Wählen Sie das richtige Material
Die Wahl des richtigen Kunststoffmaterials für Spritzgussteile kann schwierig sein. Zu den Faktoren, die in den meisten Fällen berücksichtigt werden müssen, gehören die Härte, Festigkeit, Dichte, Schrumpfung, der Schmelzpunkt und die Kosten des Materials. Abhängig vom Verwendungsszenario kann es auch erforderlich sein, die UV-Beständigkeit, chemische Beständigkeit, elektrische Leitfähigkeit, Wärmeisolierung, Selbstschmierung, Schlagfestigkeit, Biokompatibilität, Transparenz usw. des Materials zu berücksichtigen. Nachfolgend finden Sie eine Rangliste der allgemeinen Eigenschaften einiger gängiger Materialien Kunststoffe.
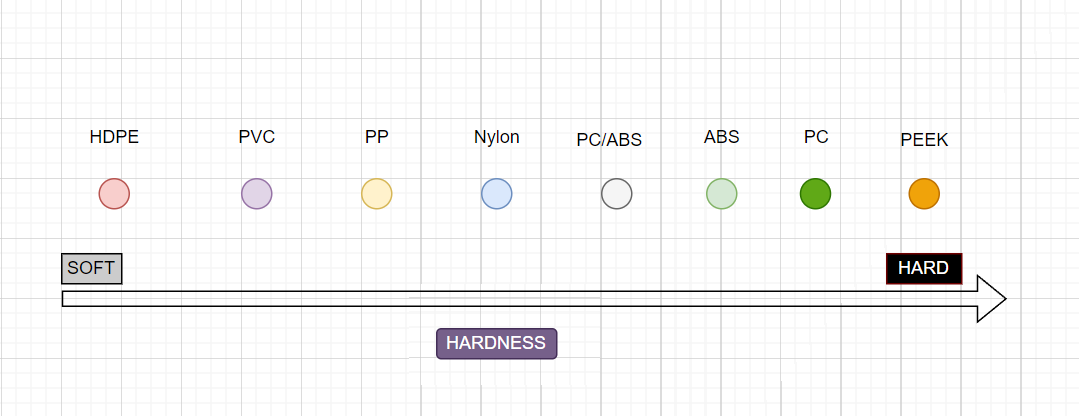
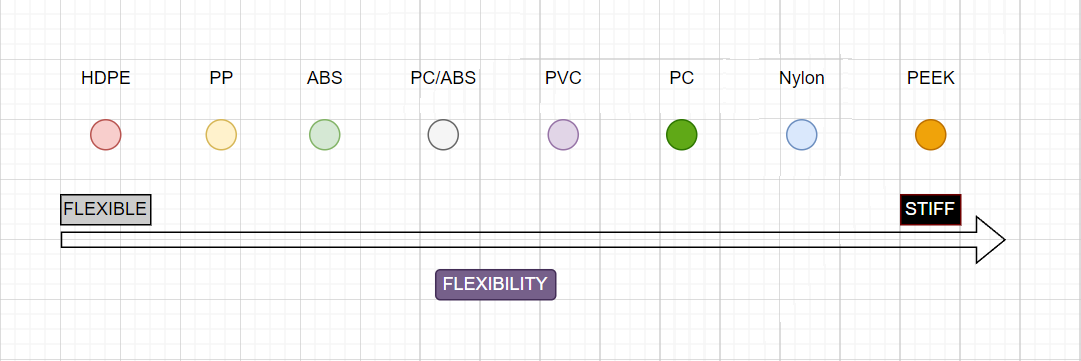
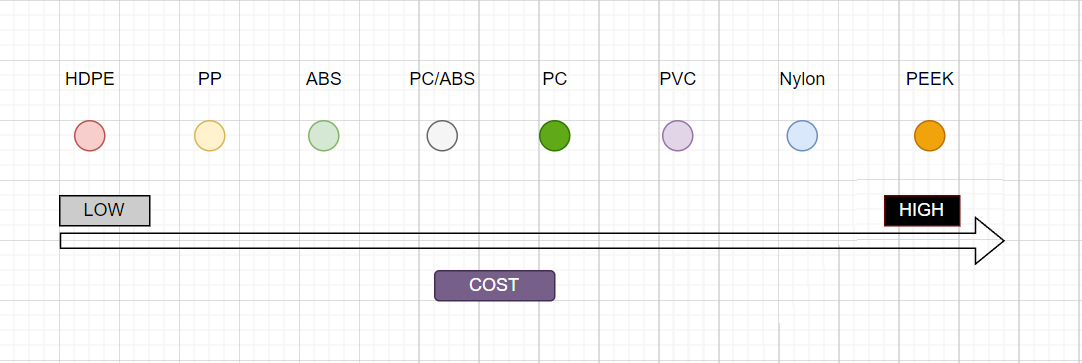
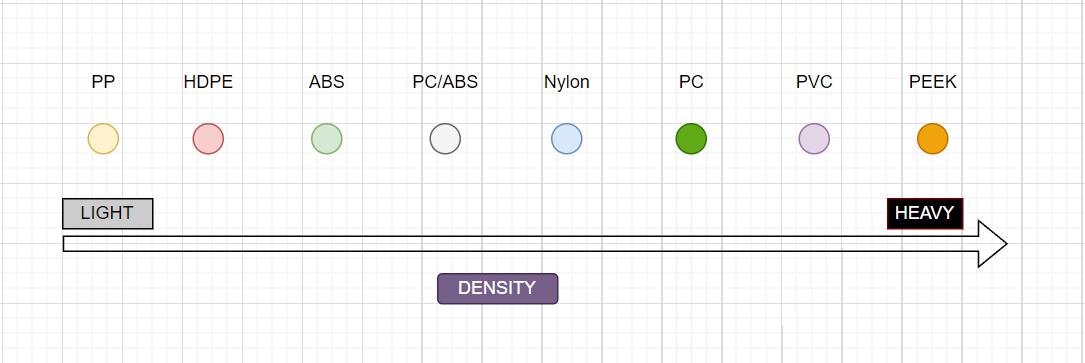
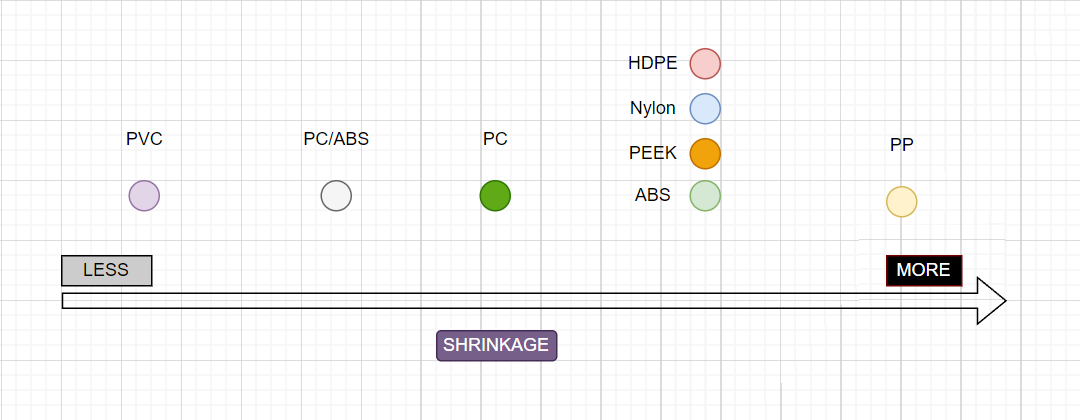
Wo finde ich die Informationen?
Umfassende Datenberichte zu Kunststoffen verschiedener Hersteller finden Sie unter www.ides.com.
https://www.makeitfrom.com/material-group/Thermoplastic bietet eine intuitive Benutzeroberfläche zum Erhalten allgemeiner Kunststoffeigenschaften.
Große Hersteller bieten auch PDF-Dateien mit Informationen zu ihren Kunststoffmaterialien an. Das Datenblatt zu den Kunststoffeigenschaften von Sabic finden Sie beispielsweise unter https://www.sabic.com/en/products/polymers.
Kunststoffzusätze und Füllstoffe
Kunststoff Additive und Füllstoffe, egal ob organische oder anorganische Verbindungen, werden in Kunststoffe eingearbeitet, um deren Eigenschaften zu verändern. Obwohl die meisten Kunststoffe von Natur aus langlebig und schlagfest sind, können sie Eigenschaften wie Sprödigkeit, Härte, Entflammbarkeit oder übermäßiges Gewicht aufweisen, die für den vorgesehenen Zweck ungeeignet sein können. Der Zusatz von Zusatzstoffen