Rippen in Spritzgussteilen erhöhen die Festigkeit und Steifigkeit und machen das Teil steifer. Ohne Rippen bräuchten wir ein dickeres und schwereres Teil, um die gleiche Steifigkeit zu erreichen. Um übermäßiges Einsinken und Gewicht zu vermeiden, sollte die Dicke der Rippen etwa 50 % der Nennwandstärke betragen. Darüber hinaus bietet es sich an, die Rippen über runde Ecken mit der Basis zu verbinden. In diesem Artikel werden die Best Practices für Rippendesigns von Spritzgussteilen besprochen.
Die Rolle von Rippen in Spritzgussteilen
Rippen sind ein wesentlicher Bestandteil der Funktionalität von Spritzgussteilen aus Kunststoff.
Verbessern Sie die Haltbarkeit und Steifigkeit des Produkts, ohne die Hauptwände des Formteils zu verdicken. Minimieren Sie Kunststoffabfälle im Kunststoffspritzgussprozess. Vermeiden Sie es, dem Produkt unnötiges Gewicht hinzuzufügen. Optimieren Sie die Kosteneffizienz.
Rippen können Produktverwerfungen und Verformungen aufgrund ungleichmäßiger Kräfte aufgrund unterschiedlicher Wandstärken verhindern.
Rippen können zusätzliche Wege für den Fluss von geschmolzenem Kunststoff schaffen, um die dünnen Abschnitte von Spritzgussteilen zu füllen.
Die richtigen Maße, um Einfallstellen zu vermeiden
Einer der wichtigsten Grundsätze bei der Gestaltung von Kunststoffspritzgussteilen ist die Einhaltung einer gleichmäßigen Wandstärke. Bei Wandstärkenveränderungen kommt es bei Kunststoffspritzgussteilen zu Einfallstellen. Durch die Rippen kommt es zwangsläufig zu gewissen Veränderungen der Wandstärke der Spritzgussteile. Daher steht bei der Entscheidung über die Größe der Rippenabschnitte vor allem die Frage im Vordergrund, wie Einfallstellen vermieden werden.
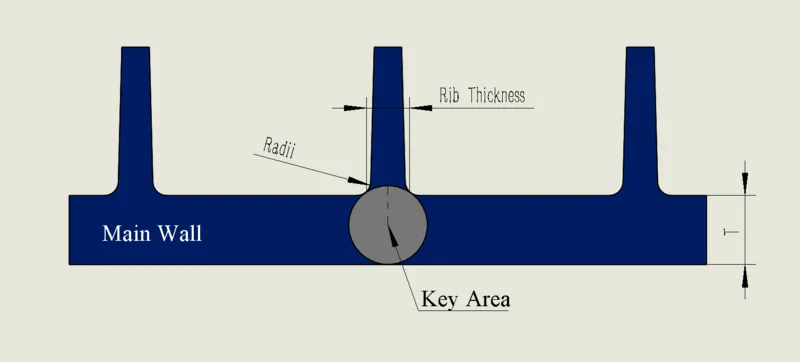
Wie in der Abbildung gezeigt, sollte beim Hinzufügen von Rippen der Durchmesser des Schlüsselbereichs so weit wie möglich reduziert werden. Die Größe des Schlüsselbereichs stellt die durch die Rippen verursachte Wandstärkenänderung dar. Offensichtlich sind der Eckenradius und die Rippendicke die wichtigsten Zahlen zur Minimierung des Schlüsselbereichs.
