Herkömmliche Metallverarbeitungsprozesse sind äußerst energieintensiv und erzeugen erhebliche Abfälle, da bei der Herstellung bis zu 90 % des Metalls weggeschnitten werden. Dies verbraucht nicht nur übermäßig viel Energie, sondern erhöht auch unnötig das Gewicht des Endprodukts, was in Branchen wie der Luftfahrt einen kostspieligen Nachteil darstellt. Der Metall-3D-Druck zeigt uns verschiedene Möglichkeiten, dies zu tun.
Im Gegensatz, 3D Druck Minimiert den Abfall, indem nur genau die Menge an Material verwendet wird, die benötigt wird, sodass praktisch kein Abfall entsteht. Die Einschränkungen des reinen Kunststoffdrucks wurden überwunden, da Unternehmen weltweit 3D-Drucker entwickeln, die in der Lage sind, mit Metallmaterialien zu drucken. Dieser Durchbruch eröffnet neue Möglichkeiten für die direkte Herstellung komplexer Metallobjekte mithilfe der 3D-Drucktechnologie.
Was ist Metall-3D-Druck?
Der Metall-3D-Druck, auch bekannt als additive Metallfertigung, ist eine hochmoderne Fertigungstechnologie, die die Herstellung dreidimensionaler Metallobjekte ermöglicht. Es nutzt additive Verfahren, um Metallteile Schicht für Schicht aufzubauen, im Gegensatz zu herkömmlichen subtraktiven Methoden, die Schneiden, Bearbeiten oder Gießen umfassen. (Siehe bitte diesen Beitrag: 3D-Druck vs. CNC-Bearbeitung)
Beim Metall-3D-Druck werden spezielle 3D-Drucker eingesetzt, die mit Lasern oder Elektronenstrahlen ausgestattet sind, um Metallpulver selektiv zu schmelzen oder zu sintern und sie zu komplexen Formen und Strukturen zu verschmelzen. Diese Technologie ermöglicht die Herstellung hochkomplexer und kundenspezifischer Metallkomponenten, deren Herstellung mit herkömmlichen Fertigungsmethoden möglicherweise schwierig oder gar nicht möglich ist.
Der Metall-3D-Druck eröffnet spannende Möglichkeiten und Anwendungen, insbesondere in der Transportbranche. Es ermöglicht die Umsetzung von Leichtbau- und Designtechniken, die bei verschiedenen Zielen eine entscheidende Rolle spielen. Zu diesen Zielen gehören die Reduzierung des Gesamtgewichts des Fahrzeugs, die Optimierung der Energieeffizienz im Betrieb, die Senkung der Herstellungskosten und die Verbesserung der Gesamtleistung. Diese Technologie eröffnet neue Wege für Innovation und Fortschritt im Transportsektor.
Metall-3D-Druckverfahren
Der Metall-3D-Druckprozess, auch bekannt als additive Metallfertigung, umfasst mehrere wichtige Schritte:
Entwerfen des Objekts
Der Prozess beginnt mit der Erstellung eines digitalen Entwurfs des gewünschten Objekts mithilfe einer CAD-Software (Computer Aided Design). Das Design kann an die spezifischen Anforderungen und Möglichkeiten des Metall-3D-Drucks angepasst und optimiert werden.
Vorbereiten der CAD-Datei
Anschließend wird der CAD-Entwurf in ein mit dem Metall-3D-Drucker kompatibles Format umgewandelt. Dies kann das Zerlegen des 3D-Modells in dünne Querschnittsschichten, die Bestimmung der geeigneten Stützstrukturen und die Festlegung von Druckparametern umfassen.
Materialauswahl
Die Wahl des Metallpulvermaterials ist beim Metall-3D-Druck von entscheidender Bedeutung. Abhängig von der spezifischen Anwendung und den gewünschten Eigenschaften des gedruckten Objekts können verschiedene Metalle wie Titan, Aluminium, Edelstahl und Nickellegierungen verwendet werden.
Vorbereiten des Druckers
Der Metall-3D-Drucker wird entsprechend den Spezifikationen des verwendeten Metallmaterials eingerichtet und kalibriert. Dazu gehört die Sicherstellung der richtigen Temperatur, Gasatmosphäre und anderer Prozessparameter, die für einen erfolgreichen Druck erforderlich sind.
