Spritzgießen ist eine weit verbreitete Fertigungsmethode zur effizienten Herstellung großer Mengen identischer Kunststoffkomponenten mit präzisen Toleranzen. Bei diesem Verfahren werden thermoplastische Flocken oder Pellets geschmolzen und dann in eine Form eingespritzt. Nachdem der geschmolzene Kunststoff abgekühlt und erstarrt ist, werden Auswerferstifte verwendet, um das fertige Teil aus der Form zu entnehmen. Spritzguss wird in zahlreichen Konsumgütern eingesetzt, von Alltagsgegenständen wie Telefonladegeräten und Legosteinen bis hin zu Automobilkomponenten.
Sobald die Form erstellt ist, bietet sie Ingenieuren eine zuverlässige Möglichkeit, komplizierte Teile konsistent und kostengünstig zu reproduzieren. Daher kommt der Verfeinerung der Formenbauprozesse eine enorme Bedeutung zu.
Bedeutung der Designverbesserung
Designverbesserungen bei Kunststoffspritzgussteilen sind aus mehreren Gründen von großer Bedeutung:
Verbesserte Funktionalität und Leistung
Die Verbesserung des Designs von Spritzgussteilen kann zu einer verbesserten Funktionalität und Leistung führen. Durch die Optimierung der Geometrie der Spritzgussteile, die Integration von Merkmalen für eine bessere strukturelle Integrität und die Beseitigung von Konstruktionsfehlern kann die Gesamtfunktionalität der Teile verbessert werden. Dies kann zu einer besseren Produktleistung und Kundenzufriedenheit führen.
Kostenreduzierung
Designverbesserungen können dazu beitragen, die mit Spritzgussteilen verbundenen Kosten zu senken. Durch die Optimierung der Teilegeometrie ist es möglich, den Materialverbrauch zu minimieren, was zu Materialkosteneinsparungen führt. Darüber hinaus können vereinfachte Designs und verbesserte Formbarkeit zu einer geringeren Werkzeugkomplexität und Produktionszeit führen, was zu Kosteneinsparungen bei der Herstellung führt.
Qualität und Beständigkeit
Designverbesserungen tragen zu einer verbesserten Teilequalität und -konsistenz bei. Eine gleichmäßige Wandstärke, die richtige Anschnittplatzierung und das Entlüftungsdesign tragen dazu bei, eine gleichmäßige Füllung zu erreichen und Fehler wie Einfallstellen und Verwerfungen zu reduzieren. Indem man sich darauf konzentriert Design für Herstellbarkeit (DFM)-Prinzipien erhöht die Wahrscheinlichkeit, gleichbleibend hochwertige Teile zu erhalten.
Produktionseffizienz
Optimierte Designs ermöglichen effiziente Fertigungsprozesse. Durch die Zusammenarbeit mit Formenbauern und die Berücksichtigung der Formbarkeit während der Entwurfsphase können potenzielle Fertigungsherausforderungen bereits im Vorfeld erkannt und gelöst werden. Dies führt zu reibungsloseren Produktionsabläufen, reduzierten Ausfallzeiten und erhöhter Produktivität.
Materialauswahl und Innovation
Designverbesserungen ermöglichen die Erforschung und Nutzung fortschrittlicher Materialien und Zusatzstoffe. Durch verbesserte Designmerkmale wird es möglich, Materialien mit verbesserten Eigenschaften wie erhöhter Festigkeit, Hitzebeständigkeit oder verbesserter Ästhetik zu nutzen. Dies eröffnet Möglichkeiten für Innovation und Differenzierung in der Produktentwicklung.
Nachhaltigkeit und Umweltauswirkungen
Designverbesserungen können auch zu Nachhaltigkeitsbemühungen beitragen. Durch die Reduzierung von Materialverschwendung durch optimierte Designs, die Verwendung recycelter Materialien oder den Einsatz umweltfreundlicher Zusatzstoffe können die mit Spritzgussteilen verbundenen Umweltauswirkungen minimiert werden.