oder Füllstoffen ermöglicht die Umwandlung von Kunststoffen in ihre beabsichtigten Anwendungen unter Beibehaltung der attraktiven Eigenschaften, die ursprünglich die Aufmerksamkeit auf sich gezogen haben. Nahezu jede Art von Kunststoff enthält irgendeine Form von Zusatzstoffen, um seine Leistung für den vorgesehenen Verwendungszweck zu optimieren.
Die häufigsten Kunststoffzusätze/Füllstoffe sind wahrscheinlich Weichmacher, Glasfaser, Kohlefaser und Talkum.
Bei den meisten Weichmachern handelt es sich um Ester, die durch die Reaktion von Säuren mit Alkoholen entstehen, und die zugesetzte Menge hat Einfluss auf das Endprodukt. Vinylhandschuhe enthalten beispielsweise etwa 50 % Weichmacher, um ihre Flexibilität und ihren Tragekomfort zu gewährleisten.
Fiberglas wird verwendet, um die Kunststoffschrumpfung zu reduzieren und gleichzeitig die Festigkeit und Steifigkeit zu erhöhen. Es erhöht typischerweise auch die Dichte des Kunststoffs und macht ihn schwerer. Andererseits erhöht Kohlefaser die Festigkeit des Kunststoffs zusätzlich und ist deutlich leichter als Glasfaser.
Die Anwendungseigenschaften von Talkumpuder variieren je nach Kunststoffmaterial. Bei ABS und Nylon bietet der Zusatz von Talkumpuder nicht nur wirtschaftliche Vorteile, sondern auch Verbesserungen bei der Hitzebeständigkeit und Formschrumpfung. Bei Polyethylen erhöht die Zugabe von Talkumpuder vor allem die Steifigkeit und Hitzebeständigkeit, verringert die Formschrumpfung und senkt die Kosten. Talkumpuder findet die breiteste und bedeutendste Anwendung in Polypropylen, wo es die Gesamtfestigkeit und Hitzebeständigkeit verbessert, die Formschrumpfung verringert und die Steifigkeit erhöht. Darüber hinaus kann hochwertiges Talkumpuder in Polypropylen als Keimbildner wirken und so die Gesamtleistung von Polypropylen effektiv verbessern.
