Beim Gießen handelt es sich um einen Prozess, bei dem geschmolzenes Metall in eine Form gegossen wird, um bestimmte Abmessungen zu erreichen. Es gibt zwei Hauptarten des Castings: Feinguss und Druckguss. Aufgrund ihrer Vor- und Nachteile werden diese Methoden zur Herstellung verschiedener Arten von Produkten eingesetzt. Inwiefern unterscheidet sich Feinguss vom Druckguss?
Feinguss
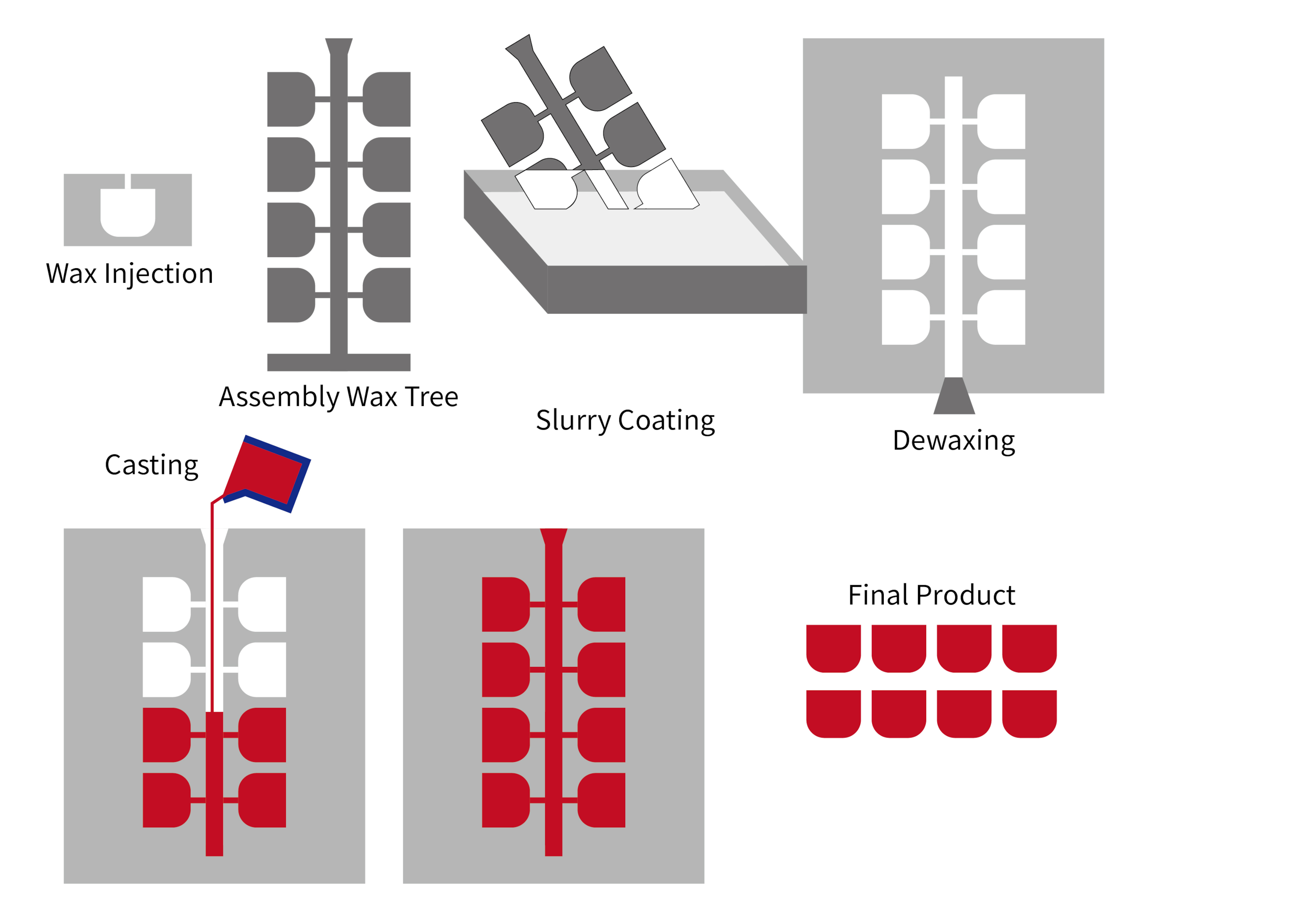
Der Feinguss, auch Präzisionsguss oder Wachsausschmelzguss genannt, umfasst mehrere Schritte. Zunächst wird ein Wachsmodell in der gewünschten Form des Bauteils erstellt. Dieses Muster wird dann an einem Anguss befestigt, um eine Baugruppe zu bilden. Anschließend wird die Baugruppe in flüssige Keramik getaucht, um eine Schutzschicht zu bilden, und das Wachs wird durch Erhitzen in einem Ofen entfernt. Anschließend wird die Schale mit flüssigem Metall gefüllt und auf Raumtemperatur abgekühlt, bevor die Schale geschnitten wird, um die massiv geformten Komponenten zu erhalten.