Tipps zum Design von Spritzgussformen
Die Konstruktion von Teilen für das Spritzgießen bietet Produktdesignern erhebliche Flexibilität bei der Integration komplexer Geometrien. Für Produktteams ist es jedoch von entscheidender Bedeutung, ihre Designs an den spezifischen Anforderungen des Unternehmens auszurichten Spritzgießen verarbeiten.
Die Änderung des Designs nach der Herstellung des Teils stellt erhebliche Herausforderungen dar. Daher müssen Produktdesigner zunächst sicherstellen, dass das Kunststoffteil für den Spritzguss einwandfrei ausgelegt ist. Dieser Ansatz minimiert das Risiko von Werkzeugkonstruktionsproblemen, maximiert die Ergebnisse und senkt die Kosten. Um saubere und funktionsfähige Teile zu erstellen, empfiehlt es sich, die folgenden Tipps für die Kunststoffspritzgusskonstruktion zu beachten:
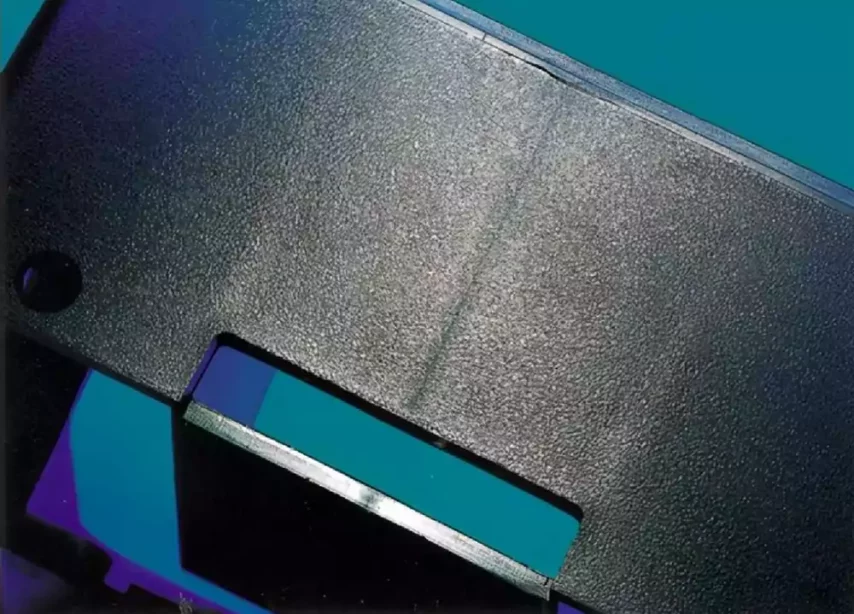
Unvermeidliche Spuren
Spritzguss Teile haben mehrere Markierungen, die nicht vermieden werden können, Trennlinien, Auswurfstiftmarkierungen, Stichmarkierungen/Anschnitte und einige Schweißmarkierungen. Es ist wichtig, sie an geeigneten Orten zu platzieren, wo sie weder das Aussehen noch die Funktion beeinträchtigen. Das ist eine sehr wichtige Aufgabe beim Entwerfen eines Spritzgussteils. Jedes Formteil weist eine sichtbare Trennlinie an der Stelle auf, an der sich die beiden Formhälften trennen, sowie Markierungen der Auswerferstifte und Anschnittpositionen. Diese Elemente sind Teil des Formprozesses und können nicht vollständig eliminiert werden. Daher ist es wichtig, diese Faktoren bereits in der ersten Entwurfsphase des Teils zu berücksichtigen, um negative Auswirkungen auf die Ästhetik oder strukturelle Integrität des Teils zu vermeiden.
Kunststoff schrumpft
Darüber hinaus ist es wichtig, die Materialschrumpfung während des Abkühlprozesses zu berücksichtigen. Dieses Phänomen tritt beim Abkühlen des Materials auf und kann die Abmessungen des Teils beeinflussen. Um die Maßhaltigkeit sicherzustellen, sollte beim Werkzeugaufbau die erwartete Schrumpfung berücksichtigt werden. Es ist außerdem wichtig zu verhindern, dass das Teil in der Form stecken bleibt, weil das Material um die Stahlelemente herum schrumpft. Durch die Berücksichtigung dieser Faktoren während des Designprozesses können die potenziellen Probleme im Zusammenhang mit der Materialschrumpfung gemindert werden.