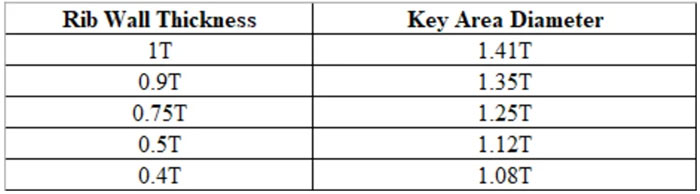
Rippenstärke
Die Tabelle listet die Auswirkung der Rippendicke auf den Schlüsselbereichsdurchmesser auf. Wenn die Rippendicke unter 50 % der Nennwanddicke liegt, vergrößert sich der Schlüsselflächendurchmesser nur um weniger als 12 % der Nennwanddicke. Eine allgemeine Regel für die Rippenkonstruktion besteht darin, die Rippendicke bei etwa 50 % der Nennwanddicke zu halten. Abhängig von der Eigenschaft des verwendeten Kunststoffmaterials wird eine Rippendicke von 40 % bis 75 % der Nennwanddicke empfohlen.
Rippenradien
Es wird empfohlen, dort, wo die Rippe auf die Basis oder Seitenwand trifft, einen Radius einzuschließen. Dies reduziert die Spannungskonzentration, erhöht die Rippenfestigkeit und sorgt für einen gleichmäßigeren Kunststoffmaterialfluss beim Kunststoffspritzgießen. Auch Formen mit größeren Radien sind etwas günstiger in der Herstellung. Größere Radien vergrößern jedoch den Durchmesser des Schlüsselbereichs und erhöhen die Wahrscheinlichkeit von Einfallstellen. Es wird empfohlen, die Radien zwischen 25 % und 50 % der Nennwandstärke einzuhalten.
Rippenhöhe vs. Anzahl
Die folgende Tabelle zeigt die Ergebnisse einer Fallstudie zum Einfluss der Rippenhöhe auf die Steifigkeit von Teilen. Das Trägheitsmoment in der Tabelle gibt an, wie schwierig es ist, ein Kunststoffteil in eine bestimmte Richtung zu biegen. Wie die Tabelle zeigt, können wir zwei Schlussfolgerungen ziehen: 1. Die Höhe der Rippen kann die Steifigkeit des Spritzgussteils in einem geometrischen Verlauf erhöhen. 2. Die Rippen erhöhen die Steifigkeit des Formteils, ohne ihm viel Gewicht zu verleihen. Wenn beispielsweise in der Tabelle die Rippenhöhe auf 12 mm erhöht wird, erhöht sich die Steifigkeit um das 7.6-fache, während das Gewicht nur um 15 % zunimmt. Zum Vergleich: Wenn die Gesamtwandstärke des Materials verdoppelt wird, verdoppelt sich das Gewicht des Materials, aber die Steifigkeit erhöht sich nur um das Siebenfache.
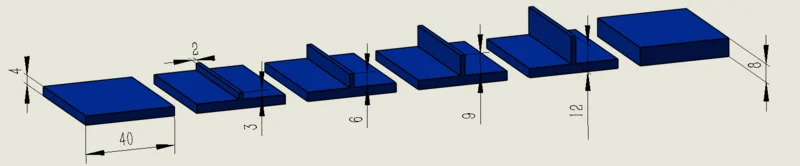
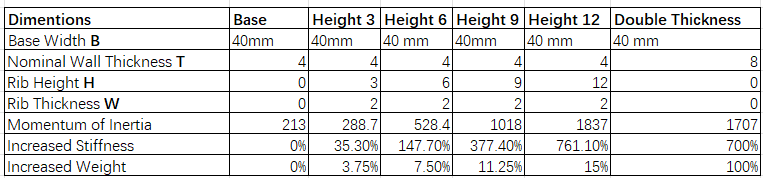
Allerdings verursacht eine hohe Rippenhöhe auch Probleme. Wenn die Rippenhöhe zu hoch ist, kann es beim Kunststoffspritzguss zu Füllproblemen kommen. Dies liegt daran, dass der geschmolzene Kunststoff Schwierigkeiten hat, die hohen und engen Räume der Rippenhöhle vollständig zu füllen, was zu einer unvollständigen oder unzureichenden Füllung führt. Der Kunststoff erreicht möglicherweise nicht die Spitze der Rippen, was zu ungefüllten oder teilweise gefüllten Abschnitten führt, was die strukturelle Integrität der Rippe schwächen und zu Fehlern im endgültigen Formteil führen kann.
