Toleranzen spielen im Maschinenbau eine entscheidende Rolle, indem sie die zulässige Abweichung von vorgegebenen Maßen definieren. Sie sind wichtig, um die Verwendbarkeit des Endprodukts sicherzustellen, insbesondere wenn es Teil einer größeren Baugruppe ist.
Wenn in kritischen Bereichen keine angemessenen Toleranzen festgelegt werden, kann dies dazu führen, dass Teile nicht mit dem beabsichtigten Design übereinstimmen, da unterschiedliche Herstellungsmethoden naturgemäß ein gewisses Maß an Ungenauigkeit mit sich bringen.
Andererseits ermöglicht die Festlegung geeigneter Toleranzen produzierenden Unternehmen, sich stärker auf bestimmte Aspekte des Produktionsprozesses zu konzentrieren. Diese Liebe zum Detail kann den Unterschied zwischen perfekt passenden Bauteilen und dem Ergebnis unbrauchbarer Altmetalle ausmachen.
Was ist Toleranz im Ingenieurwesen?
Die technische Toleranz bezieht sich auf den akzeptablen Abweichungsbereich von Messungen, die aus einer Basismessung abgeleitet werden. Toleranzen können auf verschiedene Einheiten angewendet werden, wie z. B. Temperatur (°C), Luftfeuchtigkeit (g/m3) oder, im Fall des Maschinenbaus, Längen-, Winkel- und andere physikalische Maße.
Unabhängig von der Einheit legt eine Toleranz einen zulässigen Messbereich um den Nennwert bzw. Basispunkt fest. Um dies zu veranschaulichen, betrachten Sie die Konstruktion eines Siebes, das zum Trennen von 3.5-mm-Kieselsteinen von 2.5-mm-Kieselsteinen verwendet wird. Ziel ist es, die kleineren Kieselsteine durch das Sieb passieren zu lassen, während die größeren zurückgehalten werden.
Die größeren Gesteine haben eine Größe zwischen 3.3 mm und 3.7 mm, während die kleineren im Bereich von 2.3 mm bis 2.7 mm liegen. Um sicherzustellen, dass nur die kleineren Kieselsteine durch die Löcher gelangen, während die größeren auf dem Sieb bleiben, kann für den Lochdurchmesser ein Nennwert von 2.8 mm eingestellt werden. Aufgrund der Fertigungspräzision können einige Löcher jedoch einen Durchmesser von 2.6 mm haben.
Durch die Festlegung einer Untergrenze von -0 mm und einer Obergrenze von +0.3 mm kann gewährleistet werden, dass alle Löcher einen Durchmesser von 2.8 mm bis 3.1 mm haben. Dadurch wird sichergestellt, dass das Sieb ordnungsgemäß funktioniert und die gewünschten Kieselsteine effektiv trennt, während die größeren zurückgehalten werden. Der Bereich 2.8~3.1 mm wird hier als Toleranzzone oder Toleranzbereich bezeichnet.