Behalten Sie konstante Wandstärken bei
Die Steuerung der Formdicke ist ein grundlegendes Prinzip bei der Konstruktion von Spritzgussteilen. Ungleichmäßige Wandstärken können beim Abkühlen des thermoplastischen Materials zu Problemen wie Verzug oder Einfallstellen führen. Die empfohlenen Wandstärken variieren je nach Art des verwendeten Kunststoffs. Beispielsweise hat Polyurethan (PUR) typischerweise eine gleichmäßige Wandstärke im Bereich von 0.080 bis 0.750 Zoll, während Polystyrol (PS) einen engeren Bereich von 0.035 bis 0.150 Zoll aufweist. Eine allgemeine Richtlinie empfiehlt, die Wandstärke zwischen 1.2 mm und 3 mm zu halten, um optimale Ergebnisse zu erzielen.

Bei der Konstruktion von Teilen mit unterschiedlichen Dicken ist es wichtig, auf fließende Übergänge zwischen ihnen zu achten. Dies fördert den gleichmäßigen Fluss des geschmolzenen Kunststoffs innerhalb des Formhohlraums. Ein effektiver Ansatz besteht darin, eine Fase oder Ausrundung einzubauen, die dreimal so lang ist wie der Dickenunterschied.
In einigen Fällen erfordern komplexe Geometrien dickere Abschnitte in der Spritzgussformkonstruktion. Diese Abschnitte können jedoch zu Mängeln wie Verzug und Einsinken führen. Um dieses Problem zu lösen, können Produktdesigner diese dickeren Abschnitte aushöhlen und dabei die vorgeschriebenen Wandstärkenbeschränkungen einhalten. Die Einbeziehung von Rippen in das Teil trägt zur Verstärkung der ausgehöhlten Abschnitte bei und sorgt für strukturelle Steifigkeit.
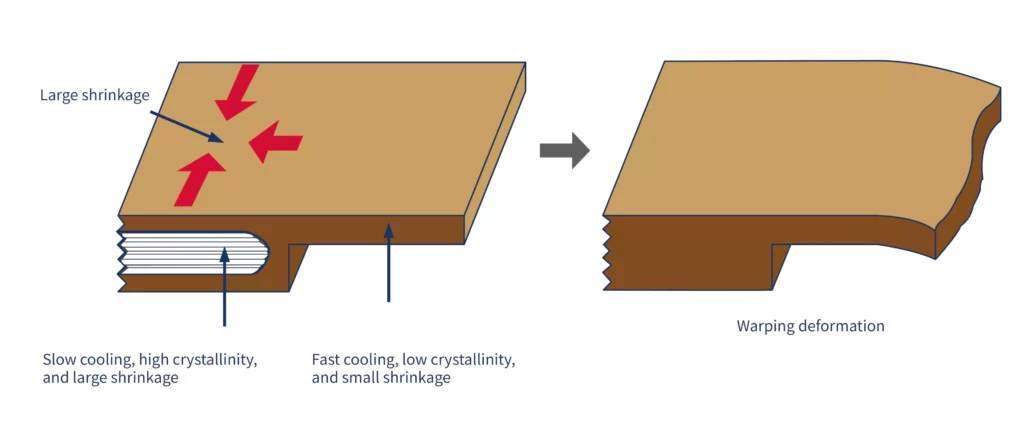
Die geeignete Dicke der Rippen hängt vom jeweils verwendeten Thermoplast ab. Im Allgemeinen sollten Rippen weniger als zwei Drittel der Hauptwandstärke betragen, um Einfallstellen auf der Außenfläche durch zu große Rippenstärke zu vermeiden.
Beseitigen Sie unwichtige Hinterschneidungen
Hinterschnitte in Spritzgussteilen beziehen sich auf Merkmale, die das saubere Auswerfen des Teils aus der Form verhindern, ohne dass es zu strukturellen Schäden kommt. Hinterschneidungen können verschiedene Formen annehmen, beispielsweise Löcher, Hohlräume oder Bereiche, in denen die Ausrichtung von der Trennlinie der Form abweicht. Idealerweise sollten Produktdesigner danach streben, Hinterschnitte gänzlich zu vermeiden, da sie die Komplexität, Kosten und Arbeitsintensität des Spritzgussformdesigns unnötig erhöhen.
