Kalt- oder Heißkanal: Wahl für effizienteres Spritzgießen
I. Einleitung
Kunststoffspritzguss ist ein Herstellungsverfahren zur Herstellung von Teilen durch Einspritzen von geschmolzenem Kunststoff in eine Form, wo dieser abkühlt und sich in der gewünschten Form verfestigt.
Als Anguss bezeichnet man beim Spritzgießen den Kanal, der den Anguss (wo das geschmolzene Kunststoffmaterial zuerst in die Form eingeführt wird) mit den einzelnen Hohlräumen (wo die endgültige Form des Teils geformt wird) verbindet. Mit anderen Worten: Es handelt sich um den Weg, der den geschmolzenen Kunststoff von der Düse der Einspritzmaschine in die Formhohlräume leitet.
Das Läufersystem ist ein wichtiger Bestandteil von Spritzgießen weil dadurch das Kunststoffmaterial gleichmäßig und gleichmäßig in die Formhohlräume fließen kann. Es gibt zwei Haupttypen von Läufersystemen: Kaltkanäle und Heißkanäle. In diesem Artikel werden die Strukturen dieser beiden Systeme, ihre Funktionsweise sowie ihre Vor- und Nachteile erläutert.
II. Kaltkanalsysteme
Die Kaltkanal-Kunststoffspritzgussform ist in zwei Typen unterteilt: die Zwei-Platten-Form und die Drei-Platten-Form.
Zweiplattenform
Eine Zweiplatten-Spritzgussform ist aufgrund ihres einfachen Aufbaus am gebräuchlichsten. Zur Bildung des Formhohlraums werden 2 Formplatten benötigt. Der Angusskanal in der Zweiplattenform nimmt keine separate Angussplatte ein, sondern ist eher ein Teil des Formhohlraums.
Beim Spritzgießen kühlen und verfestigen sich der Angusskanal, der Anguss und das fertige Produkt gleichzeitig. Beim Öffnen der Form kommen alle gleichzeitig heraus. Das Endprodukt wird dann manuell vom Anguss und vom Anguss getrennt.
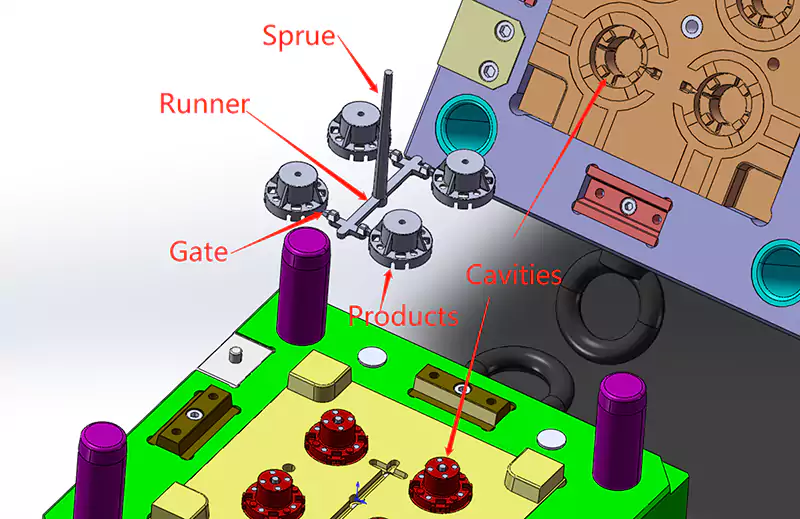
Dreiplattenform
Der Aufbau der Dreiplatten-Spritzgussform ist etwas komplex. Der Läufer ist separat auf einer Kaltläuferplatte verteilt. Obwohl der Angusskanal und der Angusskanal immer noch abkühlen und sich gleichzeitig mit den Endprodukten verfestigen, trennen sich Angusskanal und Angusskanal beim Öffnen der Form automatisch vom Teil.
Viele Produkte erfordern eine einheitliche Geometrie. Derzeit bietet eine Drei-Platten-Form mehr Vorteile als eine Zwei-Platten-Form. Beim Spritzgießen kreisförmiger Produkte lässt sich beispielsweise mit zwei Plattenformen leicht die Form einer Ellipse erzeugen, und mit drei Plattenformen kann Kunststoff an mehreren Punkten eingespritzt werden, sodass die Materialverteilung und Schrumpfung gleichmäßiger sind und die Rundheit des Produkts besser ist.