Drucken des Objekts
Der Metall-3D-Drucker startet den additiven Fertigungsprozess, indem er eine dünne Schicht Metallpulver auf die Bauplattform aufträgt. Anschließend wird die Pulverschicht anhand der in der CAD-Datei bereitgestellten Anweisungen mithilfe einer Hochenergiequelle, beispielsweise einem Laser oder einem Elektronenstrahl, selektiv geschmolzen oder gesintert. Dieser Vorgang wird Schicht für Schicht wiederholt, bis das vollständige Objekt entsteht.
Nachbearbeitung
Nach dem Drucken kann das Metallobjekt verschiedenen Nachbearbeitungsschritten unterzogen werden, um seine mechanischen Eigenschaften, die Oberflächenbeschaffenheit und die Maßhaltigkeit zu verbessern. Dies kann das Entfernen von Stützstrukturen, Wärmebehandlung, maschinelle Bearbeitung, Polieren oder das Aufbringen zusätzlicher Beschichtungen oder Veredelungen umfassen.
Wie funktioniert es?
Im Gegensatz zu herkömmlichen Druckern, die Kunststoff schmelzen und auftragen, erfordert der Metalldruck aufgrund der sehr hohen Verarbeitungstemperatur und des Schmelzpunkts von Metallen andere Vorgehensweisen. Im Bereich des Metalldrucks haben sich drei weit verbreitete Techniken herausgebildet. Eine dieser Techniken ist das so genannte Binder Jetting, das im Vergleich zu anderen Metalldruckverfahren erhebliche Materialeffizienzvorteile bietet und diese um mehr als das Zehnfache übertrifft.
Binderdüsen
Der Prozess des Binder Jetting ähnelt stark dem MIM-Prozess. Bindematerialien werden verwendet, um das Metallpulver zu binden, damit das Metallpulver die entworfene Form annehmen kann.
Beim Binder-Jetting-Druckverfahren sind folgende Schritte erforderlich:
Kammervorbereitung
Die Baukammer ist mit Inertgas wie Argon gefüllt, um eine Oxidation des Metalls während des Druckens zu verhindern.
Metallpulverabscheidung
Eine dünne Schicht Metallpulver, typischerweise 20 bis 50 Mikrometer dick, wird gleichmäßig in der Baukammer verteilt. Die Schichtdicke hängt von Faktoren wie den Fließeigenschaften, der Partikelgröße und der Form der Metallpartikel ab.
Anwendung von Polymerbindemitteln
Eine Polymerverbindung, die als Bindemittel fungiert, wird entsprechend der 3D-Kontur des zu druckenden Bauteils auf bestimmte Bereiche der Metallpulverschicht aufgesprüht. Dieses Bindemittel hilft dabei, die Metallpartikel miteinander zu verbinden. Damit nur die Metallpulver im 3D-Umriss gebunden werden, werden im folgenden Schritt die Metallpulver entfernt, die nicht im 3D-Umriss enthalten sind.
Schichtweiser Aufbau
Der Vorgang wird wiederholt, wobei weitere Schichten aus Metallpulver und Bindemittel übereinander aufgetragen werden, wodurch das Objekt nach und nach entsteht. Jede Schicht entspricht einem Querschnitt des 3D-Modells.
Sammlung und Wiederverwendung von überschüssigem Pulver
Nach dem Drucken wird das überschüssige Metallpulver gesammelt, gefiltert und mit nicht verwendeten Metallpulverpartikeln aufgefrischt. Dieses recycelte Pulver kann in nachfolgenden Drucken wiederverwendet werden, wodurch Materialverschwendung reduziert wird.
Komponententrennung und Nachbearbeitung
Das gedruckte Bauteil wird mithilfe verschiedener Techniken, beispielsweise mechanisch oder chemisch, von der Baukammer getrennt. Bei Bedarf können Nachbearbeitungsschritte wie das Entfernen von Stützstrukturen oder das Anbringen von Nachbehandlungen durchgeführt werden.
Genauigkeit
Das gedruckte Bauteil erreicht in der Regel ein hohes Maß an Genauigkeit, typischerweise innerhalb von ±0.1 mm, abhängig von den spezifischen Druckerfunktionen und der Komplexität des Designs.