Im Kunststoffspritzgussbereich werden häufig zahlreiche weitere Kunststoffadditive eingesetzt. Einige Beispiele umfassen Schmierstoffe, Schlagverstärker, Flammschutzmittel, Antistatika und Antioxidantien. Es ist wichtig zu erkennen, dass viele Kunststoffeigenschaften durch diese Zusatzstoffe verändert werden können.
Typische Verwendungszwecke von Kunststoff
Viele Kunststoffe haben aufgrund besonders herausragender Eigenschaften typische Anwendungen. PTFE ist beispielsweise hochtemperatur- und chemikalienbeständig und wird daher zur Beschichtung von Küchenutensilien verwendet. PP lässt sich ständig falten und entfalten und für das Scharnier des Brillenetuis verwenden. ABS/PC verfügt über eine hohe Festigkeit und Schlagfestigkeit und wird in den Gehäusen verschiedener Elektrogeräte verwendet. Diese typischen Anwendungsszenarien können als wichtige Referenz bei der Materialauswahl herangezogen werden.
So wählen Sie das richtige Material für Spritzgussteile aus
Für Kunststoffmaterialien stehen etwa 85,000 bis 90,000 kommerzielle Optionen zur Verfügung. Dieses umfangreiche Spektrum lässt sich in etwa 45 Polymerfamilien oder -mischungen einteilen. Die Auswahl des am besten geeigneten Materials für ein bestimmtes Projekt kann einer Detektivarbeit ähneln. Um den Prozess zu vereinfachen, empfehlen wir einen 3-Schritte-Workflow.
Beginnen Sie zunächst damit, eine ähnliche typische Verwendung von Kunststoff zu identifizieren, beispielsweise im Fall von Zahnrädern, bei denen gängige Kunststoffe wie PEEK, POM und Nylon verwendet werden.
Vergleichen Sie anschließend die Eigenschaften dieser Kunststoffe und berücksichtigen Sie dabei möglicherweise weitere Faktoren wie Hochtemperaturbeständigkeit oder chemische Beständigkeit. Dies wird dazu beitragen, die Materialoptionen einzugrenzen.
Erwägen Sie abschließend die Verwendung geeigneter Zusatzstoffe oder Füllstoffe zur Verbesserung etwaiger Eigenschaften, die den Anforderungen möglicherweise nicht vollständig entsprechen.
Tolerieren Sie keine unnötigen Toleranzen
Im Allgemeinen kann beim Kunststoffspritzguss eine Toleranz von +/- 0.1 mm erreicht werden. Eine sehr enge Toleranz von +/- 0.025 mm ist hart, aber immer noch möglich. Zu den Faktoren, die sich auf die Endprodukttoleranz auswirken, gehören Schrumpfung, Verzug und Temperaturschwankungen.
Je höher die Schrumpfung, desto schwieriger ist es, enge Toleranzen einzuhalten. Beispielsweise beträgt die Schrumpfung von POM 1.5 bis 3 %, während PC/ABS eine Schrumpfung von 0.6 % aufweist. Es ist viel einfacher, bei einem PC/ABS-Teil eine enge Toleranz einzuhalten als bei einem POM-Teil. Der gebräuchlichste Weg, die Schrumpfung zu reduzieren, besteht darin, dem Kunststoff Glasfaser oder Kohlefaser beizufügen. Durch den Zusatz von 30 % Glasfaser im Nylon wird die Schrumpfung von 1.5 % auf weniger als 0.5 % reduziert.
Der Verzug wird durch innere Spannungen verursacht, die durch geeignete Konstruktionen reduziert werden können. Eine ordnungsgemäße Alterung nach der Injektion des Produkts kann ebenfalls hilfreich sein.
Im Raumtemperaturbereich liegt der lineare Wärmeausdehnungskoeffizient (CLTE) bei den meisten Thermoplasten zwischen etwa 0.6 x 10-4 und 2.3 x 10-4 K-1. Oder ein 50 mm langer Thermoplast mit einer Temperaturänderung von 20 Grad Celsius würde seine Größenänderung etwa 0.06 mm bis 0.23 mm betragen. Dies zeigt uns, dass es eine große Herausforderung sein kann, bei Temperaturänderungen enge Toleranzen einzuhalten. Wenn Sie jedoch Kunststoffe mit einer geringeren Wärmeausdehnungsrate wählen, kann dies dazu beitragen, engere Toleranzen zu erreichen und einzuhalten.
Wählen Sie die richtige Wandstärke und achten Sie auf Konsistenz.
Für die Wandstärke eines Spritzgussteils gibt es 2 Prinzipien. Halten Sie angemessene dünne Wandstärken ein und Halten Sie die Wandstärke so gleichmäßig wie möglich. Die Gründe sind wie folgt.
Dicke Wände sind nicht nötig: In den meisten Fällen sehr Dicke Wände sind nicht erforderlich. Das Verhältnis von Festigkeit zu Gewicht ist bei einem Hohlrohr besser als bei einem Vollstab. Das gleiche Prinzip gilt auch für andere Formen. Mit anderen Worten: Eine sehr dicke Wand kann jederzeit durch eine relativ hohle Struktur mit geringerer Wandstärke bei gleicher Festigkeit ersetzt werden.
Materialverbrauch: Dicke Wände bedeuten mehr Material und damit höhere Materialkosten und möglicherweise eine größere Spritzgießmaschine.
