Die Pulvermetallurgie (PM) umfasst verschiedene Methoden zur Herstellung von Materialien oder Bauteilen unter Verwendung von Metallpulvern. Durch den Einsatz von PM-Prozessen kann die Abhängigkeit von subtraktiven Fertigungstechniken minimiert oder ganz eliminiert werden. Dies verringert nicht nur den Materialabfall, sondern führt auch zu Kosteneinsparungen bei der Herstellung des Endprodukts.
Was ist Pulvermetallurgie?
Die Pulvermetallurgie dient als Mittel zur Herstellung einzigartiger Materialien, die durch Schmelzen oder andere herkömmliche Verfahren nur schwer oder gar nicht erhältlich sind. Ein bemerkenswertes Beispiel ist Wolframcarbid (WC), ein wichtiges Produkt in der Industrie. WC besteht aus gebundenen WC-Partikeln und Kobalt und wird häufig zum Schneiden und Formen verschiedener Metalle verwendet.
Darüber hinaus liefert die Pulvermetallurgie eine vielfältige Produktpalette, darunter Sinterfilter, poröse, ölimprägnierte Lager, elektrische Kontakte und Zahnräder. Diese Produkte finden in verschiedenen Branchen breite Anwendung.
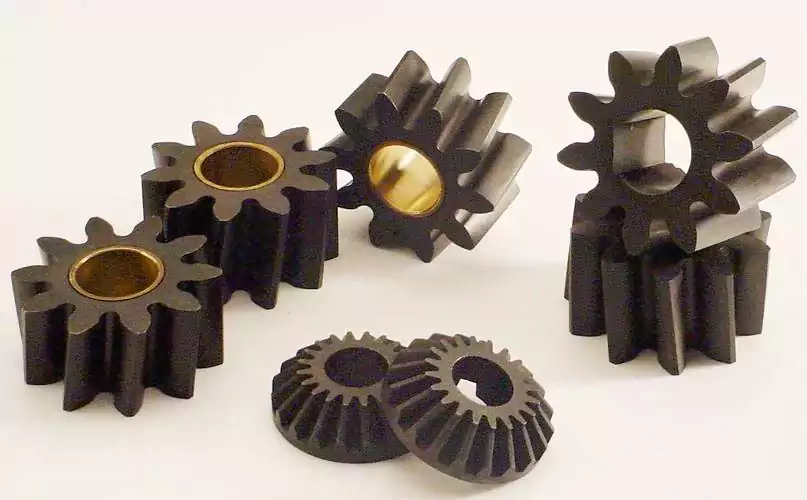
In den letzten Jahren hat sich die Einführung von additiven Fertigungstechniken (Additive Manufacturing, AM) auf der Basis von Metallpulvern in großem Maßstab, wie z. B. das selektive Lasersintern, zu einer neuen und kommerziell bedeutenden Kategorie innerhalb der Pulvermetallurgieanwendungen entwickelt. Diese Entwicklung hat weitere Möglichkeiten für die Herstellung komplexer Bauteile und Objekte aus Metallpulvern eröffnet.