Arten der Toleranz
Hier sind die Arten von Toleranzen aufgeführt, die im Ingenieurwesen häufig anzutreffen sind:
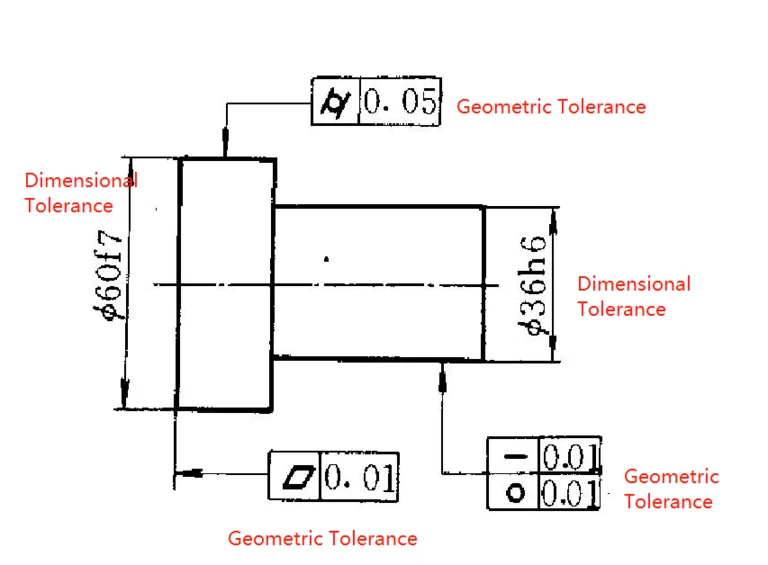
Maßtoleranz
Unter Maßtoleranz versteht man die zulässige Abweichung in der Größe oder den Abmessungen eines Bauteils. Dadurch wird sichergestellt, dass die Komponente den gewünschten Spezifikationen entspricht und funktioniert. Diese Art von Toleranz wird normalerweise anhand linearer Maße wie Länge, Breite, Höhe, Durchmesser oder Dicke angegeben.
Geometrische Toleranz
Geometrische Toleranz Steuert die Form, Ausrichtung und Position von Features auf einer Komponente. Es ermöglicht Variationen in Form, Winkel und Position und stellt gleichzeitig sicher, dass die funktionalen Anforderungen der Komponente erfüllt werden. Geometrische Toleranzen umfassen verschiedene Untertypen:
A. Formtoleranz
Die Formtoleranz gibt die akzeptable Abweichung in der Gesamtform eines Merkmals an, z. B. Geradheit, Ebenheit, Kreisförmigkeit oder Zylindrizität.
B. Orientierungstoleranz
Die Ausrichtungstoleranz regelt die zulässige Variation der Winkel, Neigungen oder Ausrichtungen von Features. Beispiele hierfür sind Rechtwinkligkeit, Parallelität, Winkligkeit und Konizität.
C. Positionstoleranz
Die Positionstoleranz steuert die Abweichung der Position eines Features von seiner gewünschten Position. Dabei werden sowohl die Lage als auch die Größe der Toleranzzone berücksichtigt, um den akzeptablen Abweichungsbereich zu bestimmen.
D. Profiltoleranz
Die Profiltoleranz definiert die zulässige Variation der Kontur oder des Oberflächenprofils eines Merkmals. Es stellt sicher, dass die Querschnittsform oder Oberfläche des Features den spezifizierten Anforderungen entspricht.
Toleranz der Oberflächenstruktur
Die Oberflächentexturtoleranz bezieht sich auf die akzeptable Variation der Textur, Rauheit oder Beschaffenheit einer Oberfläche. Dabei werden Faktoren wie Oberflächenrauheit, Welligkeit und Lage berücksichtigt, die sich auf die funktionalen oder ästhetischen Eigenschaften des Bauteils auswirken.
Materialeigenschaftstoleranz
Unter Materialeigenschaftstoleranz versteht man die akzeptable Variation der physikalischen oder mechanischen Eigenschaften von Materialien, die in technischen Konstruktionen verwendet werden. Dazu können Toleranzen für Eigenschaften wie Zugfestigkeit, Härte, Elastizität, Leitfähigkeit oder Wärmeausdehnung gehören.
Montagetoleranz
Die Montagetoleranz gibt die zulässige Variation der Passung, Ausrichtung oder Passung von Komponenten während des Montageprozesses an. Es stellt sicher, dass Teile korrekt zusammengebaut werden können und wie vorgesehen zusammenarbeiten.
