Wenn es um die Umformung von Nichteisenmetallen mit niedrigem Schmelzpunkt geht, Hochdruck-Druckguss (HPDC) steht im Mittelpunkt. Dieses weit verbreitete Herstellungsverfahren zeichnet sich durch die Herstellung komplexer, nahezu endgeformter Teile in großem Maßstab aus. Der Reiz von HPDC liegt in seiner Fähigkeit, Teile zu produzieren, die für die Bearbeitung und Montage vorbereitet sind, wodurch umfangreiche Nachbearbeitungsarbeiten entfallen. Mit minimalem Verzugsrisiko und der Flexibilität, mit Spezialstahl und Eisenlegierungen zu arbeiten, beweist HPDC sein Können. Dank der schieren Kraft des hohen Drucks dringt das geschmolzene Metall in jeden noch so kleinen Spalt der Form ein und ermöglicht so die Schaffung komplizierter und faszinierender Formen.
Simulation im HPDC
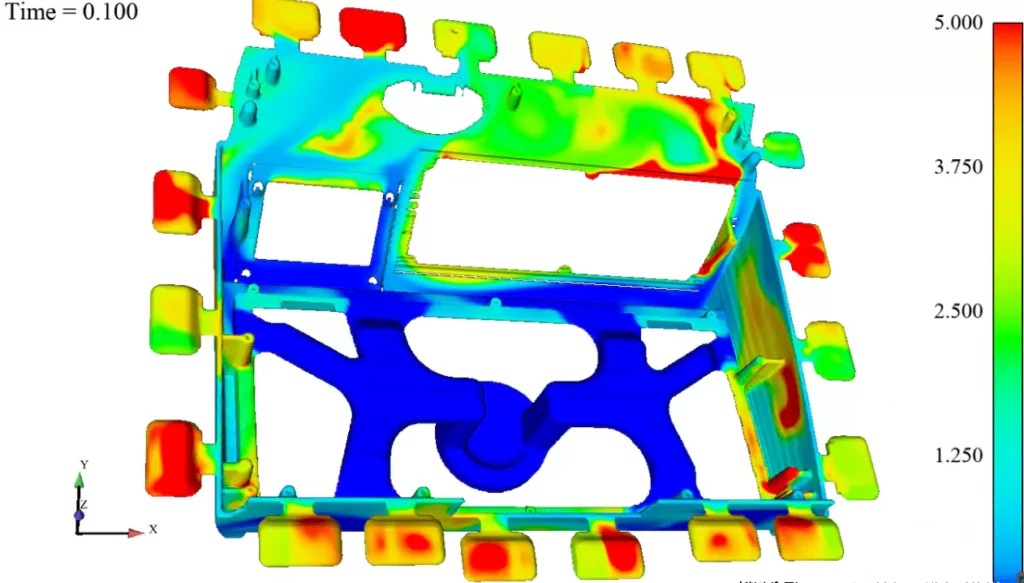
1. Überblick über Simulationssoftware
Wenn es darum geht, die Komplexität des Hochdruck-Druckgusses (HPDC) zu meistern, ist Simulationssoftware wie die renommierte Z-CAST tritt ins Rampenlicht. Dieses leistungsstarke Tool ermöglicht es Herstellern, in die Welt der virtuellen Modellierung und Simulation einzutauchen und bietet ein umfassendes Verständnis des HPDC-Prozesses. Mit Z-CAST können Ingenieure den gesamten Gießvorgang simulieren, vom ersten Feilen bis zur anschließenden Erstarrung, und dabei sogar Wärmebelastungs- und Wärmebehandlungssimulationen berücksichtigen. Diese bemerkenswerte Software wird zu einem unschätzbaren Verbündeten im Kampf gegen Fehler, die das Endprodukt beeinträchtigen können.
Die Fähigkeiten von Z-CAST reichen weit und ermöglichen es Herstellern, eine Reihe von Fehlern zu identifizieren und zu beseitigen, die während des HPDC-Prozesses auftreten können. Durch die Durchführung von Simulationen können potenzielle Probleme wie störende Grate, ungefüllte Abschnitte, störende Blasen und das gefürchtete Heißreißen erkannt und proaktiv behoben werden. Die Möglichkeit, den Gussprozess virtuell nachzubilden und jeden Schritt sorgfältig zu analysieren, versetzt Ingenieure in die Lage, fundierte Entscheidungen zu treffen, Design- und Prozessparameter zu optimieren und die Produktion zu optimieren, um eine überragende Gussqualität zu erzielen.