Pulvermetallurgie-Prozess
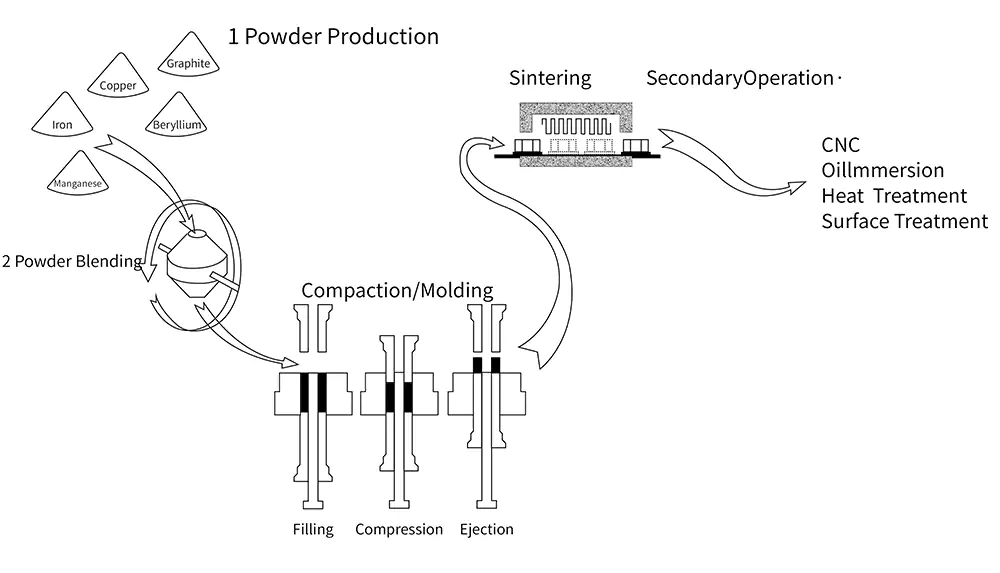
Der Pulvermetallurgieprozess umfasst mehrere wichtige Schritte zur Umwandlung von Metallpulvern in fertige Komponenten. Hier finden Sie einen Überblick über den typischen Prozess der Pulvermetallurgie:
Pulverherstellung
Metallpulver werden durch Methoden wie Zerstäubung, mechanisches Legieren oder chemische Prozesse hergestellt. In dieser Phase wird sichergestellt, dass die flüssigen Metallpulver die gewünschte Zusammensetzung und die gewünschten Eigenschaften haben.
Pulvermischung
Verschiedene Pulver können gemischt werden, um bestimmte Legierungszusammensetzungen zu erreichen oder bestimmte Eigenschaften zu verbessern. Durch das Mischen von Pulver wird eine homogene Mischung vor der Weiterverarbeitung gewährleistet.
Verdichtung
Die gemischten Pulver werden in einen Formhohlraum gegeben und einer Hochdruckverdichtung unterzogen. Bei diesem Verfahren werden die Pulver mit Kraft verdichtet, wodurch ein Grünling mit der gewünschten Form und Dichte entsteht.
Sintern
Der Grünling wird in einer kontrollierten Atmosphäre oder im Vakuum auf eine Temperatur unterhalb des Schmelzpunkts des Metalls erhitzt. Durch das Sintern kommt es zu einer Bindung der Partikel, was zu einer Verdichtung und der Bildung eines festen Bauteils mit verbesserter mechanischer Festigkeit führt.
Nachbehandlung
Zusätzliche Behandlungen können angewendet werden, um die Eigenschaften oder die Oberflächenbeschaffenheit des Sinterteils zu verbessern. Diese Vorgänge können Bearbeitung, Wärmebehandlung, Imprägnierung, Beschichtung oder Oberflächenmodifizierung umfassen.
Inspektion und Qualitätskontrolle
Die fertigen Komponenten werden einer strengen Prüfung unterzogen, um sicherzustellen, dass sie den erforderlichen Spezifikationen entsprechen. Dies kann Maßmessungen, Mikrostrukturanalysen, mechanische Prüfungen und zerstörungsfreie Prüfungen umfassen.
Konfektionierung
Bei Bedarf können die Komponenten weiteren Veredelungsvorgängen wie Polieren, Plattieren oder Beschichten unterzogen werden, um die gewünschten ästhetischen oder funktionalen Eigenschaften zu erzielen.
Das Pulvermetallurgieverfahren bietet Vorteile wie Kosteneffizienz, Materialeffizienz, komplexe Geometrien und die Möglichkeit, Teile mit maßgeschneiderten Eigenschaften herzustellen. Es findet Anwendung in verschiedenen Branchen, darunter Automobil, Luft- und Raumfahrt, Elektronik, Medizin und Konsumgüter.
Methoden der Pulvermetallurgie
Die Pulvermetallurgie umfasst verschiedene Verfahren zur Herstellung von Bauteilen aus Metallpulvern. Hier sind einige gängige Methoden der Pulvermetallurgie:
Presspulvermetallurgie
Die Presspulvermetallurgie, auch Pulververdichtung oder Pulverpressen genannt, ist ein Herstellungsverfahren, bei dem Metallpulver mithilfe von Hochdruckgeräten in gewünschte Formen verdichtet werden. Der Prozess beginnt mit der Auswahl und Mischung von Metallpulvern, gefolgt von der Platzierung der Pulver in einem Formhohlraum. Durch die Anwendung einer hohen Druckkraft werden die Pulver verdichtet, sodass ein Grünling mit der gewünschten Form und Dichte entsteht. Anschließend wird der Grünling gesintert, wobei sich die Pulver zu einem festen Bauteil verbinden.