Überlegungen beim Festlegen von Toleranzen
Toleranzen kosten Geld, keine Toleranz kostet Leistungen. Der Trick besteht darin, die goldene Mitte zu finden. Hier ist ein Beispiel. Als ich einen RC-Helikopter entwarf, musste ich die Toleranz der Geradheit der Hauptwelle festlegen, die das Hauptblatt des Hubschraubers dreht. Wir haben zunächst einige Tests durchgeführt, um zu ermitteln, wie stark der Hubschrauber vibriert, wenn die Geradheit um 0.01 mm, 0.02 mm, 0.03 mm, 0.04 mm und 0.05 mm abweicht. Dann haben wir überlegt, wie die Welle hergestellt wird, und eine Schätzung der Ausfallrate vorgenommen, wenn wir einen Toleranzbereich von 0.01, 0.02, 0.03 usw. benötigen. Und schließlich entscheiden wir, dass die Toleranz 0.03 mm betragen sollte, wobei die Vibration in einem kontrollierbaren Bereich liegt und die Herstellung der Teile nicht allzu schwierig ist.
Die Bestimmung geeigneter Toleranzen in der Technik erfordert eine sorgfältige Abwägung ihrer Auswirkungen auf andere Faktoren und das Ergebnis eines Prozesses. Diese Entscheidung beruht häufig auf wissenschaftlichen Grundsätzen, technischem Fachwissen und Berufserfahrung. Experimentelle Untersuchungen wie die Versuchsplanung und formale technische Bewertungen sind wertvolle Instrumente zur Untersuchung der Auswirkungen von Toleranzen.
Klar definierte technische Toleranzen in einer Spezifikation garantieren jedoch nicht die Einhaltung dieser Toleranzen. Tatsächliche Produktionsprozesse und Systemabläufe beinhalten naturgemäß Schwankungen im Input und Output. Darüber hinaus unterliegen Messungen Fehlern und statistischen Unsicherheiten. In Fällen, in denen die Messungen einer Normalverteilung folgen, können die Ausläufer der Messwerte erheblich über plus und minus drei Standardabweichungen vom Prozessdurchschnitt hinausgehen. Es ist möglich, dass erhebliche Teile eines oder beider Enden die angegebenen Toleranzgrenzen überschreiten.
Die Verarbeitungsfähigkeit von Systemen, Materialien und Produkten muss den vorgegebenen technischen Toleranzen entsprechen. Es sollten Prozesskontrollen implementiert und ein wirksames Qualitätsmanagementsystem (z. B. Total Quality Management) vorhanden sein, um sicherzustellen, dass die tatsächliche Produktion innerhalb der gewünschten Toleranzen bleibt. Ein Prozessfähigkeitsindex wird üblicherweise verwendet, um die Beziehung zwischen Toleranzen und der tatsächlich gemessenen Produktion anzugeben.
Die Auswahl der Toleranzen wird auch vom geplanten statistischen Stichprobenplan und seinen Merkmalen, einschließlich des akzeptablen Qualitätsniveaus, beeinflusst. Bei dieser Überlegung geht es darum, ob die Toleranzen äußerst streng sein müssen (um ein hohes Vertrauen in eine 100-prozentige Konformität zu gewährleisten) oder ob in bestimmten Fällen ein kleiner Prozentsatz der Abweichung von der Toleranz akzeptabel sein kann.
Toleranzen festlegen
Die Festlegung von Toleranzen in der Technik erfordert die sorgfältige Berücksichtigung verschiedener Faktoren und Überlegungen. Hier sind einige wichtige Schritte und Überlegungen bei der Festlegung von Toleranzen:
Design-Anforderungen
Beginnen Sie damit, die Designanforderungen und Funktionsspezifikationen der Komponente oder des Systems zu verstehen. Identifizieren Sie kritische Abmessungen, Funktionen und Leistungskriterien, die erfüllt werden müssen.
Technische Standards und Codes
Konsultieren Sie relevante technische Standards, Codes und Vorschriften, die für die Branche oder Anwendung spezifisch sind. Diese Normen enthalten Richtlinien und empfohlene Toleranzen für verschiedene Komponenten und Materialien.