Nach Abschluss des Bauprozesses und der Trennung der Fertigungsmetallteile von der Bauplatte gilt es als „grünes“ 3D-gedrucktes Metallobjekt. Dieses grüne Objekt weist jedoch eine geringe mechanische Festigkeit und eine hohe Porosität auf. Um diese Einschränkungen zu beseitigen, werden zwei gängige Ansätze verwendet:
Sintern
Das grüne Objekt wird in einen Ofen gelegt, der mit herkömmlichen Heizelementen und Mikrowellentechnologie ausgestattet ist. Die Temperatur wird auf ein Niveau knapp unter dem Schmelzpunkt des Metalls (jedoch deutlich über dem Schmelzpunkt des Polymerbinders) erhöht. Bei steigender Temperatur entzündet sich der Polymerbinder und verbrennt. Die starke Hitze erleichtert einen Prozess namens „Sintern“, bei dem die Metallpartikel miteinander verbunden werden und die mikroskopisch kleinen Löcher und Hohlräume füllen. Dieser Sinterprozess führt zu einer Porenfüllung von ca. 97 %, wodurch die mechanischen Eigenschaften des Objekts verbessert werden.
Infiltration
Bei dieser Methode wird das grüne Objekt einem Ofen ausgesetzt, um das verbleibende Polymerbindemittel zu entfernen, wodurch etwa 60 % Hohlräume in der Struktur zurückbleiben. Um die Porosität weiter zu verstärken und zu reduzieren, wird das Objekt anschließend mit einem Bronzematerial infiltriert. Die Bronze füllt die durch die Entfernung des Polymerbindemittels entstandenen Hohlräume, was zu einer erhöhten Festigkeit und einer deutlichen Reduzierung (ca. 90 %) des Porenvolumens führt.
Schrumpfung ist ein Problem beim 3D-Metalldruck mit Binder Jetting, insbesondere während der Sinter- oder Infiltrationsphase im Ofen. Hohe Temperaturen können aufgrund der Metallerweichung zu Maßungenauigkeiten, Verwerfungen oder Verformungen führen. Geschickter Maschinenbetrieb und sorgfältige Überlegungen in der ersten Entwurfsphase werden eingesetzt, um potenzielle Schrumpfungen auszugleichen und die gewünschte Maßhaltigkeit und Form des Endprodukts sicherzustellen.
Selektives Laserschmelzen
Es handelt sich um eine weitere bekannte Technik im Metall-3D-Druck, die sich vom Binder Jetting unterscheidet. Selektiver Laser bedeutet hier, dass der Laser ausgewählte Pfade und Positionen durchläuft.
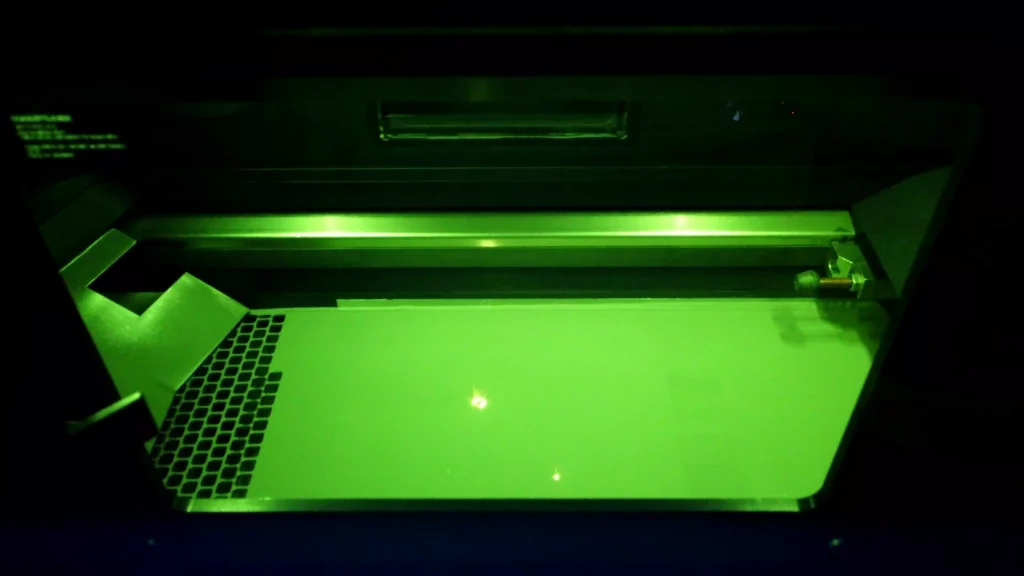
Hier ein Überblick über den SLM-Prozess:
Kammervorbereitung
Die Baukammer ist mit einem Inertgas gefüllt, um eine sauerstofffreie Umgebung zu schaffen, die eine Oxidation des Metalls während des Druckvorgangs verhindert.
