Urethanharz ist ein vielseitiges Material, das zur Herstellung verschiedener Kunststoffgegenstände verwendet wird. Seine Einsatzmöglichkeiten sind vielfältig, denn es lassen sich sowohl biegsame, fast gummiartige Produkte als auch starre Kunststoffe herstellen.
Was ist Urethanguss?
Urethanguss (oder Polyurethanguss oder Vakuumguss) ist eine Technik, die bei der Herstellung von Kleinserienprodukten mit geringem Volumen, wie z. B. maßgefertigten Modellen oder Filmrequisiten, eingesetzt wird. Bei diesem Vorgang wird das Urethan in eine Form gegossen und aushärten gelassen. Auf die Einzelheiten gehen wir später näher ein.
Urethanguss ist eine hervorragende und kostengünstige Möglichkeit, sowohl Teile als auch ganze Modelle in hoher Qualität herzustellen. Es ist besonders nützlich für komplizierte Designs, da es schnell und zu geringeren Kosten als andere Methoden eine polierte Oberfläche erzeugt.
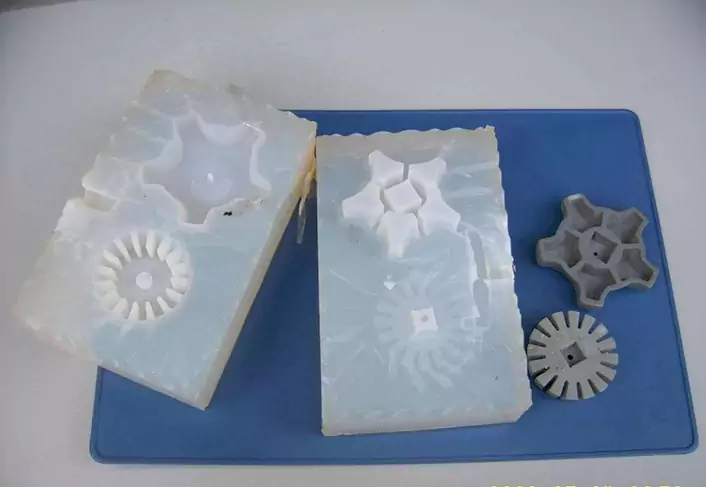
Kurze Geschichte und Entwicklung
Das Urethan-Gießverfahren entstand Mitte des 20. Jahrhunderts, als erstmals Polyurethan, ein synthetisches Polymer, entwickelt wurde. Das Material erfreute sich aufgrund seiner Haltbarkeit, Flexibilität und Vielseitigkeit schnell großer Beliebtheit, und die Hersteller begannen, mit Möglichkeiten zu experimentieren, es für die Herstellung einer Vielzahl von Produkten zu verwenden.
In den Anfängen des Urethangusses wurde das Verfahren hauptsächlich zur Herstellung von Formen für die Herstellung von Polyurethanschaumprodukten wie Autositzen und Matratzen eingesetzt. Mit der Weiterentwicklung der Technologie, die dem Verfahren zugrunde liegt, wurde es jedoch möglich, Urethanguss auch zur Herstellung von massiven Kunststoffteilen zu verwenden.
Heutzutage wird das Urethangussverfahren häufig in Branchen wie der Luft- und Raumfahrt, der Automobilindustrie und der Medizintechnik eingesetzt, in denen qualitativ hochwertige Teile in kleinen Stückzahlen benötigt werden. Der Prozess ist im Laufe der Zeit immer ausgefeilter geworden, da Fortschritte bei Materialien, Ausrüstung und Software eine höhere Präzision und Effizienz bei der Herstellung von Teilen ermöglichen.
Urethan-Gießverfahren
Urethanguss ist ein Herstellungsverfahren, bei dem flüssiges Polyurethan in eine Form gegossen wird, um ein festes Kunststoffteil zu erzeugen. Das Verfahren wird häufig zur Herstellung von Prototypen, Kleinserien und Ersatzteilen für bestehende Produkte eingesetzt.
Hier sind die grundlegenden Schritte des Urethan-Gießprozesses:
Erstellen Sie ein Meisterwerk
Abhängig von der Art des Designs kann das Meisterwerk durch CNC-Bearbeitung, 3D-Druck oder andere Bearbeitungsverfahren erstellt werden. Das Meisterwerk wird in späteren Verfahren zur Herstellung von Formen verwendet.
Erstellen Sie eine Form
Die Form des Urethangusses kann aus Metall, Silikon oder sogar Holz bestehen, in der Rapid-Prototyping-Industrie wird sie jedoch am häufigsten aus Silikon hergestellt. Das flüssige Silikon wird in eine Schachtel gegossen und das Meisterwerk in die Schachtel gelegt. Das Silikon wird dann ausgehärtet und vom flüssigen in den festen Zustand umgewandelt. Anschließend wird das feste Silikon in zwei Hälften geschnitten, das Meisterwerk entnommen. Der Hohlraum in der Silikonform hat dann die exakte Form des Meisterwerks.
