Was ist Wasserstrahlschneiden?
Wasserstrahlschneiden ist ein Materialschneideprozess, bei dem ein Hochdruckwasserstrahl oder eine Kombination aus Wasser und Schleifmaterial zum Schneiden verschiedener Materialien verwendet wird. Bei diesem Verfahren wird Wasser auf eine hohe Geschwindigkeit beschleunigt und dann auf das Werkstück gerichtet, um einen präzisen, sauberen Schnitt zu erzeugen.
Das Schneiden ist eine vielseitige Schneidmethode, die für eine Vielzahl von Materialien eingesetzt werden kann, darunter Metalle, Kunststoffe, Verbundwerkstoffe, Steine, Keramik und sogar Lebensmittel. Es ist eine beliebte Alternative zu herkömmlichen Schneidmethoden, da es umweltfreundlich ist, nur wenig Abfall produziert und keine Wärmeeinflusszonen (HAZ) entstehen, die die Eigenschaften des zu schneidenden Materials verändern können.
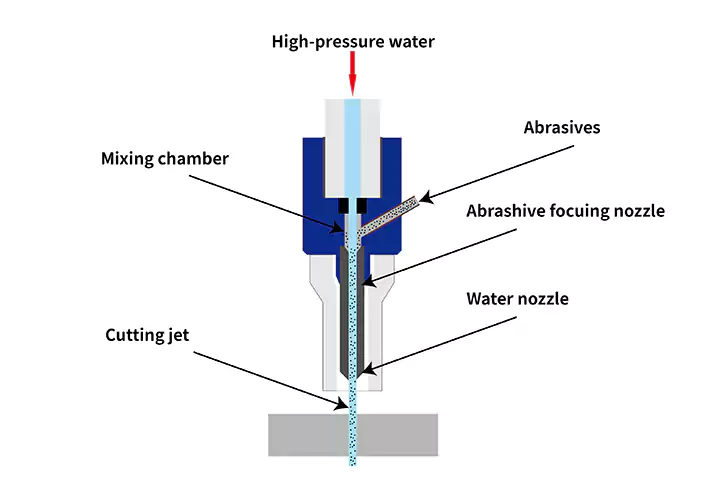
Kurze Geschichte und Entwicklung
Das Wasserstrahlschneiden hat seine Wurzeln im hydraulischen Bergbau, der im 1800. Jahrhundert dazu genutzt wurde, mithilfe von Hochdruckwasserstrahlen Mineralien aus dem Boden zu gewinnen. In den 1930er Jahren wurde das Konzept des Wasserstrahlschneidens für industrielle Anwendungen weiterentwickelt und in den 1950er Jahren wurde die erste kommerzielle Wasserstrahlschneidanlage eingeführt.
Die frühen Schneidsysteme waren in ihren Fähigkeiten begrenzt und wurden hauptsächlich zum Schneiden weicher Materialien wie Papier und Textilien verwendet. Mit der Entwicklung leistungsstärkerer Pumpen und fortschrittlicherer Schneidköpfe wurde das Wasserstrahlschneiden jedoch auch zum Schneiden härterer Materialien wie Metall, Stein und Glas geeignet.
In den 1970er Jahren wurde das abrasive Wasserstrahlschneiden eingeführt, bei dem abrasive Materialien wie Granat mit Wasser gemischt wurden, um die Schneidleistung zu erhöhen. Dies ermöglichte den Einsatz des Wasserstrahlschneidens für noch härtere Materialien und die Wasserstrahltechnologie hat sich seitdem kontinuierlich weiterentwickelt und verbessert.
Heutzutage wird das Schneiden in einer Vielzahl von Branchen eingesetzt, von der Luft- und Raumfahrt über die Automobilindustrie bis hin zur Lebensmittelindustrie, Verarbeitung und Kunst. Es ist zu einer beliebten Alternative zu herkömmlichen Schneidmethoden geworden, wie z Laserschneiden und Plasmaschneiden, aufgrund seiner Vielseitigkeit, Präzision und Umweltfreundlichkeit.