Metallpulverabscheidung
Eine dünne Schicht Metallpulver wird gleichmäßig auf der Bauplattform verteilt.
Laserfusion
Ein Hochleistungslaser scannt das Metallpulver im Querschnittsbereich des Objekts und schmilzt es selektiv, wodurch die Partikel miteinander verschmolzen werden und eine feste Schicht des Objekts entsteht. Basierend auf dem digitalen Design wird der Laser präzise gesteuert.
Schichtweiser Aufbau
Nach Fertigstellung einer Schicht bewegt sich die Bauplattform um eine bestimmte Strecke nach unten, typischerweise im Bereich von 50 bis 200 Mikrometern. Anschließend trägt ein Nachbeschichter eine neue Schicht Metallpulver auf die vorherige Schicht auf.
Laserscanning und Fusion
Der Laser scannt und schmilzt das Metallpulver in der neu aufgetragenen Schicht und verschmilzt es mit der darunter liegenden Schicht.
Wiederholen und aufbauen
Der Vorgang wird Schicht für Schicht wiederholt, wobei die Bauplattform abgesenkt wird und eine neue Pulverschicht verteilt und selektiv geschmolzen wird, bis das gesamte Objekt aufgebaut ist.
Sammlung und Wiederverwendung überschüssigen Pulvers
Nach dem Drucken wird das überschüssige Metallpulver gesammelt, gefiltert und mit frischem Pulver gemischt, um es in nachfolgenden Drucken wiederzuverwenden. Dieser Recyclingprozess trägt dazu bei, Materialverschwendung zu minimieren.
Selektives Laserschmelzen ermöglicht die Herstellung komplexer Geometrien und hochauflösender Teile mit hervorragenden mechanischen Eigenschaften. Es wird häufig in Branchen wie der Luft- und Raumfahrt, der Medizintechnik und der Automobilindustrie zur Herstellung funktionaler Metallkomponenten mit präzisen Abmessungen und feinen Details eingesetzt.
Beim selektiven Laserschmelzen (SLM) sind keine separaten Heiz- und Sinterprozesse erforderlich, da das Metallpulver direkt zum Objekt geschmolzen wird. Diese einzigartige Eigenschaft führt zu einem Endprodukt mit deutlich höherer mechanischer Festigkeit. Daher ist SLM das bevorzugte Verfahren zur Herstellung von Komponenten, die außergewöhnliche mechanische Eigenschaften wie Metallermüdungsbeständigkeit, Bruchdehnung und Elastizitätsmodul erfordern.
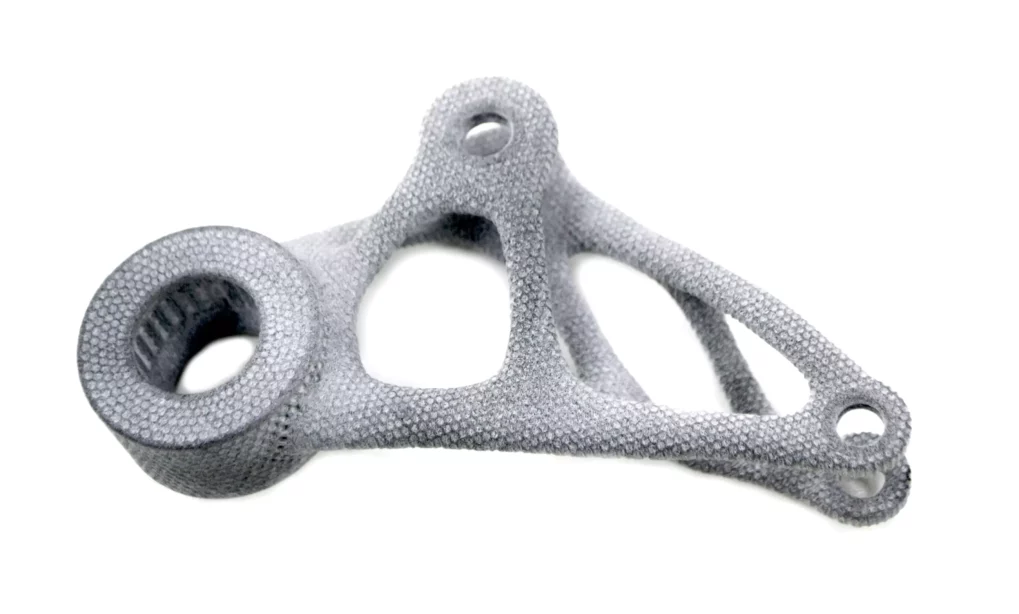
Sowohl bei der Binder-Jetting- als auch bei der SLM-Technik steht die Materialeffizienz im Vordergrund. Das in diesen Prozessen verwendete Metallpulver wird gesammelt, gefiltert und zur Wiederverwendung mit frischem Pulver vermischt. Dieser Recyclingansatz stellt sicher, dass der erzeugte Abfall auf weniger als 5 % minimiert wird, was zu einem nachhaltigeren und kostengünstigeren Herstellungsprozess beiträgt.