Zykluszeit: Dickere Wände brauchen während des Formprozesses länger zum Abkühlen, was zu längeren Zykluszeiten für jedes Teil führt. Dies kann die Produktion verlangsamen und die Kosten erhöhen.
Verzug: Dicke Wände sind beim Abkühlen und Erstarren anfälliger für Verformungen und Verformungen. Dies kann dazu führen, dass Teile nicht den erforderlichen Toleranzen oder Abmessungen entsprechen.
Einfallstellen: Da dicke Abschnitte anders schnell abkühlen und schrumpfen als dünnere Abschnitte, können sich auf der Oberfläche des Teils Einfallstellen oder Vertiefungen bilden, die das Aussehen und die Oberflächenbeschaffenheit beeinträchtigen. Weitere Informationen zur Entstehung von Einfallstellen finden Sie hier Dieser Artikel.
Einspritzdruck: Das Formen dicker Wände erfordert möglicherweise höhere Einspritzdrücke, was die Formausrüstung belasten und das Risiko von Defekten erhöhen kann.
Spannungskonzentration: Dicke Wände können Spannungskonzentrationspunkte im Teil erzeugen, die es anfälliger für Risse oder Brüche unter Belastung oder Stößen machen können.
Die optimale Wandstärke hängt von der Viskosität des Materials und der Struktur des Bauteils ab. Im Allgemeinen liegt die optimale Wandstärke für die meisten Thermoplaste zwischen 1 und 4 mm. Im Folgenden sind die empfohlenen Wandstärken für einige gängige Kunststoffmaterialien aufgeführt.
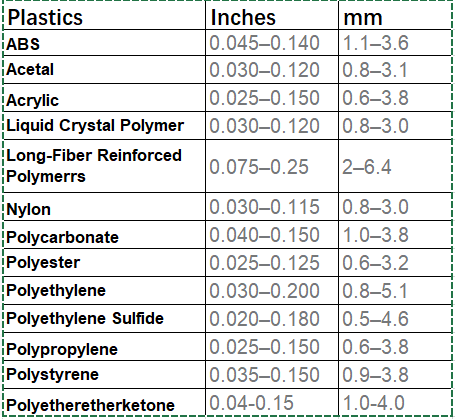
Auch eine zu dünne Wand ist problematisch: Bei einer gegebenen Wandstärke ist die Strecke, über die der geschmolzene Kunststoff fließen kann, begrenzt. Wenn die Wand zu dünn ist, sind sehr hoher Druck und hohe Temperaturen erforderlich und die Gesamtgröße des Teils ist begrenzt. Erfahrungsgemäß sollte normales Plastik keine Wandstärke haben, die dünner als 0.03 Zoll bzw. 0.75 mm ist.
Was ist, wenn wirklich eine dicke Wand benötigt wird?: Andere Kunststoffformverfahren eignen sich besser für die Herstellung von Teilen mit sehr dicken Wänden. Spritzgegossener Strukturschaum, gasunterstütztes Spritzgießen, Formpressen und Reaktionsspritzgießen sind allesamt Verfahren, die für ihre Wirksamkeit bei der Herstellung dickwandiger Teile bekannt sind.
Halten Sie eine gleichbleibende Wandstärke ein.
Ungleichmäßige Wandstärken können zu Verformungen führen, da sie unterschiedlich schnell abkühlen und sich zusammenziehen. Wenn Sie unterschiedliche Dicken benötigen, stellen Sie sicher, dass die Änderung 20 % der Standardwandstärke nicht überschreitet und sorgen Sie für einen glatten oder konischen Übergang. Dies führt zu einem qualitativ besseren Teil mit geringerem Risiko von Verformungen.
Wenn Sie noch Fragen zu Wandstärken haben, wenden Sie sich bitte an CapableMachining. Wir verfügen über erfahrene Ingenieure, die alle Ihre Fragen beantworten.
Beziehen Sie Formschrägen in Ihr Design ein.
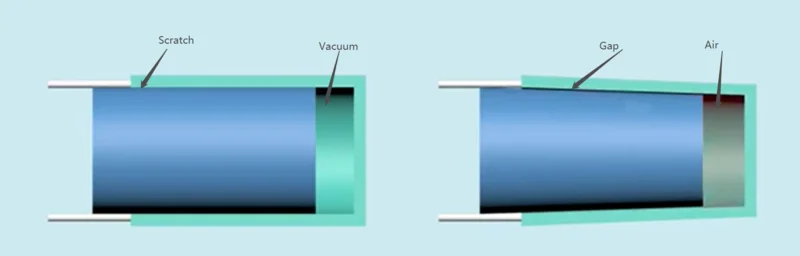
Der Entformungswinkel dient hauptsächlich dazu, zu verhindern, dass das Produkt aufgrund von Adhäsion oder Vakuumdruck während des Formöffnungsvorgangs nicht ausgeworfen werden kann. Gleichzeitig kann der Entformungswinkel auch Oberflächenkratzer reduzieren. In den meisten Fällen werden Entformungswinkel von 1 bis 2° angewendet. Höhere Schrumpfung und weichere Materialien erfordern einen etwas größeren Entformungswinkel. Es gibt noch ein paar weitere Feinheiten der Schrägenwinkel:
Anforderungen an vertikale Flächen: 0.5°~1°
Häufigste Situationen: 1 ~ 2°
Alle Absperrflächen: 3°
Flächen mit flachen Texturen: 1 ~ 2°
Gesichter mit tiefen Texturen: 5° oder mehr
Das Absperrflächenwinkel ist eine spezielle Formschräge. Es dient nicht der einfacheren Formtrennung, sondern der Verlängerung der Formlebenszyklen. Die Absperrflächen sind die Flächen, an denen Metall an Metall reibt. Abbildung 2 zeigt ein Beispiel für ein gängiges Snap-Fit-Design. Wenn sich die Form öffnet und schließt, reibt Metall an der Verschlussoberfläche. Um die Reibung zu verringern, insbesondere wenn die beiden Hälften der Spritzgussform leicht falsch ausgerichtet sind, wird ein etwas größerer Winkel (3°) empfohlen.