Arbeitsgrundsätze
Dies kann durch verschiedene Methoden erreicht werden, die meisten beinhalten jedoch das Mischen von Schleifmaterial mit Wasser, um Partikel vom Werkstück zu entfernen. Mit diesem äußerst vielseitigen Herstellungsverfahren kann ein Werkstück nach präzisen Spezifikationen geschnitten, geformt und gestaltet werden.
Im Vergleich zu anderen Schneidverfahren wie Plasma- oder Laserschneiden hat das Wasserstrahlschneiden mehrere Vorteile. Es bietet eine höhere Genauigkeit, kann komplexe Designs verarbeiten und thermisch empfindliche Materialien schneiden, ohne deren Eigenschaften zu verändern. Das Schleifmaterial wirkt wie Schleifpapier und erodiert das Werkstück, ohne Hitze zu erzeugen oder seine Härte zu beeinflussen. Die resultierenden Schnittkanten sind sauber und erfordern keine weitere Bearbeitung vor dem Schweißen.
Der Wasserstrahlschneidprozess
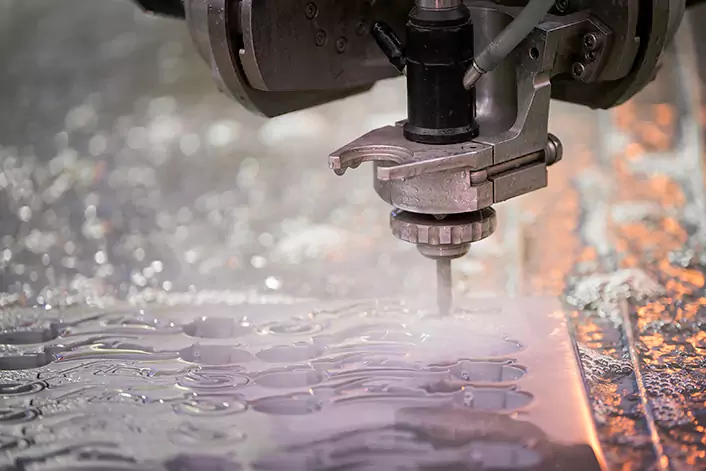
Schnittfugenbreite messen
Die Breite der Schnittfuge bezieht sich auf die Materialmenge, die während des Schneidvorgangs entfernt wird, und wurde ursprünglich verwendet, um die Breite des von einem Sägeblatt entfernten Materials zu beschreiben. Beim Wasserstrahlschneiden bezieht sich die Schnittfuge auf die Breite des Wasserstrahls, die typischerweise 0.04 Zoll oder weniger beträgt und Innenecken mit einem Radius erzeugt, der der Strahlbreite entspricht. Mehrere Faktoren beeinflussen die Größe der Schnittfuge, wie etwa die Materialstärke, die Art, die Schnittqualität und die Düsenkonfiguration.
Designer müssen die Schnittfugengröße berücksichtigen, wenn sie die endgültigen Produktabmessungen bestimmen. Wenn die Schnittfugenbreite beispielsweise 0.042 Zoll beträgt, müssen die endgültigen Produktabmessungen entsprechend angepasst werden, um die Schnittbreite zu berücksichtigen; Andernfalls weicht das Endprodukt um 0.042 Zoll ab.
Abhängig von der Materialstärke, seiner Härte und den Merkmalen des Wasserstrahlschneidkopfs kann einer der drei Kegel geformt werden: V-förmiger Kegel, umgekehrter Kegel oder Tonnenkegel. Der Gewindeschneider muss bei der Planung berücksichtigt werden. Und der Bediener des Schneidprozesses muss die Parameter der Wasserstrahlschneidmaschine anpassen, um den Kegelwinkel zu minimieren.
Erstes Wasserstrahl-Piercing
Der erste Schnitt, der mit einem Wasserstrahlschneider erzeugt wird, wird als Loch bezeichnet und hat im Vergleich zur normalen Schnittfuge eine größere Breite. Das Lochen markiert den Beginn des Wasserstrahlschneidprozesses und kann mit verschiedenen Techniken durchgeführt werden, darunter stationäre, lineare, kreisförmige und Niederdruckmethoden. Die gewählte Einstechtechnik hängt vom jeweiligen zu schneidenden Material und der Menge des anfallenden Schrotts ab.
