Mechanische Endbearbeitung:
Wie bearbeitet:
Dies bedeutet, dass nach der Bearbeitung keine zusätzliche Oberflächenbehandlung erforderlich ist.
Edelstahl könnte Korrosion in der Luft selbst widerstehen. Normalerweise ist keine zusätzliche Oberflächenbehandlung erforderlich.
Aluminium könnte selbst eine feine und dichte Oxidschicht bilden, die vor Korrosion in der Luft schützt. Manchmal ist die Oberfläche „wie bearbeitet“ gut genug.
In anderen Fällen, in denen Korrosionsschutz und Aussehen nicht im Vordergrund stehen, ist die Oberfläche im bearbeiteten Zustand die einfachste Wahl.
Sandstrahlen:
Beim Sandstrahlen wird Druckluft als Energiequelle verwendet, um einen Hochgeschwindigkeitsstrahl zu erzeugen, der das Schleifmaterial (Quarzsand, Schmirgel, Glaspellets usw.) auf die Oberfläche des Werkstücks sprüht. Durch die Aufprall- und Schneidwirkung des Schleifmittels auf die Werkstückoberfläche kann die Oberfläche einen gewissen Grad an Sauberkeit und eine gewisse Rauheit erreichen, sodass die mechanischen Eigenschaften der Werkstückoberfläche verbessert werden. Es verbessert die Ermüdungsfestigkeit des Werkstücks. Außerdem vergrößert es die Gesamtoberfläche des Werkstücks und erhöht somit die Haftung weiterer Oberflächenbehandlungseffekte (Farbe, Kunststoffspray usw.).
Der Prozess kann als Endbearbeitung oder als Vorprozess vor anderen Oberflächenbehandlungen eingesetzt werden.
In einer technischen Zeichnung gibt es normalerweise eine Zahl, die die in diesem Prozess verwendete Sandgröße kennzeichnet, zum Beispiel # 120 Sandstrahlen. #120 bedeutet hier, dass der Sand das Sieb mit 120 Löchern pro Quadratzoll passieren kann.
Wir verwenden standardmäßig Sand Nr. 120.
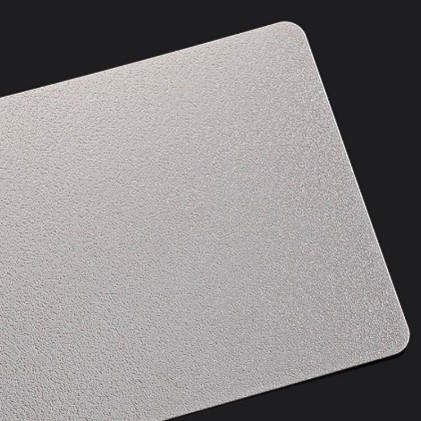
Bürsten:
Verwenden Sie Schleifpapier oder Sandtuch, um die Oberfläche eines Metallteils zu bürsten. Es entsteht eine Art flaches lineares Array-Muster auf der Oberfläche. Der Hauptzweck dieser Veredelung besteht darin, leichte Maschinenspuren abzudecken.
Es kann als Endbearbeitung oder als Vorbehandlung vor anderen Oberflächenbehandlungen verwendet werden.
Es gibt auch eine Zahl zur Markierung der Sandgröße.
Wir verwenden #100 und #120 am häufigsten.
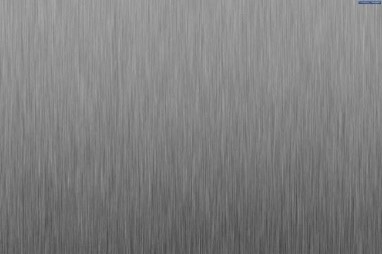
Taumeln:
Eine Trommelmaschine rührt einen Haufen Schleifmittel (auch Trommelmedien genannt) um. Der häufigste Tumbling hat einen Durchmesser von etwa 1 Meter. Bei den Schleifmitteln kann es sich um Glaskugeln, Edelstahlkugeln oder Nadeln oder verschiedene Arten von Steinen handeln. Schleifmittel gibt es in verschiedenen Größen und Formen. Sie können Kugeln, Dreiecke oder unregelmäßige Quadrate sein, mit Größen zwischen einigen mm und einigen cm.
