Einige Hinterschnittmerkmale sind unvermeidlich
Im Spritzgussverfahren ist es wichtig, Designs mit Hinterschneidungen zu vermeiden, da diese beim Entformen des Produkts Probleme verursachen können. Aber manchmal sind diese Hinterschneidungen notwendig, damit das Produkt richtig funktioniert. Daher müssen Produktdesigner die Methoden des Hinterschnittformens erlernen. Wenn Konstrukteure dies verstehen, wissen sie, was möglich ist und was nicht und wie sich dies auf die Kosten für die Herstellung der Form und des Spritzgusses auswirkt. In diesem Artikel werden verschiedene Möglichkeiten zum Erstellen dieser Hinterschneidungen in Formen erläutert.
Zu den Möglichkeiten, mit Hinterschneidungsspritzguss umzugehen, gehören das Anpassen der Trennlinie, das Einbringen von Schlitzen, die Verwendung von Kernzügen, Schiebemechanismen, Hebern, Opferkernen, Abstreifkernen, handbestückten Kernen, Abschraubmechanismen und zusammenklappbaren Kernen. Weitere Informationen zu jeder dieser Methoden finden Sie weiter unten.
Trennlinie anpassen
Eine Trennlinie für eine Form Spritzgießen ist die Grenze oder Trennlinie zwischen den beiden Hälften einer Form, bekannt als „Kern“ und „Hohlraum“. Diese Linie markiert den Trennpunkt, an dem diese Formhälften aufeinandertreffen und sich trennen, um das fertig geformte Produkt freizugeben. Verschieben Sie die Trennlinie der Form an den Punkt, an dem der Hinterschnitt beginnt. Dadurch wird der Hinterschnitt aufhören, ein Hinterschnitt zu sein. Diese Methode eignet sich nur für Hinterschnitte an der Außenseite des Teils. Hinterschneidungen innerhalb des Teils können nicht behoben werden. Durch die Anpassung der Trennfuge steigen die Herstellungskosten der Form kaum. Diese Methode sollte wann immer möglich angewendet werden.
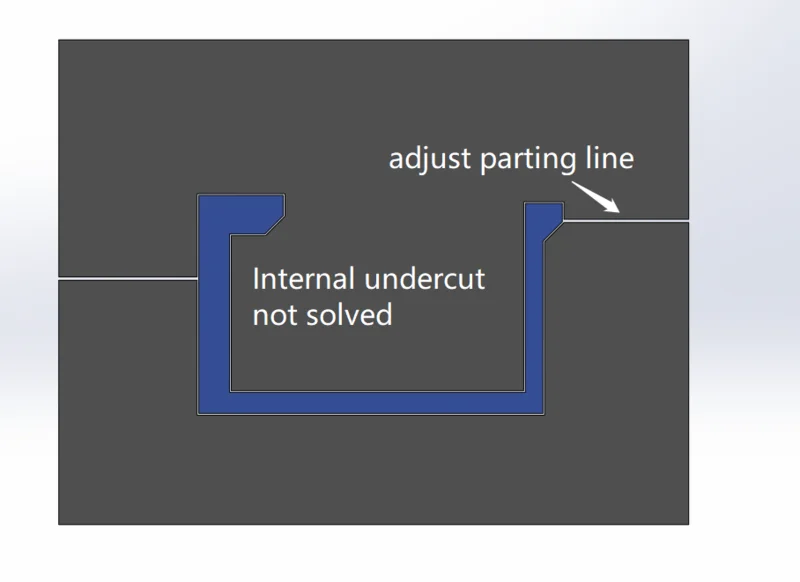
Einbindung von Slots
Auch das Anbringen einer Rille am unteren Rand der Hinterschneidung und das Entfernen des blockierenden Kunststoffs können das Problem der Hinterschneidung lösen. Diese Methode erhöht auch kaum die Herstellungskosten der Form, aber die Nut kann das Aussehen, die Festigkeit und manchmal auch die Funktionalität des Teils beeinträchtigen. Es ist nicht für alle Situationen geeignet.