Vor- und Nachteile von Kaltkanalsystemen:
Zu den Vorteilen von Kaltkanalsystemen gehören geringere Anschaffungskosten und einfachere Wartungsanforderungen. Außerdem ist es toleranter gegenüber hitzeempfindlichen Kunststoffen. Es ist relativ einfach, die Anschnitt- oder Angussgröße zu ändern, um den Kunststofffluss in die Hohlräume auszugleichen. Es ist auch einfacher für schnelle Farbwechsel.
Für ein Kaltkanalsystem sind keine hochqualifizierten und qualifizierten Formenbauer und Formentechniker erforderlich. Und die Einfachheit des Systems ist gegenüber Fertigungsfakultäten toleranter.
Zu den Nachteilen von Kaltkanalsystemen zählen ein erhöhter Materialabfall und eine geringere Energieeffizienz. Kaltkanalsysteme erfordern eine längere Kühlzeit für ein bestimmtes Teil und verlängern daher die Zykluszeit. Kaltkanalsysteme könnten auch zu erhöhten Ausschussraten sowie der Möglichkeit von Graten oder Einfallstellen am fertigen Teil führen. Kaltkanalsysteme werden typischerweise für Teile mit geringerem Produktionsvolumen oder für hitzeempfindliche Materialien eingesetzt.
III. Heißkanalsysteme
Heißkanalsysteme Verwenden Sie beheizte Angusskanäle, um das Material im geschmolzenen Zustand zu halten, bis es in den Formhohlraum eingespritzt wird. nicht wie ein Kaltkanalsystem, dessen Kanal und Teile bei jedem Zyklus gekühlt und ausgeworfen werden. In einem Heißkanalwerkzeug werden in jedem Zyklus nur die Teile aufgerufen und ausgeworfen. Beim Läufer entsteht kein Plastikmüll.
Entsprechend der Methode, mit der das Angusssystem die Wärme des Kunststoffs im Anguss aufrechterhält, werden Heißkanalsysteme in drei Kategorien unterteilt. Es handelt sich um den isolierten Läufer, den innenbeheizten Läufer und den außenbeheizten Läufer.
Der isolierte Heißkanal
Der isolierte Heißkanal erscheint unter den dreien am frühesten und ist auch der einfachste. Dieses grundlegende Heißkanaldesign verwendet einen sehr großen Kanal, um den geschmolzenen Kunststoff im Kanalsystem zu halten. In diesem großen Kanal verfestigte sich zuerst das Kunststoffmaterial in der Nähe der kalten Wände und bildete eine Isolierschicht, die das Material in der Mitte heiß hielt. Der geschmolzene Kunststoff fließt durch die Mitte und liefert genügend Wärme, um den Lauf des Läufers am Laufen zu halten.
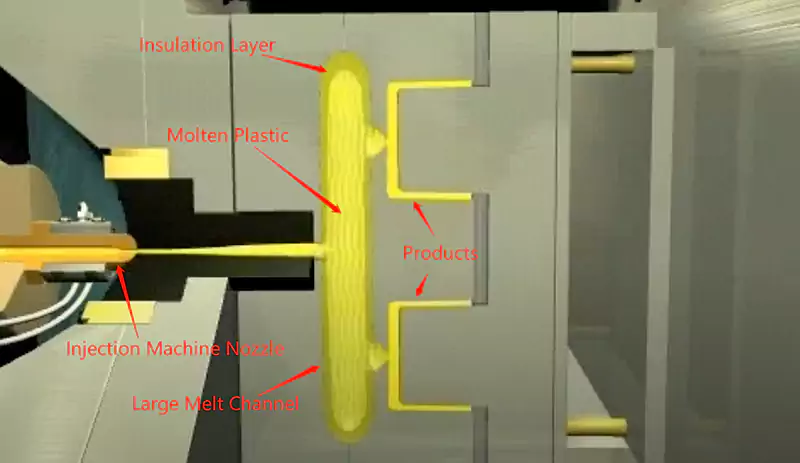
Die isolierten Heißkanal-Short-Comings
Dieses Design ist sehr wirtschaftlich. Es ist für schnelllaufende Formen geeignet. Da das Angusssystem nicht viel Kontrolle bietet, eignet es sich nur für Allzweck-Kunststoffmaterialien. Wenn sich ein isolierter Heißkanal verfestigt, sei es durch einen mechanischen Defekt oder gerade am Ende der Produktion, muss die Angussplatte geöffnet und der verfestigte Angusskanal entfernt werden, bevor die Produktion wieder aufgenommen werden kann.