Metallspritzguss
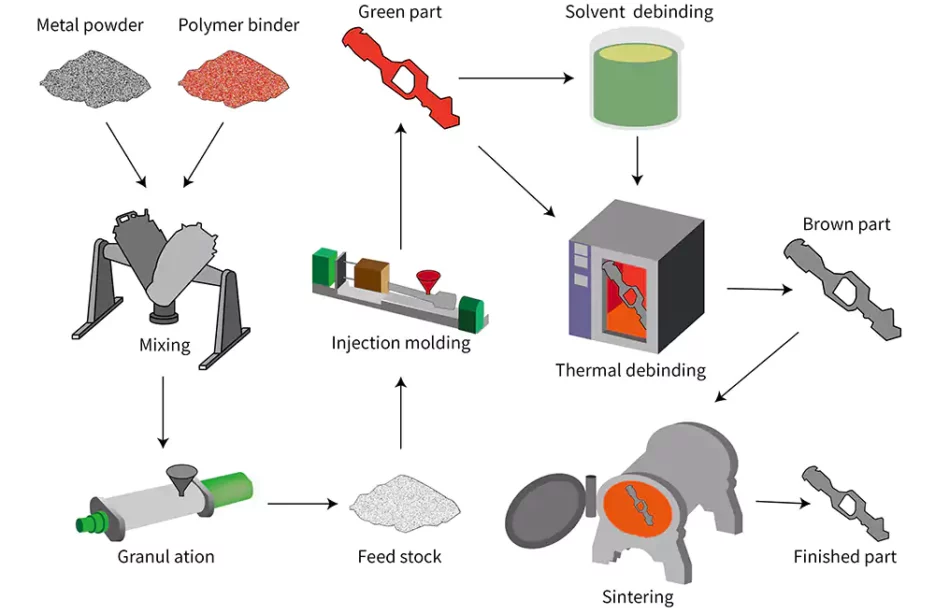
Metallspritzguss (MIM) wurde 1973 von Parmatech in den USA erfunden. In den frühen 1980er Jahren unternahmen viele Unternehmen in Europa und Japan erhebliche Anstrengungen, um diese Technologie zu erforschen und rasch bekannt zu machen. Insbesondere Mitte der 1980er Jahre machte die Technologie nach der Industrialisierung große Fortschritte und verzeichnete erstaunliche jährliche Wachstumsraten.
Weltweit sind mittlerweile über 100 Unternehmen an der Entwicklung und dem Vertrieb dieser Technologie beteiligt. Die MIM-Technologie hat sich zu einem dynamischen Hightech-Bereich in der neuen Fertigungsindustrie entwickelt. Es handelt sich um eine bahnbrechende Technologie in der globalen metallurgischen Industrie und eine wichtige Richtung für die Entwicklung der Pulvermetallurgietechnologie.
Die MIM-Technologie, die verschiedene Disziplinen wie Kunststoffformung, Polymerchemie, Pulvermetallurgie und Materialwissenschaft vereint, ermöglicht die schnelle und präzise Herstellung hochdichter, hochpräziser, dreidimensionaler Verbundformteile mittels Formspritzguss. Es ermöglicht die Umsetzung von Designideen in Produkte mit spezifischen Strukturen und Funktionsmerkmalen und erleichtert die Massenproduktion von Komponenten. Es stellt ein neues Paradigma in der Fertigungstechnologiebranche dar.
Metallspritzguss (MIM) ist ein fortschrittliches Metallbearbeitungsverfahren, bei dem fein pulverisiertes Metall mit einem Bindemittel kombiniert wird, um ein spezielles „Ausgangsmaterial“ zu erzeugen. Das am häufigsten verwendete Bindemittel ist ein thermoplastisches Polymer wie PP, PE, PS oder manchmal auch Wachs. Dieses Ausgangsmaterial wird dann mithilfe von Spritzgusstechniken geformt und verfestigt. Das Verfahren ermöglicht die effiziente Produktion großvolumiger und komplexer Teile in einem einzigen Schritt.