Beim Trommelpolieren, auch Vibrationspolieren genannt, handelt es sich lediglich um einen Prozess, bei dem die Teile mit den gewünschten Trommelmedien vermischt werden, manchmal auch mit einem chemischen Mittel, um eine glänzendere Oberfläche zu erzielen.
Abhängig vom gewählten Medium entsteht eine eher glatte Oberfläche, die teils glänzend, teils nicht glänzt. Der Hauptzweck dieses Prozesses besteht darin, eine einheitliche Oberfläche zu schaffen, die alle Teile berücksichtigt und auch scharfe Kanten bricht.

Polieren:
Ziel dieses Prozesses ist es, eine sehr glatte und glänzende Oberfläche zu erzeugen. Jede Anforderung an eine Oberflächenrauheit von weniger als Ra0.6 um muss möglicherweise poliert werden. Die gebräuchlichste Methode besteht darin, die Oberfläche einfach mit Sandpapier und später mit Textilmaterial zu bürsten. Die Medien zum Bürsten der Oberfläche sollten von grob bis fein, von hart bis weich sein. Ein typischer Arbeitsablauf besteht darin, zuerst Schleifpapier Nr. 120, dann Nr. 200, dann langsam bis Nr. 2000 und später Sackleinenscheibe, Stoffscheibe und Wollscheibe zu verwenden.
Je hart das Werkstück ist, desto einfacher lässt sich eine glattere Oberfläche erzielen.
Mechanische Oberflächenbehandlungen verändern das Aussehen der Oberfläche, bieten jedoch keinen zusätzlichen Korrosionsschutz. Wenn wir zusätzliche Hilfe zum Schutz der Teile vor Korrosion benötigen, benötigen wir eine chemische und elektrochemische Oberflächenbehandlung.

Chemische und elektrochemische Oberflächenbehandlung
Die meisten chemischen und elektrochemischen Oberflächenbehandlungen zielen darauf ab, eine Art dichten Metalloxidfilm oder Metallverbindungsfilm auf der Metalloberfläche zu erzeugen. Einige Metalle können diesen Film auf natürliche Weise erzeugen, beispielsweise Nickel und Chrom. Galvanotechnik und die stromlose Beschichtung machen sich diese Eigenschaft zunutze, um die Oberfläche des Werkstücks mit einer solchen Metallschicht zu überziehen, dass der dadurch erzeugte dichte Film das Werkstück vor Oxidation schützt. Der Vorteil dieses Schutzes besteht darin, dass Ni-Cr bei leichter Beschädigung der Oxidschicht durch Einwirkung von Luft die Oxidschicht regenerieren und so weitere Korrosion verhindern kann.
Die durch die Aluminiumlegierung in der Luft erzeugte Oxidschicht reicht nicht aus, um die Anforderungen an eine langfristige Korrosionsbeständigkeit zu erfüllen. Daher ist eine bestimmte chemische und elektrochemische Reaktion erforderlich, um den Oxidfilm zu stärken, der eloxiert wird.
Eine weitere Maßnahme zur Verhinderung der Oxidation des Werkstücks besteht darin, die Oberfläche des Werkstücks vollständig mit einer anderen Substanz zu bedecken und so das Werkstück vor dem Kontakt mit der Luft zu schützen. B. Lackieren, Kunststoffspritzen usw. Die Korrosionsbeständigkeit solcher Maßnahmen hängt von den Eigenschaften und der Dicke der vom Werkstück bedeckten Substanz ab.
Passivieren:
Passivierung von Edelstahl:
Durch das Beizen von Edelstahl kann ein Teil des freien Eisens auf der Oberfläche des Werkstücks entfernt werden, wodurch der Chromgehalt der Oberfläche erhöht wird. Chrom bildet einen dichten Oxidfilm auf der Werkstückoberfläche. Der durch den höheren Chromgehalt gebildete Schutzfilm ist dichter und härter und verbessert so die Korrosionsbeständigkeit von Werkstücken aus Edelstahl.