Der innenbeheizte Läufer
Bei dieser Konstruktion wird eine Heizvorrichtung verwendet, um den Kunststoff im Fließkanal mit Wärme zu versorgen. Bei dem Gerät handelt es sich typischerweise um ein Rohr oder eine Gruppe von Rohren mit Heizkomponenten, die in der Mitte der Strömungskanäle eingesetzt sind und das Kunststoffmaterial von innen nach außen erhitzen. Das Kunststoffmaterial in der Nähe der Kanalwände bildet eine Kaltschicht, die den geschmolzenen Kunststoff von den Metallwänden isoliert. Das System ist immer noch relativ einfach und daher kostengünstiger in der Herstellung und Wartung.
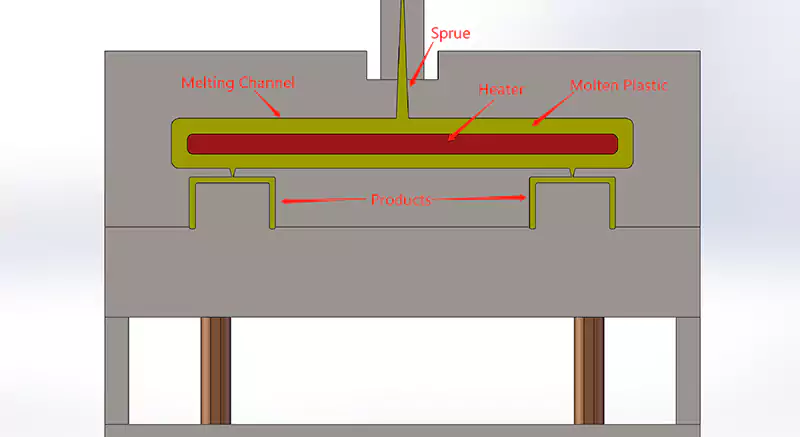
Der innenbeheizte Läufer Short Comings
Das innenbeheizte Läufersystem ist recht groß. Es muss über einen größeren Schmelzekanal verfügen, um das Heizrohr aufzunehmen. Es gibt viele Kreuzungen im System und der Kunststofffluss ist nicht gleichmäßig, was dazu führt, dass der Kunststoff hängen bleibt und sich zersetzt. Das Kunststoffmaterial in der Nähe der Heizung leidet unter einer viel höheren Temperatur als der Kunststoff in der Nähe der kalten Wände. Daher ist dieses Angusssystem nicht für temperaturempfindliche Kunststoffmaterialien geeignet.
Wenn ein Farbwechsel erforderlich ist, muss das gesamte Angusssystem demontiert und der Kunststoff im System gereinigt werden, bevor neuer Farbkunststoff eingespritzt werden kann. Der Prozess könnte zeitaufwändig und kostspielig sein.
Der von außen beheizte Läufer
Trotz seiner Komplexität ist der extern beheizte Läufer das beliebteste der drei Heißkanalsysteme. Ein extern beheizter Läufer besteht typischerweise aus den folgenden Hauptteilen: dem Heißkanalverteiler, den Heißkanaldüsen und der Temperaturregeleinheit.
Ein Heißkanalverteiler führt geschmolzenes Material den verschiedenen Düsen zu, die es in den Formhohlraum einspritzen. Externe Heizgeräte werden im oder am Verteiler und an den Düsen montiert. Die Wärmeübertragung vom Verteilermetall zum Kunststoff führt zu einer gleichmäßigeren Temperaturverteilung im Kunststoffmaterial.
