Obwohl Alchemie möglicherweise nicht real ist, ist die Galvanisierung eine naheliegende Alternative zur Umwandlung gewöhnlicher chemischer Elemente in wertvolle Elemente. Dabei wird Strom angelegt, um ein unedles Metall wie Kupfer oder Aluminium mit einer dünnen Schicht eines anderen Metalls wie Gold oder Silber zu überziehen. Galvanisieren dient vielen Zwecken, die über die bloße Verbesserung des Aussehens kostengünstiger Metalle hinausgehen. Es kann auch verwendet werden, um Gegenstände rostbeständig zu machen und sogar Kunststoff wie Metall aussehen zu lassen. Wie funktioniert diese faszinierende Technik? Lassen Sie uns tiefer eintauchen und es herausfinden.
Was ist Galvanisieren?
In den Galvanisieren Dabei wird ein elektrischer Strom durch eine Elektrolytlösung geleitet, indem zwei Elektroden darin eingetaucht und an eine Stromversorgung oder Batterie angeschlossen werden. Sowohl die Elektroden als auch die Elektrolyte bestehen aus sorgfältig ausgewählten Elementen oder Verbindungen. Während der Strom durch den Stromkreis fließt, zerfällt der Elektrolyt, wodurch sich einige seiner Metallatome auf einer der Elektroden ablagern und diese effektiv elektroplattieren. Mit dieser Methode kann eine Vielzahl von Metallen plattiert werden, darunter Kupfer, Gold, Silber, Zink, Zinn, Cadmium, Nickel, Chrom, Platin und Blei.
Dieser Prozess ähnelt der Elektrolyse, bei der Strom zum Aufspalten einer chemischen Lösung eingesetzt wird. Elektrochemie ist die Untersuchung chemischer Reaktionen, die durch Elektrizität verursacht oder beschleunigt werden, um Produkte herzustellen, die für Wissenschaft oder Industrie nützlich sind. Dazu gehören Galvanisieren, Elektrolyse und die Funktionsweise von Batterien.
Wie funktioniert Galvanisieren?
Hier sind die grundlegenden Schritte beim Galvanisieren:
Elektrolyse
Der Galvanisierungsprozess basiert auf dem Prinzip der Elektrolyse, einer chemischen Reaktion bzw. der Zersetzung eines Stoffes durch elektrischen Strom. Wenn ein Gleichstrom (DC) durch eine Lösung geleitet wird, die Ionen des zu plattierenden Metalls enthält, werden die Metallionen an der Kathode (negative Elektrode) reduziert (dh sie gewinnen Elektronen). Sie werden auf der Oberfläche der zu plattierenden Kathode (den zu plattierenden Teilen) abgeschieden. Währenddessen verliert die Anode (positive Elektrode), die normalerweise das Beschichtungsmetall ist, Elektronen und verwandelt sich in gelöste Metallionen.
Elektroden
Elektroden sind leitfähige Materialien, die den elektrischen Strom in die Elektrolytlösung leiten. Die Kathode besteht typischerweise aus dem zu plattierenden Metall, während die Anode normalerweise aus dem zu plattierenden Metall besteht.
Galvanisierungsbad
Das Galvanisierbad ist die Lösung, die die Metallionen enthält, die auf das Objekt plattiert werden sollen. Es besteht typischerweise aus einem Salz des betreffenden Metalls, das in Wasser gelöst ist, zusammen mit verschiedenen Zusatzstoffen zur Verbesserung des Galvanisierungsprozesses, wie z. B. Puffern zur Kontrolle des pH-Werts der Lösung, Tensiden zur Reduzierung der Oberflächenspannung und Komplexbildnern zur Unterstützung der Ionenbindung in der Lösung.