Schritte des Feingussprozesses
Feinguss, auch Präzisionsguss oder Wachsausschmelzguss genannt, umfasst typischerweise die folgenden Prozessschritte:
Erstellen des Wachsmusters
Es wird ein Wachsmodell in der gewünschten Form des endgültigen Bauteils erstellt. Dies kann von Hand oder maschinell erfolgen.
Versammlung
Das Wachsmodell wird dann an einem Gussrahmen befestigt, um einen Montagebaum zu bilden. Mehrere Wachsmodelle können auf einem einzigen Gussrahmen montiert werden.
Keramiktauchen
Die Baugruppe wird in eine Keramikaufschlämmung getaucht, um eine Keramikschale zu bilden. Diese Hülle dient als Form für das geschmolzene Metall.
Wachsentfernung
Die Keramikschale wird dann in einem Ofen erhitzt, um die Keramik auszuhärten und das Wachsmodell wegzuschmelzen, wodurch ein Hohlraum in der Keramikschale in Form des Modells zurückbleibt.
Metallfüllung
Die Keramikschale wird mit geschmolzenem Metall gefüllt, typischerweise indem das Metall durch den Einguss in den Hohlraum gegossen wird. Man lässt das Metall abkühlen und erstarren.
Schneiden der Schale
Sobald das Metall abgekühlt und erstarrt ist, wird die Keramikschale abgebrochen, wodurch der Guss mit den noch daran befestigten Einzelteilen zum Vorschein kommt.
Konfektionierung
Anschließend werden die Einzelteile vom Guss getrennt und überschüssiges Material entfernt. Abhängig von der gewünschten Oberfläche erfordern die Teile möglicherweise zusätzliche Bearbeitung, Polieren oder andere Endbearbeitungsprozesse.
Vorteile des Feingusses
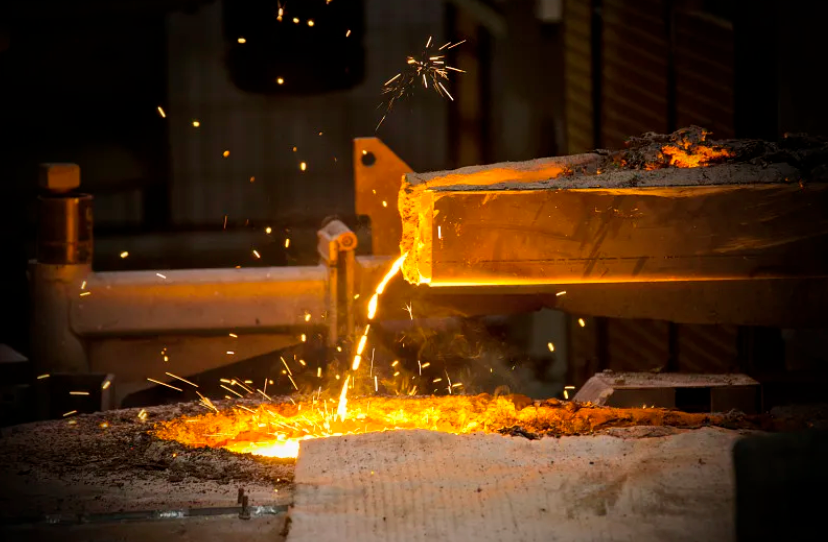
Feinguss bietet mehrere Vorteile, darunter:
Geeignet für komplexe Designs
Feinguss eignet sich gut für die Herstellung komplexer Teile mit komplizierten Formen, feinen Details und dünnen Wänden. Dies liegt daran, dass das Wachsmodell leicht manipuliert werden kann, um nahezu jede Form zu erzeugen.