Der Hauptbestandteil von Passivierungsmitteln für Edelstahl ist Salpetersäure oder Zitronensäure. Abhängig von der Zusammensetzung des Edelstahls werden auch Flusssäure, Kaliumchromat und Hydroxylverbindungen dotiert.
Die Dicke des Passivierungsfilms ist sehr gering und hat kaum Einfluss auf Abmessungen und Toleranzen.
Passivierung der Aluminiumlegierung/Chromat-Umwandlungsbeschichtung/Alodine:
Bei der Passivierung von Aluminiumlegierungen wird hauptsächlich eine Chromatlösung verwendet, um eine Chromatumwandlungsschicht auf der Oberfläche des Werkstücks zu erzeugen. Der Prozess wird auch als bezeichnet Chromat-Konversionsbeschichtung, Alodine und Chem-Film. In der Anfangszeit wurde meist sechswertiges Chromat verwendet. Aufgrund seiner hohen Toxizität wurde es in der Neuzeit eliminiert und durch dreiwertiges Chromat ersetzt. Die Passivierungsschicht ist dünn, was grundsätzlich keinen Einfluss auf Größe und Toleranz hat und auch keinen Einfluss auf die Leitfähigkeit der Aluminiumlegierung hat. Allerdings sind die Korrosions- und Oxidationsbeständigkeit nicht so gut wie beim Eloxalverfahren.
Die Chromatkonversionsschicht erhöht die Haftung des Werkstücks zu anderen Beschichtungen, daher wird dieses Verfahren auch zur Vorbehandlung beim Lackieren eingesetzt.
Galvanotechnik:
Unter Verwendung des Prinzips der Elektrolyse wird das Substrat in die Kathode gelegt und mit der negativen Elektrode des Gleichstroms verbunden, und das plattierte Metall wird mit der Anode und der positiven Elektrode verbunden. Nach der Elektrifizierung findet eine elektrolytische Reaktion durch einen Elektrolyten statt, der plattierte Metallionen enthält, und die Oberfläche der Kathode wird mit einer Schicht aus plattiertem Metall bedeckt.
Die Hauptziele der Galvanisierung sind Korrosionsschutz, besseres Aussehen, Verschleißfestigkeit, Erhöhung der Härte usw.
Verkupfern: Wird als Grundierung verwendet, um die Haftung der Galvanikschicht zu verbessern.
Vernickelung: Wird als Grundierung oder für das Erscheinungsbild verwendet, um die Korrosions- und Verschleißfestigkeit zu verbessern.
Verchromung: Verbessert die Korrosionsbeständigkeit und erhöht die Oberflächenhärte.
Vergoldung: Verbesserung der elektrischen Leitfähigkeit und Verschleißfestigkeit.
Versilberung: Verbessert die elektrische Leitfähigkeit.
Verzinkt: Grundierung oder Korrosionsschutz.
Aufgrund der unregelmäßigen Form des Werkstücks ist die Stromdichte an jedem Teil des Werkstücks nicht genau gleich. Gleichzeitig wird der Elektrolytfluss aufgrund der Form des Werkstücks ungleichmäßig sein. Daher ist die Beschichtungsdicke jedes Teils des Werkstücks unterschiedlich. Die meisten Galvanikprozesse wirken sich auf die Werkstückgröße aus, was sich aufgrund ungleichmäßiger Schichtdicken negativ auf die Toleranzen auswirken kann.
Stromloses Plattieren:
Die stromlose Beschichtung ist eine Methode, die keinen Strom benötigt und nach dem Prinzip einer Redoxreaktion ein starkes Reduktionsmittel in einer Lösung mit Metallionen verwendet, um Metallionen zu Metallen zu reduzieren und sie auf der Oberfläche verschiedener Materialien abzuscheiden, um dichte Schichten zu bilden Beschichtungen.