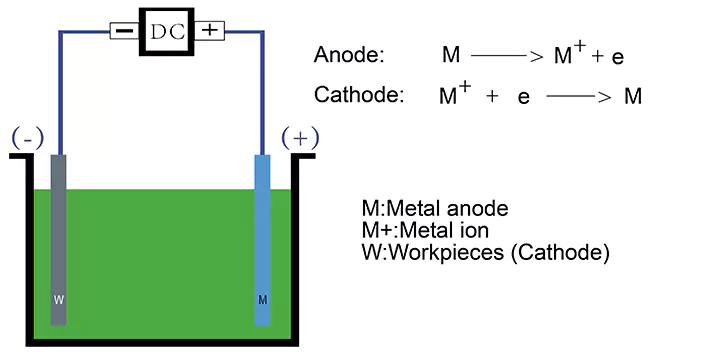
Ablagerung des Metalls
Während der elektrische Strom durch die Elektrolytlösung fließt, werden Metallionen von der Kathode angezogen und auf der Oberfläche des zu plattierenden Objekts abgeschieden. Die Abscheidungsgeschwindigkeit hängt von einer Reihe von Faktoren ab, beispielsweise der Stromdichte (der Strommenge pro Flächeneinheit), der Konzentration der Metallionen im Galvanisierungsbad und der Temperatur der Lösung.
Arten der Galvanisierung
Die dekorative Galvanisierung dient vor allem der optischen Aufwertung von Gegenständen. Dabei wird eine dünne Schicht eines edleren Metalls wie Gold oder Silber auf ein weniger teures Metall wie Kupfer oder Nickel aufgetragen, um ihm ein dekoratives Finish zu verleihen. Dekorative Galvanisierung wird häufig in der Schmuckindustrie sowie für Wohndekorationen wie Türklinken, Leuchten und Bilderrahmen verwendet.
Funktionelle Galvanisierung hingegen dient der Verbesserung der Eigenschaften und Leistungsfähigkeit eines Materials. Dabei wird eine Schicht aus einem bestimmten Metall auf ein Objekt aufgetragen, um dessen Korrosionsbeständigkeit, Verschleißfestigkeit, Leitfähigkeit oder andere Eigenschaften zu verbessern. Funktionelle Galvanisierung wird in der Automobilindustrie häufig eingesetzt, um die Haltbarkeit von Motorteilen zu verbessern und Korrosion zu verhindern. Es wird auch in der Luft- und Raumfahrtindustrie verwendet, um die Leistung von Komponenten wie Turbinenschaufeln und Hydraulikteilen zu verbessern, und in der Elektronikindustrie, um die Leitfähigkeit zu verbessern und Korrosion zu verhindern.
Metalle für die Galvanisierung
Für die Galvanisierung können verschiedenste Metalle verwendet werden, darunter:
Gold
Silber
Kupfer
Super
Chrom
Zink
Cadmium
Zinn
Führen (Lead)
Rhodium
Palladium
Platin
Eisen
Cobalt
Aluminium
Die Wahl des Metalls hängt von den spezifischen Eigenschaften ab, die für die Anwendung erforderlich sind. Beispielsweise werden Gold und Silber aufgrund ihres glänzenden Aussehens häufig zu dekorativen Zwecken verwendet, während Verkupferung und Vernickelung aufgrund ihrer Leitfähigkeit häufig in der Elektronikindustrie eingesetzt werden. Chrom und Zink werden häufig zum Schutz vor Korrosion und Zinn und Blei zum Löten verwendet. Manchmal wird eine Kupferbeschichtung als Grundierung verwendet, um die Haftung der Beschichtung anderer Metalle wie Nickel zu erhöhen. Das für die Galvanisierung verwendete spezifische Metall wirkt sich auch auf die Kosten und die Umweltauswirkungen des Prozesses aus.
Galvanik und Toleranzen
Konstrukteure müssen verstehen, dass die Toleranz galvanisierter Teile von mehreren Variablen beeinflusst werden kann, einschließlich der Art des für die Beschichtung verwendeten Metalls und des Beschichtungsprozesses selbst. Unterschiedliche Chemikalien und Prozesse führen zu unterschiedlichen Ergebnissen, wenn es um die Gleichmäßigkeit der Schichtdicke (CTU) sowie die Gesamttoleranzen der Teile geht. Im Folgenden sind einige Dinge aufgeführt, die die Teiletoleranz durch den Galvanisierungsprozess beeinflussen können.