Es gibt jedoch einige Designstrategien, um Hinterschneidungen zu beheben, wenn sie nicht vollständig vermieden werden können. Ein Ansatz besteht darin, die Trennlinie der Form so anzupassen, dass sie den Hinterschnitt schneidet. Diese Methode eignet sich vor allem für Konstruktionen mit Hinterschnitten an der Außenseite der Form.
Für flexible Merkmale und Materialien besteht eine weitere Option darin, Bumpoffs oder Stripping-Hinterschnitte zu verwenden. Bei Bumpoffs wird ein Merkmal entworfen, das sich beim Auswerfen über die Form ausdehnen und verformen kann. Es ist wichtig, den Abdruck von den Stützstrukturen der Form entfernt zu positionieren und sicherzustellen, dass er einen Steigungswinkel von 30 bis 45 Grad aufweist.
Als letzten Ausweg, wenn Hinterschneidungen durch Konstruktionsänderungen nicht beseitigt werden können, können Seiteneingriffe oder Heber eingesetzt werden. Bei seitlich wirkenden Kernen handelt es sich um senkrechte Einsätze, die beim Öffnen und Schließen in die Form hinein- und herausgleiten. Es ist jedoch wichtig zu beachten, dass diese Mechanismen die Kosten und die Komplexität erheblich erhöhen. Auch wenn diese Lösungen verfügbar sind, wird den Designern empfohlen, Hinterschneidungen wann immer möglich zu vermeiden und Hinterschneidungen während der Prototyping-Phase zu eliminieren.
Schaffen Sie Platz für Zugluft
Durch die Einbeziehung einer leichten Verjüngung, die üblicherweise als Formschräge bezeichnet wird, in die Teilekonstruktion kann der Auswurfvorgang aus der Form erheblich verbessert werden. Dies ist besonders vorteilhaft, um Kratzer und Reibung zwischen dem fertigen Produkt und der Form zu reduzieren. Dadurch bleibt die Oberfläche des Bauteils unbeschädigt und der gesamte Fertigungsprozess verläuft effizienter.
Einen Entwurf zu verstehen ist so einfach wie die Vorstellung einer Eiswürfelschale. Wenn Eiswürfel geformt und aus dem Gefrierschrank genommen werden, ist es nicht nötig, sie mit einem Werkzeug gewaltsam aus ihren einzelnen Formen zu hebeln. Dies liegt daran, dass die Eiswürfelschale durch ihre Teilkonstruktion einen gewissen Luftzug aufweist, sodass die Würfel bei leichtem Druck mühelos herausspringen können. Ebenso ermöglicht die Integration von Formschrägen in Spritzgussteile ein reibungsloses Auswerfen aus der Form und rationalisiert so den Produktionsprozess. Der typische Entformungswinkel beträgt 1 bis 3 Grad.
Schlussfolgerung
Zusammenfassend lässt sich sagen, dass die Verbesserung des Designs von Spritzgussteilen von größter Bedeutung ist, um optimale Ergebnisse in Bezug auf Funktionalität, Kosteneffizienz, Qualität und Nachhaltigkeit zu erzielen. Durch die sorgfältige Verwaltung von Faktoren wie Wandstärke, Entformungsschrägen, Nennwandstärke, Hinterschneidungen und Materialschrumpfung können Produktdesigner Teile erstellen, die für den Spritzgussprozess geeignet sind.
Das Streben nach verbesserten Designs für Spritzgussteile ermöglicht es Herstellern, die Erwartungen der Kunden zu erfüllen, die Produktleistung zu verbessern, die Herstellungskosten zu senken und zu Nachhaltigkeitsbemühungen beizutragen. Durch die Nutzung von Designverbesserungen können Produktdesigner das volle Potenzial des Spritzgusses ausschöpfen und hochwertige Kunststoffteile herstellen, die in zahlreichen Konsumgütern unseres täglichen Lebens unverzichtbar sind.