Die empfohlene maximale Rippenhöhe beträgt das Dreifache der Nennwandstärke. Wenn zusätzliche Steifigkeit erforderlich ist, ist es vorzuziehen, mehrere kürzere Rippen zu verwenden.
Entformungsschräge
Damit das Teil im Spritzgussprozess reibungslos ausgeworfen werden kann, muss das Entformungsschräge ist notwendig. Der Entformungswinkel von Rippen wird im Allgemeinen auf 0.5 bis 2° eingestellt, am häufigsten sind 1 bis 1.5°. Die Größe des Entformungswinkels wird hauptsächlich unter zwei Gesichtspunkten betrachtet.
1. Die Eigenschaft des Materials, insbesondere die Schrumpfung und Viskosität des Materials. Materialien mit hoher Viskosität und starker Schrumpfung haften eher am Formkern, daher ist ein größerer Entformungswinkel erforderlich. Materialien mit niedriger Viskosität und geringer Schrumpfung können kleinere Entformungswinkel verwenden.
2. Vermeiden Sie es, die obere Breite der Rippe zu klein zu machen. Dies erfordert eine umfassende Berücksichtigung der Rippendicke, -höhe und des Entformungswinkels. Wenn die obere Breite der Rippe zu klein ist, wird es schwierig, das Teil während des Kunststoffspritzgusses auszuwerfen, da möglicherweise nicht genügend Platz für die Auswurfstifte übrig bleibt. Wie in der Abbildung unten dargestellt, konzentriert sich die Biegespannung des Teils hauptsächlich an der Oberseite der Rippe. Aus mechanischen Gründen sollte die Oberseite der Rippe auch nicht zu schmal sein. Aus dem gleichen Grund sollte auch die Rippenhöhe innerhalb eines bestimmten Bereichs kontrolliert werden.
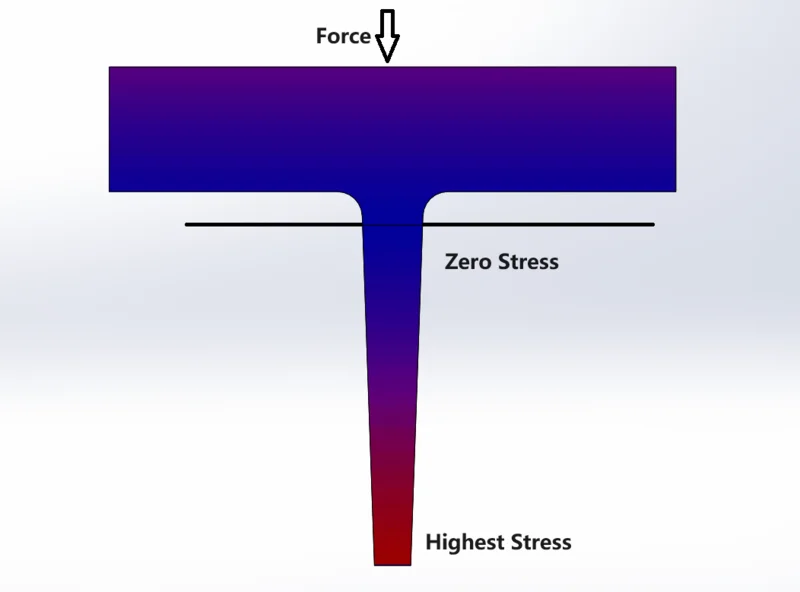
Die Eigenschaften des Materials
Aus produktionstechnischer Sicht haben die physikalischen Eigenschaften des Materials, wie Schmelzviskosität und Schrumpfung, großen Einfluss auf die Rippengestaltung. Für stark schrumpfendes Material sollten relativ geringe Rippendicken (z. B. 40 % Nennwanddicke oder weniger) und kleinere Radien verwendet werden. Bei schrumpfarmen Materialien kann die Rippendicke für eine bessere Steifigkeit bis zu 75 % der Nennwanddicke betragen. Ein Material mit hoher Schmelzviskosität erfordert geringere Rippenhöhen oder größere Rippendicken, um sicherzustellen, dass das Spritzgussteil beim Spritzgießen vollständig gefüllt ist.