Kantenaufbau
Kantenaufbau kommt beim Galvanisieren häufig vor. Er tritt auf, wenn die Kanten eines Teils dicker als die Mitte sind, da die Kanten eine stärkere Verteilung des Galvanisierungsstroms aufweisen. Dies kann zu einer schlechten Passung zwischen den Komponenten führen. Aus gestalterischer Sicht sollten Sie möglichst abgerundete Kanten verwenden.
Fassbeschichtung vs. Rackbeschichtung
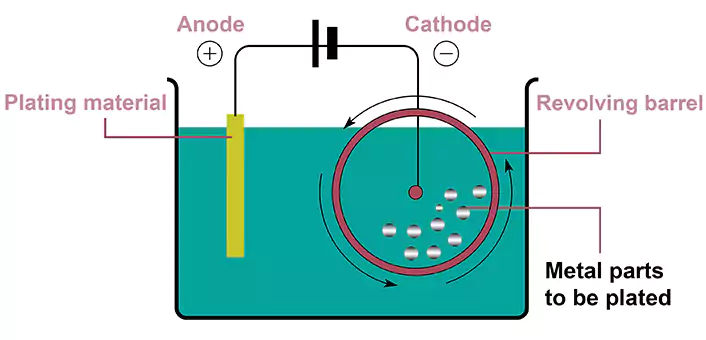
Bei der Trommelbeschichtung werden die Teile in ein rotierendes Fass gelegt, das mit der Beschichtungslösung gefüllt ist, wodurch eine gleichmäßige Abdeckung des Substrats gewährleistet wird. Die Rotation des Zylinders ist auch wichtig, um eine gute CTU (Coating Thickness Uniformity) zu erreichen. Da die Größe und Form der Teile in diesem Prozess keine Rolle spielt, können sie außerdem zum Beschichten kleiner und komplizierter Komponenten sowie großer und komplexer Komponenten verwendet werden. Die Begrenzung der Teilegröße einer Trommelbeschichtung hängt nur von der Trommelgröße ab. Da die CTU ziemlich gut ist, ist es einfacher, Toleranzen bei der Anwendung der Trommelbeschichtung zu kontrollieren.
Beim Gestellgalvanisieren werden Teile an Gestellen aufgehängt und in die Galvanolösung getaucht. Das nahe Ende (in der Nähe der Stromversorgung) ist normalerweise dicker beschichtet, während das entfernte Ende dünner beschichtet ist. Die schlechte CTU in der Rack-Beschichtung kann zu Problemen bei der Toleranzkontrolle führen. Der Konstrukteur muss mehr Toleranz einräumen, wenn eine Gestellbeschichtung ausgewählt wird, oder der Schleifprozess nach der Gestellbeschichtung muss berücksichtigt werden, um eine enge Toleranz einzuhalten.
Schwer durchströmbare Bereiche
Wenn die Form des Teils komplex ist, bilden einige Ecken halbgeschlossene Bereiche. Während des Galvanisierungsprozesses können die Metallionen in der Galvanisierungslösung in diesen schwer fließenden Bereichen nicht rechtzeitig wieder aufgefüllt werden und es bildet sich eine sehr dünne Galvanisierungsschicht, die die Präzision und das Aussehen der Teile beeinträchtigt.
Es ist wichtig, diese Überlegungen in den Designprozess einzubeziehen, um die ordnungsgemäße Leistung galvanisierter Komponenten sicherzustellen.