2. Identifizierung von Fehlern durch Simulation
Simulation spielt eine zentrale Rolle in der Welt der Hochdruck-Druckguss (HPDC), indem es den Einfluss von Werkzeug- und Prozessparametern auf Defekte beleuchtet. Durch die Nutzung der Leistungsfähigkeit von Simulationssoftware wie dem innovativen Z-CAST erhalten Hersteller die Möglichkeit, Fehler zu identifizieren und zu untersuchen, die den HPDC-Prozess beeinträchtigen können, darunter Grate, ungefüllte Abschnitte, Blasen und Heißrisse.
Durch Simulation können Ingenieure die komplexe Beziehung zwischen Werkzeug- und Prozessparametern untersuchen und deren Einfluss auf das Auftreten von Fehlern untersuchen. Durch virtuelles Experimentieren mit verschiedenen Werkzeugdesigns und Prozesseinstellungen können Hersteller wertvolle Erkenntnisse gewinnen. Sie können analysieren, wie sich Variationen in der Formgeometrie, Prozessparametern und Kühlstrategien auf die Defektbildung auswirken.
Simulation bietet eine Plattform für iteratives Testen und Optimieren. Ingenieure können die Formenkonstruktionen verfeinern und Prozessparameter auf der Grundlage von Simulationsergebnissen anpassen, um Fehler zu minimieren. Mit jedem virtuellen Experiment vertieft sich das Verständnis der Ursache-Wirkungs-Beziehung zwischen Werkzeug- und Prozessparametern und Defekten.
Nehmen wir zum Beispiel das Auftreten von Flash während der HPDC. Mithilfe der Simulation können Ingenieure untersuchen, wie sich Änderungen im Chip-Design, im Angusssystem oder in den Schussparametern auf die Gratbildung auswirken. Durch die iterative Verfeinerung dieser Parameter können Hersteller optimale Einstellungen erreichen, die Gratdefekte minimieren.
Durch Simulation können Hersteller datengesteuerte Entscheidungen treffen und Chip- und Prozessparameter zur Fehlerreduzierung im HPDC optimieren. Durch den Einsatz von Simulationstools wie Z-CAST können Hersteller ihre Prozesse optimieren, was zu einer verbesserten Gussqualität und einer höheren Produktivität führt.
3. Parameter optimieren, um Fehler zu minimieren
Die Simulation hat sich im Bereich des Hochdruck-Druckgusses (HPDC) als wertvolles Werkzeug zur Optimierung von Guss- und Prozessparametern zur Minimierung von Fehlern erwiesen. Durch den Einsatz von Simulationstechniken können Hersteller sich auf die Suche nach fehlerfreien Gussteilen durch sorgfältige Parameteroptimierung machen.
Ein bemerkenswertes Beispiel ist eine Studie, in der das verwendet wurde Taguchi-Methode Optimierung der Prozessparameter zur Minimierung von Lunkerdefekten im HPDC der ADC 12-Legierung. Durch Simulation wurden verschiedene Prozessparameter bewertet, darunter die Position des Endschalters, der Verstärkungsdruck, die Geschwindigkeit der Phase 1 und die Geschwindigkeit der Phase 2. Ziel war es, die optimalen Einstellungen zu ermitteln, die zu minimalen Lunkerfehlern führen würden.
Die Studie ergab, dass die optimalen Prozessparameter zur Minimierung von Lunkerfehlern wie folgt ermittelt wurden: eine Endschalterposition von 170 mm, ein Verstärkungsdruck von 300 kg/cm², eine Phase-1-Geschwindigkeit von 1 m/s und eine Phase-2-Geschwindigkeit von 4 MS. Diese optimierten Parameter wurden durch umfangreiche Simulationsanalysen ermittelt und ermöglichen es Herstellern, ihren HPDC-Prozess für eine überlegene Gussqualität zu optimieren.
Durch den Einsatz von Simulationen zur Optimierung von Form- und Prozessparametern können Hersteller Fehler proaktiv beheben und die Gesamtqualität von HPDC-Gussteilen verbessern. Die Simulation ermöglicht eine umfassende Bewertung verschiedener Parameter und ermöglicht es Herstellern, fundierte Entscheidungen zu treffen und optimale Einstellungen zu erreichen, die zu einer Fehlerreduzierung führen.
Durch die Leistungsfähigkeit der Simulation können Hersteller eine kontinuierliche Reise der Parameteroptimierung beschreiten, neue Möglichkeiten für fehlerfreie HPDC-Gussteile erschließen und die Kundenzufriedenheit sicherstellen.