Theoretisch kann MIM für große Teile eingesetzt werden, in der Industrie wird die MIM-Technologie jedoch hauptsächlich für große Mengen kleiner Teile eingesetzt. MIM-Rohstoffe können aus verschiedenen Metallen bestehen, wobei Edelstahl aufgrund seiner weit verbreiteten Verwendung in der Pulvermetallurgie die häufigste Wahl ist.
Nach der ersten Formungsphase wird das Bindemittel im Ausgangsmaterial durch einen als Entbindung bezeichneten Prozess entfernt. Die häufigste Entbinderung erfolgt durch Erhitzen der Formteile, sodass das Bindemittel durch die kleinen Kanäle in den Formteilen extrahiert werden kann. Anschließend werden die Metallpartikel einer Diffusionsbindung und Verdichtung unterzogen, um die gewünschten Festigkeitseigenschaften zu erreichen. Bemerkenswert ist, dass dieser Verdichtungsprozess typischerweise zu einer Schrumpfung von etwa 15 bis 25 % in jeder Dimension des Endprodukts führt.
Sobald der Entbinderungsprozess abgeschlossen ist, wird der verbleibende bindemittelfreie Teil, der sogenannte Braunteil, einem Hochtemperatur-Sinterprozess unterzogen. Beim Sintern wird das Teil in einer kontrollierten Atmosphäre erhitzt, wodurch sich die Metallpartikel miteinander verbinden und verdichten. Dabei erfährt das Teil eine Schrumpfung, die zu einer weiteren Verdichtung führt.
Nach dem Sintern kann das Teil weiteren Endbearbeitungsvorgängen wie maschineller Bearbeitung, Polieren oder Oberflächenbehandlung unterzogen werden, um die gewünschte endgültige Form, Abmessungen und Oberflächeneigenschaften zu erreichen. Die typische Dichte, die nach dem Metallspritzgussverfahren (MIM) erreicht wird, ist im Allgemeinen hoch und liegt nahe an der theoretischen Dichte des verwendeten Metallmaterials. Im Allgemeinen kann die Dichte von MIM-Teilen zwischen 95 % und 99.8 % der theoretischen Dichte liegen. Das Erreichen von Dichten über 98 % ist bei vielen MIM-Anwendungen üblich.
MIM findet in zahlreichen Branchen Anwendung und produziert kleine Komponenten für ein breites Produktspektrum. Durch die Nutzung der Vorteile von MIM können Hersteller eine kostengünstige Produktion, komplizierte Designs und verbesserte mechanische Eigenschaften erreichen.
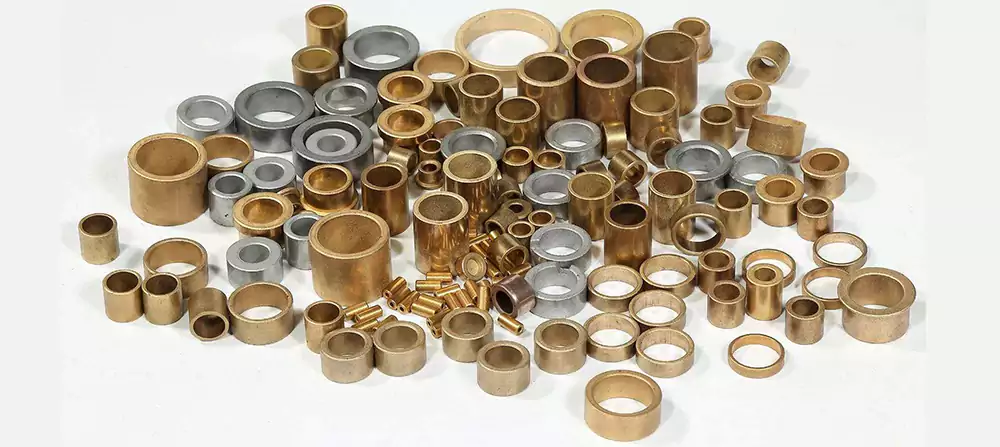
Durch elektrischen Strom unterstütztes Sintern
Stromunterstütztes Sintern (ECAS)-Technologien basieren auf elektrischen Strömen, um Pulver zu verdichten. Dies hat den Vorteil, dass die Produktionszeit drastisch verkürzt wird (von 15 Minuten beim langsamsten ECAS auf einige Mikrosekunden beim schnellsten), keine lange Ofenerwärmung erforderlich ist und nahezu theoretische Dichten möglich sind der Nachteil einfacher Formen. Die in ECAS eingesetzten Pulver können dank der Möglichkeit des direkten Sinterns ohne Vorpressen und ohne einen Grünling auf Bindemittel verzichten.