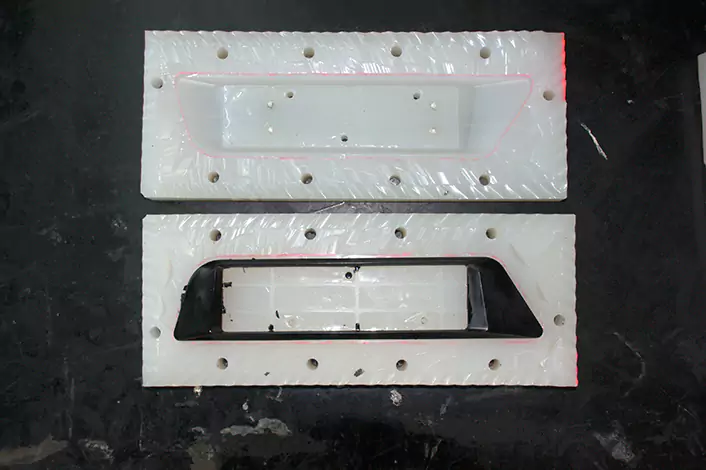
Mischen und gießen Sie das Polyurethan
Vor jedem Guss wird die Oberfläche des Formhohlraums mit einem Trennmittel bedeckt, um ein Anhaften des Urethans zu verhindern.
Das Polyurethan-Material besteht aus zwei separaten Flüssigkeiten, die im richtigen Verhältnis miteinander vermischt werden müssen. Wenn eine Farbe erforderlich ist, sollte die Tönung ebenfalls in die Flüssigkeit gemischt werden. Sobald das Material vermischt ist, beginnt eine chemische Reaktion, die es in ein festes Stück verwandelt. Dies nennt man Aushärten, oder in einem ausgefalleneren Fachjargon, Vulkanisation bei Raumtemperatur. Der Vulkanisationsprozess kann je nach Art des verwendeten Polyurethans Minuten bis Stunden dauern. Anschließend werden die gemischten Polyurethanharze in den Formhohlraum gegossen.
Vakuumkammer
Es ist unvermeidlich, dass beim Mischen Klumpen im Polyurethan entstehen. Die Klumpen könnten die Festigkeit und das Aussehen des Endprodukts beeinträchtigen. Sie müssen entfernt werden. Dazu wird die Form in eine Vakuumkammer gestellt, wo durch den niedrigen Luftdruck um die Form herum Blasen aus der Flüssigkeit entstehen. Aus diesem Grund wird das Urethan-Gießverfahren auch Vakuumgießen genannt.
Entformen Sie das Teil
Sobald das Teil im Formhohlraum ausgehärtet ist, kann es aus der Form entnommen werden. Normalerweise bedeutet dies lediglich, die beiden Hälften der Form zu öffnen und das Produkt herauszunehmen. Wenn das Produkt oder die Form jedoch komplex ist, kann dieser Schritt manchmal eine Herausforderung sein. Sobald die Anschnitte und Steigleitungen vom Teil abgeschnitten sind, entsteht eine perfekte Kopie der Meisterwerksform.
Beenden Sie das Teil
Nachdem das Teil aus der Form entfernt wurde, muss es möglicherweise poliert oder lackiert werden, um das gewünschte Aussehen und die gewünschte Haptik zu erzielen.
Die Silikonform kann für ca. 12–20 Abgüsse verwendet werden, bevor sie ausgetauscht werden muss. Wenn Silikon beim Urethanguss den Harzen ausgesetzt wird, wird es durch den chemischen Abbau hart und zerfällt schließlich.
Ausrüstung erforderlich
Die für Urethangussarbeiten erforderliche Ausrüstung umfasst:
Mischausrüstung
Um das Urethanharz und etwaige Zusatzstoffe genau zu vermischen, sind Mischbehälter, Rührstäbe oder -paddel sowie Messwerkzeuge erforderlich.
Formtrennmittel
Typischerweise wird ein Sprüh- oder Pinselapplikator verwendet, um das Trennmittel auf die Formoberfläche aufzutragen.
Vakuumkammer und Pumpe
Mit optionaler Ausrüstung werden Luftblasen aus der Mischung entfernt und die Qualität des endgültigen Gussstücks verbessert.
Heizgeräte
In einigen Fällen kann Wärme verwendet werden, um den Aushärtungsprozess des Urethanmaterials zu beschleunigen.