Fehler minimieren
1. Verbesserte Produktqualität durch Fehlerminimierung
Die Simulation im Hochdruck-Druckguss (HPDC) bietet erhebliche Vorteile, insbesondere bei der Verbesserung der Produktqualität durch Minimierung von Fehlern. Durch den Einsatz von Simulationen gewinnen Hersteller ein tieferes Verständnis der Flüssigkeitsströmung und der Erstarrungsdynamik, was zu einer verbesserten Produktqualität und Eigenschaftsstabilität führt. Dies ermöglicht wiederum die Reduzierung konservativer Sicherheitsfaktoren, die üblicherweise bei der Komponentenkonstruktion verwendet werden.
Beispielsweise ermöglicht eine Gießsimulationssoftware wie ProCAST die umfassende Simulation des gesamten HPDC-Prozesses für eine Al-Si-Legierung. Von der Gusserwärmung und dem thermischen Gusszyklus bis hin zum Vorfüllen der Gießkammer, der langsamen/schnellen Schussinjektion, dem Füllen/Erstarren der Gussform und der Intensivierung erfasst das vollständige numerische Modell die Feinheiten des Gießprozesses. Durch die Nutzung dieses Simulationsmodells können Hersteller den HPDC-Prozess mithilfe einer systematischen Methodik optimieren.
Optimierungsbemühungen können die Bestimmung der idealen Anzahl an Thermoformzyklen und die Feinabstimmung des Kolbenschussprofils umfassen, um die Defektbildung während der Einspritzung zu minimieren. Die Ergebnisse dieser Optimierungsbemühungen zeigen verbesserte mechanische Eigenschaften und verdeutlichen die positiven Auswirkungen der simulationsgesteuerten Fehlerminimierung auf die Produktqualität.
Durch den Einsatz von Simulationen zur Erforschung und Optimierung des HPDC-Prozesses können Hersteller erhebliche Fortschritte bei der Produktqualität erzielen. Die Fähigkeit, den Flüssigkeitsfluss, die Erstarrung und andere kritische Aspekte des Gießprozesses genau vorherzusagen und zu steuern, ermöglicht es Herstellern, Prozessparameter zu optimieren, Fehler zu minimieren und letztendlich Produkte mit verbesserten mechanischen Eigenschaften und Zuverlässigkeit zu liefern.
Durch die simulationsgesteuerte Fehlerminimierung können Hersteller konservative Sicherheitsfaktoren bei der Komponentenkonstruktion zuverlässig reduzieren, was zu effizienteren und kostengünstigeren Herstellungsprozessen führt und gleichzeitig die höchsten Produktqualitätsstandards einhält.
2. Effizienzsteigerung durch Simulation
Die Simulation bietet beim Hochdruck-Druckguss (HPDC) einen erheblichen Vorteil, da sie die Effizienz durch die Reduzierung von Versuch-und-Irrtum-Methoden bei der Identifizierung und Minimierung von Fehlern erhöht. Die Integration von Computer Aided Engineering (CAE) hat die Fertigungsindustrie revolutioniert und bietet einen zuverlässigen und effizienten Ansatz.
In der Gussindustrie hat die numerische Modellierung des Gussprozesses mithilfe von CAE die traditionellen Versuch-und-Irrtum-Forschungs- und Entwicklungsverfahren ersetzt. Dieser Wandel hat zu einer verbesserten Effizienz und Zuverlässigkeit geführt. Durch den Einsatz fortschrittlicher paralleler Rechentechniken und verschiedener Berechnungsmodelle können detaillierte Untersuchungen des Flüssigkeitsflusses, der Wärmeübertragung, der Erstarrung und der Defektbildung unter verschiedenen Gussbedingungen durchgeführt werden.
Dieser umfassende Ansatz ermöglicht die Untersuchung des Bauteildesigns und die Optimierung der Gussparameter. Hersteller können Produkte für die anschließende mikrostrukturelle und mechanische Charakterisierung mit größerer Sicherheit herstellen. Durch die Herstellung eines direkten Zusammenhangs zwischen Prozessbedingungen, Gussqualität und mechanischen Eigenschaften werden praktische, wirtschaftliche und energieeffiziente Verfahren wie Kokillenguss, Hochdruckguss (HPDC) und Stranggießen erreicht werden.