Null Formschrägewinkel
Beim Feingießen können Teile ohne Entformungswinkel hergestellt werden, d. h. dem Winkel zwischen dem Teil und der Richtung der Formfreigabe. Dadurch können auch Teile mit vertikalen oder hinterschnittenen Flächen ohne aufwändige Werkzeugbestückung hergestellt werden.
Niedrigere Werkzeugkosten für geringere Stückzahlen
Feinguss ist im Allgemeinen kostengünstiger als andere Gussverfahren, wenn kleinere Teilemengen hergestellt werden, da die Werkzeugkosten geringer sind. Dies macht es zu einer kostengünstigen Option für die Produktion kleiner Stückzahlen.
Hervorragende Oberflächenbeschaffenheit
Durch Feinguss können Teile mit einer glatten Oberflächenbeschaffenheit und engen Maßtoleranzen hergestellt werden, wodurch zusätzliche Bearbeitungs- oder Endbearbeitungsvorgänge überflüssig werden können.
Vielseitige Materialoptionen
Feinguss kann mit einer breiten Palette von Materialien verwendet werden, darunter Stahl, Aluminium, Messing und Bronze, was eine größere Flexibilität bei der Teilekonstruktion und Materialauswahl ermöglicht.
Nachteile des Feingusses
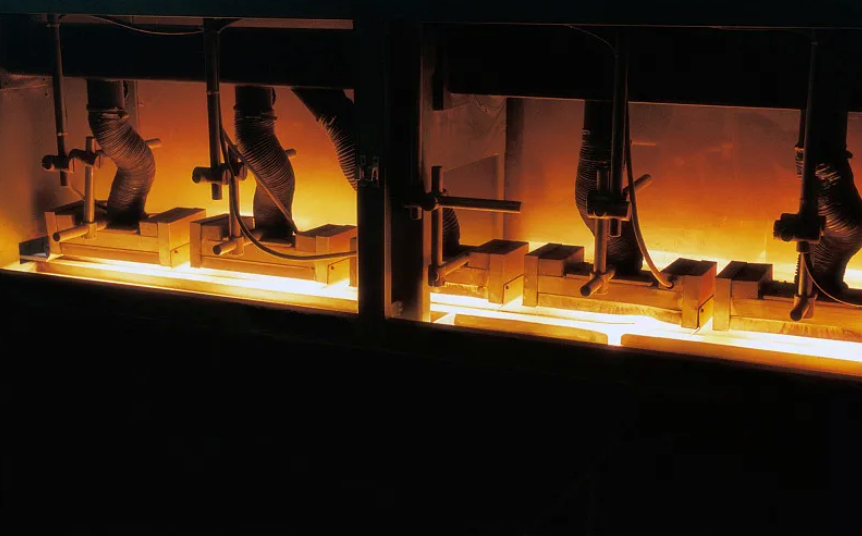
Während Feinguss viele Vorteile bietet, sind auch einige potenzielle Nachteile zu berücksichtigen, darunter:
Höhere Werkzeugkosten für großvolumige Projekte
Feinguss kann bei größeren Produktionsserien teurer sein als andere Gussverfahren, da die Werkzeugkosten höher sein können. Auch die Erstellung von Wachsmodellen und Keramikformen kann zeitaufwändig und arbeitsintensiv sein, was die Kosten erhöhen kann.
