Wie Galvanisieren funktioniert und wo es eingesetzt wird
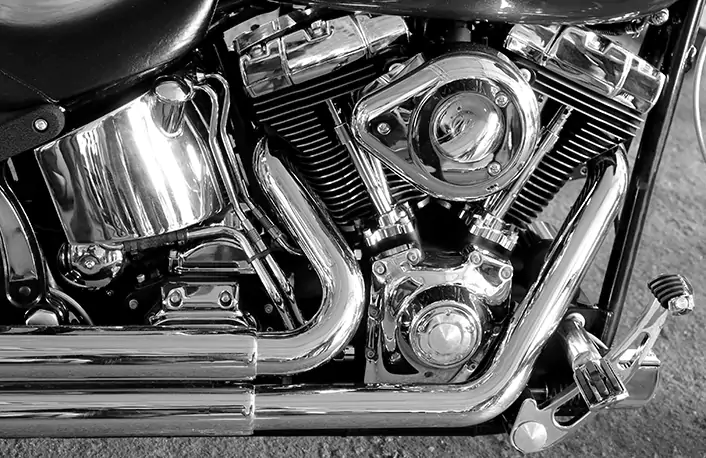
Inhaltsverzeichnis Was ist Galvanisieren? Wie funktioniert Galvanisieren? Elektrolyse Elektroden Galvanisierungsbad Abscheidung des Metalls Arten der Galvanisierung Metalle für die Galvanisierung Galvanisieren und Toleranzen Kantenaufbau Trommelplattierung vs. Gestellplattierung Schwer fließende Bereiche Galvanisieren von Kunststoffen Wie werden…