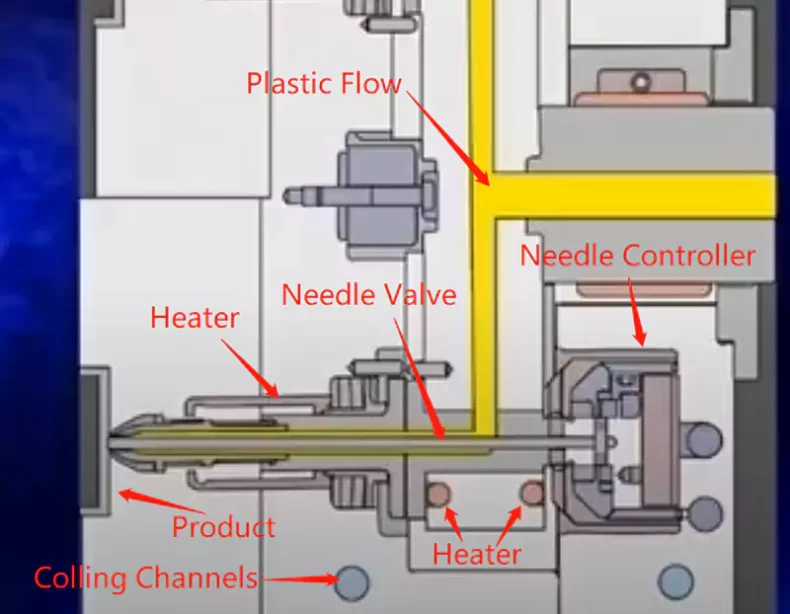
Besserer Formfluss
Bei dieser Art der Erwärmung sind die Schmelzekanäle in der Regel klein und rund und der Materialfluss ist ungehindert. Bei diesem System gibt es keine Hindernisse in den Schmelzekanälen. Diese Methode bietet dem Kunststofffluss den geringsten Widerstand und damit den geringsten Druckabfall. Dies ermöglicht möglicherweise eine kleinere Spritzgießmaschine in der Produktion. Aufgrund der ungehinderten Kanäle kommt es außerdem zu weniger Materialansammlungen und damit zu einer geringeren Gefahr einer Materialverschlechterung. Im Vergleich zum internen Heizsystem bietet dieses System einen viel schnelleren Farb- oder Materialwechsel.
Längere Lebensdauer der Heizung
Die Temperaturkontrolleinheit wird verwendet, um das geschmolzene Material auf einer geringen Temperaturschwankung zu halten und sicherzustellen, dass das Material geschmolzen bleibt, bevor es in die Form eingespritzt wird. Die Temperaturregeleinheit ermöglicht eine sehr präzise Regelung der Temperatur des Heizgeräts. Die Heizung in einem externen Heizsystem arbeitet in einer viel besseren Umgebung als die Heizungen in einem internen Heizsystem und hat daher eine längere Lebensdauer.
Bessere Kontrolle des Injektionsprozesses
Der Nadelverschluss, der den Materialfluss in den Formhohlraum steuert, ist eine weitere wichtige Komponente des Heißkanalsystems. Der Nadelverschluss ermöglicht es, das Kunststoffverteilersystem jederzeit mit dem Formhohlraum zu verbinden und zu trennen. Dies führt zu einer wesentlich besseren Flusskontrolle im Kunststoffspritzprozess.
Heißkanalsystemen können zusätzliche Funktionen wie Kühlkanäle und Drucksensoren hinzugefügt werden, um die Präzision und Kontrolle des Spritzgießprozesses zu erhöhen.
Im Vergleich zum Kaltkanalsystem und den anderen beiden eher einfachen Heißkanalsystemen bietet das extern beheizte Kanalsystem mehr Flexibilität und Kontrolle beim Spritzgießen. Beispielsweise können Tore zu unterschiedlichen Zeiten geöffnet und geschlossen werden, um Produktfehler wie Schlagspuren, Verbindungsspuren usw. zu beseitigen.
Diese Flexibilität ist unerlässlich, um die qualitativ hochwertige Einspritzung großer Endteile sicherzustellen. Da es keinen erstarrten Anguss oder Angusskanal gibt, wird Material gespart und die Zykluszeit verkürzt.

Kurze Ankünfte
Heißkanalsysteme erfordern aufgrund ihrer komplizierten Konstruktion eine häufige Wartung und Reinigung, was maximale Leistung und Systemlebensdauer garantiert. Dies ist aufgrund ihrer Komplexität besonders wichtig für externe Heizkanalsysteme.
Die Komplexität der externen Heizkanalsysteme bedeutet auch eine längere Formherstellungszeit, höhere Formkosten und erfordert mehr erfahrene Techniker für den Zusammenbau der Form, den Betrieb des Einspritzprozesses und die Wartung der Form.
Vor- und Nachteile von Heißkanalsystemen
Zu den Vorteilen von Heißkanalsystemen gehören Energieeffizienz und reduzierter Materialabfall. Heißkanalsysteme können außerdem zu schnelleren Zykluszeiten und einer verbesserten Teilequalität sowie geringeren Ausschussraten führen.
Zu den Nachteilen eines Heißkanalsystems zählen die höheren Anschaffungskosten und der höhere Wartungsaufwand. (Eine Heißkanalform könnte fünfmal so viel wie eine Kaltkanalform oder mehr kosten.)
Heißkanalsysteme werden typischerweise für Teile mit sehr hohen Produktionsmengen und für Materialien verwendet, die hohen Temperaturen über einen längeren Zeitraum standhalten können. Denn im Heißkanalsystem bleibt der Kunststoff länger im geschmolzenen Zustand.