Auf einfache Formen beschränkt
Obwohl sich der Feinguss gut für die Herstellung komplexer Teile eignet, ist er im Vergleich zu einigen anderen Gussverfahren auf einfachere Formen beschränkt. Dies liegt daran, dass das Wachsmodell nur bis zu einem gewissen Grad manipuliert werden kann, bevor es zu zerbrechlich und komplex in der Handhabung wird.
Längere Vorlaufzeit
Der Feingussprozess dauert in der Regel länger als andere Gussverfahren, da die Erstellung der Wachsmodelle, der Keramikformen und das Gießen des Metalls Zeit in Anspruch nehmen. Dadurch kann es zu längeren Vorlaufzeiten bei der Teilefertigung kommen.
Porosität
Feinguss kann manchmal zu Teilen mit Porosität führen, bei denen es sich um winzige Hohlräume oder Löcher im Metall handelt. Dies kann das Teil schwächen oder dazu führen, dass es unter Belastung versagt.
Materialbeschränkungen
Feinguss eignet sich möglicherweise nicht für bestimmte Materialien, z. B. solche mit hohem Schmelzpunkt oder solche, die schwer zu gießen sind, was die Auswahl an Materialien, die für Teile verwendet werden können, einschränken kann.
Feinguss ist ein hochpräzises und vielseitiges Verfahren, das jedoch einige Einschränkungen und potenzielle Nachteile aufweist, die im Design- und Produktionsprozess berücksichtigt werden müssen.
Druckguss
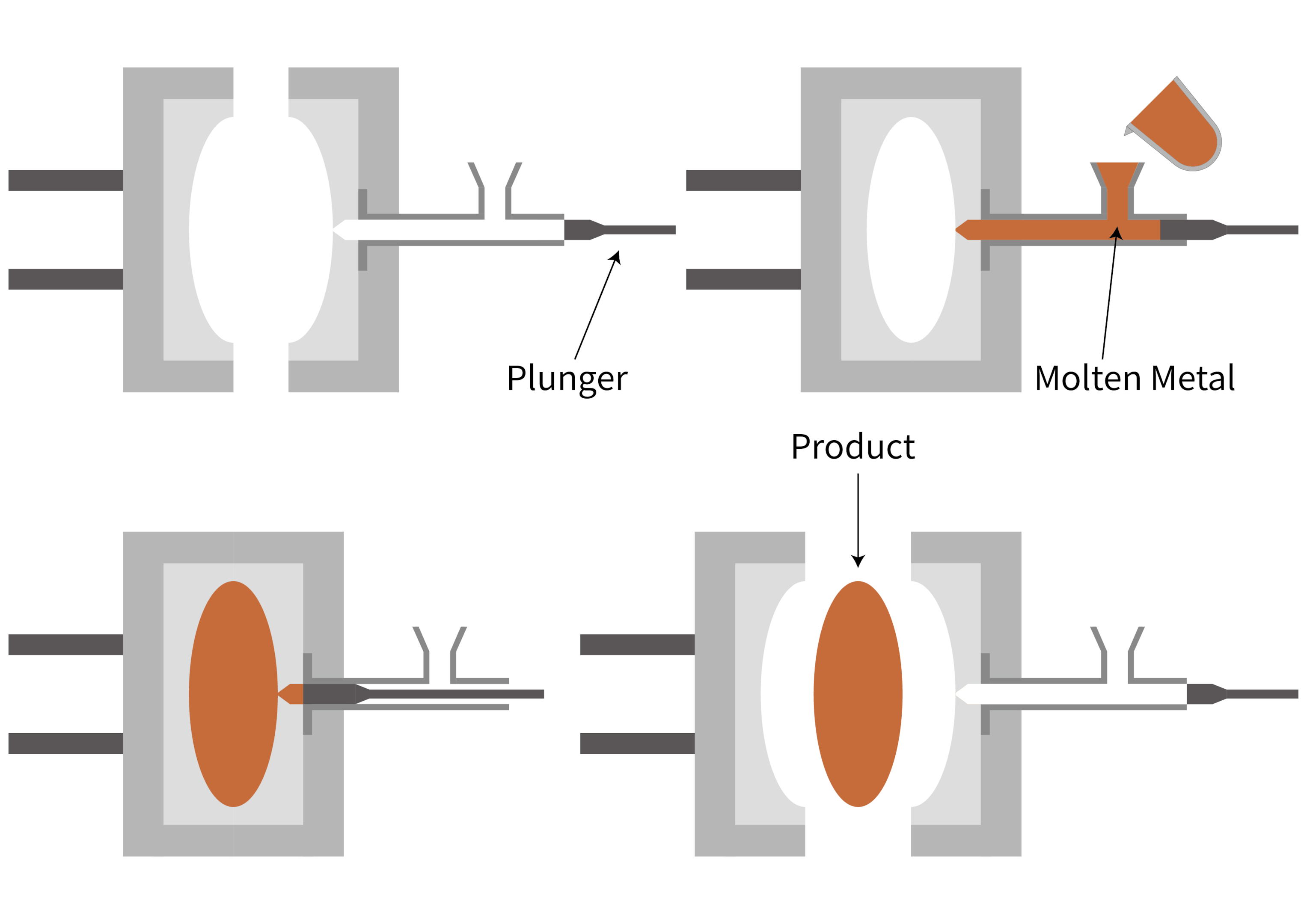
Beim Druckguss wird geschmolzenes Metall mit hohem Druck in einen Formhohlraum gedrückt. Der Gießer erstellt aus gehärtetem Werkzeugstahl eine Matrize in der Form der gewünschten Teile. Auf die Matrize wird ein Trennmittel aufgetragen und ein Zylinder mit geschmolzenem Metall gefüllt, das dann mit