Beispiel: Geben Sie Eisen in eine Kupfersulfatlösung und auf der Oberfläche des Eisens bildet sich eine Kupferschicht. Aufgrund der Notwendigkeit, die Haftung der Beschichtung, die Produktkonsistenz, die Kosten und andere Faktoren in der industriellen Produktion zu berücksichtigen, ist die Zusammensetzung der beim stromlosen Plattieren verwendeten Lösung natürlich viel komplizierter. Es enthält neben der Verbindung bzw. Komplexlösung des Beschichtungsmetalls auch verschiedene Zusatzstoffe wie Puffer, Beschleuniger und Stabilisatoren. Aber die Grundprinzipien sind die gleichen.
Die Kosten für die stromlose Beschichtung sind viel höher als für die Galvanisierung. Die Dicke der Beschichtung ist viel einfacher zu kontrollieren als beim Galvanisieren. Wenn die Form des Werkstücks komplex ist, gibt es immer noch einige Bereiche, in denen die Dicke der Beschichtung aufgrund des begrenzten Flusses der Galvanisierungslösung nicht gleichmäßig ist. Aber insgesamt ist die Toleranzkontrolle bei stromlos plattierten Werkstücken viel einfacher als beim Galvanisieren.
Die stromlose Beschichtung eignet sich zum Vernickeln, Versilbern, Verkupfern usw. auf Gusseisen, Kohlenstoffstahl, Kupferlegierungen, Aluminiumlegierungen, Edelstahl und anderen Substraten.
Chemisches Polieren:
Wenn das Metall in die Säurelösung eingetaucht wird, werden die unebenen Teile der Metalloberfläche aufgrund der größeren Kontaktfläche schneller geätzt als die glatten Teile. Die Industrie nutzt dieses Phänomen, um die Rauheit der Werkstückoberfläche zu verbessern (weniger rau zu machen), was durch chemisches Polieren erfolgt. Chemisches Polieren findet hauptsächlich bei Edelstahl, Kupfer und Kupferlegierungen Anwendung. Chemisches Polieren hat eine gute Polierwirkung auf Stahlteile, insbesondere auf kohlenstoffarmen Stahl, sodass chemisches Polieren für einige Stahlteile verwendet werden kann, die mechanisch schwer zu polieren sind.
Da die Polierflüssigkeit zunächst den natürlich auf der Metalloberfläche gebildeten Schutzfilm zerstören muss, sind ihre Hauptbestandteile eine Mischung aus Säuren wie Schwefelsäure, Salpetersäure, Salzsäure, Phosphorsäure und Flusssäure. Chemisches Polieren kann allein zur Verbesserung der Oberflächenbeschaffenheit des Werkstücks oder als Zwischenschritt in anderen Oberflächenbehandlungen zur Verbesserung des Glanzes des Endprodukts eingesetzt werden. Beispielsweise trägt beim Eloxieren einer Aluminiumlegierung das chemische Polieren als Zwischenschritt dazu bei, ein glänzendes Endprodukt zu erhalten.
Schwärzung/Schwarzoxid:
Wird im Allgemeinen für Kohlenstoffstahl verwendet.
Nach dem alkalischen Waschen und Beizen zur Entfernung von Fett und Verschmutzungen erhitzen und in einer Passivierungslösung einweichen. Die Passivierungslösung ist normalerweise eine Mischung aus Natriumcarbonat, Natriumnitrat, Alkali und Natriumhydroxid. Nach der chemischen Reaktion bildet sich auf der Oberfläche des Kohlenstoffstahls eine dichte Schutzschicht aus Eisenoxid, die einen schwarzen Glanz aufweist.
Daher der Name „Schwärzung“. Dieses Verfahren hat die Rostschutzfunktion von Kohlenstoffstahl verbessert, ist jedoch weitaus weniger effektiv als Galvanikverfahren wie Verzinken und Vernickeln. In einer Umgebung mit relativ hoher Temperatur und Luftfeuchtigkeit besteht immer noch die Gefahr, dass das geschwärzte Werkstück rostet. Der durch diesen Prozess gebildete Oxidfilm ist extrem dünn und sein Einfluss auf die Werkstücktoleranz kann völlig vernachlässigt werden.
Gelegentlich wird das Schwärzungsverfahren auch bei Edelstahl angewendet. Im Allgemeinen besteht der Zweck darin, die Farbveränderung der Oberfläche zu verfolgen, was sich kaum positiv auf die Korrosionsschutzleistung von Edelstahl auswirkt.