Kunststoffe galvanisieren
Kunststoffe sind aufgrund ihrer Erschwinglichkeit, Flexibilität und ihres geringen Gewichts zu einem der vielseitigsten und am weitesten verbreiteten Materialien geworden. Allerdings könnten die geringen Kosten und das einheitliche Erscheinungsbild von Kunststoff von manchen als Nachteil angesehen werden. Um dieses Problem anzugehen, besteht eine Lösung darin, einen dünnen Metallfilm auf Kunststoffoberflächen zu galvanisieren, um ihnen ein attraktives und glänzendes Aussehen zu verleihen und gleichzeitig die praktischen Vorteile von Kunststoff beizubehalten. Dieses Verfahren kann auf verschiedene Arten von Kunststoffen angewendet werden, wie z ABS, Nylon, Polycarbonat, Phenolkunststoffe und Harnstoff-Formaldehyd. Galvanisierte Kunststoffteile kommen häufig in Sanitär-, Haushalts-, Automobil- und Elektrokomponenten vor und bieten eine rostfreie und kostengünstige Alternative zu Ganzmetallteilen, die nach dem Galvanisieren kein zusätzliches Polieren erfordern.
Wie werden Kunststoffe galvanisiert?
Die Herausforderung beim Galvanisieren von Kunststoffen ist ihre mangelnde elektrische Leitfähigkeit. Dies macht den Prozess jedoch nicht unmöglich und es werden zusätzliche Schritte unternommen, um die Kunststoffoberfläche elektrisch leitfähig zu machen. Der erste Schritt besteht darin, den Kunststoff gründlich zu reinigen, um oberflächliche Verunreinigungen wie Fett, Schmutz oder Flecken zu entfernen.
Anschließend wird der Kunststoff mit Säure und einem Katalysator behandelt, um die Oberfläche für die Metallbeschichtung vorzubereiten. Anschließend wird der Kunststoff in ein Bad mit Kupfer oder Nickel (häufiger ist Kupfer) getaucht, wodurch eine ultradünne Metallschicht mit einer Dicke von weniger als einem Mikrometer entsteht. Nach dieser Erstbehandlung ist der Kunststoff bereit für die Galvanisierung und kann je nach den Verschleißanforderungen der Anwendung mit einer Dicke von 10–30 Mikrometern beschichtet werden.
Vorteile des Galvanikverfahrens
Die Vorteile der Galvanisierung sind folgende:
Verbesserte Korrosionsbeständigkeit
Nickel und Chrom können eine dichte Oxidschicht in der Luft bilden, und die Galvanisierung mit Nickel oder Chrom kann die Korrosionsbeständigkeit von Metallen verbessern und sie vor Schäden durch Feuchtigkeit und andere Umweltfaktoren schützen. Gold ist ein inertes Metall, es oxidiert nicht leicht, die Vergoldung isoliert das Grundmetall von äußeren Medien und verbessert somit auch die Korrosionsbeständigkeit. Beispielsweise müssen Bodenfeuchtigkeitssensoren der Korrosion des Bodens widerstehen und die elektronische Leitfähigkeit der Oberfläche aufrechterhalten. Eine Vergoldung ist die einzige Lösung.
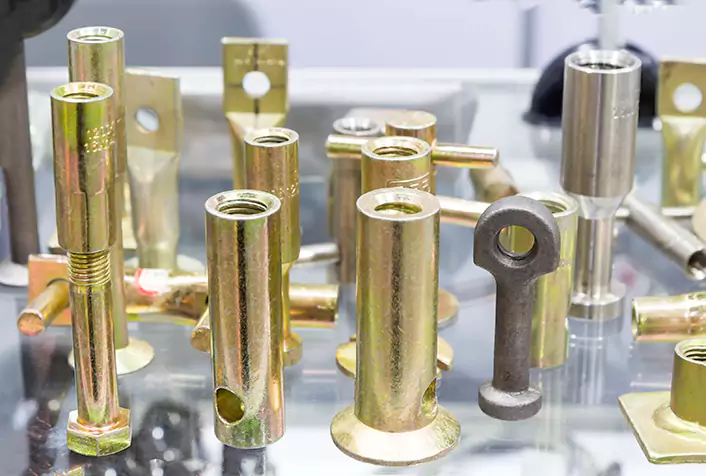
Verbesserte Verschleißfestigkeit
Galvanisieren kann auch die Verschleißfestigkeit von Metallen verbessern und sie dadurch haltbarer und langlebiger machen. Eine galvanisierte Metalloberfläche ist sicherlich schwerer zu zerkratzen als eine lackierte oder pulverbeschichtete Oberfläche.