einem Kolben in die Hohlräume der Matrize gedrückt wird. Der Kolben hält den Druck auf das Metall aufrecht, während es die Form füllt. Sobald das Metall ausreichend abgekühlt ist, wird das Gussstück aus der Form entfernt und die einzelnen Teile werden abgeschnitten. Schließlich wird jedes Teil nach Bedarf bearbeitet, um es fertigzustellen.
Schritte des Druckgussprozesses
Typischerweise umfasst der Druckguss die folgenden Prozessschritte:
Erstellen des Würfels
Aus gehärtetem Werkzeugstahl wird eine Matrize in der Form der gewünschten Teile hergestellt. Die Matrize kann mehrere Hohlräume zur gleichzeitigen Herstellung mehrerer Teile enthalten.
Auftragen von Trennmittel
Auf die Gussform wird ein Trennmittel aufgetragen, um zu verhindern, dass die Metallschmelze während des Gießvorgangs am Stahl kleben bleibt.
Abfüllen von geschmolzenem Metall
Ein Zylinder wird mit geschmolzenem Metall gefüllt, das dann mit einem Kolben in die Formhohlräume gedrückt wird. Der Kolben übt Druck auf das Metall aus, während es die Matrize füllt.
Druck ausüben
Sobald das geschmolzene Metall den Formhohlraum gefüllt hat, wird Druck auf das Metall ausgeübt, um sicherzustellen, dass es alle komplizierten Details des Formhohlraums ausfüllt und schnell erstarrt.
Entfernen des Produkts
Sobald das Metall abgekühlt und erstarrt ist, wird das Gussprodukt aus der Form entfernt.
Teile beschneiden
Anschließend werden die Einzelteile vom Guss getrennt und überschüssiges Material entfernt.
Konfektionierung
Abhängig von der gewünschten Oberfläche erfordern die Teile möglicherweise zusätzliche Bearbeitung, Polieren oder andere Endbearbeitungsprozesse.