Verjüngende Schnittfugenbreite
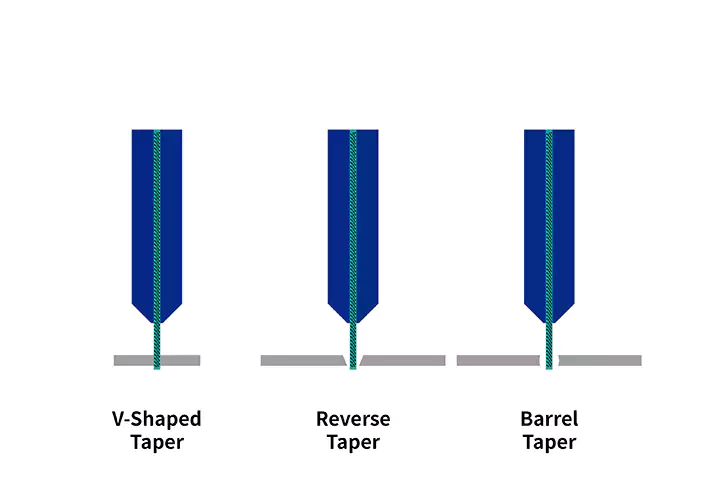
Dieser Schnitt erzeugt eine V-förmige Verjüngung, die den Unterschied in der Schnittfugenbreite am oberen und unteren Rand des Schnitts darstellt. Diese Verjüngung entsteht, weil der Wasserstrahl etwas Energie verliert, wenn er tiefer in das Material eindringt, was dazu führt, dass oben mehr Material entfernt wird als unten.
Beim Schneiden von weichen und biegsamen Materialien kann es bei langsamen Schnittgeschwindigkeiten zu einer umgekehrten Verjüngung kommen, bei der die Schnittfuge aufgrund des erhöhten Materialabtrags unten breiter ist.
Darüber hinaus können sich bei extrem dicken Materialien Fassverjüngungen bilden, bei denen der Schnitt in der Mitte am breitesten ist.
Während die Verjüngung bei den meisten Schneidarbeiten kein Problem darstellt, kann sie bei Präzisionswerkzeugen, bei denen die geschnittenen Teile genau zusammenpassen müssen, zu Problemen führen. In solchen Fällen muss die Verjüngung in Betracht gezogen und gesteuert werden, um präzise Schnitte zu gewährleisten.
Unter Druck setzen
Um Wasser zum Schneiden unter Druck zu setzen, werden verschiedene Methoden eingesetzt, darunter lineare Verstärker und rotierende Direktantriebspumpen. Beide Pumpentypen bestehen aus einem Motor, Wasserfiltern, Steuerungssystemen und Sensoren.
Lineare Verstärkerpumpen verwenden Hydrauliköl unter Druckbedingungen von etwa 3000 psi. Das Niederdrucköl wirkt auf einen Kolben, dessen Stirnfläche 20-mal größer ist als die des Hochdruckkolbens, der gegen das Wasser drückt. Aufgrund des Größenunterschieds zwischen Nieder- und Hochdruckpumpe wird der Druck auf den größeren Kolben um das Zwanzigfache verstärkt, was zu einem Druck von 20 psi führt.
Im Gegensatz zur linearen Verstärkerpumpe, die Hydrauliköl verwendet, kommt die Rotationspumpe mit Direktantrieb ohne Hydrauliköl aus. Es besteht aus einem Elektromotor, der eine Kurbel antreibt, die die Kolben antreibt, die den Wasserdruck erzeugen. Direktantriebspumpen sind mit 30-PS-Motoren ausgestattet und verfügen über einen Einlass, der die Pumpe mit Wasser versorgt.
Hochdruckschläuche
Nach Verlassen der Pumpe wird das unter Druck stehende Wasser über Hochdruckschläuche zum Schneidkopf transportiert. Dieser Schlauch ist äußerst langlebig und zeichnet sich durch eine außergewöhnliche Streckgrenze und Zugfestigkeit sowie eine glatte Innenoberfläche aus. Er besteht typischerweise aus kaltverformtem Edelstahl oder thermoplastischem Druckschlauch und ist in Größen von 0.25 Zoll bis 0.563 Zoll und in verschiedenen Längen erhältlich, um verschiedenen Wasserstrahlschneiderdesigns gerecht zu werden.