Herstellungsprozess
Berücksichtigen Sie die Herstellungsprozesse, die zur Herstellung der Komponente oder des Systems verwendet werden. Unterschiedliche Fertigungsmethoden weisen inhärente Einschränkungen und Variationen auf, die sich auf die erreichbaren Toleranzen auswirken können. Verstehen Sie die Möglichkeiten und Grenzen der gewählten Herstellungsprozesse.
Design für Herstellbarkeit
Entwerfen Sie die Komponente unter Berücksichtigung der Herstellbarkeit. Optimieren Sie das Design, um eine einfachere und genauere Fertigung zu ermöglichen und die Notwendigkeit enger Toleranzen zu reduzieren. Die Zusammenarbeit zwischen Konstrukteuren und Fertigungsexperten kann dabei helfen, Bereiche zu identifizieren, in denen Toleranzen gelockert oder Merkmale für eine verbesserte Herstellbarkeit geändert werden können.
Statistische Analyse
Führen Sie statistische Analysen durch, um die mit dem Herstellungsprozess verbundene Variabilität und die möglichen Auswirkungen auf die Leistung der Komponente zu verstehen. Diese Analyse hilft dabei, den akzeptablen Toleranzbereich zu bestimmen, um die inhärente Variabilität zu berücksichtigen und sicherzustellen, dass die Komponente die gewünschten Leistungskriterien erfüllt.
Toleranzstapelanalyse
Führen Sie eine Toleranzstapelanalyse durch, um die kumulativen Auswirkungen von Toleranzen auf die Endbaugruppe zu bewerten. Diese Analyse hilft dabei, potenzielle Quellen für Störungen, Fehlausrichtungen oder Funktionsprobleme zu identifizieren, die sich aus den kombinierten Variationen einzelner Komponenten ergeben.
Toleranzzuordnung
Weisen Sie einzelnen Abmessungen und Merkmalen Toleranzen zu, basierend auf ihrer Bedeutung für die Funktionalität und Leistung der Komponente. Berücksichtigen Sie die Wechselbeziehungen zwischen Abmessungen und Merkmalen, um sicherzustellen, dass das Gesamtdesign innerhalb der gewünschten Spezifikationen bleibt.
Designverifizierung und Prototyping
Validieren Sie das Design und die Toleranzen durch Prototyping, Tests und Analysen. Dieser Schritt hilft dabei, potenzielle Probleme oder Abweichungen von der beabsichtigten Leistung zu erkennen und notwendige Anpassungen vorzunehmen.
Dokumentation und Kommunikation
Dokumentieren Sie die festgelegten Toleranzen eindeutig in technischen Zeichnungen, Spezifikationen und Fertigungsdokumentationen. Sorgen Sie für eine wirksame Kommunikation der Toleranzanforderungen an alle an den Herstellungs- und Montageprozessen beteiligten Beteiligten.
FORTLAUFENDE VERBESSERUNGEN
Bewerten und verbessern Sie regelmäßig Toleranzspezifikationen basierend auf dem Feedback aus der Fertigung, der Qualitätskontrolle und dem Kundenfeedback. Verfolgen Sie eine Einstellung zur kontinuierlichen Verbesserung, um Toleranzen im Laufe der Zeit zu optimieren und so die Produktleistung, Kosteneffizienz und Kundenzufriedenheit zu verbessern.
Toleranzmanagement und -kontrolle
Toleranzmanagement und -kontrolle beziehen sich auf den Prozess der Verwaltung und Kontrolle der akzeptablen Variation in den Abmessungen, Eigenschaften oder der Leistung eines Produkts oder Prozesses. Toleranz ist die zulässige Abweichung oder Variation einer physikalischen Abmessung oder Eigenschaft eines Produkts oder Prozesses. Es stellt sicher, dass das Produkt oder der Prozess die erforderlichen Spezifikationen erfüllt und ordnungsgemäß funktioniert.