Vorteile des Druckgusses
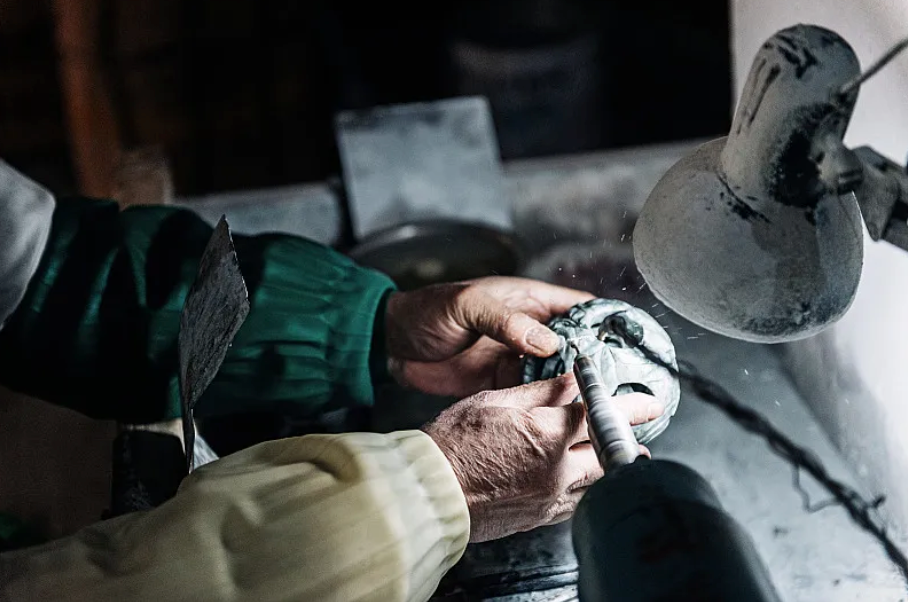
Druckguss hat viele Vorteile, darunter:
Konsistente Wiederholbarkeit
Druckguss bietet eine hohe Maßgenauigkeit und Konsistenz bei der Herstellung identischer Teile in großen Mengen. Dies liegt daran, dass das Verfahren auf der Verwendung von Matrizen aus gehärtetem Stahl beruht, die präzise bearbeitet werden können, um Teile mit engen Toleranzen herzustellen.
Geeignet für große Produktionsläufe
Druckguss eignet sich gut für Großserienproduktionen, da damit schnell und effizient große Mengen an Teilen hergestellt werden können. Dies macht es zu einem idealen Verfahren zur Herstellung von Gussteilen für die Automobil-, Luft- und Raumfahrt- und Konsumgüterindustrie.
Kostengünstig
Druckguss kann eine kostengünstige Option für große Produktionsserien sein, da die hohen anfänglichen Werkzeugkosten durch die Möglichkeit ausgeglichen werden, große Mengen an Teilen zu niedrigen Stückkosten herzustellen.
Nachteile des Druckgusses
Während Druckguss viele Vorteile bietet, bringt er auch einige Nachteile mit sich, darunter:
Höhere Werkzeugkosten
Die anfänglichen Werkzeugkosten für den Druckguss können recht hoch sein, was die Kosteneffizienz bei kleineren Produktionsläufen beeinträchtigen kann. Die Werkzeugkosten sind größtenteils auf die Präzision zurückzuführen, die bei der Bearbeitung der Matrizen erforderlich ist, und auf den harten Stahl, der verwendet wird, um dem unter hohem Druck stehenden Metallfluss standzuhalten.
Auf einfache Formen beschränkt
Druckguss eignet sich im Allgemeinen am besten für einfache Formen mit gleichmäßigen Wandstärken. Komplexe Formen können beim Druckgussprozess eine Herausforderung darstellen, da die hohen Drücke, die beim Prozess auftreten, zu Fehlern im Guss führen können.
Spröde Teile
Im Druckgussverfahren hergestellte Teile können spröder sein als solche, die mit anderen Gussverfahren hergestellt wurden. Dies liegt daran, dass die hohen Drücke, die bei dem Prozess auftreten, zu kleinen Defekten in den Druckgussteilen führen können, die das Teil mit der Zeit schwächen können.
Begrenzte Materialauswahl
Druckguss ist typischerweise auf Nichteisenmetalle wie Aluminium, Magnesium und Zink beschränkt. Dies schränkt die Auswahl an Materialien ein, die im Herstellungsprozess verwendet werden können.