Simulationsbasierte Optimierung ermöglicht es Herstellern, bereits in der Entwurfs- und Produktionsphase fundierte Entscheidungen und Anpassungen zu treffen. Durch die Nutzung der Erkenntnisse aus virtuellen Experimenten können Hersteller den Bedarf an physischen Prototypen und umfangreichen Versuch-und-Irrtum-Iterationen minimieren. Es reduziert den Zeit- und Ressourcenverbrauch erheblich, was zu einer höheren Gesamteffizienz bei der Fehlererkennung und -behebung führt.
3. Kosteneinsparungen durch Simulation
Simulation im Hochdruck-Druckguss (HPDC) bietet erhebliche Kosteneinsparungen durch die Reduzierung der Anzahl fehlerhafter Produkte. Durch den Einsatz von Simulationsprogrammen können Hersteller eine genauere und effizientere Gestaltung des Gussstücklayouts erreichen, was zu Kostensenkungen und einer verbesserten Produktqualität führt.
Traditionell hing die Auswahl der HPDC-Bedingungen stark vom Fachwissen und der Erfahrung einzelner Mitarbeiter in der Gussindustrie ab. Simulationsprogramme haben diesen Prozess jedoch revolutioniert, indem sie einen systematischen Ansatz zur Bedingungsauswahl bieten. Durch den Einsatz fortschrittlicher Simulationstools können Hersteller den HPDC-Prozess genau modellieren und analysieren und so potenzielle Fehler identifizieren und die Gussparameter optimieren.
Durch die Simulation des Gießprozesses können Hersteller wertvolle Einblicke in das Verhalten des Flusses, der Erstarrung und der Abkühlung geschmolzenen Metalls gewinnen. Es ermöglicht ihnen, fundierte Entscheidungen hinsichtlich des Werkzeugdesigns, der Prozessparameter und der Materialauswahl zu treffen. Durch die Optimierung dieser Faktoren durch Simulation kann die Anzahl fehlerhafter Produkte deutlich reduziert werden.
Die Reduzierung fehlerhafter Produkte führt direkt zu Kosteneinsparungen für die Hersteller. Nacharbeit, Ausschuss und die damit verbundenen Arbeits- und Materialkosten werden minimiert, wenn Mängel frühzeitig in der Entwurfs- und Produktionsphase erkannt und behoben werden. Mithilfe der Simulation können Hersteller potenzielle Probleme wie Porosität oder Schrumpfung erkennen und die notwendigen Anpassungen vornehmen, um qualitativ hochwertige Gussteile sicherzustellen.
Mithilfe der Simulation können Hersteller auch verschiedene Design- und Prozessalternativen erkunden, ohne dass physische Prototypen erforderlich sind. Das spart nicht nur Zeit, sondern reduziert auch die Materialkosten. Durch das virtuelle Testen und Bewerten verschiedener Szenarien können Hersteller ihre Gießprozesse optimieren und fundierte Entscheidungen treffen, die zu Kosteneinsparungen führen.
Hindernisse und Einschränkungen
1. Genauigkeit von Simulationsmodellen
Die genaue Simulation des Hochdruck-Druckgussverfahrens (HPDC) stellt aufgrund seiner inhärenten Komplexität eine Herausforderung dar. Um präzise Ergebnisse zu erzielen, müssen verschiedene Faktoren berücksichtigt werden, die nur für HPDC gelten.
Die erste Herausforderung ergibt sich aus der Komplexität der Herstellungszyklen bei HPDC. Die Simulation muss die aufeinanderfolgenden Schritte des Prozesses berücksichtigen, einschließlich Formfüllung, Erstarrung und Abkühlung. Diese voneinander abhängigen Phasen machen es erforderlich, das dynamische Verhalten genau zu erfassen, um zuverlässige Simulationen zu erhalten.
Komplexe Teilegeometrien erschweren den Simulationsprozess zusätzlich. Bei HPDC handelt es sich oft um komplizierte Formen und das Einspritzen von geschmolzenem Metall mit hohen Geschwindigkeiten. Die genaue Modellierung solcher Geometrien bei gleichzeitiger Simulation des Flüssigkeitsflusses und der Erstarrung stellt eigene Herausforderungen dar. Darüber hinaus kann die Berechnung von Simulationen für komplexe Fälle sehr viel Zeit in Anspruch nehmen und von Stunden bis zu mehreren Tagen reichen, was effiziente Rechenressourcen erfordert.
In bestimmten Szenarien kann das Bedürfnis nach Zweckmäßigkeit das Streben nach hoher Genauigkeit überwiegen. Insbesondere bei zeitlichen Einschränkungen können Kompromisse zwischen Simulationsgeschwindigkeit und -präzision erforderlich sein.