IV. Zu berücksichtigende Faktoren bei der Wahl zwischen Kaltkanal- und Heißkanalsystemen
Überlegungen zu Produktionsvolumen und Kosten:
Die einmalige Investition in das Heißkanalsystem ist relativ hoch, die Produktionseffizienz ist jedoch hoch und die Produktionskosten pro Zyklus sind niedrig, da die Zeit zum Abkühlen des Kanals eingespart wird. Darüber hinaus werden auch die Kosten für das Nachschleifen und Recyceln des Angusskanals eingespart.
Im Gegenteil, die Einspritzzykluskosten des Kaltkanalsystems sind höher, und die Anfangsinvestition zur Erzielung der besten Stückkosten ist umso höher, je höher die erwartete Gesamtleistung des Produkts ist, desto mehr sollte das Heißkanalsystem in Betracht gezogen werden und desto niedriger ist die Gesamtsumme Je höher die Leistung, desto stärker sollte das Kaltkanalsystem gewichtet werden. Typische Anwendungen von Heißkanalsystemen sind hauptsächlich großvolumige zivile Produkte wie Flaschenverschlüsse.
Materialart und Eigenschaften:
Obwohl das Heißkanalsystem erfolgreich auf gängige Kunststoffe wie PA, PP, PET, POM, ABS usw. angewendet wurde, muss bei der Überlegung über den Einsatz immer noch die Verweilzeit der Kunststoffe im System berücksichtigt werden. Wenn die Zeit zu lang ist, werden einige hitzeempfindliche Kunststoffe zersetzt, es kommt zu Verfärbungen und sogar zu einer Veränderung der Materialeigenschaften.
Komplexität und Größe des zu formenden Teils:
Das Heißkanalsystem ermöglicht eine bessere Kontrolle über die Qualität des Endprodukts. Produkte mit großen Abmessungen können beim Einspritzen eher zu Qualitätsproblemen führen, und auch die Verluste durch Abfallprodukte sind größer. Daher ist das Heißkanalsystem bei großen oder hochkomplexen Produkten meist die bessere Wahl.
V. Schlussfolgerung
Kaltkanal- und Heißkanalsysteme sind die beiden Haupttypen von Spritzgusskanalsystemen, die jeweils ihre Vor- und Nachteile haben.
Heißkanalsysteme bieten eine kürzere Zykluszeit, niedrigere Zykluskosten sowie niedrigere Materialkosten und eine geringere Ausschussrate für das Endprodukt. Die Nachteile sind höhere Anschaffungs- und Wartungskosten.
Kaltkanalsysteme sind im Allgemeinen für geringere Produktionsmengen und hitzeempfindliche Materialien kostengünstiger, während Heißkanalsysteme für größere Produktionsmengen und Materialien, die hohen Temperaturen über einen längeren Zeitraum standhalten können, möglicherweise kostengünstiger sind.
Bei der Entscheidung, welcher Systemtyp verwendet werden soll, sollten das Produktionsvolumen und die Kostenüberlegungen, die Materialart und -eigenschaften sowie die Komplexität und Größe des zu formenden Teils berücksichtigt werden.
Am Ende ist es wichtig, gemeinsam mit einem Spezialisten herauszufinden, welches System für Ihre spezifischen Bedürfnisse und Anforderungen am besten geeignet ist. Wenn Sie Fragen zum Spritzgießen oder Formenbau für Ihre Projekte haben, senden Sie Capable Machining eine E-Mail und wir beantworten diese gerne.
Häufig gestellte Fragen:
- Kann ein Heißkanalsystem für die Kleinserienproduktion eingesetzt werden?
- Ja, ein Heißkanalsystem kann für die Produktion kleiner Stückzahlen verwendet werden, aber in den meisten Fällen geringer Stückzahlen ist es möglicherweise nicht die kostengünstigste Lösung, es sei denn, das Ziel besteht darin, eine gute Qualität für die Einspritzung großer Produkte zu erzielen.
- Kann ein Kaltkanalsystem für die Massenproduktion eingesetzt werden?
- Ja, ein Kaltkanalsystem kann für die Massenproduktion verwendet werden. Es wird häufig für Mengen von Hunderttausenden Stück verwendet. Die Wahl zwischen einem Heiß- oder Kaltkanalsystem ergibt sich aus der Abwägung von Material- und Zykluszeitverlusten gegenüber hohen Formkosten und hohen Wartungskosten.