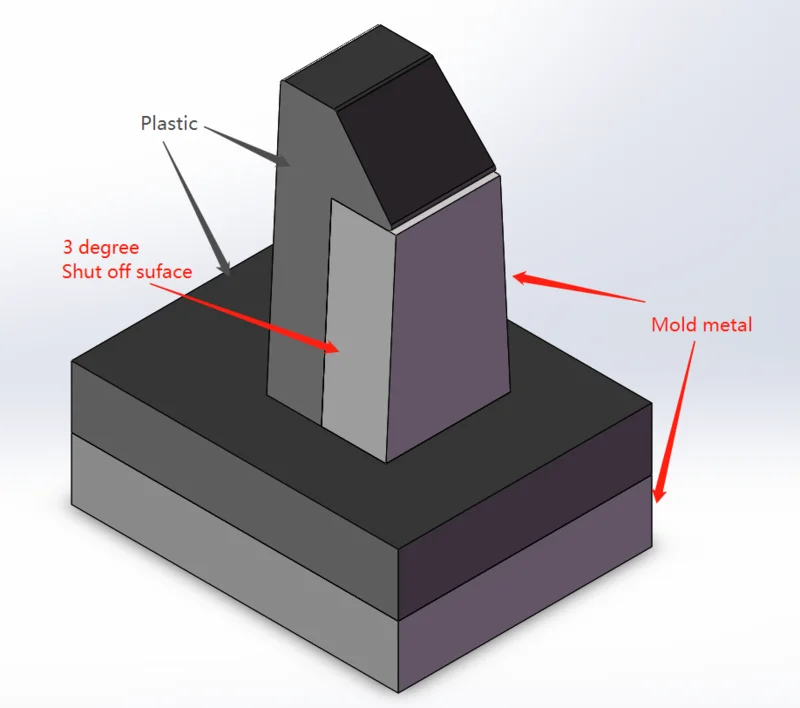
Rippen und Zwickel hinzufügen
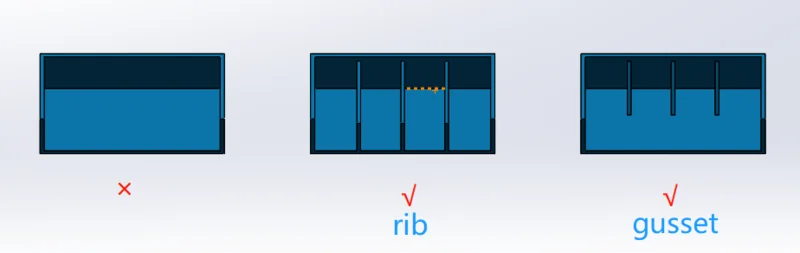
Rippen und Zwickel können die strukturelle Festigkeit eines Spritzgussteils erheblich erhöhen. Eine T-förmige Struktur ist bei gleichem Materialgewicht viel stärker als eine I-förmige Struktur. Um ein optimales Ergebnis zu erzielen, müssen Dicke, Höhe und Spannweite der Rippen sorgfältig abgewogen werden. Nachfolgend finden Sie einige allgemeine Regeln.
-
Die Dicke der Rippe an ihrer Basis sollte etwa 50-75 % der Nennwandstärke betragen.
-
Die Höhe der Rippe sollte etwa das 2.5- bis 3-fache der Nennwandstärke betragen.
-
Die Basis der Rippe sollte einen Radius von etwa dem 0.25- bis 0.4-fachen der Nennwandstärke haben.
Der Abstand zwischen zwei Rippen sollte etwa das 2- bis 3-fache der Nennwandstärke betragen.
Wenn eine Rippe an die Hauptwand anschließt, entsteht immer ein dickerer Bereich. Um Oberflächenfehler (Einfallstellen) zu vermeiden, ist es wichtig, diesen dicken Bereich so klein wie möglich zu halten. Wenn die Rippe jedoch zu dünn ist, muss sie möglicherweise tiefer gemacht werden, um genügend Festigkeit zu gewährleisten. Dies kann jedoch zu Problemen wie Knicken unter Druck führen und die Arbeit mit der Form erschweren. Auch mit hohem Druck eingespritzte Rippen können in der Form stecken bleiben.
Auch der gekrümmte Übergangsbereich zwischen Rippe und Hauptwand (Kehlradius) sollte nicht zu klein sein. Es dient dazu, die Spannung dort zu reduzieren, wo die Rippe auf die Hauptwand trifft. Idealerweise sollte der Kehlradius mindestens 25 Prozent der Rippendicke betragen.
Die Rippen selbst sollten im Allgemeinen zwischen der Hälfte und drei Viertel der Wandstärke betragen. Allerdings ist es am besten, das obere Ende dieses Bereichs anzustreben, wenn Sie mit Kunststoffen arbeiten, die eine geringe Schrumpfung aufweisen und weniger anfällig für Einfallstellen sind.