Formen sind auf die endgültige Form des Teils ausgelegt, da sich die Pulver verdichten, während sie den Hohlraum unter angelegtem Druck füllen, wodurch das Problem von Formschwankungen durch nichtisotropes Sintern und Verzerrungen durch die Schwerkraft bei hohen Temperaturen vermieden wird. Die gebräuchlichste dieser Technologien ist das Heißpressen, das bei der Herstellung von Diamantwerkzeugen für die Bauindustrie eingesetzt wird. Funkenplasmasintern und Elektrosinterschmieden sind zwei moderne, industriell kommerzielle ECAS-Technologien.
Vorteile der Pulvermetallurgie
Als Fertigungsverfahren zur Herstellung von Metallbauteilen bietet die Pulvermetallurgie (PM) mehrere Vorteile. Hier sind einige der wichtigsten Vorteile:
Kosteneffizienz
Die Pulvermetallurgie kann im Vergleich zu herkömmlichen Herstellungsverfahren wie maschineller Bearbeitung oder Gießen eine kostengünstige Methode sein. Es ermöglicht eine hohe Materialausnutzung, da während des Prozesses wenig bis gar kein Material verschwendet wird. Darüber hinaus kann PM den Bedarf an umfangreichen Bearbeitungsvorgängen reduzieren, was die Kosten weiter senkt.
Komplexe Geometrie
PM ermöglicht die Herstellung von Komponenten mit komplexen Formen und komplizierten Merkmalen, deren Herstellung mit anderen Methoden schwierig oder kostspielig sein kann. Die Flexibilität des Pulvermetallurgieverfahrens ermöglicht die Herstellung von Bauteilen mit inneren Hohlräumen, Hinterschneidungen und feinen Details.
Materialvielfalt
Die Pulvermetallurgie ist auf eine Vielzahl von Materialien anwendbar, darunter verschiedene Eisen- und Nichteisenmetalle sowie Keramik und Verbundwerkstoffe. Diese Vielseitigkeit ermöglicht die Herstellung von Komponenten mit unterschiedlichen Eigenschaften und Merkmalen, um spezifische Anwendungsanforderungen zu erfüllen.
Verbesserte Materialeigenschaften
Durch den PM-Prozess können Bauteile mit hervorragenden mechanischen Eigenschaften entstehen. Während der Verdichtungs- und Sinterphase verbinden sich die Metallpulver miteinander, was zu einer dichten und homogenen Struktur führt. Dadurch entstehen Bauteile mit hoher Festigkeit, guter Verschleißfestigkeit und verbesserter Dimensionsstabilität.
Kontrolle über die Porosität
Die Porositätskontrolle ist einer der wesentlichen Vorteile von PM. Durch die Anpassung der Pulvereigenschaften, Verdichtungsparameter und Sinterbedingungen ist es möglich, die Porosität des Endbauteils zu steuern. Dies ermöglicht maßgeschneiderte Porositätsniveaus, was bei Anwendungen vorteilhaft sein kann, bei denen Porosität gewünscht ist, beispielsweise für selbstschmierende oder Filtrationskomponenten.
Weniger Abfall und Umweltbelastung
Bei der Pulvermetallurgie handelt es sich um einen endkonturnahen Herstellungsprozess, d. h. es werden Komponenten hergestellt, die nur minimale zusätzliche Bearbeitung oder Verarbeitung erfordern. Dadurch werden Abfall und Energieverbrauch reduziert, was zu einer geringeren Umweltbelastung im Vergleich zu herkömmlichen Herstellungsmethoden führt.
Verbesserte Materialausnutzung
PM ermöglicht die Verwendung von recycelten Materialien und Abfallmaterialien, die bei anderen Prozessen anfallen. Diese Materialien können mit neuen Pulvern gemischt werden, um Komponenten herzustellen, was die Nachhaltigkeit fördert und die Rohstoffkosten senkt.