Schneidkopf
Während das unter Druck stehende Wasser durch den Schneidkopf strömt, passiert es eine Öffnung aus Diamant, Rubin oder Saphir, deren Loch kleiner als die Spitze einer Stecknadel ist. Die Geschwindigkeit des Wassers steigt schnell auf über 90,000 psi oder 2500 Meilen pro Stunde, wenn es durch die Öffnung fließt. Die Leistung des Schneidkopfes wirkt sich direkt auf den Schneidprozess aus und ein Präzisionswerkzeug-Schneidkopf kann bei korrekter Verwendung zwischen 500 und 1000 Stunden halten.
Es gibt zwei Haupttypen: reines Wasserstrahlschneiden und abrasives Wasserstrahlschneiden.
Reines Wasserstrahlschneiden
Beim reinen Wasserstrahlschneiden wird ausschließlich Wasser verwendet, das unter Druck steht und auf das zu schneidende Material gerichtet wird. Diese Methode eignet sich zum Schneiden weicher Materialien wie Gummi, Schaumstoff und Papier. Reine Wasserstrahlschneider sind die älteste Art von Wasserstrahlschneidwerkzeugen. Sie werden bevorzugt, da sie nur minimale Feuchtigkeit auf der Oberfläche des Werkstücks erzeugen und so das Risiko von Verformungen verringern. Diese Fräser erzeugen einen schmalen Strahl, der präzise Schnitte mit minimalem Materialverlust ermöglicht. Der Schneidkopf eines reinen Wasserstrahlschneiders enthält normalerweise einen Edelstein, Rubine sind jedoch nicht für die Verwendung mit reinem Wasser geeignet. Der Strom bewegt sich mit einer Geschwindigkeit von Mach 2 für 40,000 psi und Mach 3 für 60,000 psi.
Abrasives Wasserstrahlschneiden
Beim Abrasiv-Wasserstrahlschneiden wird abrasives Material, typischerweise Granat, mit Hochdruckwasser gemischt, um die Schneidleistung zu erhöhen. Diese Methode eignet sich zum Schneiden härterer Materialien wie Metalle, Stein, Glas und Keramik.
Ein abrasives Material wird in den Schneidkopf eines abrasiven Wasserstrahlschneidsystems eingeführt, wo es ordnungsgemäß mit dem Wasserstrom vermischt wird. Durch die Zugabe eines Schleifmittels wird der Strahl geschärft und die Schneidwirkung erhöht. Dadurch kann ein abrasiver Wasserstrahlschneider jedes Material schneiden, unabhängig von seiner Dicke oder Härte.
Anwendungen
Es verfügt über ein breites Anwendungsspektrum in verschiedenen Branchen. Einige häufige Anwendungen sind:
Luft- und Raumfahrt
Es wird zum Schneiden von Materialien wie Titan und Verbundwerkstoffen für Luft- und Raumfahrtkomponenten wie Triebwerksteile und Flugzeuginnenräume verwendet.
Automobil
Es wird zum Schneiden von Metall- und Kunststoffteilen für Pkw und Lkw verwendet.
Architektur
Das Schneiden wird verwendet, um komplizierte Designs und Muster auf Gebäudefassaden und Inneneinrichtungen wie Böden, Wänden und Arbeitsplatten zu erstellen.
Lebensmittelverarbeitung
Dieses Schneiden wird zum Schneiden von Lebensmitteln wie Obst, Gemüse und Fleisch sowie zur Verarbeitung von Materialien wie Käse und Schokolade verwendet.
Medical
Es wird zum Schneiden medizinischer Geräte und Instrumente sowie zur Herstellung von Implantaten und Prothesen verwendet.
Kunst und Skulptur
Dieser Zuschnitt wird zur Herstellung komplizierter Designs und Formen aus Metall, Stein und Glas für künstlerische Zwecke verwendet.