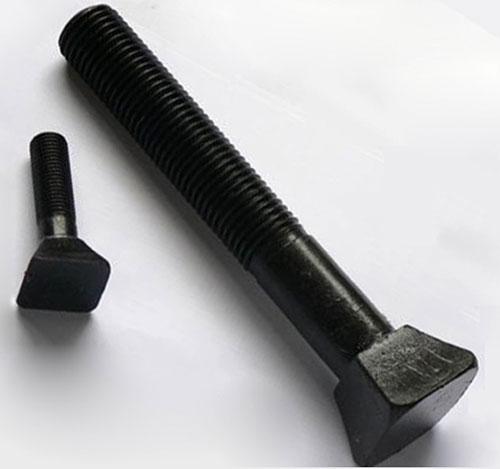
Eloxieren:
Eloxieren kann zur Oberflächenbehandlung von Aluminiumlegierungen und Titanlegierungen eingesetzt werden.
Das Eloxieren von Aluminiumlegierungen ist die häufigste und erfolgreichste Oberflächenbehandlung von Aluminiumlegierungen. Aluminium und seine Legierungen werden in einen entsprechenden Elektrolyten (z. B. Schwefelsäure, Chromsäure, Oxalsäure usw.) als Anode gegeben und unter bestimmten Bedingungen und unter Einwirkung eines angelegten Stroms elektrolysiert. Das Aluminium der Anode oder seine Legierung wird oxidiert und es bildet sich eine dünne Schicht Aluminiumoxid auf der Oberfläche.
Die Dicke der Aluminiumoxidschicht hängt von Spannung, Strom, Elektrolytkonzentration, Temperatur, Reaktionszeit usw. ab. Durch diesen Prozess entsteht eine poröse Struktur, die mit einem Farbstoff eingefärbt und anschließend verschlossen werden kann. Dadurch erhält man Endprodukte in verschiedenen Farben. Der Glanz des Endprodukts kann auch durch chemisches Polieren während der Vorbehandlung oder durch eine Laugenbehandlung erhöht werden, um eine gleichmäßig matte Oberfläche zu erhalten.
Eloxieren Typ II:
Dies ist die Art der Eloxierung, auf die sich die anodische Oxidation von Aluminiumlegierungen im Allgemeinen bezieht. Auch als Farbanodisierung bekannt. Dabei werden eine relativ hohe Temperatur des Elektrolyten, eine hohe Konzentration, eine niedrige Spannung und eine niedrige Stromstärke angewendet, und der erhaltene Oxidfilm ist dünn, im Allgemeinen unter 15 µm. Nicht leitend, guter Korrosionsschutz. Die Verschleißschutzleistung der Oberfläche wurde verbessert. Wenn die Vorbehandlungszeit streng kontrolliert wird, kann ein Endprodukt mit höherer Toleranz erhalten werden.
Eloxieren Typ III:
Es wird auch als Hartbeschichtungsanodisierung bezeichnet. Die Elektrolyttemperatur ist niedriger, die Konzentration ist geringer, die Spannung und die Stromstärke sind höher und die Dicke des erhaltenen Oxidfilms ist dicker, größer als 15 µm. Hohe Oberflächenhärte, >300HV. Nicht leitend, ausgezeichneter Korrosionsschutz; einige hartbeschichtete eloxierte Aluminiumlegierungen können einem Salznebeltest mehr als 30 Tage standhalten. Aufgrund der hohen Schichtdicke (bis zu 250 µm) ist es schwierig, die Toleranz des Werkstücks zu kontrollieren.
Eloxierte Werkstücke verfügen im Allgemeinen über Aufhängelöcher zur Verbindung mit den Elektroden, und die Aufhängelöcher werden nach Abschluss des Prozesses nicht von der Oxidschicht bedeckt.
Einfluss von Aluminiumlegierungsmaterialien auf die Anodisierung
Die meisten heute in der Industrie verwendeten Eloxierungen sind Schwefelanodisierungen.