Feinguss vs. Druckguss
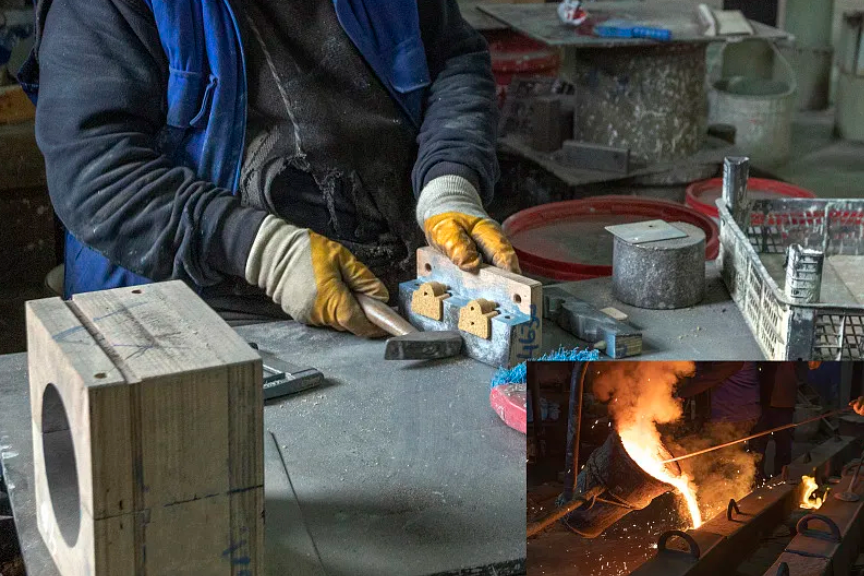
Design
Feinguss ermöglicht eine größere Designflexibilität und ermöglicht das Gießen komplexer Formen mit präzisen Abmessungen, komplizierten Geometrien und dünnwandigen Teilen. Mit Druckguss lassen sich zwar auch präzise dimensionale Ergebnisse erzielen, es lassen sich jedoch keine so komplexen Designs herstellen wie mit Feinguss.
Materialauswahl
Feinguss bietet eine größere Auswahl an Materialoptionen, da sowohl Eisen- als auch Nichteisenlegierungen verwendet werden können. Andererseits wird Druckguss hauptsächlich für Materialien wie Aluminium-, Zink- und Magnesiumlegierungen eingesetzt.
Teilegröße
Beim Feinguss gibt es Größenbeschränkungen, da das Wachsmodell sicher am Gusskanal befestigt und wiederholt in die Keramikaufschlämmung getaucht werden muss. Im Gegensatz dazu unterliegt der Druckguss weniger Größenbeschränkungen und kann größere Komponenten herstellen, verursacht jedoch höhere Werkzeug- und Stückkosten für größere Produkte. Die Größe der Druckgussteile wird durch die Spannkraft begrenzt, die die Gussausrüstung erzeugen kann.
Kosten
Feinguss ist ein arbeitsintensiver Prozess, der zu hervorragenden Abmessungen und einer guten Oberflächenbeschaffenheit führt, was ihn zu einer relativ kostenintensiven Gussmethode macht. Es kann jedoch möglicherweise die Notwendigkeit einer Nachbearbeitung reduzieren oder ganz eliminieren, was sowohl Zeit als auch Geld spart. Druckguss hingegen verursacht höhere Werkzeugkosten und erfordert manchmal Nachbearbeitungsvorgänge für fertige Komponenten, was ihn bei großen Bestellmengen kostengünstiger macht.
Schlussfolgerung
Zusammenfassend lässt sich sagen, dass sowohl Feinguss als auch Druckguss ihre Vor- und Nachteile haben. Feinguss bietet eine größere Designflexibilität und Materialauswahl und eignet sich gut für komplexe Formen und kleinere Produktionsläufe. Druckguss eignet sich besser für größere Produktionsläufe und unterliegt weniger Größenbeschränkungen, ist jedoch auf einfachere Formen und Materialien beschränkt. Die Wahl zwischen Feinguss und Druckguss hängt letztendlich von den spezifischen Anforderungen des Projekts ab, einschließlich Designkomplexität, Materialauswahl, Teilegröße und Kostenüberlegungen.