HPDC-Simulationen müssen außerdem die Komplexität von Formen einschließlich fester und beweglicher Platten, Kerne und Kühlkanäle sowie Maschinenparameter wie Temperatur- und Geschwindigkeitsprofile berücksichtigen. Die Einbeziehung dieser komplizierten Randbedingungen in den Modellierungsprozess erhöht die Gesamtkomplexität und erfordert eine sorgfältige Kalibrierung.
Die Bewältigung dieser Herausforderungen erfordert kontinuierliche Weiterentwicklungen der Simulationstechniken, verbesserte Modellierungsfähigkeiten und effiziente Rechenressourcen. Die Zusammenarbeit zwischen Forschern, Softwareentwicklern und Branchenexperten ist von entscheidender Bedeutung, um diese Hindernisse zu überwinden und die Genauigkeit von Simulationsmodellen für HPDC zu verbessern.
Während die Herausforderungen hinsichtlich der Genauigkeit weiterhin bestehen, streben laufende Forschung und technologische Fortschritte danach, den Simulationsprozess zu verfeinern, um präzisere Vorhersagen und Optimierung der HPDC-Parameter zu ermöglichen.
2. Komplexität des HPDC-Prozesses
Der HPDC-Prozess stellt aufgrund seiner inhärenten Komplexität erhebliche Herausforderungen dar, die sich auf die Genauigkeit der Simulationsergebnisse auswirken können. Das Verständnis und die Bewältigung dieser Komplexitäten sind für den effektiven Einsatz von Simulationstools bei der Optimierung von HPDC-Prozessen von entscheidender Bedeutung.
Die komplizierte Natur von HPDC, die durch aufeinanderfolgende Herstellungszyklen gekennzeichnet ist, stellt eine Herausforderung für die Simulation dar. Die Erfassung des gesamten Prozesses, einschließlich der komplexen Geometrien der Teile und des Einspritzens der Legierung mit hohen Geschwindigkeiten, erfordert umfangreiche Rechenressourcen und kann zu langen Berechnungszeiten führen, die sich manchmal über mehrere Tage erstrecken.
Die einzigartigen Eigenschaften von HPDC, wie komplexe Formen bestehend aus festen und beweglichen Platten, Kernen und Kühlkanälen, sowie Maschinenparameter wie Einspritztemperatur, Kolbengeschwindigkeiten und Zykluszeiten, erhöhen die Anzahl der Randbedingungen, die bei der Modellierung berücksichtigt werden müssen Verfahren. Die genaue Berücksichtigung dieser Faktoren erhöht die Komplexität der Simulation.
Zusätzlich zu den allgemeinen Schwierigkeiten, die mit numerischen Simulationen von Metallgussprozessen verbunden sind, bringt HPDC spezifische Herausforderungen mit sich, die sich auf die Zuverlässigkeit der Ergebnisse auswirken. Ein entscheidender Aspekt ist die Gewinnung zuverlässiger und präziser Daten zu den Materialeigenschaften komplexer Legierungen. Die Genauigkeit der Simulation hängt stark von der Verfügbarkeit genauer Materialdaten ab.
Die Komplexität des HPDC-Prozesses, der die komplizierten Teilegeometrien, hohen Einspritzgeschwindigkeiten und die Vielzahl der beteiligten Parameter umfasst, stellt ständige Herausforderungen für eine genaue Simulation dar. Forscher und Ingenieure arbeiten weiterhin daran, diese Komplexität zu überwinden, die Modellierungstechniken zu verbessern und die Zuverlässigkeit der Simulationsergebnisse zu erhöhen.
Schlussfolgerung
Simulation spielt eine entscheidende Rolle bei der Minimierung von Fehlern beim Hochdruckguss (HPDC). Mithilfe von Software wie Z-CAST ermöglicht die Simulation die Identifizierung und Optimierung von Form- und Prozessparametern, um Fehler effektiv zu minimieren. Dies führt zu einer verbesserten Produktqualität, erhöhter Effizienz und Kosteneinsparungen. Es ist auch wichtig, die Herausforderungen und Einschränkungen anzuerkennen, die mit der Simulation in HPDC verbunden sind, wie z. B. die Sicherstellung der Modellgenauigkeit und die Notwendigkeit von Fachwissen für eine effektive Implementierung. Zukünftige Forschungsbemühungen können sich auf die Verfeinerung von Simulationsmodellen und die Erforschung von Synergien mit neuen Technologien wie maschinellem Lernen konzentrieren, um die Fehlerminimierung in HPDC weiter zu verbessern.