Reines Aluminium (Serie 1000) bildet beim Eloxieren mit Schwefelsäure eine nahezu transparente Oxidfilmstruktur. Diese Schichtstruktur wurde ordnungsgemäß versiegelt, was die Oberflächenhärte und Korrosionsbeständigkeit von reinem Aluminium erheblich verbessert. Andere Serien von Aluminiumlegierungen wie der Al-Cu-Legierungsoxidfilm der Serie 2000 sind graurot; Al-Mn-Legierung der Serie 3000, der Oxidfilm ist grau oder gelb; Der Oxidfilm aus einer Al-Si-Legierung der Serie 4000 ist dunkelgrau bis schwarz; 5000 Die Transparenz des Oxidfilms ist bei der Al-Mg-Legierung der Serie deutlich reduziert; Das Eloxierungsergebnis der 6000er-Serie ist das beste und der Oxidfilm ist transparenter. Der Oxidfilm der 7000er-Serie ist dunkelgrau und der Oxidfilm der Al-Cr-Legierung ist gelb.
Bei Aluminiumgussserien mit hohem Si-Gehalt wie der ADC-Serie ist der Oxidfilm instabil, lässt sich leicht abziehen und erscheint dunkelgrau oder schwarz, hauptsächlich weil Si als unlöslicher Bestandteil im Oxidfilm verbleibt. Daher erfordert die Oxidation von Aluminiumguss die Zugabe von Metallsalzen oder organischen Säuren zur Oxidationslösung. In der tatsächlichen Produktion wird bei Kleinserien- oder Einzelstück-Aluminiumgussprodukten im Allgemeinen keine Eloxierung angewendet.
Mikrolichtbogenoxidation (MAO) oder Mikroplasmaoxidation (MPO):
Das Prinzip der Mikrolichtbogenoxidation ist noch nicht ganz klar. Es ist nur bekannt, dass die Metalloberfläche des Substrats unter Einwirkung höherer elektrischer Spannung im Kontaktteil des Elektrolyten einen kurzzeitigen Szintillationslichtbogen erzeugt und die Temperatur mehrere tausend Grad erreichen kann. Die Metalloberfläche des Materials schmilzt, bricht aus und kristallisiert und bildet eine Keramikschicht. Es eignet sich für Legierungen mit mehr als 40 % Aluminium, Magnesium und Titan.
Die durch Mikrolichtbogenoxidation erzeugte Keramikschicht weist eine extrem hohe Härte auf. Nehmen wir als Beispiel eine Aluminiumlegierung nach der Behandlung, die Härte der Keramikschicht beträgt >1200HV. Der Autor hat Mikrolichtbogenoxidation zur Behandlung von Aluminiumlegierungen eingesetzt. Der Fräser hinterlässt keine Spuren, wenn er über die Oberfläche schneidet. Die Oberflächengüte ist geringer als beim Polieren, aber höher als bei der normalen Bearbeitung.
Wenn das Werkstück vor der Mikrolichtbogenoxidation poliert wird, verringert sich die Oberflächengüte nach der Mikrolichtbogenoxidation und die Oberflächengüte rauer Werkstücke wird nach der Mikrolichtbogenoxidation verbessert. Die Keramikschicht auf Aluminiumbasis weist eine starke Korrosionsbeständigkeit, einen Salzsprühtest > 480 Stunden, eine gute Isolierung und eine graue oder dunkelgraue Farbe auf. Die Dicke der Keramikschicht kann durch Steuerung der Prozesszeit gesteuert werden, sodass ein Endprodukt mit höherer Toleranz erhalten werden kann. Die Kosten sind viel höher als beim herkömmlichen Eloxieren.
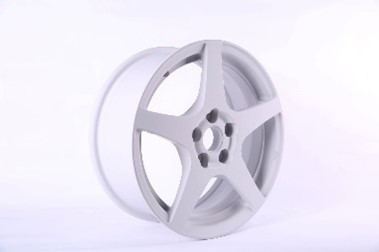
Sprühfarbe:
Sprühlackieren ist das gebräuchlichste Oberflächenbehandlungsverfahren. Es zerstäubt den Lack mit Hilfe von Druckluft oder Zentrifugalkraft durch eine Spritzpistole oder einen Scheibenzerstäuber in gleichmäßige und feine Tröpfchen und trägt ihn auf die Oberfläche des Werkstücks auf. Der Hauptzweck besteht darin, Korrosion zu verhindern und die Farbe zu verstärken.