Bringen Sie Radien und Verrundungen am Spritzgussteil an.
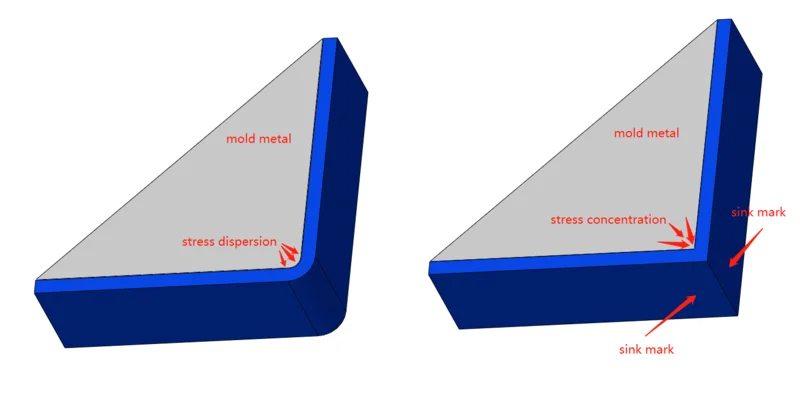
Die Einbindung abgerundeter Kanten in Spritzgussteile bietet, wann immer möglich, mehrere Vorteile. Erstens werden scharfe Ecken eliminiert, wodurch sowohl der Materialfluss als auch die strukturelle Integrität des Teils verbessert werden. Wenn Kunststoff abkühlt und schrumpft, konzentriert sich die Spannung auf scharfe Ecken. Bei Radienecken verteilt sich die Belastung über einen relativ langen Kurvenbereich und verringert so die Einfallstelle.
Radien und Verrundungen erleichtern auch das Auswerfen von Teilen, indem sie im Vergleich zu scharfen Ecken die Wahrscheinlichkeit verringern, dass Ecken während des Auswurfvorgangs stecken bleiben.
Darüber hinaus erhöht die Einbeziehung scharfer Ecken in Ihre Teilekonstruktion die Produktionskosten erheblich, da zur Erzielung dieser scharfen Ecken in der Form teure Fertigungstechniken erforderlich sind.
Um Ihr Design zu optimieren, sollten Sie erwägen, Innenradien hinzuzufügen, die mindestens dem 0.5-fachen der Dicke der angrenzenden Wand entsprechen, und Außenradien, die dem 1.5-fachen der Größe entsprechen.
Minimieren Sie Hinterschnitte und integrieren Sie Schlitze, wenn möglich.
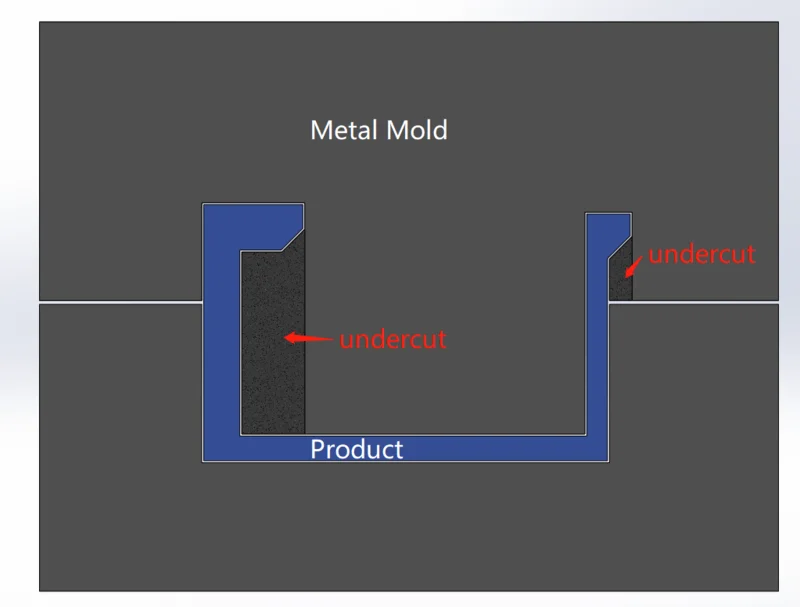
Ein Hinterschnitt bezieht sich auf ein Merkmal oder einen Bereich in der Geometrie eines Teils, bei dem es nicht möglich ist, das geformte Teil direkt aus der Form zu entfernen. Dies liegt daran, dass die Hinterschneidung eine mechanische Sperre erzeugt, die ein einfaches Auswerfen des Teils verhindert und eine komplexe Formkonstruktion oder zusätzliche Mechanismen zum Entfernen erfordert.