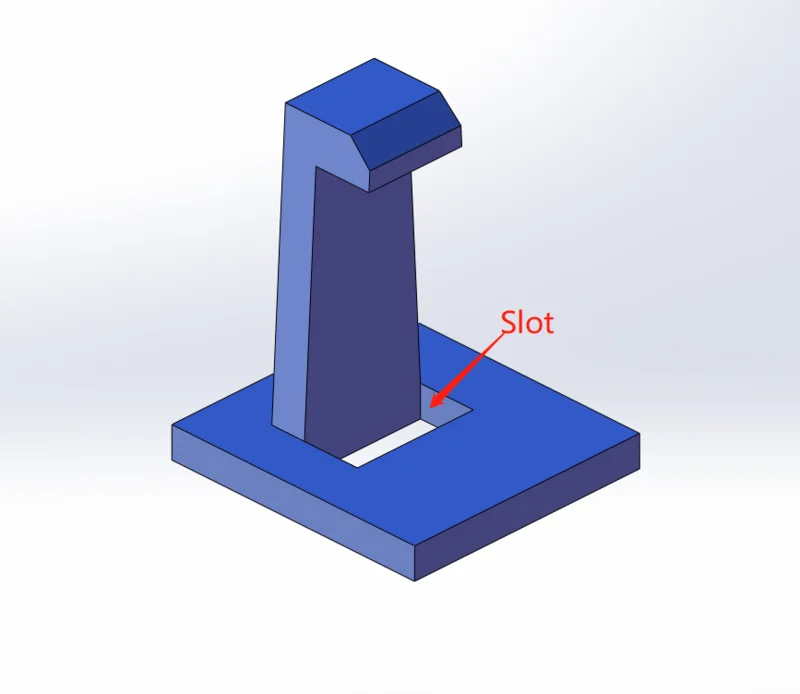
Kernzüge
Wie in Abbildung 1 dargestellt, bildet die Unterseite des Teils eine Hinterschneidung. Die Seitenkerne werden durch einen pneumatischen oder hydraulischen Mechanismus angetrieben. Dieser Mechanismus ist mit der hydraulischen bzw pneumatischer Druck der Spritzgießmaschine während des Spritzgießvorgangs. Entweder vor dem Öffnen der Form oder vor dem Auswerfen des Teils wird der Kern gezogen und dann das Teil ausgeworfen.
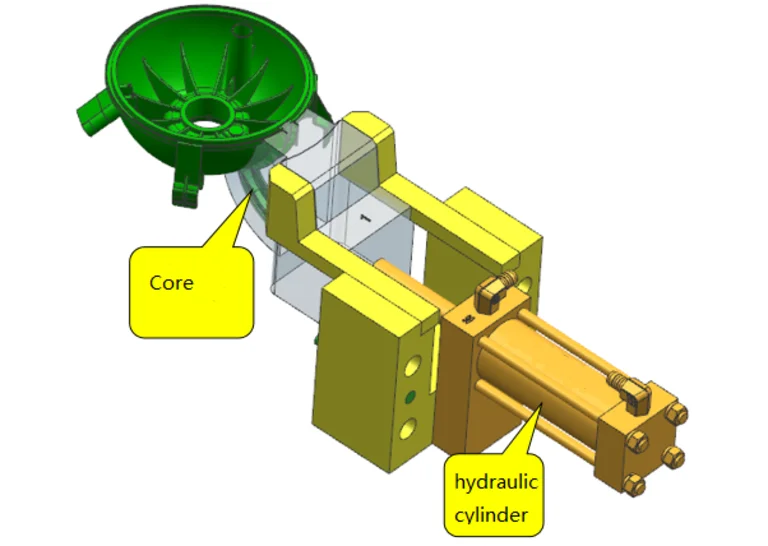
Für längere Kernbewegungen oder wenn mehr Kraft benötigt wird, kommt der hydraulische Kernrückzug zum Einsatz. Wenn schnelles Spritzgießen erforderlich ist und der Verfahrweg gering ist, wird häufig ein pneumatischer Antrieb verwendet. Diese Kernzugstruktur erfordert einige zusätzliche Teile zur Unterstützung des Kernrückzugsmechanismus, ist aber immer noch ein relativ einfacher Ansatz für die Formgestaltung. Im Vergleich zu anderen Strukturen ist es relativ unkompliziert und erhöht die Kosten für die Formherstellung nicht wesentlich. Auch die zusätzlichen Kosten für Zylinder, egal ob hydraulisch oder pneumatisch, sind vertretbar.
Während des Produktionsprozesses ist es jedoch wichtig, auf mögliche Öl- oder Luftlecks zu achten.
Hebemechanismen und Schiebemechanismen
Hebemechanismen sind typischerweise als bewegliche Elemente innerhalb der Form konzipiert. Beim Öffnen der Form bewegen sich diese Mechanismen beim Auswurfvorgang in vertikaler Richtung und heben das Formteil von den Hinterschneidungen ab, sodass es sicher aus der Form ausgeworfen werden kann. Diese Bewegung trägt dazu bei, das Teil aus der Form zu lösen, ohne dass es zu Beschädigungen oder Verformungen kommt. Lifter werden normalerweise verwendet, um interne Hinterschneidungen zu beheben.