Persönliche Schutzausrüstung (PPE)
Möglicherweise sind Handschuhe, Schutzbrille und eine Atemschutzmaske erforderlich, um den Anwender vor dem Kontakt mit dem Urethanmaterial und etwaigen Dämpfen zu schützen.
Form
Das zu gießende Objekt besteht typischerweise aus Silikon, Polyurethan oder anderen Materialien.
Werkbank oder Tisch
Damit die Form und das Gussmaterial während des Gussprozesses stabil bleiben, ist ein ebener und ebener Untergrund erforderlich.
Klammern oder Gewichte
Wird verwendet, um Produktionsteile in der Form an der Arbeitsfläche zu befestigen und jegliche Bewegung während des Gießvorgangs zu verhindern.
Anwendungen des Urethangusses
Zu den Anwendungen des Urethangusses gehören:
Prototyping
Mit Urethanguss können schnell und kostengünstig Prototypen von Produkten hergestellt werden. Der Prozess ermöglicht es Designern und Ingenieuren, ihre Entwürfe zu testen und Änderungen vorzunehmen, bevor sie sich für teure Werkzeuge entscheiden.
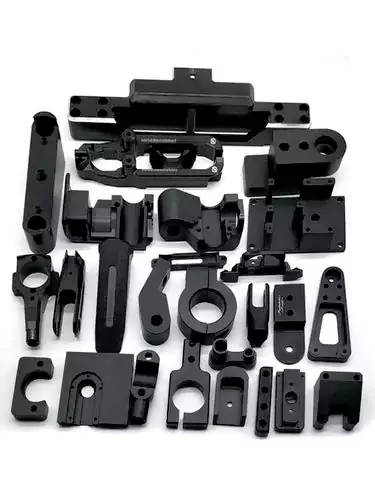
Kleinserienproduktion
Urethanguss ist ein ideales Verfahren zur Herstellung kleiner bis mittlerer Teilemengen. Die beim Urethanguss verwendeten Formen sind langlebig und können qualitativ hochwertige Teile in einer begrenzten Produktionsserie herstellen.
Ersatzteile
Urethanguss ist eine hervorragende Methode zur Herstellung von Ersatzteilen für Maschinen, Geräte und andere Produkte. Dieses Verfahren ermöglicht eine schnelle Durchlaufzeit und eine kostengünstige Produktion von Teilen, die nicht mehr verfügbar oder mit anderen Methoden zu teuer für die Herstellung sind.
Medizinische Geräte
Urethanguss wird häufig bei der Herstellung von medizinischen Geräten wie Prothesen, Zahnspangen und anderen orthopädischen Geräten verwendet. Der Prozess ermöglicht die Erstellung maßgeschneiderter Geräte, die leicht an die Bedürfnisse des Patienten angepasst werden können.
Verbraucherprodukte
Urethanguss wird bei der Herstellung einer breiten Palette von Konsumgütern verwendet, darunter Spielzeug, Sportgeräte und Haushaltswaren. Das Verfahren ermöglicht die Herstellung hochwertiger Produkte, die individuell angepasst und in kleinen Mengen hergestellt werden können.
Automobil- und Luftfahrtteile
Urethanguss wird bei der Herstellung von Automobil- und Luftfahrtteilen wie Stoßfängern, Spoilern und Innenraumkomponenten verwendet. Der Prozess ermöglicht die Herstellung leichter, langlebiger und hochwertiger Teile, die den strengen Anforderungen dieser Branchen gerecht werden.
Warum sollten Sie sich für Urethanguss entscheiden?
Zu den Vorteilen des Urethangusses gehören:
Kosten sparen
Wenn Dutzende von Prototypen erforderlich sind, sind Urethan-Gussteile oft pro Stück kostengünstiger als die additive Fertigung. Generative Fertigung kann den Preis erhöhen, da für die Herstellung von mehr Prototypen mehrere Bauvorgänge erforderlich sind, während mit dem Urethangussverfahren Teile kontinuierlich geformt werden können.
Zur Herstellung gegossener Urethanteile werden üblicherweise Silikonformen verwendet. Die Kosten für Silikonformen sind in der Regel deutlich niedriger als die für Aluminium- oder Stahlwerkzeuge, die beim Spritzgießen verwendet werden. Die für die Herstellung von Urethanteilen erforderlichen Formen können Hunderte bis Tausende von Dollar kosten, während Spritzgusswerkzeuge Tausende bis Zehntausende Dollar kosten können.