Konsistenz und Wiederholbarkeit
Die Pulvermetallurgie bietet eine hervorragende Kontrolle über den Herstellungsprozess, was zu einer gleichbleibenden und wiederholbaren Produktqualität führt. Dies ist insbesondere für Branchen von Vorteil, die eine hohe Präzision und Zuverlässigkeit erfordern, wie beispielsweise die Automobil-, Luft- und Raumfahrt- und Medizinbranche.
Anwendungen der Pulvermetallurgie
Die Pulvermetallurgie (PM) findet aufgrund ihrer Vielseitigkeit und Fähigkeit, Komponenten mit spezifischen Eigenschaften herzustellen, in verschiedenen Branchen Anwendung. Hier sind einige häufige Anwendungen der Pulvermetallurgie-Technologie:
Automobilindustrie
Pulvermetallurgie wird in der Automobilindustrie häufig zur Herstellung von Komponenten wie Zahnrädern, Nockenwellen, Pleueln, Ventilsitzeinsätzen, Kettenrädern und Ölpumpenrotoren eingesetzt. PM-Komponenten bieten eine hohe Festigkeit, Verschleißfestigkeit und Maßgenauigkeit und eignen sich daher für anspruchsvolle Automobilanwendungen.
Luft-und Raumfahrtindustrie
Die Luft- und Raumfahrtindustrie nutzt mehrere pulvermetallurgische Verfahren zur Herstellung kritischer Komponenten wie Turbinenschaufeln, Kompressorteile und Strukturkomponenten. PM-Komponenten in Luft- und Raumfahrtanwendungen bieten Hochtemperaturbeständigkeit, Korrosionsbeständigkeit und geringes Gewicht und tragen so zu einer verbesserten Flugzeugleistung bei.
Elektronik-Industrie
Pulvermetallurgie wird in der Elektronikindustrie zur Herstellung elektrischer Kontakte, magnetischer Komponenten, Kühlkörper und Steckverbinder eingesetzt. PM-Komponenten bieten eine gute elektrische Leitfähigkeit, magnetische Eigenschaften und Wärmemanagementfähigkeiten.
Elektrowerkzeuge und Haushaltsgeräte
Die Pulvermetallurgie wird bei der Herstellung von Komponenten für Elektrowerkzeuge, Haushaltsgeräte und Haushaltsgegenstände eingesetzt. Beispiele hierfür sind Zahnräder, Lager, Buchsen und Schneidwerkzeuge. PM-Komponenten bieten in diesen Anwendungen eine hohe Verschleißfestigkeit, Dimensionsstabilität und verbesserte Effizienz.
Öl-und Gasindustrie
Pulvermetallurgie wird in der Öl- und Gasindustrie zur Herstellung von Komponenten wie Ventilkörpern, Pumpenteilen und Bohrwerkzeugkomponenten eingesetzt. PM-Komponenten in diesem Bereich bieten eine hohe Festigkeit, Korrosionsbeständigkeit und die Fähigkeit, rauen Betriebsbedingungen standzuhalten.
Verteidigungs- und Schusswaffenindustrie
Pulvermetallurgie wird im Verteidigungsbereich zur Herstellung von Schusswaffenkomponenten wie Waffenläufen, Schlagbolzen und Verschlussblöcken eingesetzt. PM-Komponenten in Schusswaffen bieten eine verbesserte Festigkeit, Haltbarkeit und Maßgenauigkeit.
Schlussfolgerung
Zusammenfassend lässt sich sagen, dass die Pulvermetallurgie (PM) ein äußerst vielseitiges Herstellungsverfahren ist, das zahlreiche Vorteile bei der Herstellung von Metallbauteilen bietet. Es ermöglicht die Erstellung komplexer Formen, eine präzise Maßkontrolle und die Verwendung einer breiten Palette von Materialien.
Insgesamt ist die Pulvermetallurgie ein wertvolle Herstellungstechnik Das Unternehmen spielt weiterhin eine wichtige Rolle bei der Herstellung hochwertiger Metallkomponenten, trägt zum Fortschritt in verschiedenen Branchen bei und erfüllt die Anforderungen moderner technischer Herausforderungen.