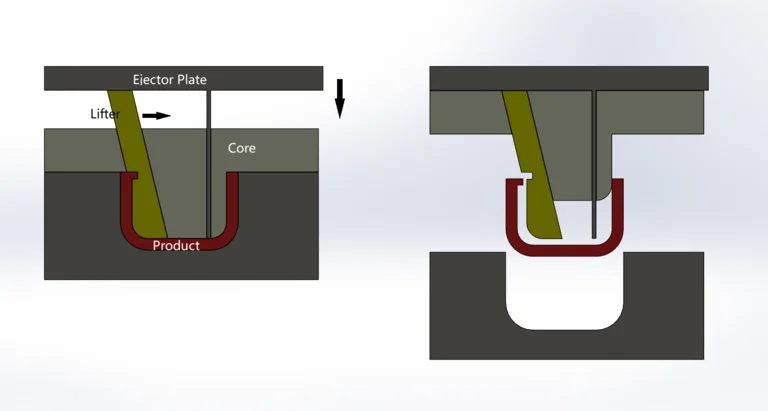
Schieber bewegen sich horizontal innerhalb der Form. Beim Öffnen der Form bewegen sich diese Schieber parallel zur Trennlinie der Form und ermöglichen so ein sanftes Lösen des Formteils aus den hinterschnittenen Bereichen. Durch das Hinein- und Herausschieben schaffen sie den nötigen Freiraum, damit das Teil ausgeworfen werden kann, ohne dabei hängenzubleiben oder beschädigt zu werden. Schieber werden normalerweise verwendet, um äußere Hinterschneidungen zu beheben.
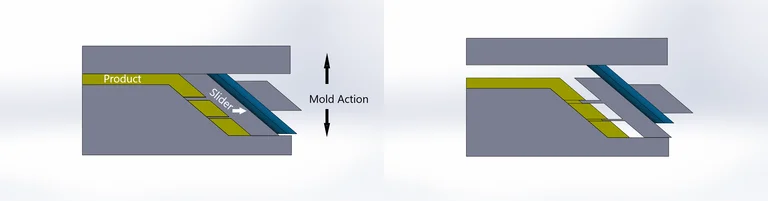
Sowohl Heber als auch Schieber erfordern komplexe Formstrukturen und erhöhen die Herstellungskosten der Form erheblich. Diese Mechanismen gelten jedoch als die zuverlässigste Methode zum Hinterschnittspritzgießen. Daher sind sie im Formenbau sehr beliebt.
Abschläge
Beim Abstoßen wird ein bewegliches Merkmal oder eine bewegliche Komponente in der Form geschaffen, die das geformte Teil während des Auswurfvorgangs von einer Hinterschneidung abstoßen oder „abstoßen“ kann. Dies ermöglicht die erfolgreiche Entnahme des Teils aus der Form, selbst wenn Hinterschneidungen vorhanden sind, und sorgt so für einen reibungslosen und effizienten Kunststoffspritzgussprozess.
Bei der Verwendung von Bump-Offs im Formdesign für das Kunststoffspritzgießen kann es beim Öffnen der Form zu einer leichten Verformung oder Durchbiegung des Kunststoffprodukts kommen. Der Abstoßmechanismus ist so konzipiert, dass er eine kontrollierte Kraft ausübt, um das Formteil zu lösen, insbesondere wenn komplexe Hinterschnitte vorhanden sind. Diese kontrollierte Kraft kann zu einer vorübergehenden Verformung oder Biegung des Kunststoffprodukts führen. Aufgrund seiner elastischen Eigenschaften nimmt der Kunststoff jedoch typischerweise wieder seine vorgesehene Form an, sobald er vollständig aus der Form gelöst ist. Der Grad der Verformung und die Fähigkeit des Materials, sich zurückzubiegen, hängen von verschiedenen Faktoren ab, wie etwa den Materialeigenschaften, dem Design und dem spezifischen Abstoßmechanismus, der in der Form verwendet wird.
Bei eher flexiblen Materialien sollten Abschläge verwendet werden, hartes und sprödes Material könnte brechen. Und der Abstoßwinkel sollte 30–45 Grad betragen. Faserverstärktes Material ist im Allgemeinen nicht für Bump-Offs geeignet, Glasfaser oder Faserkohlenstoff machen Kunststoff spröde und können bei Bump-Offs leicht brechen.