Verbessertes Aussehen
Galvanisieren kann das Aussehen von Metallen verbessern und ihnen ein glänzendes und attraktives Finish verleihen.
Reduzierte Reibung
Durch Galvanisieren kann die Reibung zwischen beweglichen Metallteilen verringert werden, wodurch diese glatter und effizienter werden.
Vielseitigkeit
Galvanisieren kann auf einer Vielzahl von Materialien angewendet werden, darunter Metalle, Kunststoffe und Keramik, was es zu einer vielseitigen Beschichtungsoption für viele Branchen macht.
Kosteneffizient
Im Vergleich zu anderen Verfahren wie Lackieren oder Pulverbeschichten ist die Galvanisierung eine relativ kostengünstige Methode zur Beschichtung von Metallen.
Nachteile der Galvanisierung
Allerdings hat es auch mehrere Nachteile:
Umweltsorgen
Bei der Galvanisierung werden Chemikalien verwendet, die bei unsachgemäßer Handhabung schädlich für die Umwelt sein können. Abfallentsorgung und verschüttete Chemikalien können zur Verschmutzung und Kontamination von Boden, Wasser und Luft führen.
Begrenzte Materialoptionen
Nicht alle Materialien können galvanisiert werden und das Verfahren ist möglicherweise für bestimmte Materialien oder Formen nicht geeignet. Einige Materialien erfordern möglicherweise eine Vorbehandlung oder spezielle Verfahren, um sie für die Galvanisierung vorzubereiten.
Gesundheits- und Sicherheitsrisiken

Die beim Galvanisieren verwendeten Chemikalien können gefährlich sein, wenn sie nicht ordnungsgemäß gehandhabt werden, und die Arbeiter sind möglicherweise dem Risiko ausgesetzt, Dämpfen, Staub und anderen Gefahren ausgesetzt zu sein.
Energieverbrauch
Galvanisieren kann eine erhebliche Menge Energie verbrauchen und zu Treibhausgasemissionen und anderen Umweltauswirkungen beitragen.
Schlussfolgerung
Zusammenfassend ist Galvanisieren ein Prozess, bei dem ein elektrischer Strom durch eine Elektrolytlösung geleitet wird, um ein Metall mit einer dünnen Schicht eines anderen Metalls zu überziehen. Dieses Verfahren hat eine Reihe von Anwendungen in verschiedenen Branchen, darunter dekorative und funktionelle Beschichtungen, verbesserte Korrosions- und Verschleißfestigkeit sowie verringerte Reibung.
Der Galvanisierungsprozess beginnt mit der Reinigung des Substrats und der anschließenden Behandlung mit einer Säureätzung und einem Katalysator, um es elektrisch leitfähig zu machen. Das Substrat wird dann in ein Bad des gewünschten Metalls getaucht, das durch Anlegen von elektrischem Strom auf der Oberfläche abgeschieden wird.
Galvanisieren wird häufig in Branchen wie der Automobil-, Luft- und Raumfahrt-, Elektronik- und Schmuckindustrie eingesetzt. Es ist wichtig, Teile herzustellen, die korrosionsbeständig, verschleißfest und attraktiv sind. Das Verfahren wird auch zur Herstellung von Legierungen und zur Herstellung von Metalloptiken aus Kunststoff und anderen nichtmetallischen Materialien eingesetzt.
Insgesamt spielt die Galvanisierung in verschiedenen Branchen eine entscheidende Rolle und trägt zur Herstellung langlebiger und ästhetisch ansprechender Produkte bei. Das Verfahren hat seine Vor- und Nachteile, darunter Umweltbedenken, Kosten, begrenzte Materialoptionen sowie Gesundheits- und Sicherheitsrisiken, die sorgfältig gemanagt werden müssen, um sichere und nachhaltige Verfahren zu gewährleisten.