Die Richtung der Rippen
Aus konstruktiver Sicht optimiert die Positionierung der Rippen in Richtung der Biegekraft die Steifigkeit. Aus produktionstechnischer Sicht verringert die Ausrichtung der Rippen an der Materialflussrichtung die Wahrscheinlichkeit einer unvollständigen Füllung und von Lufteinschlüssen. Wenn auf beiden Seiten Steifigkeit erforderlich ist, sollten auf jeder Seite Rippen eingesetzt werden.
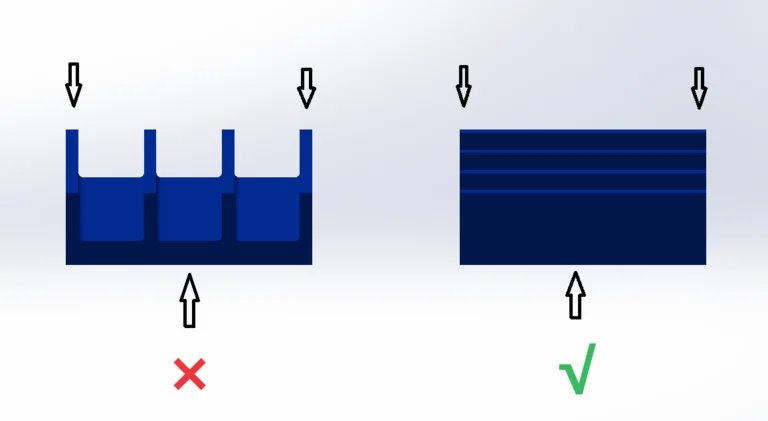

Rippenabstand
Wie bereits erwähnt, werden mehrere kürzere Rippen einer einzelnen hohen Rippe vorgezogen. Wenn mehrere Rippen verwendet werden, ist ein übermäßiger Engstand unerwünscht. Die Rippen sollten einen Mindestabstand einhalten, der ihrer Höhe entspricht und das Dreifache der Primärwandstärke nicht überschreiten darf. Wenn die Rippen näher beieinander liegen, besteht die Gefahr einer unzureichenden Kühlung der Rippenbasis, was möglicherweise den Spritzgussprozess verlängert und sowohl die Zykluszeit als auch die Teilekosten erhöht. Wenn der Rippenabstand zu gering ist, bedeutet dies außerdem, dass der Formkern zwischen den Rippen möglicherweise zu dünn ist und während des Herstellungsprozesses leicht beschädigt werden kann.
Rippen-Entkernung
Wenn dicke Rippen erforderlich sind, entkernen Sie sie hinten oder darunter. Dadurch werden die Rippenwände dünner und ein kosmetisches Einsinken kann verhindert werden. Das Ausbohren wird häufig bei Rippenkreuzungen eingesetzt. Auch die Größe des Kerns sollte der Regel folgen, eine gleichmäßige Wandstärke aufrechtzuerhalten.