Bump-Off-Designs sind im Vergleich zur Lifter- oder Slider-Lösung relativ kostengünstig, die Verwendung ist jedoch durch die Komplexität des Materials und der Spritzgussteile begrenzt.
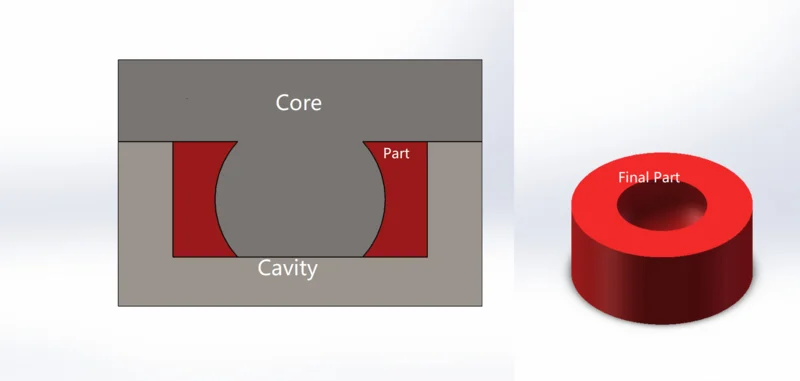
Von Hand geladene Kerne
Der handbeladene Kern ist eine alternative Methode eines Hebers oder Schiebers. Anstatt die ineinandergreifenden Elemente des Kerns anzuheben oder zu verschieben, Es wird in ein abnehmbares Teil oder einen Einsatz verwandelt. Nach dem Produktauswurf wird der Einsatz manuell entnommen. Da der Einsatz manuell in die Spritzgussform eingelegt und nach dem Spritzen entfernt werden muss, erhöht diese Methode die Arbeitskosten und die Zykluszeit des Spritzgusses. Im Vergleich zur Heber- oder Schieberkonstruktion werden dadurch Formkosten eingespart. Nicht alle Hinterschneidungen können auf diese Weise gelöst werden. Für Kleinserienfertigungen oder komplexe Hinterschnitte ist diese Methode eine gute Lösung.
Abschraubmechanismen
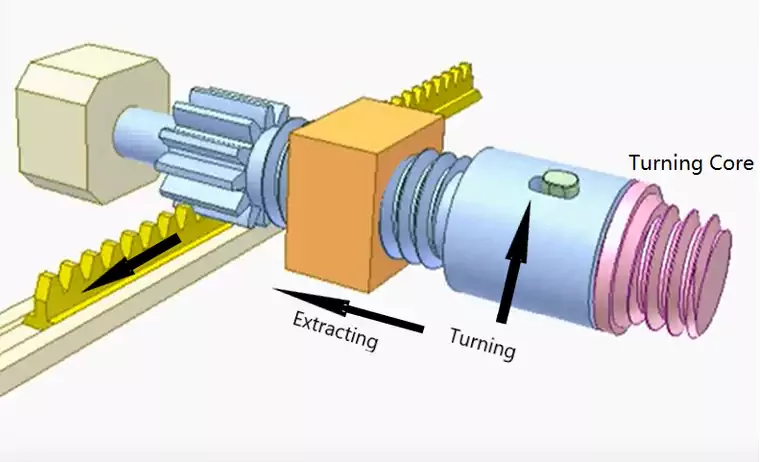
Schraubengewinde in einem Spritzgussteil erzeugen Hinterschnitte. Um dieses Problem zu lösen, ist ein Drehkern erforderlich. Der Drehvorgang erfolgt entweder durch das Öffnen der Form oder durch einen Hydraulikzylinder.
Beim Öffnen der Form treibt der Hydraulikzylinder vor dem Öffnungsvorgang eine Reihe von Zahnrädern an, dreht sich, schraubt den Drehkern heraus und zieht ihn heraus. Damit das Schraubengewinde beim Öffnen der Form nicht abgerissen wird.
Der Abschraubmechanismus ist speziell auf die Hinterschnittmerkmale des Schraubengewindes ausgelegt. Es erfordert zusätzliche 3 oder mehr Zahnräder und ein paar Lager im Mechanismus. Bediener müssen bei der Formwartung sehr vorsichtig sein und sicherstellen, dass die Zahnräder nicht beschädigt oder falsch ausgerichtet sind. Sowohl die Wartung als auch die zusätzlichen Mechanismen erhöhen die Formkosten. Aber es ist immer noch die gebräuchlichste Methode, um Probleme mit dem Unterschnitt des Schraubengewindes zu beheben.