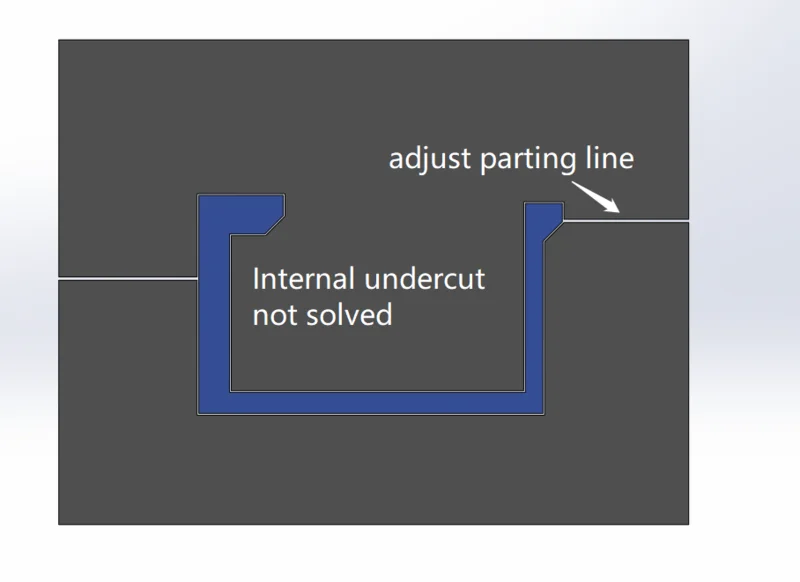
Um die äußeren Hinterschnitte zu beheben, können Konstrukteure die Trennlinie des Teils anpassen und die Hinterschnitte für den Auswurf zugänglich machen. Es gibt andere Techniken, um mit internen und externen Unterschnitten umzugehen.
Kernzüge: Beim Kernziehen werden hydraulische oder mechanische Systeme verwendet, um bewegliche Kerne in die Form zurückzuziehen. Diese Kerne passen sich der Form des Hinterschnitts an. Nach dem Erstarren des Kunststoffmaterials werden die Kerne aus dem Formteil gezogen und können so leicht gelöst werden. Kernzüge sind bei einfachen bis mittelschweren Hinterschnitten wirksam.
Schiebemechanismen: Schieber sind Formkomponenten, die sich senkrecht zur Öffnungs- und Schließbewegung der Form bewegen. Sie werden verwendet, um die Hinterschneidung beim Auswerfen aus der Form zu drücken. Schiebemechanismen sind vielseitig und können mit verschiedenen Hinterschnittformen umgehen, können jedoch die Formgestaltung komplexer machen.
Heber: Heber sind mechanische Komponenten, die das Formteil physisch anheben oder neigen, um Hinterschnitte freizugeben. Sie sind nützlich für kompliziertere Formen und anspruchsvolle Hinterschnitte, tragen aber auch zur Komplexität und Kosten der Form bei.
Opferkerne: Bei dieser Methode werden entfernbare Kerneinsätze innerhalb der Form verwendet. Diese Einsätze verbleiben im Formteil und werden nach dem Formen entfernt, um das Auswerfen zu erleichtern.
Abschläge: Durch Bump-offs oder Abstreif-Hinterschnitte wird eine leichte, kontrollierte Kraft auf die Form ausgeübt, um das Lösen des geformten Teils zu erleichtern, insbesondere wenn es sich um Teile handelt, die flexibel genug sind, um sich zu verformen und auszudehnen.
Andere Nebenaktionen: Diese Kategorie umfasst verschiedene Nebenaktionen wie manuelles Laden von Kernen, Abschraubmechanismen, zusammenklappbare Kerne und mehr. Diese Mechanismen werden verwendet, um spezifische Hinterschneidungsszenarien und komplexe Teilegeometrien zu bewältigen.
All dies erhöht die Kosten der Form und die Komplexität der Form. Dies sind die letzten Auswegmethoden, die Formkonstrukteuren zur Verfügung stehen, um sich mit der Hinterschnittstruktur zu befassen, nachdem die Teilekonstruktion abgeschlossen ist. Die beste Methode in der Teilekonstruktionsphase ist natürlich Unterschnitte vermeiden or einen Steckplatz hinzufügen unter den Hinterschneidungen, auch Absperrung genannt.
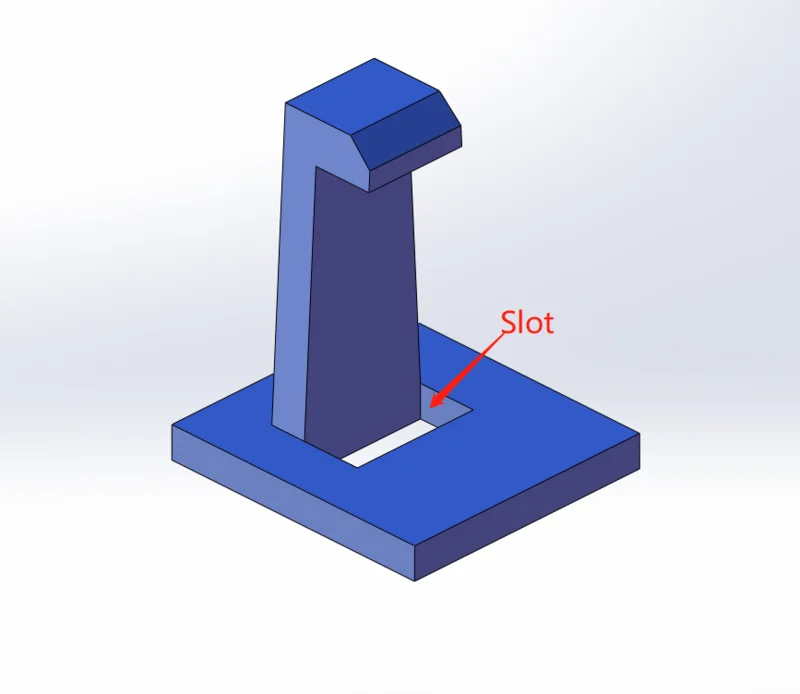
Befestigen Sie die Vorsprünge an Seitenwänden oder Rippen
Vorsprünge sind zylindrische Abstandshalter, die in ein Kunststoffteil eingegossen sind und einen Einsatz, eine selbstschneidende Schraube oder einen Stift für den Zusammenbau oder die Montage von Teilen aufnehmen. Der Vorsprung wird ebenso wie die Rippen an der Sollwand befestigt. Wie bei den Rippen sollte auch die Dicke der Wurzeln nicht zu groß sein, um Schrumpfspuren zu vermeiden. Daher muss auch die Wandstärke des Vorsprungs im Bereich von 50 % bis 75 % der Nennwandstärke liegen. Um die Festigkeit eines solchen dünnwandigen Vorsprungs zu gewährleisten, werden normalerweise Zwickel und Rippen hinzugefügt, um die Seitenwände zu stützen oder mit ihnen zu verbinden.