Beim Toleranzmanagement geht es darum, die zulässigen Grenzen für verschiedene Abmessungen, Merkmale oder Parameter eines Produkts oder Prozesses zu bestimmen. Diese Grenzwerte werden typischerweise in technischen Zeichnungen, Spezifikationen oder Standards definiert. Ziel ist es, ein Gleichgewicht zwischen der gewünschten Funktionalität, der Machbarkeit der Herstellung und Kostenaspekten zu finden.
Hier sind einige Schlüsselaspekte des Toleranzmanagements und der Toleranzkontrolle:
Designtoleranz
Während der Entwurfsphase legen Ingenieure die Toleranzen für einzelne Abmessungen, geometrische Merkmale und Leistungsmerkmale des Produkts fest. Sie berücksichtigen Faktoren wie funktionale Anforderungen, Fertigungskapazitäten und Kostenauswirkungen.
Statistische Analyse
Zur Analyse und Festlegung von Toleranzen werden häufig statistische Methoden eingesetzt. Techniken wie statistische Prozesskontrolle (SPC), Prozessfähigkeitsanalyse und Versuchsplanung (DOE) können dabei helfen, die geeigneten Toleranzen auf der Grundlage des gewünschten Qualitätsniveaus und der Prozessfähigkeit zu bestimmen.
Herstellungsprozess
Das Toleranzmanagement erfordert die Berücksichtigung der Möglichkeiten und Grenzen der beteiligten Fertigungsprozesse. Verschiedene Herstellungsprozesse weisen unterschiedliche Präzisionsgrade auf und die Toleranzen müssen entsprechend eingestellt werden, um eine konsistente und zuverlässige Produktion zu gewährleisten.
Inspektion und Qualitätskontrolle
Die Toleranzkontrolle umfasst die Inspektion und Verifizierung des hergestellten Produkts, um sicherzustellen, dass es innerhalb der festgelegten Toleranzen liegt. Dies kann den Einsatz verschiedener Messtechniken wie Koordinatenmessgeräte (KMG), Messgeräte oder visuelle Inspektionen umfassen, um kritische Abmessungen oder Merkmale zu überprüfen.
Kostenüberlegungen
Das Toleranzmanagement berücksichtigt auch Kostenimplikationen. Engere Toleranzen können aufgrund erhöhter Präzisionsanforderungen, strengerer Prozesskontrollen und höherem Prüfaufwand zu höheren Herstellungskosten führen. Es ist wichtig, das gewünschte Qualitätsniveau mit den Kostenbeschränkungen in Einklang zu bringen.
Iterative Verbesserung
Toleranzmanagement ist ein iterativer Prozess. Rückmeldungen aus Fertigung, Inspektion und Kundenfeedback werden genutzt, um die Toleranzen kontinuierlich zu verfeinern und zu verbessern. Dabei geht es darum, die Leistung des Produkts unter realen Bedingungen zu bewerten und die notwendigen Anpassungen vorzunehmen, um die Kundenzufriedenheit sicherzustellen.
Schlussfolgerung
In Kompetente Bearbeitung Zusammenfassend lässt sich sagen, dass technische Toleranzen eine entscheidende Rolle bei der Gewährleistung der Funktionalität, Leistung und Herstellbarkeit von Komponenten und Systemen spielen. Toleranzen definieren die akzeptablen Abweichungen in Abmessungen, Form, Ausrichtung und anderen kritischen Parametern eines Designs. Durch die effektive Festlegung und Verwaltung von Toleranzen können Ingenieure das gewünschte Gleichgewicht zwischen Designanforderungen, Fertigungsdurchführbarkeit und Kostenoptimierung erreichen.
Letztendlich ist die technische Toleranz ein entscheidender Aspekt des technischen Designs und ermöglicht die Realisierung zuverlässiger, funktionaler und qualitativ hochwertiger Produkte. Indem Ingenieure die Bedeutung von Toleranz verstehen und etablierte Best Practices befolgen, können sie die Komplexität der Toleranz erfolgreich bewältigen und zur Weiterentwicklung technischer Innovationen beitragen.