Zusammenklappbare Kerne
Faltkerne sind Spezialkomponenten, die beim Kunststoffspritzguss zur Bearbeitung von Hinterschnitten oder komplexen Teilegeometrien verwendet werden. Sie dienen dazu, innere Merkmale oder Hohlräume in einem Kunststoffteil zu erzeugen, die normalerweise ein einfaches Auswerfen aus der Form verhindern würden.
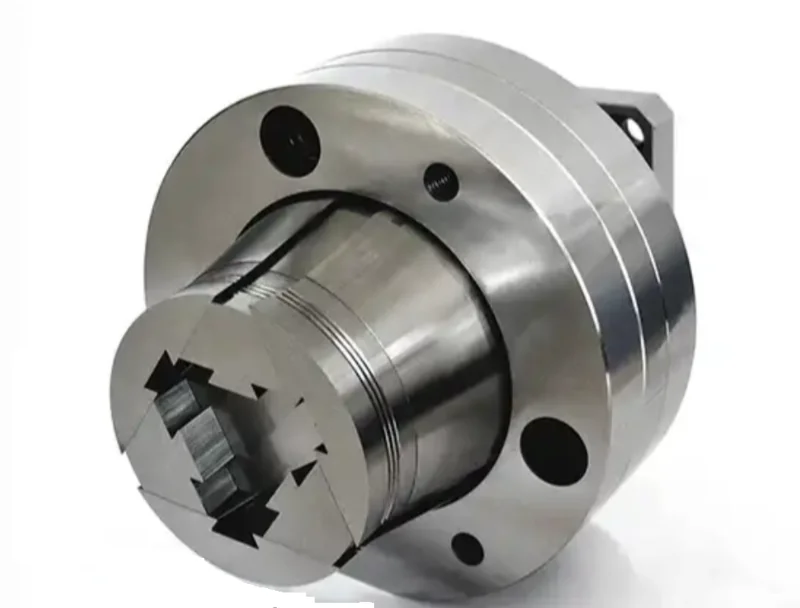
So funktionieren sie:
Ausgangsform: Zunächst hat der faltbare Kern eine größere Form, die in die Form passt und das Einspritzen von Kunststoff um ihn herum ermöglicht.
Spritze: Kunststoffmaterial wird in die Form um den faltbaren Kern herum eingespritzt und nimmt die Form der Form und die ursprüngliche Form des faltbaren Kerns an.
Rückzug: Nachdem das Kunststoffmaterial abgekühlt und verfestigt ist, wird der kollabierbare Kern nach innen zurückgezogen bzw. kollabiert. Dadurch entstehen interne Hinterschnitte oder Hohlräume im Formteil.
Auswurf: Sobald der zusammenklappbare Kern zurückgezogen ist, lässt sich das Formteil mit den inneren Merkmalen leicht aus der Form auswerfen.
Zusammenklappbare Kerne sind besonders nützlich für die Herstellung komplexer Teile mit inneren Hinterschnitten, Gewinden, Löchern oder anderen komplizierten Merkmalen, deren Herstellung mit herkömmlichen Formtechniken ansonsten schwierig wäre. Sie ermöglichen eine effiziente Produktion komplexer Teile und gewährleisten gleichzeitig ein reibungsloses Auswerfen aus der Form.
Bei kollabierbaren Kernen handelt es sich um komplizierte Strukturen aus hochpräzisen Metallkomponenten, die erheblich zu den zusätzlichen Formkosten beitragen. Daher werden sie am effektivsten in Szenarien der Massenproduktion oder in Fällen eingesetzt, in denen alternative Formenkonstruktionen Schwierigkeiten haben, den Anforderungen des Spritzgießens für ein bestimmtes Teil gerecht zu werden.
Sprechen Sie mit Experten, wenn Sie Zweifel haben
Zusammenfassend lässt sich sagen, dass es in der Tat eine herausfordernde Reise ist, sich in der komplizierten Landschaft der Hinterschneidungen beim Spritzgießen zurechtzufinden. Allerdings mit der richtigen Expertise und den richtigen Ressourcen, wie sie unter angeboten werden Kompetente BearbeitungWas wie eine Herausforderung erscheint, kann sich mühelos in einen strategischen Vorteil verwandeln. Unser Expertenteam ist bestrebt, maßgeschneiderte Lösungen bereitzustellen, die nicht nur Hinterschneidungen effektiv beheben, sondern den gesamten Spritzgussprozess verbessern. Entdecken Sie, wie wir Herausforderungen in Chancen verwandeln und den Weg für eine reibungslose Produktion und außergewöhnliche Ergebnisse ebnen. Kontaktieren Sie uns noch heute und lassen Sie uns gemeinsam diese Reise der Transformation antreten.