeitung bietet verschiedene Vakuumbeschichtungsdienstleistungen an. Wir bieten Vakuumbeschichtungstechnologie über unsere eigene komplette Lieferkette an, sodass wir umfassende Dienstleistungen von der Bearbeitung bis zu verschiedenen Oberflächenbehandlungen anbieten können.