Fertigung
Es wird zum Schneiden einer Vielzahl von Materialien für verschiedene Fertigungsanwendungen verwendet, darunter Dichtungen, Dichtungen und Maschinenteile.
Vorteile
Es bietet mehrere Vorteile gegenüber anderen Schneidmethoden. Zu den wichtigsten Vorteilen gehören:
Vielseitigkeit
Wasserstrahlschneiden kann eine Vielzahl von Materialien schneiden, darunter Metalle, Kunststoffe, Keramik, Verbundwerkstoffe und mehr. Es kann auch komplizierte Formen und Muster präzise schneiden.
Keine Wärmeeinflusszone
Während des Schneidvorgangs entsteht keine Wärme, was bedeutet, dass es im zu schneidenden Material keine Wärmeeinflusszone (HAZ) gibt. Dadurch eignet es sich ideal zum Schneiden hitzeempfindlicher Materialien wie Metalle und Kunststoffe.
Minimaler Materialverlust
Durch das Wasserstrahlschneiden entsteht eine schmale Schnittfuge, sodass beim Schneidvorgang nur minimaler Materialverlust entsteht. Insbesondere beim Schneiden teurer Materialien können dadurch Kosten eingespart werden.
Umweltfreundlichkeit
Beim Wasserstrahlschneiden entstehen weder gefährliche Abfälle noch schädliche Dämpfe, was es zu einer umweltfreundlichen Schneidmethode macht.
Sicher
Es erzeugt weder Funken noch Hitze, was es zu einer sichereren Schneidmethode als andere wie Plasma- oder Laserschneiden macht.
Keine Nachbearbeitung erforderlich
Beim Wasserstrahlschneiden entstehen glatte und gratfreie Kanten, sodass nachträgliche Nachbearbeitungen wie Schleifen oder Polieren nicht erforderlich sind.
Einschränkungen des Wasserstrahlschneidens
Während das Wasserstrahlschneiden viele Vorteile hat, weist es auch einige Einschränkungen auf. Zu den wichtigsten Einschränkungen gehören:
Begrenzte Dicke
Das Wasserstrahlschneiden ist am effektivsten bei Materialien mit einer Dicke von bis zu 4–6 cm. Für dickere Materialien sind möglicherweise andere Schneidmethoden geeigneter.
Langsamere Schnittgeschwindigkeit
Dieses Schneiden ist im Allgemeinen langsamer als andere Schneidmethoden wie Plasma- oder Laserschneiden. Dies kann die Effizienz bei der Massenproduktion beeinträchtigen.
Anfängliche Investitionskosten
Wasserstrahlschneidemaschinen können teuer sein, was es für kleine Unternehmen oder Einzelpersonen schwierig machen kann, sie sich zu leisten.
Staub erzeugen
Beim Abrasivwasserstrahlschneiden können Staub und Ablagerungen aus dem Abrasivmaterial entstehen, die bei unsachgemäßer Kontrolle gefährlich sein können.
Hoher Wartungsaufwand
Wasserstrahlschneidmaschinen erfordern eine regelmäßige Wartung, einschließlich des Austauschs verschlissener Teile und der Überwachung der Wasserqualität.
Schlussfolgerung
Das Wasserstrahlschneiden ist ein äußerst vielseitiges und präzises Schneidverfahren, das gegenüber anderen Schneidverfahren mehrere Vorteile bietet. Es ist in der Lage, eine Vielzahl von Materialien präzise zu schneiden, erzeugt keine Wärmeeinflusszone und ist umweltfreundlich. Es wird in verschiedenen Branchen eingesetzt, darunter Luft- und Raumfahrt, Automobil, Architektur, Lebensmittelverarbeitung, Medizin, Kunst und Fertigung.
Allerdings weist das Wasserstrahlschneiden einige Einschränkungen auf, wie z. B. eine begrenzte Dicke, eine langsamere Schnittgeschwindigkeit und einen hohen Wartungsaufwand. Trotz dieser Einschränkungen bleibt das Wasserstrahlschneiden eine beliebte und effektive Schneidmethode für eine Vielzahl von Anwendungen.