Design-Flexibilität
Beim Formen von Urethan werden weiche Werkzeuge oder Silikonformen verwendet, um gegossene Urethanteile herzustellen, sodass Designänderungen schnell auf der Grundlage von Kundenfeedback umgesetzt werden können. Da Silikonformen eine begrenzte Anzahl an Schüssen haben (normalerweise 25–30 pro Form), können Designänderungen von Form zu Form mit minimalen Kosten vorgenommen werden. Selbst wenn ein Werkzeug überarbeitet oder neu angefertigt werden muss, betragen die Kosten nur einen Bruchteil dessen, was ein Spritzgusswerkzeug kosten würde, und die Vorlaufzeit halbiert sich.
Designflexibilität ist ein weiterer Vorteil dieses Prozesses, der es ermöglicht, dass Produkte schwer formbare Merkmale wie Hinterschnitte, dicke Abschnitte oder andere Elemente enthalten, die beim Spritzgießen aufgrund der Verwendung von weichen Werkzeugen und duroplastischen Materialien nicht erreichbar wären.
Mit flexiblen und elastischen Formen können Teile ohne teure Handlasten oder Schlitten entnommen werden, wie sie beim Spritzgießen erforderlich sind. Formen können auch in mehreren Teilen erstellt werden, die einfach entfernt werden können, um das Teil zu lösen und für die nächsten Aufnahmen zusammenzubauen.
Werkzeugvorlaufzeit
Im Vergleich zum herkömmlichen Spritzgießen ist die Werkzeugvorlaufzeit für das Formen von Urethansilikon kürzer. Während die Herstellung eines Spritzgusswerkzeugs vier bis zwölf oder mehr Wochen dauern kann, können Silikonformen, die beim Urethanguss verwendet werden, unabhängig von der Teilegröße in nur ein bis zwei Tagen fertiggestellt werden.
Materielle Opfergaben
Beim Urethanformen werden Polyurethane verwendet, um die Eigenschaften von Kunststoffen in Produktionsqualität zu reproduzieren, die beim Spritzgießen verwendet werden. Urethanguss wird sehr oft verwendet, um das richtige Material für die spätere Massenproduktion zu bestimmen.
Teilfertigstellung
Gegossene Urethane besitzen Festigkeit und Oberflächenfinish Das ist sehr vergleichbar mit Spritzgussteilen. 3D Druck Andererseits kann nicht die gleiche Festigkeit und Oberfläche bereitgestellt werden. Dies ist ein weiterer Grund dafür, dass Urthanguss zum Testen und Entscheiden verwendet wird, welches Material für die Massenproduktion verwendet werden soll.
Urethanguss vs. Unterschiede beim Kunststoffspritzguss
Schauen wir uns einige Unterschiede genauer an, die Sie bei der Wahl zwischen Spritzguss und Urethanguss beachten sollten:
Ein wichtiger Aspekt sind die Vorlaufkosten, da Spritzgussformen aufgrund ihrer Metallkonstruktion weitaus teurer sind. Dies macht das Spritzgießen zu einer besseren Option für die langfristige Massenproduktion, während Urethan-Gussformen wesentlich kostengünstiger hergestellt werden können, was sie ideal für Einzelanfertigungen oder Kleinserien eignet.
Auch die Materialkosten sind ein zu berücksichtigender Faktor. Kunststoffe in Produktionsqualität wie PVC, ABS, Acetal und LPDE sind viel teurer als Urethan, weshalb Urethan die bessere Wahl für Prototypen und Kleinserienarbeiten ist.
Die Vorlaufzeiten für das Spritzgießen können lang sein, manchmal dauert die Herstellung der Formen Monate. Urethan-Silikonformen hingegen lassen sich viel schneller herstellen und können sogar mit einem hergestellt werden 3D Drucker oder von Hand. Dies verkürzt die Vorlaufzeiten erheblich und ermöglicht eine schnelle Produktlieferung.
Die Kosten pro Teil sind beim Urethanguss in der Regel höher, da mit jeder Form nur eine begrenzte Anzahl von Teilen hergestellt werden kann. Beim Spritzgießen hingegen entstehen höhere Stückzahlen, was zu geringeren Material- und Werkzeugkosten führt. Insgesamt ist das Spritzgießen in der Regel die kostengünstigste Option für eine langfristige Produktion.
Schlussfolgerung
Zusammenfassend lässt sich sagen, dass Urethanguss eine wertvolle Alternative ist Kunststoff-Spritzguss für Kleinserienfertigung und Prototyping. Während es einige Nachteile wie begrenzte Materialoptionen und Kosten pro Teil mit sich bringt, bietet Urethanguss Vorteile wie schnellere Vorlaufzeiten, niedrigere Vorlaufkosten und anpassbare Eigenschaften. Wenn Sie die Unterschiede zwischen den beiden Prozessen verstehen und die spezifischen Anforderungen Ihres Projekts berücksichtigen, können Sie eine fundierte Entscheidung darüber treffen, welche Methode für Ihre Produktentwicklungs- und Produktionsziele am besten geeignet ist.