Elektrostatisches Spray:
Auch Abstauben genannt. Die Spritzpistole sprüht Harzpulver durch die Wirkung von Hochdruckluft, und das pulverförmige Harz wird durch elektrostatische Hochspannungsgeräte in der Nähe der Düse aufgeladen. Das Harz wird vom Werkstück mit entgegengesetzter Polarität adsorbiert, und wenn das Pulver eine bestimmte Dicke erreicht, stoppt die Adsorption aufgrund der elektrostatischen Abstoßung. Anschließend wird das Pulver durch Erhitzen geschmolzen und verfestigt sich zu einem harten Film auf der Oberfläche des Werkstücks.
Durch Sprühen kann das Werkstück in verschiedenen Farben erhalten werden. Durch eine ausreichende Dicke der elektrostatischen Sprühbehandlung kann eine gute Witterungsbeständigkeit erreicht werden. Viele Aluminiumprofile für den Außenbereich verwenden elektrostatisches Sprühen, um die Witterungsbeständigkeit zu erhöhen.
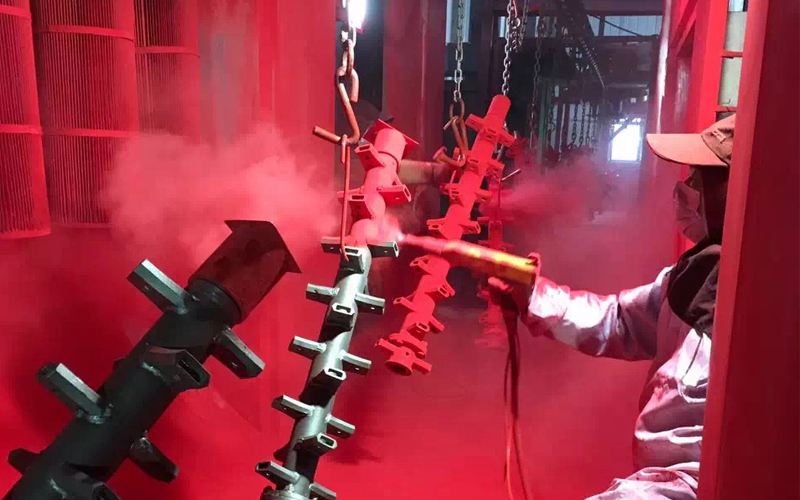
Elektrophoretische Beschichtung/ Elektrophoretische Malerei:
Die Implementierungsumgebung der elektrophoretischen Beschichtung ähnelt der der Galvanisierung, bei der das Metallwerkstück mit der Elektrode verbunden und in die Lösung eingetaucht werden muss. Das Prinzip und die Lösungszusammensetzung sind jedoch recht unterschiedlich. Die Wirkstoffe der elektrophoretischen Beschichtungslösung sind hauptsächlich Epoxidharze, Lacke oder andere wasserbasierte Beschichtungen.
Das Werkstück wird durch einen elektrischen Strom geleitet, um die in der Lösung suspendierten Partikel anzuziehen und sie auf der Oberfläche des Substrats abzuscheiden, um einen Schutzfilm zu bilden, dessen Dicke durch Strom und Zeit gesteuert werden kann. Die elektrophoretische Beschichtung umfasst eine anodische elektrophoretische Beschichtung (das Werkstück ist mit der Anode verbunden) und eine kathodische elektrophoretische Beschichtung (das Werkstück ist mit der Kathode verbunden). In der Industrie wird vor allem die kathodische Elektrotauchlackierung eingesetzt. Obwohl der fertige Film in seinen Eigenschaften der Sprühfarbe ähnelt, sind seine Moleküle dichter gepackt und die Oberflächenbeschaffenheit ist hoch. Die Hauptfunktion der Elektrophorese ist der Korrosionsschutz und die Oberflächendekoration.
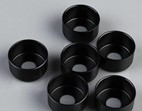