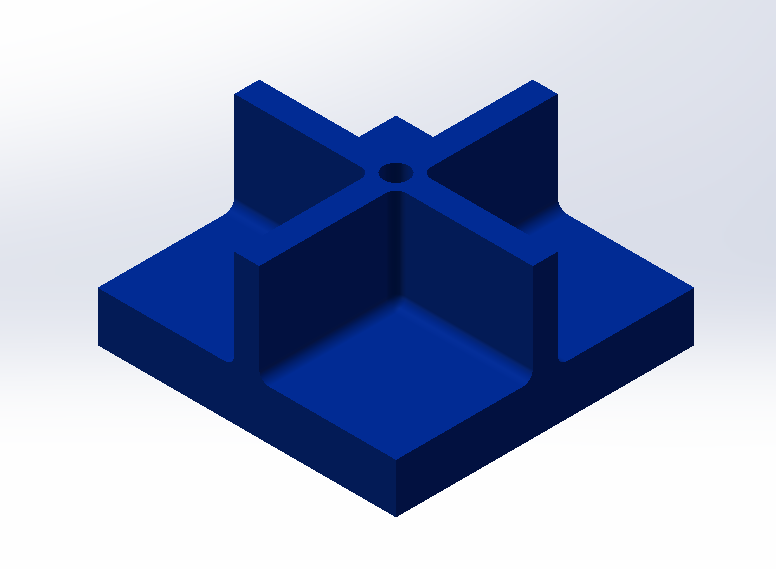
Regeln sind gemacht um gebrochen zu werden
Zusammenfassend lautet der allgemeine Leitfaden zur Rippenkonstruktion von Kunststoffspritzgussteilen wie folgt:
Rippenstärke 40 % bis 75 % der Nennwandstärke.
Rippenradien 25 % bis 50 % der Nennwandstärke.
Die maximale Rippenhöhe beträgt weniger als das Dreifache der Nennwandstärke.
Mehrere Rippen werden einer einzelnen hohen Rippe vorgezogen.
Die Materialeigenschaften spielen eine wichtige Rolle bei der Bestimmung der Rippenabmessungen.
Der Rippenabstand sollte mindestens das Dreifache der Nennwandstärke betragen.
Die Rippenrichtung sollte entlang der Biegekraft- bzw. Materialflussrichtung beim Spritzgießen erfolgen.
Dies sind jedoch nur allgemeine Richtlinien. Im realen Design werden diese Richtlinien in vielen erfolgreichen Fällen nicht vollständig übernommen. Selbst wenn diese Richtlinien vollständig befolgt werden, gibt es beim Kunststoffspritzguss immer noch viele schwierige Probleme. Beispielsweise führen Rippen, die dünner als die Nennwandstärke sind, dazu, dass die Rippen zuerst abkühlen und die Hauptwand später abkühlt, wodurch sich das Teil verzieht. Beim tatsächlichen Design stoßen wir häufig auf Konflikte zwischen diesen Richtlinien, was die Auswahl erschwert. Diese Richtlinien sind manchmal nicht immer anwendbar. Beispielsweise müssen bei einigen Strukturteilen keine kosmetischen Effekte berücksichtigt werden, so dass selbst das Auftreten von Einfallstellen kein großes Problem darstellt. In diesem Fall kann davon ausgegangen werden, dass die Dicke der Rippen mit der Dicke der Hauptwand übereinstimmt. Manchmal sind Einfallstellen völlig inakzeptabel. In diesem Fall muss darüber nachgedacht werden, eine noch geringere Rippendicke zu verwenden und am Rippengrund nur Radien von 0 zu verwenden.
Insgesamt handelt es sich bei den in diesem Artikel beschriebenen Gestaltungsrichtlinien für Rippen von Kunststoffspritzgussteilen lediglich um Richtwerte, die in der Praxis flexibel anzuwenden und anzupassen sind.
Wenn Sie sich mit dem Design von Kunststoffteilen befassen, kommt es darauf an, die richtige Unterstützung zu haben. Erkunden CapableMachining.com für wertvolle Einblicke und Zusammenarbeit. Durch die Nutzung ihres Fachwissens können Sie Ihre Designs verbessern und so Effizienz und Erfolg sicherstellen. Mit CapableMachining.com Als Ihr Partner wird die Verwirklichung Ihrer Kunststoffspritzgussteile-Designs zu einem reibungsloseren Prozess.