Additive Fertigung mit Drahtlichtbogen
Wire Arc Additive Manufacturing (WAAM) ist eine Fertigungstechnik zur Herstellung oder Reparatur von Metallkomponenten. Es fällt in die Kategorie der Direct Energy Deposition (DED)-Prozesse im Bereich der additiven Fertigung. WAAM beinhaltet die sequentielle Abscheidung von Metallschichten, um nach und nach eine gewünschte dreidimensionale Form zu bilden.
Dieses Verfahren kombiniert zwei Fertigungsverfahren: das Gas-Metalllichtbogenschweißen (GMAW) und die additive Fertigung. GMAW ist eine Lichtbogenschweißtechnik, die zum Verschmelzen von Metallteilen verwendet wird, während sich die additive Fertigung auf den Industriebegriff für 3D-Druck bezieht. Bei WAAM erfolgt die Teilefertigung durch die Integration eines Schweißroboters in eine Stromquelle. Der Roboter verwendet einen Schweißbrenner, um das Drahtmaterial zu schmelzen und anschließend die 3D-Komponenten zu bauen.
Bei WAAM wird der Metalldraht durch eine Düse oder einen Schweißbrenner geführt und die Lichtbogenwärme schmilzt den Draht, der dann auf einem Substrat oder zuvor aufgetragenen Schichten abgeschieden wird. Der Prozess wird Schicht für Schicht fortgesetzt, bis das gewünschte Objekt entsteht. Die abgeschiedenen Schichten verfestigen sich und verbinden sich miteinander, wodurch ein Metallteil entsteht. Offensichtlich hätten die aus WAAM gefertigten Teile eine eher raue Oberfläche. Um eine bessere Oberfläche zu erhalten, sind Nachbearbeitungen wie Schleifen oder Polieren erforderlich.
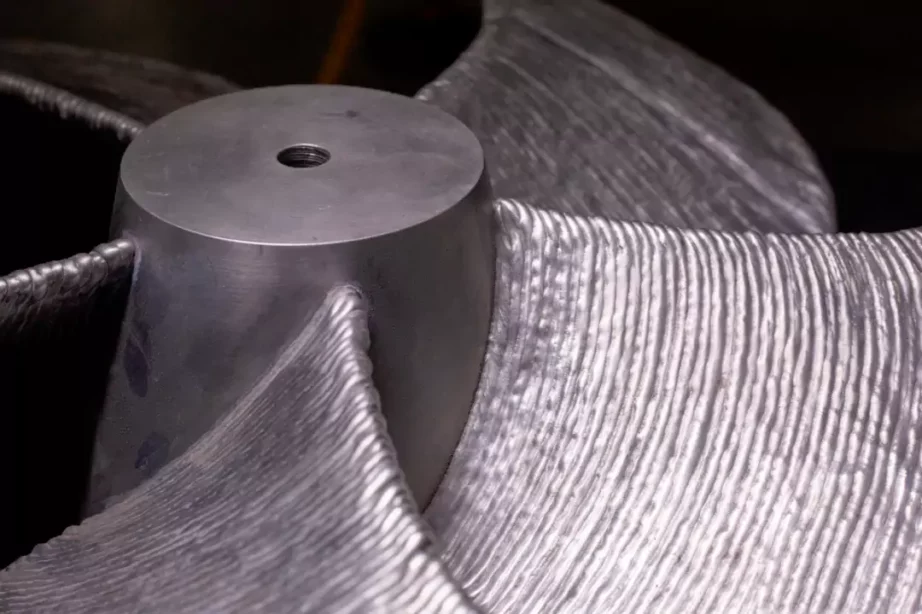
WAAM bietet mehrere Vorteile, darunter schnellere Bauraten im Vergleich zu einigen anderen Metall-3D-Drucktechniken, geringere Materialkosten aufgrund der Verwendung von Draht anstelle von Pulver und die Möglichkeit, mit einer breiten Palette von Metalllegierungen zu arbeiten. Es wird häufig zur Herstellung großformatiger Metallkomponenten wie Flugzeugflügel, Schiffspropeller oder Teile von Flugzeugtriebwerken verwendet. Das Verfahren findet Anwendung in Branchen wie der Luft- und Raumfahrt, der Automobilindustrie und der Schifffahrt. Es ist sehr nützlich, Prototypen großer Teile herzustellen. Der alternative Herstellungsprozess würde teure Großgeräte erfordern und viel teures Material verschwenden.