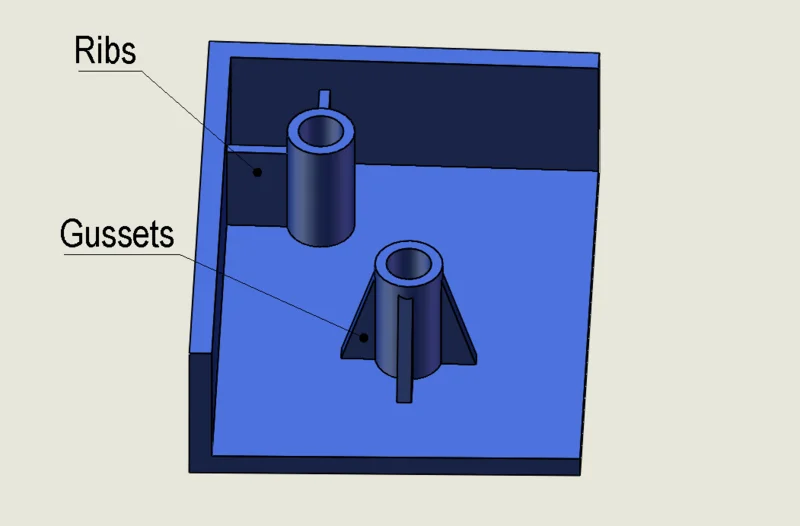
Vermeiden Sie tiefe Löcher und tiefe schmale Rillen
Dies ist hauptsächlich auf Überlegungen zur Formstruktur zurückzuführen. Die Formstruktur, die dem tiefen Loch entspricht, ist ein langer Stift, und die schmale und tiefe Nut entspricht dem dünnen Blech. Diese beiden Strukturen weisen eine geringe Festigkeit auf. Während des Spritzgussprozesses muss die Formstruktur Zehntausenden Stößen der heißschmelzenden Kunststoffflüssigkeit standhalten. Dies kann dazu führen, dass sich dünne Bleche und lange Stifte verbiegen oder brechen, und die gebrochenen Teile können manchmal Schäden an anderen Formteilen verursachen. Deshalb sollte es so weit wie möglich vermieden werden. Generell sollten Strukturen mit einem Loch-Tiefen-Verhältnis über 10 und Schlitze mit einem Breiten-Tiefen-Verhältnis über 10 vermieden werden.
Anschnittplatzierung: Betonung der Teileästhetik
Für die erfolgreiche Gestaltung und Produktion Ihres Spritzgussteils ist es entscheidend, dass der Hersteller Ihre Erwartungen an das Erscheinungsbild versteht.
Beim Spritzgießen sind bestimmte Markierungen unvermeidlich, darunter Angussmarkierungen, Trennflächenmarkierungen, seitliche Kernmarkierungen, Auswerferstiftmarkierungen und mehr. Es ist wichtig, eine offene Kommunikation mit dem Werkzeughersteller zu führen und Ihre spezifischen optischen Vorlieben hervorzuheben.
Angussmarken sind beispielsweise die Spuren, die dort zurückbleiben, wo das geschmolzene Material in die Form gelangt. Um diese Flecken dort zu vermeiden, wo sie unerwünscht sind, ist es wichtig, eng mit erfahrenen Herstellern zusammenzuarbeiten. Sie wählen Anschnitttypen, Anschnittpositionen, Trennflächenpositionen und andere Parameter sorgfältig auf der Grundlage Ihrer Anforderungen aus, um diese Markierungen zu minimieren und das gewünschte Finish für Ihr Teil zu erzielen.
Sprechen Sie mit den Experten: Optimieren Sie das Design Ihrer Spritzgussteile
Bei CapableMachining hat unser erfahrenes Expertenteam nicht nur eine Vielzahl von Kunststoffteilkonstruktionen miterlebt, sondern auch zahlreiche Herausforderungen im Zusammenhang mit der Teilekonstruktion und den Spritzgussprozessen erfolgreich gemeistert. Die Zusammenarbeit mit erfahrenen Spritzgussunternehmen zu Beginn Ihrer Designreise kann Ihren Weg zum Erfolg erheblich optimieren.
Wir sind stolz darauf, wertvolle Beratung anzubieten, die auf unserem umfassenden Branchenwissen basiert. Wenn Sie über einen Aspekt der Gestaltung von Spritzgussteilen nachdenken, freuen wir uns über Ihre Fragen und die Möglichkeit, maßgeschneiderte Vorschläge zu unterbreiten. Bei CapableMachining hat der Erfolg Ihres Projekts für uns Priorität.