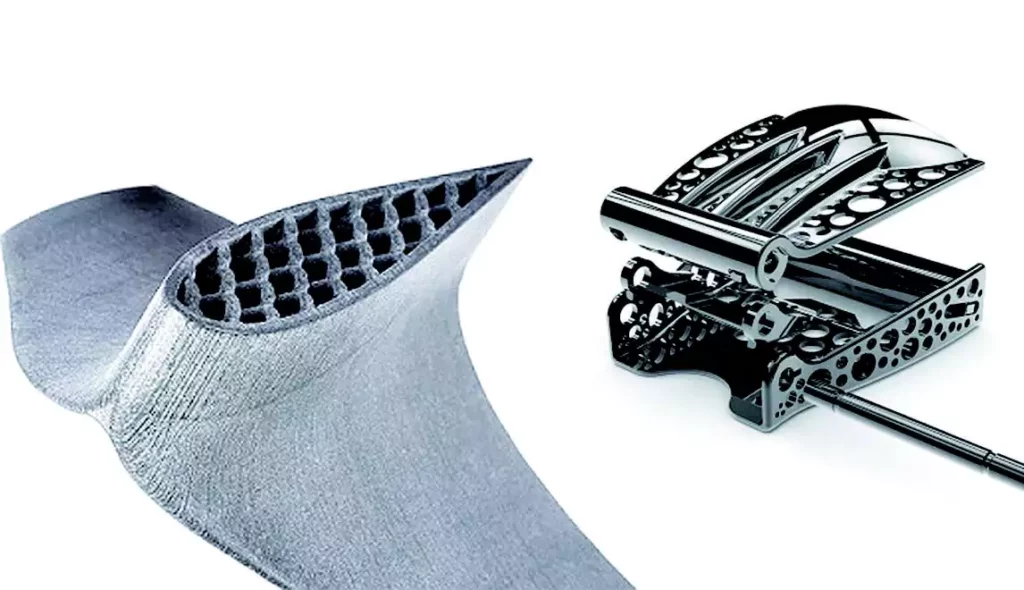
Schlussfolgerung
Zusammenfassend lässt sich sagen, dass der Metall-3D-Druck die Herstellung von Metallkomponenten revolutioniert hat. Es bietet zahlreiche Vorteile gegenüber herkömmlichen Herstellungsmethoden, darunter eine größere Designfreiheit, weniger Materialverschwendung und die Möglichkeit, komplexe Geometrien zu erstellen. Der Metall-3D-Druck ermöglicht die Herstellung von Leichtbaustrukturen, kundenspezifischen Teilen und verbesserter Leistung in verschiedenen Branchen wie Luft- und Raumfahrt, Automobil, Gesundheitswesen und mehr.
Da der Metall-3D-Druck dank kontinuierlicher Forschung und Entwicklung immer weiter voranschreitet, birgt er das Potenzial, Industrien zu verändern, indem er die Produktion hochgradig individueller, leichter und effizienter Metallteile ermöglicht. Mit seiner Fähigkeit, Abfall zu reduzieren, die Leistung zu verbessern und die Designmöglichkeiten zu erweitern, ist der 3D-Metalldruck bereit, die Zukunft der Fertigung neu zu gestalten.